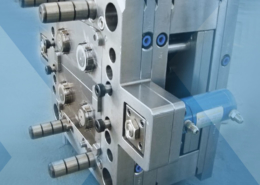
World First: Manufacturer Runs 128-Cavity Mold in 1.9-second Cycle Time - plasti
Author:gly Date: 2024-09-30
Plastics Technology’s Tech Days is back! Every Tuesday in October, a series of five online presentations will be given by industry supplier around the following topics: Injection Molding — New Technologies, Efficiencies Film Extrusion — New Technologies, Efficiencies Upstream/Downstream Operations Injection Molding — Sustainability Extrusion — Compounding Coming out of NPE2024, PT identified a variety of topics, technologies and trends that are driving and shaping the evolution of plastic products manufacturing — from recycling/recyclability and energy optimization to AI-based process control and automation implementation. PT Tech Days is designed to provide a robust, curated, accessible platform through which plastics professionals can explore these trends, have direct access to subject-matter experts and develop strategies for applying solutions in their operations.
New conductive technologies are emerging, one being a class of polymers intrinsically able to carry a current along their polymer chains. Inherently Conductive Polymers and Inherently Dissipative Polymers (ICPs and IDPs) differ in the range of conductivity they impart and the mechanism involved. Both categories are now melt-processable and thus highly efficient at creating conductive networks when alloyed with a thermoplastic matrix polymer.
Cevolution’s fiber will be made with a continuous process that is capable of very high productivity and uses relatively low-cost feedstocks. The raw form is a randomly oriented, continuous-filament mat, but user-friendly forms (chopped and milled fibers and needled mat) are being developed.
Implementing a production monitoring system as the foundation of a ‘smart factory’ is about integrating people with new technology as much as it is about integrating machines and computers. Here are tips from a company that has gone through the process.
Despite price increase nominations going into second quarter, it appeared there was potential for generally flat pricing with the exception of a major downward correction for PP.
Engel combined two-component molding with IML in an unusual sequence. Thin-walled lids for ice-cream containers were molded on an e-motion 200 T US combi all-electric machine. Using a core-back process, the machine first injected the colored frame, then the label was placed in the same mold and the clear center panel of the lid was molded over the label.
Designing a thermoplastic compound to conduct an electrical charge is difficult and costly, since most polymers are naturally ill suited to the task. Plastics generally have surface resistivities of 1012 ohm/sq or higher, which puts them at the insulative end of the electrical spectrum (see graph). That is advantageous in many uses, but is a liability in others. Indeed, some degree of electrical conductivity is critical to a growing number of plastics applications.
In a time where sustainability is no longer just a buzzword, the food and beverage packaging industry is required to be at the forefront of this innovation. By adopting circular packaging processes and solutions, producers can meet regulatory requirements while also satisfying consumer demand and enhancing brand reputation. Join Husky to learn more about the broader implications of the circular economy — as well as how leading brands are leveraging this opportunity to reduce costs, increase design flexibility and boost product differentiation. Agenda: The cost and operational benefits of embracing circularity Key materials in circular packaging — including rPET and emerging bioplastics How to design a circular food and beverage package Strategies for selecting sustainable closures to future-proof packaging solutions Optimization and streamlining of production processes for enhanced efficiency How Husky Technologies can enable your sustainable success
Ube’s other new series is the UU2e Fusion line of two-platen hybid machines. Built in the U.S. and spanning 1100 to 2200 tons, these machines use multiple servomotors and gear pumps to drive the hydraulic pumps. There is also a servomotor and ballscrew for clamp traverse motions, so hydraulic screw recovery can run in parallel with clamp opening and closing. Modular design lets users choose a clamp, injection unit, servomotors, and gear pumps according to their needs. These units also have the same e-HUMMA controller and Flex Servo technology as the UF electric series.
This month’s resin pricing report includes PT’s quarterly check-in on select engineering resins, including nylon 6 and 66.
More speed, more power, more precision, and more automated functions accomplished in and out of the mold. That’s exactly what injection machinery suppliers were offering at NPE2012.
Plastics Technology covers technical and business Information for Plastics Processors in Injection Molding, Extrusion, Blow Molding, Plastic Additives, Compounding, Plastic Materials, and Resin Pricing. About Us
Cost is the major limit on nano-tube use, as Hyperion’s fibrils are priced at around $50/lb. Over the long haul, Collins argues, the start-up of world-scale plants will bring prices down.
Swedish compounders HEXPOL TPE AB and Polykemi AB have collaborated on a 2K sustainable development project for consumer products.
