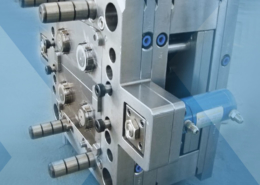
6 Types of Plastic Molding - mold and plastic
Author:gly Date: 2024-10-15
Medical injection molding is a plastic molding and manufacturing process involving liquefied plastic into a mold to create plastic products of various shapes and sizes. In this process, the plastic is allowed to conform to the shape of the mold and harden to produce the desired finished product.
Please contact us if you would like to receive a quotation and/or to find our more about how we can provide the service you are looking for.
By employing advanced medical injection molding in our manufacturing process, we are able to supply high volumes of medical components without sacrificing quality while meeting your target specifications.
If your smartphone has a clear, durable casing, it's likely made of polycarbonate. This thermoplastic polymer is a popular material among plastic parts, components, and products manufacturers. Its qualities, such…
We at Stephens Plastic are always looking for ways to improve our performance. That means working closely with and of our customers during the process, from design and prototyping to post-production and delivery, to ensure that they receive high-quality parts manufactured on a budget and delivered on time. Contact us today to learn more about how we can bring your ideas to life.
All-Plastics has expertise in providing cost-saving, high quality injection molding solutions to the Medical Device industry. Our expertise in medical injection molding allow us to support tight tolerance micro-sized components to complete medical devices.
Some of the cookies we use are essential for the site to work. We also use some non-essential cookies to collect information for making reports and to help us improve the site. The cookies collect information in an anonymous form. To control third party cookies, you can also adjust your browser settings.
Low-volume injection moulding uses softer aluminium moulds and inserts instead of hardened steel ones, which are usually simpler and less expensive to produce. These moulds are obviously not as durable as their hardened steel counterparts, but manufacturers benefit because they don’t always need to be when manufacturing low-volume components. Soft moulds, when used strategically, can lower tooling costs and shorten production times.
All-Plastics works with a variety of medical industries to provide injection molding services to help create, design, and mold custom applications and parts. Some of the medical markets we serve are:
Our Low Volume Injection Moulding is a specialised service that provides complete production-quality parts in quantities of 10,000 or less bits, depending on the method. Our low-volume moulding, also known as short runs, is closely supervised and regulated to ensure that all aspects of mould design and construction are met. Small and medium-sized companies, as well as small-batch manufacturing, benefit from this form of production.
All-Plastics employs a state-of-the-art plastic injection molding process in order to produce high-quality medical products that meet the strict guidelines set by regulatory bodies. This ensures the safety and efficiency of all manufactured medical products and tools, which include:
Our experts provide Project Management solutions from Concept to Operational Excellence, including full program documentation and component traceability. REQUEST A QUOTE
All-Plastics caters to your need for durable plastic medical components that comply with strict FDA standards and regulations.
Injection molding is one of the most widely used manufacturing processes, capable of producing intricate plastic parts with high precision. However, like any industrial process, it has its challenges, and…
Material selection and method of production are always key considerations in the manufacturing of products, devices, and components for the medical industry. This is because of the strict regulations and standards that govern the industry. Plastic injection molding meets these requirements and offers a wide range of benefits for the medical industry.
Another important advantage of using softer injection moulds is that they rarely have a negative impact on component quality: when proper design requirements are taken into account, plastic parts made in low quantities are just as good as those produced using hardened steel moulds.
Stephens Plastic has the expertise, knowledge, and experience to provide just what you need, whether it’s 10 or 100,000 plastic parts, thanks to its ability to provide both low and high volume injection moulding.
Our expertise in plastic injection moulding helps us to provide a complete turn-key solution for your plastic manufacturing needs, whether it’s an automotive part for bespoke custom builds or prototype construction for healthcare system components.
At the same time, hardened steel, which is needed for conventional moulds, requires a substantial upfront time and financial investment. Moulds made of aluminium or lower-grade steel, on the other hand, are much less costly to make and can be made far quicker. Manufacturers may use these moulds to test and produce viable parts without having to commit to large minimum orders, allowing them to fine-tune component design and production as required. This enables producers to start manufacturing faster and, in many cases, greatly increase speed-to-market, reducing the time it takes to see a return on investment.
Our medical plastic injection molding and clean room molding production solutions that increase quality, security and provide cost advantages for the Medical Market are:
We have been established for many years and with our young and vibrant management team have vast experience in all aspects of plastic injection moulding – from the design stages through to the final packaged product.
GETTING A QUOTE WITH LK-MOULD IS FREE AND SIMPLE.
FIND MORE OF OUR SERVICES:
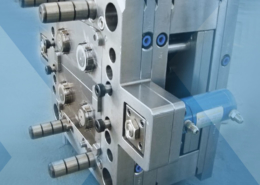
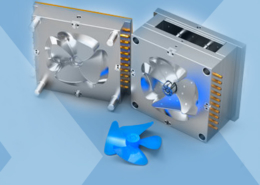
Plastic Molding

Rapid Prototyping
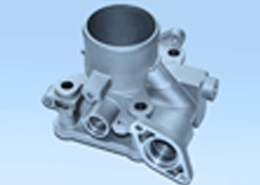
Pressure Die Casting
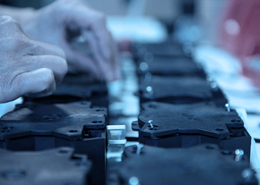
Parts Assembly
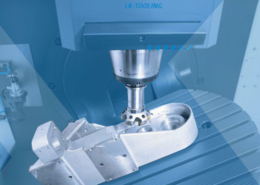