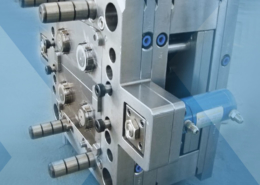
6 Types of Plastic Molding - large plastic molds
Author:gly Date: 2024-10-15
Overmolding uses a special type of plastic injection molding tool, one that has a cavity for the substrate portion and another separate cavity representing the overmolded section.
Overmolding also offers more opportunities to be creative by applying colorful designs to improve the appearance of the part as well as its performance.
Once the base cools and is semi-hardened, the mold is then rotated to a new position and connected to a separate nozzle, gate, and runner system. The remaining void of the mold tool cavity is filled with TPE or TPU elastomer, creating the overmold that bonds to the substrate.
The first conventional injection cycle forms the substrate, using a standard thermoforming resin. This resin fills the gate, runner, and cavity system of only one part of the mold, while the section representing the overmold is blocked.
Get 7-day standard lead times on simple parts between 0.5 in. x 0.5 in. and 4 in. x 3 in. Upload your part to see if it’s eligible.
In this video, Gordon Styles, the founder and President of Star Rapid, goes into greater detail explaining how these processes work, and he gives examples of each. Be sure to check it out for more useful information.
Which process is right for you depends entirely on your application. Keep in mind that they aren’t mutually exclusive molding methods because they serve different purposes. In fact, it’s not uncommon to find both used on a single product. Think, for example, of a power tool that has overmolded grips on the handle, but that also uses nutserts to bolt the case together.
You should consider using insert molding for a few main reasons. The first is that your product application needs strong mechanical fittings to hold two or more parts together, typically for an enclosure or housing. Threaded nutserts are great for this but there are many types of snap connectors as well.
In this article, we discuss insert molding and overmolding, the advantages of each, and the applications they’re best suited for. We hope these manufacturing insights, along with useful design tips, will help you get great results on your next plastic injection molding project.
And overmolding adds cushioning and shock absorption to many common household items that might protect users from accidental injury.
Overmolding is a special form of plastic injection molding. Unlike conventional molding, where a finished product is made in one cycle, overmolding requires at least one additional injection cycle using a dissimilar material. This method is also known as 2K overmolding, two-shot molding, or even multiple material molding.
If the substrate is a plastic base, then it’s customary to mold it in the same production cycle. This is done because it’s more cost-effective to make the entire finished piece at one time, rather than paying to transport and store semi-finished goods. But the more important reason is that the elastomer will adhere much better to a still-warm, semi-cured, and “sticky” substrate.
There are some unique engineering challenges that designers might face when using insert molding. The advantages of added strength and versatility must be weighed against the need for a more careful design for manufacturing review. Here are some useful guidelines to consider:
Inserts can be either male or female. Female inserts are used to make circular fittings inside the surrounding plastic. When these types of inserts have internal threads, they’re called nutserts. There are many advantages to using both male and female inserts to enhance a product’s appearance and utility.
Product developers should consider overmolding in order to improve the grip and texture on parts that need to be held in the hand or to protect the end user against vibration, heat, or electricity. Overmolding is also a great way to permanently bond rubber to metal, as is found on wheels and casters.
Now, if that design logic is applied to a fleet of aircraft or millions of automobiles on an assembly line, then the reduction in weight and cost becomes substantial.
The process is not limited to just two materials, and can theoretically be expanded to include an indefinite number of additional overmolds. However, in practice, more than two becomes increasingly complex and expensive.
Inserts should be used whenever a plastic case needs to be occasionally opened for service and then locked tight again, such as when performing routine maintenance or changing batteries. They cost a little more but that cost is offset by making a much more durable end product.
Insert molding involves placing a pre-manufactured component, such as a threaded fitting or an electrical contact, onto a mounting pin or other fixture in a plastic injection molding tool. During the molding cycle, thermoforming resin surrounds this insert and solidifies, thereby permanently sealing it into place.
This is just a partial overview of insert molding and overmolding. Are they the right solutions for you? Not sure how to apply them to your next project? Just contact our technical experts and we can offer helpful advice about how to get the best results from both processes.
Overmolding starts with a base substrate, on top of which a relatively softer TPE or TPU material is bonded. The base can be metal or plastic, although, in this article, we will focus on plastic applications primarily.
Get 7-day standard lead times on simple parts between 0.5 in. x 0.5 in. and 4 in. x 3 in. Upload your part to see if it’s eligible.
Remember that overmolding is rarely used to cover the entire base substrate. Instead, apply overmolding in sections. For each of these, keep in mind these useful design tips:
We have been manufacturing injection molds and rubber molds since 1978, and we are one of the best mold manufacturers in Taiwan, equipped with advanced CAD/CAM/MACHINE CENTER/SODICK EDM and other equipment and a professional engineering team. From initial product DFM to mold design to complete test shot molds, we are in a position to provide the best molds. With years of experience in producing high-quality molds, our customers come from all over the world, including: the United States, the United Kingdom, Germany, France, Canada, Switzerland, Sweden, Italy and Japan, etc. Believe that our high-quality molds can meet the strict needs of customers.
While there are many advantages to insert molding, there are some potential drawbacks that designers should be aware of.
Neither overmolding nor insert molding is restricted in their use to any particular industry or product type. Because both methods are so useful and adaptable, new practical applications are being found all the time that take advantage of their benefits. Here are a few examples:
To get the best results from this process, product developers should be aware of the following limitations and potential disadvantages.
Insert molding is used to put a rubber or plastic handle on a metal part, such as you might find on hand tools or kitchen knives. And insert molding is ideal for sealing wires and electrical connectors into permanent plastic housings that block out dust and moisture.
Get 7-day standard lead times on simple parts between 0.5 in. x 0.5 in. and 4 in. x 3 in. Upload your part to see if it’s eligible.
GETTING A QUOTE WITH LK-MOULD IS FREE AND SIMPLE.
FIND MORE OF OUR SERVICES:
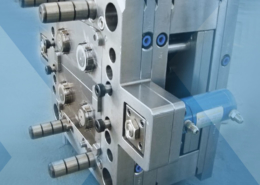
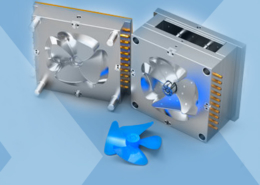
Plastic Molding

Rapid Prototyping
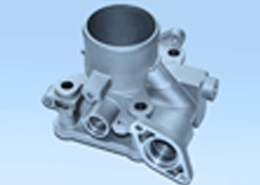
Pressure Die Casting
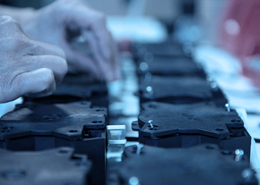
Parts Assembly
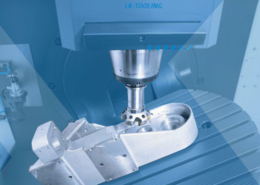