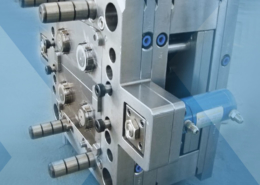
Exploring the Best Plastics for Machining: A Comprehensive Guide
Author:gly Date: 2024-06-08
Machining plastics requires a delicate balance of material properties, tooling considerations, and machining techniques to achieve optimal results. In this article, we delve into the world of machining plastics, exploring the best materials for the job, key considerations in machining processes, and the future of plastic machining technologies.
Introduction: Unlocking the Potential of Machining Plastics
Machining plastics offer unique advantages in various industries, from aerospace and automotive to medical devices and consumer electronics. Unlike metals, plastics come in a wide range of formulations, each with its own set of properties that impact machinability. The selection of the right plastic material is crucial for achieving precise, high-quality machined components.
Key Properties of Machinable Plastics
Mechanical Properties
The mechanical properties of plastics, such as hardness, tensile strength, and impact resistance, play a vital role in determining their machinability. Materials with high hardness and strength are typically more challenging to machine but offer better dimensional stability and durability in the finished parts.
Thermal Stability
Thermal stability is essential in machining plastics to prevent deformation, melting, or degradation of the material during cutting operations. Plastics with high heat resistance can withstand the elevated temperatures generated during machining processes, resulting in improved surface finish and dimensional accuracy.
Chemical Resistance
Chemical resistance is critical, especially in industries where machined parts are exposed to harsh environments or corrosive substances. Plastics that exhibit excellent chemical resistance ensure long-term performance and reliability of the machined components in challenging operating conditions.
Best Plastics for Machining Applications
Acrylic (PMMA)
Acrylic, also known as polymethyl methacrylate (PMMA), is a versatile plastic prized for its optical clarity, high impact strength, and ease of machining. It is commonly used in signage, displays, and optical components due to its excellent surface finish and dimensional stability. Acrylic machines well with conventional cutting tools and can be polished to a high gloss for aesthetic applications.
Polyethylene (PE)
Polyethylene is a lightweight, chemically resistant plastic widely used in machining applications where low friction and wear resistance are required. It is available in various forms, including high-density polyethylene (HDPE) and ultra-high molecular weight polyethylene (UHMWPE), each offering unique properties for specific machining requirements. Polyethylene is commonly used in food processing equipment, conveyor components, and wear-resistant parts.
Polypropylene (PP)
Polypropylene is a versatile thermoplastic with excellent chemical resistance, low moisture absorption, and good dimensional stability, making it suitable for a wide range of machining applications. It is used in industries such as automotive, packaging, and medical devices for components requiring resistance to chemicals, moisture, and fatigue.
Challenges and Considerations in Machining Plastics
Tool Selection and Geometry
Choosing the right cutting tools and tool geometries is critical for achieving efficient and precise machining of plastics. Sharp cutting edges, high rake angles, and minimal clearance angles help minimize heat generation, chip buildup, and tool wear during machining operations.
Chip Control and Cooling
Effective chip control and cooling are essential in plastic machining to prevent chip adhesion, tool rubbing, and thermal damage to the workpiece. Techniques such as air blast, vacuum evacuation, and flood cooling help evacuate chips and dissipate heat from the cutting zone, improving surface finish and prolonging tool life.
Workholding and Fixturing
Proper workholding and fixturing techniques are necessary to secure the workpiece and minimize vibration and deflection during machining. Clamping methods that distribute clamping forces evenly and avoid excessive pressure on the workpiece help maintain dimensional accuracy and surface finish in machined parts.
Future Trends and Innovations
Advanced Machining Technologies
Advancements in machining technologies, such as high-speed machining, ultrasonic machining, and laser machining, offer new opportunities for enhancing productivity, precision, and surface finish in plastic machining applications. These technologies enable faster material removal rates, finer feature resolution, and reduced machining forces, opening doors to new possibilities in complex part manufacturing.
Sustainable Materials and Processes
The growing emphasis on sustainability is driving research and development efforts towards eco-friendly materials and machining processes. Biodegradable plastics, recycled materials, and energy-efficient machining techniques are gaining traction as industries seek to minimize environmental impact and carbon footprint in manufacturing operations.
Conclusion: Navigating the Complexities of Machining Plastics
In conclusion, machining plastics present a myriad of opportunities and challenges for manufacturers across industries. By understanding the key properties of machinable plastics, selecting the appropriate materials, and implementing best practices in machining processes, manufacturers can achieve optimal results in terms of quality, efficiency, and sustainability.
As we look towards the future, continued research and innovation in materials science, machining technologies, and sustainable practices will shape the landscape of plastic machining, paving the way for new applications, improved performance, and reduced environmental footprint. Through collaboration and ongoing advancements, we can unlock the full potential of machining plastics and drive positive change in the manufacturing industry.
GETTING A QUOTE WITH LK-MOULD IS FREE AND SIMPLE.
FIND MORE OF OUR SERVICES:
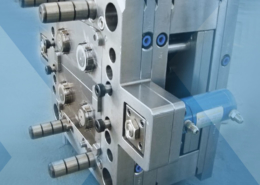
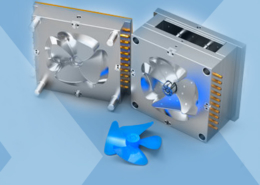
Plastic Molding

Rapid Prototyping
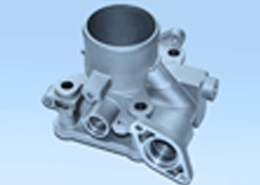
Pressure Die Casting
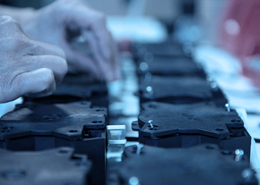
Parts Assembly
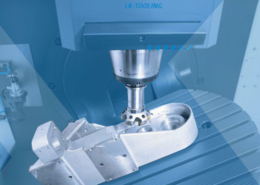