Engel demonstrated 64-cavity, flashless molding of a medical diaphragm using cold-runner valve gates on a 7-sec cycle—very fast for LSR. The e-victory 130-ton hybrid had ecodrive servo-driven hydraulics and a servo-driven screw. Because the runner was cooled right up to the gate, the mold could be run hotter (410 F vs. the typical 350-360 F) for faster cycles. The moldmaker, ACH Solution from Austria also supplied a top-entry, servo-driven mold sweep that demolded all 64 parts faster than would be possible with a pneumatic sweep. The sweep consisted of an aluminum brush that was positioned 0.015 in. away from the mold face. Automated deflashing was also integrated into the cell.
New type of pitch-based carbon fiber, soon to be commercialized by Conoco Cevolution offers higher conductivity and stiffness than other carbon fibers while remaining at the low end of the price scale. (Photo: Conoco)
Mold maintenance is critical, and with this collection of content we’ve bundled some of the very best advice we’ve published on repairing, maintaining, evaluating and even hanging molds on injection molding machines.
The aim of this presentation is to guide you through the factors and the numbers that will help you determine if a robot is a smart investment for your application. Agenda: Why are you considering automation? What problems are you trying to solve? How and why automation can help Crunch the numbers and determine the ROI
Mike Sepe has authored more than 25 ANTEC papers and more than 250 articles illustrating the importance of this interdisciplanary approach. In this collection, we present some of his best work during the years he has been contributing for Plastics Technology Magazine.
A novel pitch-based carbon fiber developed by Conoco Cevolution will be manufactured at a 4-million-lb/yr plant in Ponca City, Okla., due to come on stream in the second quarter of this year. Samples are already available. Eduardo Romero, industry manager for electrical/electronics, says Cevolution’s mesophase pitch fiber offers an order of magnitude higher electrical conductivity than PAN-type carbon fibers and significantly greater stiffness as well. The stiffness can be tailored to specific end-uses. Other benefits are outstanding purity and high thermal conductivity. These fibers will be priced to compete with PAN fibers in some applications. Romero sees potential in ESD, EMI shielding, e-paintable auto parts, and fuel-cell plates.
In this three-part collection, veteran molder and moldmaker Jim Fattori brings to bear his 40+ years of on-the-job experience and provides molders his “from the trenches” perspective on on the why, where and how of venting injection molds. Take the trial-and-error out of the molding venting process.
While the melting process does not provide perfect mixing, this study shows that mixing is indeed initiated during melting.
Milacron demonstrated the PowerPAK’s suitability for high-speed, high-volume stack-mold applications: A 550-tonner with two-stage, screw/plunger electric injection unit molded thin-wall PP lids in a 2 x 4-cavity stack mold on a 4.8-sec cycle. The machine had stack-mold support shoes and “greaseless” tiebars—said to be unusual for all-electric stack-mold operation.
Hot buttons at the show will be multi-component molding, in-mold labeling/decorating (IML/IMD), in-mold assembly, medical molding, liquid silicone rubber (LSR), micro-molding, and high-speed packaging.
KraussMaffei also announced that it installed an R&D system at Toronto University, consisting of an MX injection molding compounder with a twin-screw compounding extruder feeding a plunger injection unit. This system can feed, chop, and compound continuous glass rovings, and also has MuCell capability, making it the first in the world to produce foamed long-glass parts direct from raw fiber.
Gifted with extraordinary technical know how and an authoritative yet plain English writing style, in this collection of articles Fattori offers his insights on a variety of molding-related topics that are bound to make your days on the production floor go a little bit better.
Resin drying is a crucial, but often-misunderstood area. This collection includes details on why and what you need to dry, how to specify a dryer, and best practices.
Sumitomo’s new El-Exis SP hybrid for ultra-high speed and precision has an accumulator with bigger valves, hoses, motor, and pump to provide 1000 mm/sec injection but also more precise transitions from boost to hold stages. It’s available from 165 to 825 tons and has linear bearings instead of tiebar bushings, eliminating wear on tiebars. At the show, a 500-tonner molded 1-g HDPE bottle caps in a 96-cavity Schottli hot-runner mold on a 1.98-sec cycle. The waterfall of caps leaving the mold became a horizontal blur as they were fed to a conveyor for 100% QC inspection by an IMDVista vision inspection system from IMD Ltd. in Switzerland. It inspected all caps for short shots, color, flash, ovality, and contamination.
EMS-Grivory is also compounding nickel and zinc ferrite powders into nylon 12 and high-temperature nylons for use in “soft” magnets. These molded devices become magnetized in the presence of a current, thereby providing EMI protection for air-bag connectors and other sensitive control elements. Polymer magnets are more durable than the sintered magnets they replace, and also offer greater design freedom and the potential for lower-cost manufacture and assembly. Polymer magnets could also provide EMI protection to computers and appliances, Riffer says.
Designing a thermoplastic compound to conduct an electrical charge is difficult and costly, since most polymers are naturally ill suited to the task.
Resin drying is a crucial, but often-misunderstood area. This collection includes details on why and what you need to dry, how to specify a dryer, and best practices.
