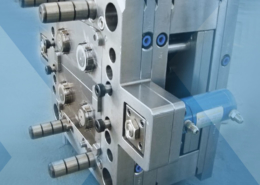
Unveiling the Wonders of Electrical PVC Moulding
Author:gly Date: 2024-06-08
Electrical PVC moulding stands as a cornerstone of modern electrical infrastructure, providing a versatile and durable solution for housing and protecting electrical wiring and components. In this article, we embark on a journey to explore the intricacies of electrical PVC moulding, from its origins to its contemporary applications and future prospects.
Introduction: A World of Possibilities
Imagine a world where electrical wiring seamlessly integrates into the built environment, concealed within sleek and durable enclosures that not only protect but also enhance the aesthetics of our surroundings. This is the promise of electrical PVC moulding – a versatile solution that combines functionality with form, offering endless possibilities for architects, engineers, and designers alike.
Origins and Evolution
Early Beginnings
The use of PVC (polyvinyl chloride) as a material for electrical enclosures dates back to the mid-20th century, coinciding with the rise of modern electrical infrastructure. PVC's inherent properties, including its durability, chemical resistance, and ease of fabrication, made it an ideal choice for housing and protecting electrical components in a variety of settings.
Technological Advancements
Advancements in manufacturing processes and materials science have further enhanced the capabilities of electrical PVC moulding. Today, state-of-the-art injection moulding techniques allow for the production of complex and precision-engineered PVC enclosures with minimal waste and maximum efficiency.
Industry Applications
Electrical PVC moulding finds applications across a diverse range of industries, from residential and commercial construction to industrial and infrastructure projects. Its versatility and durability make it suitable for a wide array of applications, including conduit systems, junction boxes, switchgear enclosures, and cable trays.
The Electrical PVC Moulding Process
Design and Engineering
The process begins with careful design and engineering, where architects, engineers, and designers collaborate to create custom solutions tailored to the specific requirements of each project. CAD (computer-aided design) software allows for precise modelling and simulation, ensuring optimal functionality and aesthetic appeal.
Material Selection
Choosing the right PVC formulation is critical to the success of the moulding process. Factors such as impact resistance, UV stability, and flame retardancy must be taken into account to ensure compliance with industry standards and regulatory requirements.
Moulding and Fabrication
Once the design and materials are finalized, the moulding process can commence. PVC resin pellets are heated and injected into precision-engineered moulds, where they cool and solidify to form the desired shape. Post-processing techniques such as trimming, drilling, and finishing may be employed to achieve the final product.
Advantages and Innovations
Durability and Weather Resistance
One of the key advantages of electrical PVC moulding is its exceptional durability and weather resistance. PVC enclosures are impervious to moisture, corrosion, and temperature fluctuations, making them ideal for outdoor and harsh environment applications.
Cost-effectiveness and Sustainability
PVC moulding offers a cost-effective solution for electrical housing and protection, with low material and labour costs compared to traditional materials such as metal or concrete. Additionally, PVC is recyclable and can be repurposed at the end of its service life, contributing to sustainability and environmental stewardship.
Design Flexibility
The versatility of PVC moulding allows for virtually unlimited design possibilities, enabling architects and designers to create custom enclosures that blend seamlessly into their surroundings. With a wide range of colours, textures, and finishes available, PVC enclosures can complement any aesthetic or architectural style.
Conclusion: Shaping the Future of Electrical Infrastructure
In conclusion, electrical PVC moulding represents a fundamental component of modern electrical infrastructure, offering a versatile, durable, and cost-effective solution for housing and protecting electrical wiring and components. As we look to the future, continued advancements in materials, manufacturing processes, and design techniques promise to further expand the capabilities of PVC moulding, unlocking new opportunities for innovation and creativity in the built environment. By embracing the principles of sustainability, flexibility, and durability, we can shape a future where electrical infrastructure not only meets but exceeds the expectations of our ever-evolving world.
GETTING A QUOTE WITH LK-MOULD IS FREE AND SIMPLE.
FIND MORE OF OUR SERVICES:
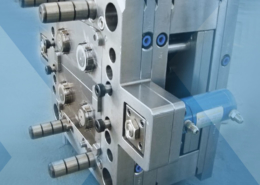
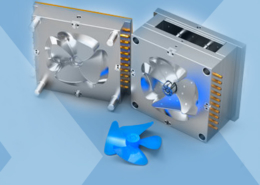
Plastic Molding

Rapid Prototyping
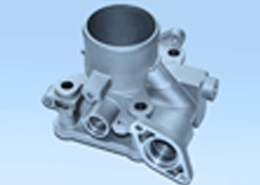
Pressure Die Casting
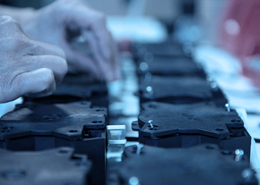
Parts Assembly
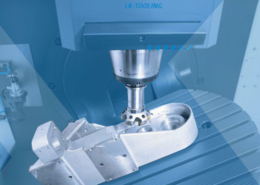