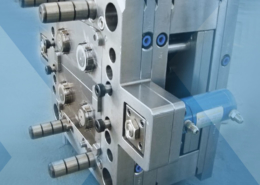
Revolutionizing Automotive Manufacturing Through Injection Molding
Author:gly Date: 2024-06-08
Introduction
In the dynamic landscape of automotive manufacturing, injection molding stands as a cornerstone technology, driving innovation, efficiency, and quality. This article delves into the realm of automotive injection molding, exploring its significance, evolution, and transformative impact on vehicle production. From interior components to exterior body panels, injection molding techniques have revolutionized the way automobiles are designed, manufactured, and experienced.
Unveiling the Essence of Automotive Injection Molding
Automotive injection molding embodies a sophisticated manufacturing process wherein molten materials, typically polymers, are injected into a pre-designed mold cavity. The process enables the rapid and cost-effective production of complex geometries with high precision and consistency. From dashboard panels to door handles, virtually every aspect of modern vehicles benefits from the versatility and efficiency of injection molding technology.
The Evolution of Automotive Injection Molding
Over the decades, automotive injection molding has undergone significant evolution, propelled by advancements in materials, machinery, and manufacturing techniques. Early iterations of injection molding in automotive applications focused primarily on interior components, such as trim panels and upholstery. However, with the advent of lightweight materials, advanced engineering plastics, and novel molding technologies, injection molding now extends its reach to exterior body panels, structural components, and even under-the-hood parts.
Enhancing Vehicle Performance and Aesthetics
The integration of injection-molded components enhances both the performance and aesthetics of modern vehicles. Lightweight yet durable materials contribute to fuel efficiency and agility, while precise molding techniques ensure optimal fit and finish. Furthermore, the versatility of injection molding allows for intricate designs, textures, and surface finishes, enabling automakers to differentiate their products and captivate consumers with visually appealing interiors and exteriors.
Driving Sustainability in Automotive Manufacturing
Sustainability has emerged as a central theme in the automotive industry, and injection molding plays a pivotal role in driving eco-friendly practices. The use of recyclable and biodegradable materials, coupled with efficient manufacturing processes, reduces environmental impact and promotes a circular economy. Moreover, lightweight components contribute to vehicle fuel efficiency and emissions reduction, aligning with global sustainability goals.
Challenges and Future Directions
Despite its numerous advantages, automotive injection molding faces challenges, including material selection, design complexity, and manufacturing scalability. Addressing these challenges requires ongoing research and innovation in material science, process optimization, and automation technology. Looking ahead, the convergence of additive manufacturing, digital design tools, and AI-driven optimization holds the potential to further revolutionize automotive injection molding, unlocking new possibilities in design freedom, cost efficiency, and sustainability.
Conclusion
In conclusion, automotive injection molding stands as a testament to human ingenuity and technological advancement. Its transformative impact on vehicle manufacturing is evident in every aspect of modern automobiles, from the structural integrity to the aesthetic appeal. As the automotive industry continues to evolve, injection molding remains a driving force behind innovation, enabling automakers to push the boundaries of design, performance, and sustainability. Embracing emerging technologies and sustainable practices will shape the future of automotive injection molding, paving the way for a more efficient, environmentally friendly, and visually stunning automotive landscape.
GETTING A QUOTE WITH LK-MOULD IS FREE AND SIMPLE.
FIND MORE OF OUR SERVICES:
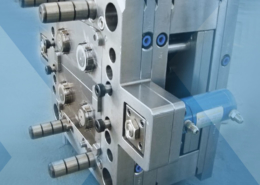
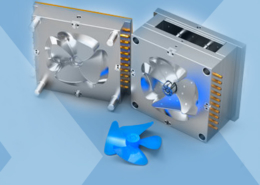
Plastic Molding

Rapid Prototyping
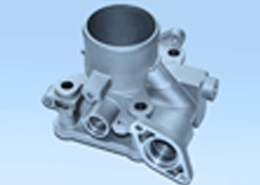
Pressure Die Casting
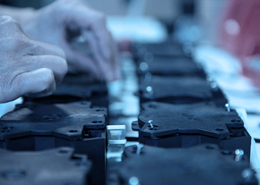
Parts Assembly
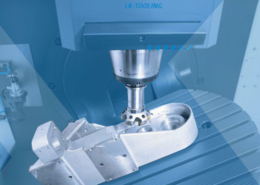