In this collection of content, we provide expert advice on welding from some of the leading authorities in the field, with tips on such matters as controls, as well as insights on how to solve common problems in welding.
In this collection, which is part one of a series representing some of John’s finest work, we present you with five articles that we think you will refer to time and again as you look to solve problems, cut cycle times and improve the quality of the parts you mold.
While prices moved up for three of the five commodity resins, there was potential for a flat trajectory for the rest of the third quarter.
Teknor Apex's Plastics Div. recently launched a family of flexible vinyl compounds designed for consistent ESD and EMI performance. Carbon-black-filled Vidux PVCs offer 100 to 108 ohm-cm volume resistivity in cable jackets, flooring, grounding mats, shielding, and other items used in cleanrooms, hospitals, and factories. At under $2/lb, they are said to be more cost-effective than alternatives based on carbon or steel fibers.
Bayer has concluded that blends of various carbon-based conductive additives, including Hyperion’s nano-tubes are a cost-effective way to tackle e-painting needs. Indeed, compatibilized blends of carbon additives are employed in new 30%-glass nylon 6 and TP polyester molding compounds that reportedly provide superior surface smoothness in door handles, fuel flaps, and large exterior auto parts.
The IMDVista system played a similar role in Engel’s booth, providing 100% inspection of HDPE water-bottle caps from a Plastisud 96-cavity mold. A 460-ton, all-electric Engel e-cap machine ran a 2.7-sec cycle without benefit of an accumulator, achieving very low energy utilization of 0.4 kwh/kg. Cam-operated mechanical slides for the tamper-evident band eliminated the need for a core pull.
Learn about sustainable scrap reprocessing—this resource offers a deep dive into everything from granulator types and options, to service tips, videos and technical articles.
Hyperion's multi-wall graphite nano-tubes have 10-nm OD and are 10 to 100 microns long, for at least a 1000:1 aspect ratio. The small size and curvilinear shape of these “fibrils” makes them difficult to disperse in plastics. To ensure satisfactory dispersion, Hyperion supplies the fibrils in pelletized masterbatches containing 15-20% fibrils, which can be let down to as little as 0.5% by weight.
Baystar's Borstar technology is helping customers deliver better, more reliable production methods to greenhouse agriculture.
Gifted with extraordinary technical know how and an authoritative yet plain English writing style, in this collection of articles Fattori offers his insights on a variety of molding-related topics that are bound to make your days on the production floor go a little bit better.
Suppliers of nano-carbons include Hyperion Catalysis, the sole commercial supplier in North America; Japan's Mitsui and Showa Denko; and an Applied Sciences affiliate, Pyrograf Products. The latter's developmental graphite nano-fiber is 100-200 nm in diam. x 100 microns long, giving it a 500-1000:1 aspect ratio. It's available in sample quantities at $70/lb. (A semi-works plant is being built.) At loadings of 0.5% to 5% by volume, Pyrograf's PF24 carbon nano-fiber boosts stiffness of plastics by 500% and drops their surface resistivity to the range of 1 to 1010 ohm/sq.
Formnext Chicago is an industrial additive manufacturing expo taking place April 8-10, 2025 at McCormick Place in Chicago, Illinois. Formnext Chicago is the second in a series of Formnext events in the U.S. being produced by Mesago Messe Frankfurt, AMT – The Association For Manufacturing Technology, and Gardner Business Media (our publisher).
Also new from Milacron is the Varian Turntable, a rotary platen for multi-shot molding. Servo drive makes it faster and more precise. It’s also grease-free. It comes in seven standard sizes to fit machines from 330 to 3300 tons.
The new concept of “3D IML” won the Emerging Technologies award in the SPI’s International Design Competition. It uses Trexel’s MuCell microcellular foaming process. Selective application of a barrier coating traps the foaming gas behind the logo lettering, giving it a raised, soft-touch feel.
PolyOne’s Stat-Tech slate includes some 20 base resins and spans a range from 1 to 1012 ohm/sq surface resistivity. Some of the less conventional matrices now being used include nitrile-rubber-modified PVC, polysulfone, and various TPEs. PolyOne is exploring use of metalized glass fiber to enhance electrical and thermal conductivity and provide reinforcement.
Niigata (niigata-us.com) had a new-generation all-electric line at the show. The MD-S6000 series comprises smaller models (55 to 150 tons), while the MD-W6000 series is medium-to-large sizes from 200 to 1100 tons. These units have wider tiebar spacing and updated controls with more user-programmable features.
Exhibitors and presenters at the plastics show emphasized 3D printing as a complement and aid to more traditional production processes.
