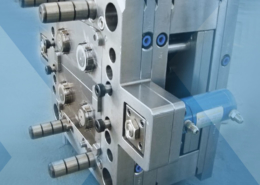
Exploring Benchtop Injection Molding: Revolutionizing Prototyping and Small-Scal
Author:gly Date: 2024-06-08
Introduction
Benchtop injection molding stands at the forefront of innovation, revolutionizing prototyping and small-scale production. This technology offers a compact, efficient solution for manufacturing plastic parts with precision and speed. As the demand for rapid prototyping and low-volume production rises across various industries, understanding the intricacies and advantages of benchtop injection molding becomes paramount.
Background Overview
Benchtop injection molding, also known as tabletop injection molding, refers to the process of injecting molten plastic into a mold cavity to create precise plastic parts. Unlike traditional injection molding machines, which are large and typically used for mass production, benchtop machines are smaller, more affordable, and suitable for prototyping and small-scale production runs.
Advantages
Benchtop Convenience
Benchtop injection molding offers unparalleled convenience, allowing businesses and hobbyists alike to produce custom plastic parts in-house. With its compact size and user-friendly interface, benchtop machines eliminate the need for outsourcing and reduce lead times significantly.
Cost-Effectiveness
The affordability of benchtop injection molding machines democratizes access to plastic manufacturing. Small businesses and startups can now prototype and produce plastic parts without breaking the bank, accelerating the product development cycle and fostering innovation.
Versatility and Flexibility
Despite their size, benchtop injection molding machines offer versatility in material selection and mold design. From thermoplastics to elastomers, these machines can accommodate a wide range of materials, catering to diverse application requirements.
Process Overview
Injection Phase
During the injection phase, the thermoplastic material is heated and injected into the mold cavity under high pressure. This process ensures that the material fills the mold completely, resulting in precise and accurate plastic parts.
Cooling and Solidification
After injection, the mold cools rapidly, causing the molten plastic to solidify and take the shape of the mold cavity. Proper cooling is crucial for achieving dimensional accuracy and minimizing defects in the final product.
Ejection
Once the plastic has solidified, the mold opens, and the finished part is ejected from the mold cavity. This step marks the completion of the injection molding cycle, and the process can be repeated to produce additional parts.
Applications
Prototyping
Benchtop injection molding is widely used for prototyping new product designs, allowing designers and engineers to test concepts quickly and iterate on designs without the high costs associated with traditional tooling.
Low-Volume Production
In addition to prototyping, benchtop injection molding is ideal for low-volume production runs. From medical devices to consumer electronics, businesses can produce small batches of plastic parts with precision and consistency.
Educational Use
Benchtop injection molding serves as an invaluable educational tool for teaching students about manufacturing processes, material properties, and design considerations. Its accessibility and hands-on nature make it an effective learning platform for aspiring engineers and designers.
Challenges and Future Directions
Quality Control
Ensuring consistent part quality remains a challenge in benchtop injection molding. Addressing issues such as shrinkage, warping, and surface defects requires ongoing research and development efforts to optimize process parameters and material selection.
Automation and Integration
As technology advances, integrating automation features into benchtop injection molding machines can enhance productivity and efficiency. Future developments may focus on incorporating robotics, machine learning, and IoT connectivity to streamline the manufacturing process further.
Sustainability
Promoting sustainability in benchtop injection molding involves exploring alternative materials, reducing energy consumption, and optimizing waste management practices. Embracing eco-friendly initiatives will be crucial for minimizing the environmental impact of plastic manufacturing.
Conclusion
In conclusion, benchtop injection molding represents a paradigm shift in plastic manufacturing, offering a compact, cost-effective solution for prototyping and low-volume production. Its versatility, convenience, and accessibility make it a valuable asset for businesses, educators, and enthusiasts alike. However, addressing challenges such as quality control and sustainability will be essential for unlocking the full potential of this technology. By embracing innovation and collaboration, the future of benchtop injection molding holds promise for revolutionizing product development and shaping the manufacturing landscape.
GETTING A QUOTE WITH LK-MOULD IS FREE AND SIMPLE.
FIND MORE OF OUR SERVICES:
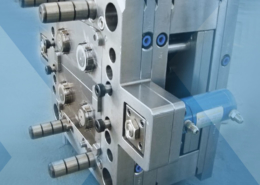
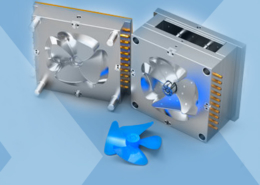
Plastic Molding

Rapid Prototyping
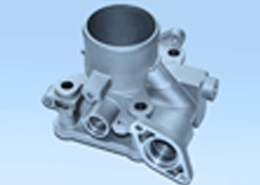
Pressure Die Casting
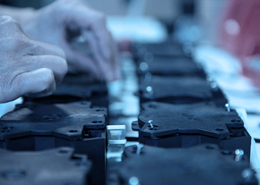
Parts Assembly
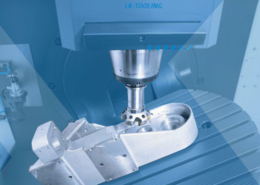