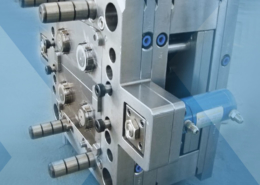
Unveiling the Innovations of Back Injection Molding: Enhancing Product Design an
Author:gly Date: 2024-06-08
Introduction
Back injection molding, a sophisticated technique in the realm of plastic manufacturing, has garnered significant attention for its ability to create complex, multi-material components with unparalleled precision and efficiency. This article explores the intricacies of back injection molding, delving into its applications, advantages, and potential for revolutionizing product design across various industries.
Background Overview
Back injection molding, also known as two-shot or multi-shot molding, involves injecting multiple materials into a single mold cavity to produce intricate components with diverse properties. This process enables manufacturers to integrate different materials, colors, and textures seamlessly, expanding the possibilities for product design and functionality. With advancements in technology and materials, back injection molding has emerged as a preferred choice for creating high-performance, visually appealing products in automotive, electronics, and consumer goods sectors.
Process Dynamics
Sequential Injection
In back injection molding, the process typically involves injecting the first material into the mold cavity, followed by a second material to form the final part. The sequence and timing of injections are critical to achieving precise alignment and adhesion between different materials, ensuring optimal performance and aesthetics of the finished product.
Mold Design Considerations
Designing molds for back injection molding requires meticulous attention to detail, including gate locations, parting lines, and material compatibility. Complex mold configurations, such as core pulls and slides, may be necessary to accommodate the geometry and functionality of the desired component.
Material Selection
Selecting compatible materials is paramount in back injection molding to ensure proper bonding and adhesion between layers. Factors such as material properties, shrinkage rates, and processing conditions must be carefully evaluated to achieve the desired performance and appearance of the final part.
Advantages and Applications
Enhanced Design Freedom
Back injection molding offers unparalleled design freedom, enabling manufacturers to create intricate geometries, textures, and surface finishes that are unattainable with traditional molding techniques. This flexibility allows for the integration of functional features, branding elements, and aesthetic enhancements in a single manufacturing step.
Improved Product Performance
By combining different materials with complementary properties, back injection molding enhances the performance and functionality of products. For example, incorporating soft-touch materials with rigid substrates in automotive interiors improves ergonomics and comfort for passengers while maintaining structural integrity and durability.
Cost Efficiency
Despite its complexity, back injection molding can streamline the manufacturing process by consolidating multiple production steps into a single operation. This leads to cost savings in terms of labor, material usage, and cycle time, making it an economically viable solution for producing high-value, multi-material components.
Challenges and Future Directions
Process Optimization
Optimizing process parameters, such as injection pressures, temperatures, and cooling rates, is crucial for achieving consistent quality and performance in back injection molding. Research efforts focus on developing advanced simulation tools and process monitoring techniques to enhance process control and predictability.
Material Innovation
Continued innovation in materials is essential for expanding the capabilities of back injection molding and addressing evolving market demands. Research initiatives aim to develop new formulations, composites, and additives tailored to the specific requirements of multi-material applications, such as improved adhesion, UV resistance, and recyclability.
Integration with Industry 4.0
The integration of back injection molding with digital technologies, such as IoT, AI, and robotics, holds promise for enhancing productivity, quality, and sustainability. Smart manufacturing solutions enable real-time monitoring of process parameters, predictive maintenance, and data-driven decision-making, optimizing overall manufacturing efficiency.
Conclusion
In conclusion, back injection molding represents a paradigm shift in plastic manufacturing, offering unparalleled versatility, performance, and efficiency in creating complex, multi-material components. By leveraging advanced process technologies, material innovations, and digital integration, manufacturers can unlock new possibilities for product design and functionality across diverse industries. Looking ahead, ongoing research and collaboration will drive further advancements in back injection molding, shaping the future of manufacturing and product development.
GETTING A QUOTE WITH LK-MOULD IS FREE AND SIMPLE.
FIND MORE OF OUR SERVICES:
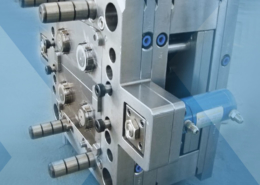
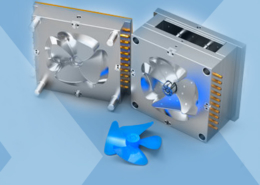
Plastic Molding

Rapid Prototyping
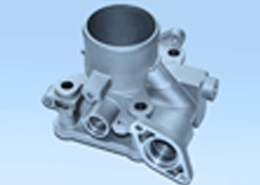
Pressure Die Casting
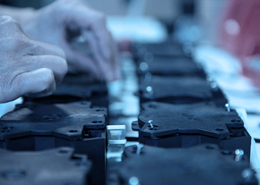
Parts Assembly
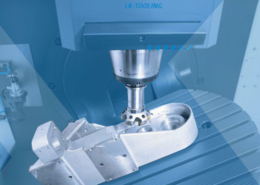