KraussMaffei, emphasized multi-component molding and in-mold assembly at the show with its SpinForm “swivel-platen” system. The firm reported that it has sold two 4400-ton, double SpinForm systems with two turning stacks to BMW in Leipzig, Germany. They will produce polyolefin structural components for electric cars next year. The system is equipped with two six-axis robots, a second injection unit in an “L” configuration, and an oven station. The system will mold an outer skin and a substructure and then, as the stacks rotate, heat-weld them together in the mold, along with a third component.
Noveon (formerly part of BFGoodrich) has developed an IDP that works in the 106 to 1011 ohm/sq surface resistivity range, offering permanent static control. Noveon uses this IDP exclusively in its own Stat-Rite compounds for injection molding and extrusion. IDPs are generally elastomers (Noveon's is a TP urethane) that contain "charge-carrying blocks" able to conduct current, but in a more restricted part of the antistatic and ESD spectrum than is covered by ICPs. In some cases, the hydrophilic nature of an IDP helps boost conductivity at the part surface. In the past, thermal-stability limits confined IDP use to low-temperature matrix resins like HIPS, PETG, ABS, and TPU, but Noveon has recently expanded its Stat-Rite line to include PP and TPU/PC compounds.
Plastics Technology covers technical and business Information for Plastics Processors in Injection Molding, Extrusion, Blow Molding, Plastic Additives, Compounding, Plastic Materials, and Resin Pricing. About Us
Available on the SE-EV series (and on SE DUZ all-electrics ) is a novel screw design described as “revolutionary” because it turns conventional plastication theory on its head. Decades-old single-screw theory holds that melting should be accomplished almost entirely by shear heating from mechanical work (friction) imparted by the screw. According to this theory, barrel heaters are intended only to prevent heat loss to the environment. But the new SL screw assembly, designed by Spiral Logic Ltd. of Hong Kong (spirallogic.com.hk) has no compression zone or compression ratio, and all the heat input for melting comes from the heater bands. Spiral Logic says this “non-compression” screw accomplishes better and more uniform melting in a shorter barrel—only 13:1. It avoids uncontrolled shear heating, which is said to result in inconsistent melt temperature, pressure, density, and viscosity.
Despite price increase nominations going into second quarter, it appeared there was potential for generally flat pricing with the exception of a major downward correction for PP.
Ultradent's entry of its Umbrella cheek retractor took home the awards for Technical Sophistication and Achievement in Economics and Efficiency at PTXPO.
These coupling cushions for an auto windshield rain sensor have a PBT frame overmolded with 5 Shore A LSR. Silicone encapsulated both sides of the PBT spanning the center of the circular parts. Arburg molded on them on a two-shot press in 38 sec, including robot transfer of the parts between cavities.
An option for Ube’s new UF series is its Cav-Change system, which is just now being introduced to the U.S. It’s an electric-driven turning-stack mold system for multi-material molding.
Say “manufacturing automation” and thoughts immediately go to the shop floor and specialized production equipment, robotics and material handling systems. But there is another realm of possible automation — the front office.
In addition, the models have 2.5X greater electrical capacity than a standard machine so they won’t overheat during high-speed molding. The regenerative braking system recovers around 6% of energy from mold open/close operations.
Wittmann Battenfeld showed off its EcoPower all-electric presses, for which it will add multicomponent injection capability this year.
Ticona offers conductive PPS grades that utilize an unconventional carbon-based conductive. The novel ingredient is said to offer many of the benefits of nano-tubes at considerably lower cost. This additive and proprietary compounding technique are said to ensure precise “tuneability” of ESD performance. The materials are also described as clean—non-sloughing and low in ionic contamination and outgassing—making them viable for use in liquid-crystal displays, electronic storage media, and microelectronic carrier trays.
JSW announced that its Die Slide Injection system for molding hollow parts is now available in the U.S. That’s because the Japanese molder that owns the patent, Sakamoto Kanagata, recently established a branch in S. Elgin, Ill.
Across all process types, sustainability was a big theme at NPE2024. But there was plenty to see in automation and artificial intelligence as well.
August 29-30 in Minneapolis all things injection molding and moldmaking will be happening at the Hyatt Regency — check out who’s speaking on what topics today.
The new screw works together with a GS Loader from Spiral Logic, which provides controlled feeding, rather than the usual “flood” feeding, and Spiral Logic’s GS check valve, which is said to provide 100% positive shutoff when the screw rotates 120° in reverse. Benefits of this system reportedly include 13% lower power consumption, less screw and barrel wear, 60% less cushion fluctuation, 74% less variation in cavity pressure, and elimination of black spots from stagnant, degraded material on the screw.
ICP- and IDP-based compounds promise to remedy all these shortcomings. They typically create a more uniform and complete conductive network than do dispersions of discrete particles of carbon black or even stainless-steel fibers. ICPs and IDPs often work at lower loadings, detract less from matrix-resin properties, and are more colorable than conventional products. IDPs even allow formulating transparent or translucent ESD products.
