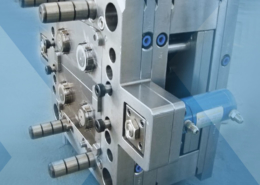
Unveiling the Precision of Ejector Rod Injection Molding: Optimizing Production
Author:gly Date: 2024-06-08
Introduction
Ejector rod injection molding stands as a pinnacle of precision engineering in plastic manufacturing, offering unparalleled control and efficiency in producing intricate components. This article delves into the intricacies of ejector rod injection molding, exploring its mechanisms, advantages, and applications across diverse industries.
Background Overview
Ejector rod injection molding, a subset of conventional injection molding, involves the use of ejector rods to facilitate the removal of molded parts from the mold cavity. This technique enhances the efficiency and reliability of the molding process by ensuring proper ejection of parts, minimizing cycle times, and reducing the risk of damage to delicate features. With advancements in mold design, materials, and automation, ejector rod injection molding has become indispensable in manufacturing high-precision components for automotive, electronics, and medical devices.
Mechanism and Operation
Ejector System Design
The ejector system in injection molding comprises ejector pins or rods, ejector plates, and actuation mechanisms. Ejector rods, typically made of hardened steel, are positioned within the mold cavity and are actuated to push the molded part out of the mold after the cooling phase.
Sequential Ejection
Ejector rod injection molding employs a sequential ejection process, where the ejector rods are activated after the mold has opened and the part has cooled sufficiently. This sequential approach ensures controlled ejection of parts, minimizing the risk of deformation or damage during the ejection phase.
Precision Control
Precision control is essential in ejector rod injection molding to achieve consistent part ejection and maintain dimensional accuracy. Advanced control systems and sensors monitor the ejection process, adjusting parameters such as ejection force, speed, and timing to optimize part quality and production efficiency.
Advantages and Applications
Enhanced Part Quality
Ejector rod injection molding ensures the uniform ejection of parts from the mold cavity, minimizing the risk of surface defects, flash, or distortion. This results in high-quality components with precise dimensions and surface finishes, meeting the stringent requirements of various industries.
Improved Production Efficiency
By streamlining the ejection process, ejector rod injection molding reduces cycle times and increases throughput, improving overall production efficiency. This translates into cost savings and faster time-to-market for manufacturers, enhancing their competitiveness in the market.
Versatility in Design
The use of ejector rods enables greater design freedom and versatility in part geometry and complexity. Manufacturers can incorporate undercuts, thin-walled sections, and intricate features into their designs, expanding the range of applications and functionalities of molded components.
Challenges and Future Directions
Optimization of Ejection Parameters
Continued research and development efforts are focused on optimizing ejection parameters, such as rod design, material selection, and ejection force profiles. Fine-tuning these parameters can further enhance part quality, minimize cycle times, and reduce energy consumption in ejector rod injection molding.
Integration with Industry 4.0
The integration of ejector rod injection molding with digital technologies, such as IoT and machine learning, holds promise for optimizing process control and predictive maintenance. Smart sensors and real-time monitoring systems enable proactive identification of issues and preemptive maintenance, maximizing uptime and productivity.
Materials Innovation
Advancements in materials science are driving the development of novel materials tailored for ejector rod injection molding applications. These materials offer improved wear resistance, thermal stability, and surface finish, enabling manufacturers to push the boundaries of part complexity and performance.
Conclusion
In conclusion, ejector rod injection molding represents a pinnacle of precision engineering and efficiency in plastic manufacturing. By leveraging advanced mechanisms, precision control, and materials innovation, manufacturers can unlock new possibilities for producing high-quality, complex components with unparalleled precision and efficiency. Looking ahead, continued research and collaboration will drive further advancements in ejector rod injection molding, shaping the future of manufacturing and product development.
GETTING A QUOTE WITH LK-MOULD IS FREE AND SIMPLE.
FIND MORE OF OUR SERVICES:
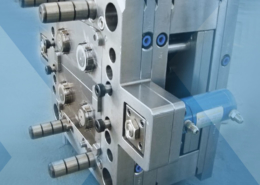
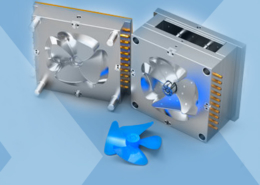
Plastic Molding

Rapid Prototyping
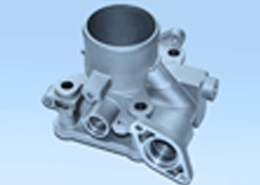
Pressure Die Casting
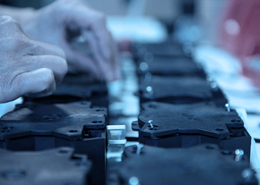
Parts Assembly
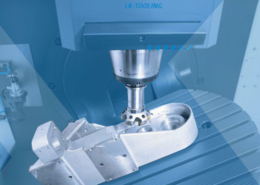