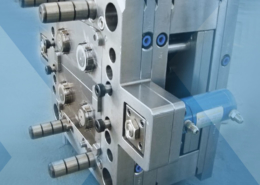
Exploring Electrical Plastic Molding: Bridging Innovation and Functionality
Author:gly Date: 2024-06-08
Introduction
In the dynamic landscape of electrical engineering, the integration of plastic molding techniques has revolutionized the design, production, and performance of electrical components and devices. Electrical plastic molding combines the versatility of plastics with the precision of molding processes to create a wide array of components, from connectors and switches to enclosures and housings. This article delves into the realm of electrical plastic molding, exploring its significance, techniques, applications, challenges, and future directions.
Significance of Electrical Plastic Molding
Enhancing Design Flexibility
Electrical plastic molding offers unparalleled design flexibility, allowing engineers to create complex shapes, intricate details, and custom features that meet specific functional and aesthetic requirements. This flexibility enables innovation in product design and differentiation in the marketplace.
Improving Performance and Reliability
Plastic materials used in electrical molding exhibit properties such as insulation, corrosion resistance, and dimensional stability, which enhance the performance and reliability of electrical components. By protecting sensitive electronics from environmental factors and mechanical stress, plastic molding contributes to the longevity and functionality of electrical systems.
Cost-Effectiveness and Scalability
The mass production capabilities of plastic molding processes, such as injection molding and extrusion, make electrical plastic molding a cost-effective solution for producing high volumes of components. This scalability allows manufacturers to meet demand fluctuations and achieve economies of scale without compromising quality or consistency.
Techniques in Electrical Plastic Molding
Injection Molding
Injection molding is the predominant technique for producing intricate and high-precision plastic components used in electrical applications. By injecting molten plastic into a mold cavity under high pressure, injection molding enables the rapid and cost-effective production of connectors, housings, and other components with tight tolerances.
Compression Molding
Compression molding involves placing thermoset plastic material in a heated mold cavity and applying pressure to shape it into the desired form. While less commonly used in electrical applications than injection molding, compression molding offers advantages such as lower tooling costs and the ability to mold large, thick-walled parts.
Overmolding
Overmolding combines multiple materials or components into a single integrated assembly, enhancing functionality, durability, and aesthetics. In electrical applications, overmolding is often used to encapsulate connectors, cables, or electronics with a protective layer of thermoplastic material, providing insulation and strain relief.
Challenges and Future Directions
Material Selection and Compatibility
Selecting the appropriate plastic material is critical to ensuring the performance, reliability, and safety of electrical components. Factors such as thermal stability, chemical resistance, and dielectric strength must be carefully considered to meet industry standards and regulatory requirements.
Sustainability and Environmental Impact
As concerns about environmental sustainability grow, the electrical industry faces pressure to reduce waste, energy consumption, and carbon emissions associated with plastic molding processes. Future research and innovation may focus on developing biodegradable plastics, recycling technologies, and eco-friendly manufacturing practices to mitigate environmental impact.
Integration of Smart Technologies
Advancements in sensor technology, connectivity, and miniaturization are driving the development of smart electrical devices and systems. Electrical plastic molding will play a crucial role in enabling the integration of sensors, antennas, and other electronic components into compact and durable housings, facilitating the proliferation of smart home, automotive, and industrial applications.
Conclusion
In conclusion, electrical plastic molding represents a convergence of innovation, functionality, and sustainability in the field of electrical engineering. By harnessing the capabilities of plastic materials and molding processes, engineers and manufacturers can design and produce a diverse range of components that power our interconnected world. As technology continues to evolve and societal demands shift, the role of electrical plastic molding will remain pivotal in driving progress, enabling innovation, and shaping the future of electrical systems and devices. By addressing challenges, embracing new technologies, and prioritizing sustainability, the electrical industry can harness the full potential of plastic molding to create safer, smarter, and more sustainable electrical solutions for generations to come.
GETTING A QUOTE WITH LK-MOULD IS FREE AND SIMPLE.
FIND MORE OF OUR SERVICES:
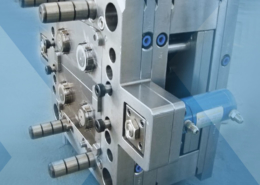
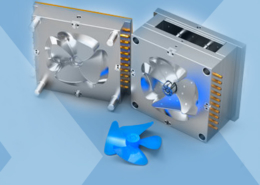
Plastic Molding

Rapid Prototyping
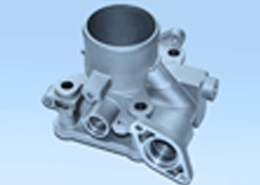
Pressure Die Casting
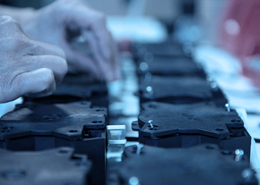
Parts Assembly
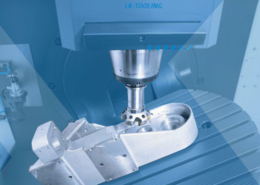