The Plastics Industry Association (PLASTICS) has released final figures for NPE2024: The Plastics Show (May 6-10; Orlando) that officially make it the largest ever NPE in several key metrics.
In this collection of content, we provide expert advice on welding from some of the leading authorities in the field, with tips on such matters as controls, as well as insights on how to solve common problems in welding.
LNP’s Stat-Loy family uses an IDP to impart permanent antistatic and ESD properties (109 to 1012 ohm/sq) to a variety of resins, including PC/ABS and a transparent ABS.
Because of its low cost, traditional carbon black is still the workhorse in conductive plastics. However, carbon black makes it difficult for compounders to hit a specific level of conductivity. It also imposes severe property tradeoffs and limitations on colorability. What's more, "sloughing" of conductive particles can damage microelectronic devices.
Sustainability continues to dominate new additives technology, but upping performance is also evident. Most of the new additives have been targeted to commodity resins and particularly polyolefins.
Pat Collins, Hyperion’s marketing manager, says fibril-based compounds can cover the full electrical spectrum at loadings at least 50% lower than would be needed with carbon fibers (which are gigantic in physical size compared with fibrils). Retention of toughness and ductility with the nano-tubes reportedly far exceeds that for the best conventional conductive compounds. Viscosity is minimally affected, Hyperion says, so its fibrils are highly suitable for thin-wall molding and provide excellent surface quality in appearance parts. There is less differential shrinkage and part warpage than with conventional filled compounds.
•Lots of new all-electric machines, especially beefed-up models meant to prove that servos can compete in high-output packaging applictions.
As noted in our March show preview, there were some impressive demonstrations of in-mold labeling. CBW Automation showed off a challenging application in labeling small syringes, requiring super-precise positioning of 16 small, extra-thin labels at high speed.
This Knowledge Center provides an overview of the considerations needed to understand the purchase, operation, and maintenance of a process cooling system.
While the major correction in PP prices was finally underway, generally stable pricing was anticipated for the other four commodity resins.
Successfully starting or restarting an injection molding machine is less about ticking boxes on a rote checklist and more about individually assessing each processing scenario and its unique variables.
Join Engel in exploring the future of battery molding technology. Discover advancements in thermoplastic composites for battery housings, innovative automation solutions and the latest in large-tonnage equipment designed for e-mobility — all with a focus on cost-efficient solutions. Agenda: Learn about cutting-edge thermoplastic composites for durable, sustainable and cost-efficient battery housings Explore advanced automation concepts for efficient and scalable production See the latest large-tonnage equipment and technology innovations for e-mobility solutions
Another new X-Pump hybrid is the N-PLAjet, designed specifically for PLA and other biopolymers. Nissei also displayed a vertical hybrid X-Pump model TNX50R2VLM (58 tons) customized to process LSR for insert molding. It has wide tiebar spacing, shot capacity down to 0.3 g, and a servo-powered turntable and ejector for fast cycles.
Those coated areas trapped the foaming gas that naturally migrates out of the plastic part after molding, resulting in permanently raised lettering.
Not all the new hybrids were two-platen types. Nissei brought out a new hybrid model with a servo-driven hydraulic X-Pump, the 500-ton FNX460-200BN1. This successor to the FNX A1 type has an expanded range of applications in polyolefin food, beverage, and medical containers and caps. It is aimed at cycle times below 10 sec and comes with 48% higher injection pressure and 55% faster injection speed than conventional machines. It also boasts high plasticating and shot capacity and precise control of nozzle and barrel temperatures. It can support parallel functions and eject on the fly while using an oil tank half the size of a standard hydraulic press.
FCS Group’s X-Type parallel quartet injection molding machine features four injection units aligned in parallel for a smaller footprint.
•Plenty of new hybrids as well, including many space-saving two-platen models. Many “hybrids” only in the sense that servo or inverter motors drove their hydraulic pumps.
Neil Hardwick, Noveon's marketing manager, says a recent initiative is tri-layer HIPS sandwich structures that optimize IDP cost-effectiveness in thermoformable sheets. For instance, one structure puts carbon-filled HIPS at the core (providing good volume resistivity and EMI shielding) while the skin layers include an IDP/HIPS compound to eliminate slough ing while ensuring excellent surface dissipation.
An innovation not reported previously is so-called “3D IML,” which won the Emerging Technology award in SPI’s International Design Competition. The application is a PP margarine tub molded by Paccor Packaging Deutschland for Planta in The Netherlands. It uses the MuCell microcellular foam process from Trexel Inc. (trexel.com). Foaming helped lightweight the package by 13% (9% through thinwalling and 4% from density reduction)and allowed 15% lower injection pressure and 36% lower clamp force. However, the novelty here is the raised logo lettering, which has an embossed, soft-touch feel. This was accomplished by applying a barrier coating to the back of the label in selective areas (behind the lettering).
Mold maintenance is critical, and with this collection of content we’ve bundled some of the very best advice we’ve published on repairing, maintaining, evaluating and even hanging molds on injection molding machines.
Introduced by Zeiger and Spark Industries at the PTXPO, the nozzle is designed for maximum heat transfer and uniformity with a continuous taper for self cleaning.
With advocacy, communication and sustainability as three main pillars, Seaholm leads a trade association to NPE that ‘is more active today than we have ever been.’
Another advance is a novel class of vapor-grown carbon nano-tubes and nano-fibers. These impart a broad range of conductivity to plastics at far lower loadings than conventional carbon-based additives, while simultaneously providing reinforcement and enhanced thermal conductivity. However, the potential of these nano-carbon products is currently limited by their $50/lb or higher price tags. This compares with $15/lb for pitch carbon fiber and stainless steel, $8/lb for PAN carbon fiber, and less than $2/lb for carbon-black powder. Greater near-term potential is seen for a developmental low-cost pitch carbon fiber that boasts improvements in both conductive and reinforcing properties.
Netstal ran 2.18-g HDPE PCO 1881 carbonated soft-drink closures in 72 cavities in 3.5 sec using a 280-m.t. Elion hybrid press with regenerative braking on the clamp. Netstal cited energy consumption for the machine as 0.48 kWh/kg and for the system overall as 0.52 kWh/kg. Caps were inspected by an Intravis vision system.
Wittmann Battenfeld exhibited the two-platen hydraulic MacroPower line, to which smaller sizes are being added. At the Milan Plast show in Italy later in April, Wittmann brought out a new 500-metric-ton model that is now the smallest in the line (down from 650 m.t. previously).
Thousands of people visit our Supplier Guide every day to source equipment and materials. Get in front of them with a free company profile.
This month’s resin pricing report includes PT’s quarterly check-in on select engineering resins, including nylon 6 and 66.
Ticona recently introduced an ESD acetal grade for auto fuel-line parts. Celcon CF802 uses novel compatibilizer technology to bond reinforcing fiber to the matrix. That is said to minimize mechanical property tradeoffs and increase resistance to attack by fuels.
Join Engel in exploring the future of battery molding technology. Discover advancements in thermoplastic composites for battery housings, innovative automation solutions and the latest in large-tonnage equipment designed for e-mobility — all with a focus on cost-efficient solutions. Agenda: Learn about cutting-edge thermoplastic composites for durable, sustainable and cost-efficient battery housings Explore advanced automation concepts for efficient and scalable production See the latest large-tonnage equipment and technology innovations for e-mobility solutions
Join KraussMaffei for an insightful webinar designed for industry professionals, engineers and anyone interested in the manufacturing processes of PVC pipes. This session will provide a comprehensive understanding of the technology behind the production of high-quality PVC pipes: from raw material preparation to final product testing. Agenda: Introduction to PVC extrusion: overview of the basic principles of PVC pipe extrusion — including the process of melting and shaping PVC resin into pipe forms Equipment and machinery: detailed explanation of the key equipment involved — such as extruders, dies and cooling systems — and their roles in the extrusion process Process parameters: insight into the critical process parameters like temperature, pressure and cooling rates that influence the quality and consistency of the final PVC pipes Energy efficiency: examination of ways to save material and energy use when extruding PVC pipe products
Thousands of people visit our Supplier Guide every day to source equipment and materials. Get in front of them with a free company profile.
Discover how artifical intelligence is revolutionizing plastics processing. Hear from industry experts on the future impact of AI on your operations and envision a fully interconnected plant.
Sustainability continues to dominate new additives technology, but upping performance is also evident. Most of the new additives have been targeted to commodity resins and particularly polyolefins.
While prices moved up for three of the five commodity resins, there was potential for a flat trajectory for the rest of the third quarter.
This “naked” view of Toyo’s new Si500V (with exterior panels removed) is one of several new all-electric machines beefed up with extra power for high-speed molding.
Today’s hyper-competitive molding environment requires more—more speed, more power, more precision, and more automated functions accomplished in and out of the mold. That’s exactly what injection machinery suppliers were offering at NPE2012 in complex molding demonstrations aimed largely at automotive, medical, and packaging applications. These were some key themes of the exhibits:
Another driver is the trend toward electrostatic spray painting of automotive and industrial parts. This method, in which paint drops are positively charged and the parts are grounded (negatively charged), is generating a flood of "e-paintable" compounds whose conductivity is tailored to optimize painting efficiency. E-painting is said to reduce overspray by up to 50%, thereby cutting both cost and volatile emissions.
Maruka USA exhibited the latest all-electric model from Toyo Machinery & Metal Co. of Japan. The Si500V is a 500-ton model in the Si-V series from 35 to 940 tons. These models are beefed up with 30-40% larger servomotors than competing machines, as well as larger ballscrew systems. The series also has wider tiebar spacing and a new V-slant toggle with a greater tilt angle that reportedly provides more uniform distribution of clamp force over the platen. The upgraded System 500 controller has a 5X faster processor than before.
Join Wittmann for an engaging webinar on the transformative impact of manufacturing execution systems (MES) in the plastic injection molding industry. Discover how MES enhances production efficiency, quality control and real-time monitoring while also reducing downtime. It will explore the integration of MES with existing systems, emphasizing compliance and traceability for automotive and medical sectors. Learn about the latest advancements in IoT and AI technologies and how they drive innovation and continuous improvement in MES. Agenda: Overview of MES benefits What is MES? Definition, role and brief history Historical perspective and evolution Longevity and analytics Connectivity: importance, standards and integration Advantages of MES: efficiency, real-time data, traceability and cost savings Emerging technologies: IoT and AI in MES
Nano-tube-based compounds offering 104 to 109 ohm/sq surface resistivity at 4-7% loadings are offered by RTP. Scott Koberna, RTP product manager for conductive compounds, says RTP’s NTC-series compounds minimize occurrence of hot and cold spots and are suitable for high-purity ESD and e-paintable compounds. RTP puts nano-tubes into HIPS, acetal, and other engineering resins. NTC grades are priced 25% to 100% higher than comparable PAN-fiber compounds.
As we reported in a Dec.’11 Close Up, Milacron has converted its Magna Toggle line to the Magna T Servo series with servo-driven hydraulics. The company is now doing the same with its Maxima Servo two-platen series and plans to offer only servo-hydraulic models by next year.
One unusual aspect is the fact that LSR encapsulates both sides of the PBT areas that span the diameter of the sensor. LSR is injected from one side, but pins hold the PBT so the LSR can flow around it on both sides. Second, the special LSR material from Wacker Chemical has a hardness of only 5 Shore A; its very low viscosity is challenging to process without flashing.
Take a deep dive into all of the various aspects of part quoting to ensure you’ve got all the bases—as in costs—covered before preparing your customer’s quote for services.
Toshiba’s packaging work cell demonstrated a 200-ton EC200SX with IML automation from Imdecol of Israel. The cell molded and labeled two PP deli containers in a 4.9-sec cycle. A clean-room enclosure over the clamp provided positive air pressure and included a particle counter to verify Class 100,000 conditions.
In addition, Sumitomo (SHI) Demag demonstrated unusual “full-cover” IML in which a food package gains barrier protection from being completely covered by the label.
RTP offers ICP compounds based on PP, PS, PE, and PC/ABS. These provide permanent ESD, accept 25% recycle content, and have a wide range of colorability. The compounds have potential in industrial packaging and containers, material-handling boxes and totes, and shelves and racks for electronics. RTP is working to stretch ICP compound performance into the EMI-shielding range (10 to 100 ohm/sq).
Injection molding news at the show was too voluminous to present in one article. Next month, we’ll report on controls, robots, hot runners, and other tooling developments from NPE. Also, see our March show preview for additional news that isn’t repeated here.
The latest from Mitsubishi is the MMX Series of large two-platen machines with Smart Pump system, consisting of a servo-driven hydraulic pump as well as an induction motor driving a variable-volume pump. These presses (1300 to 3500 m.t.) are built in China. They are more standardized than Mitsubishi’s MMS line but offer faster delivery and lower prices.
Coverage of single-use plastics can be both misleading and demoralizing. Here are 10 tips for changing the perception of the plastics industry at your company and in your community.
Across all process types, sustainability was a big theme at NPE2024. But there was plenty to see in automation and artificial intelligence as well.
In this collection of articles, two of the industry’s foremost authorities on screw design — Jim Frankand and Mark Spalding — offer their sage advice on screw design...what works, what doesn’t, and what to look for when things start going wrong.
There are even emerging applications for plastics to be nearly as conductive as pure carbon—such as bipolar plates and end plates for fuel cells.
Hyperion’s initial slate of nylon 6 and 66, PBT, and PC masterbatches has recently been broadened to include PEEK, PEI (GE’s Ultem polyetherimide), PPS, nylon 12, and PS. Coming next are PP, PET, and EVA masterbatches. Current uses include a nylon 12 that replaces metal in automotive fuel lines. It combines excellent ESD performance plus elevated toughness, which translates into the added safety benefit of increased rupture resistance. E-paintable compounds based on nano-tubes impart the necessary conductivity at just 2-3% loadings while offering a Class A surface quality.
Join this webinar to explore the transformative benefits of retrofitting your existing injection molding machines (IMMs). Engel will guide you through upgrading your equipment to enhance monitoring, control and adaptability — all while integrating digital technologies. You'll learn about the latest trends in IMM retrofitting (including Euromap interfaces and plasticizing retrofits) and discover how to future-proof your machines for a competitive edge. With insights from industry experts, it'll walk you through the decision-making process, ensuring you make informed choices that drive your business forward. Agenda: Maximize the value of your current IMMs through strategic retrofitting Learn how to integrate digital technologies to enhance monitoring and control Explore the benefits of Euromap interfaces and plasticizing retrofits Understand how retrofitting can help meet new product demands and improve adaptability Discover how Engel can support your retrofitting needs, from free consultations to execution
Introduced by Zeiger and Spark Industries at the PTXPO, the nozzle is designed for maximum heat transfer and uniformity with a continuous taper for self cleaning.
Improvements in nozzle design in recent years overcome some of the limitations of previous filter, mixing, and shut-off nozzles.
Discover how artifical intelligence is revolutionizing plastics processing. Hear from industry experts on the future impact of AI on your operations and envision a fully interconnected plant.
Formnext Chicago is an industrial additive manufacturing expo taking place April 8-10, 2025 at McCormick Place in Chicago, Illinois. Formnext Chicago is the second in a series of Formnext events in the U.S. being produced by Mesago Messe Frankfurt, AMT – The Association For Manufacturing Technology, and Gardner Business Media (our publisher).
Join this webinar to explore the transformative benefits of retrofitting your existing injection molding machines (IMMs). Engel will guide you through upgrading your equipment to enhance monitoring, control and adaptability — all while integrating digital technologies. You'll learn about the latest trends in IMM retrofitting (including Euromap interfaces and plasticizing retrofits) and discover how to future-proof your machines for a competitive edge. With insights from industry experts, it'll walk you through the decision-making process, ensuring you make informed choices that drive your business forward. Agenda: Maximize the value of your current IMMs through strategic retrofitting Learn how to integrate digital technologies to enhance monitoring and control Explore the benefits of Euromap interfaces and plasticizing retrofits Understand how retrofitting can help meet new product demands and improve adaptability Discover how Engel can support your retrofitting needs, from free consultations to execution
This Knowledge Center provides an overview of the considerations needed to understand the purchase, operation, and maintenance of a process cooling system.
Join Wittmann for an engaging webinar on the transformative impact of manufacturing execution systems (MES) in the plastic injection molding industry. Discover how MES enhances production efficiency, quality control and real-time monitoring while also reducing downtime. It will explore the integration of MES with existing systems, emphasizing compliance and traceability for automotive and medical sectors. Learn about the latest advancements in IoT and AI technologies and how they drive innovation and continuous improvement in MES. Agenda: Overview of MES benefits What is MES? Definition, role and brief history Historical perspective and evolution Longevity and analytics Connectivity: importance, standards and integration Advantages of MES: efficiency, real-time data, traceability and cost savings Emerging technologies: IoT and AI in MES
“Today, there are more reasons and better tools than ever for making electrically active compounds,” declares Mark Kaptur, product marketing manager for conductive compounds at LNP Engineering Plastics. One reason is more intensive use of electronics in cars, portable consumer devices, and appliances—plus their on-going miniaturization. Both trends increase the need to protect parts from ESD and EMI.
Across the show, sustainability ruled in new materials technology, from polyolefins and engineering resins to biobased materials.
Toshiba operated a new 200-ton EC200SX all-electric press in an automotive cell, showing off special technology developed by Japanese molder Taisei Plas Co. for bonding sheet metal to overmolded plastics. The key is a process for nano-texturing the surface of the metal to enhance bonding. Toshiba molded an automotive circuit-board holder with the help of its own new jointed-arm robot that demolded parts and inspected them with a laser mounted on the robot. Taisei technology is also used in Japan to mold a tablet computer case in which PPS attachments are overmolded onto metal. Toshiba says tight control of injection pressure afforded by the EC SX series is essential to this process.
Addressing hot-runner benefits, improvements, and everyday issues from the perspective of decades of experience with probably every brand on the market. Part 1 of 2.
Absolute Haitian introduced its own all-electric system for caps and closures, as well as cups, CD packaging, memory cards, and cellphone components. Its new Zhafir Venus/p is offered as an economical packaging alternative, since it is priced like a hydraulic machine. Features include a high-performance motor for faster injection and a longer screw (25:1) for greater plasticating capacity.
While the melting process does not provide perfect mixing, this study shows that mixing is indeed initiated during melting.
Multiple speakers at Molding 2023 will address the ways simulation can impact material substitution decisions, process profitability and simplification of mold design.
Mike Sepe has authored more than 25 ANTEC papers and more than 250 articles illustrating the importance of this interdisciplanary approach. In this collection, we present some of his best work during the years he has been contributing for Plastics Technology Magazine.
technotrans says climate protection, energy efficiency and customization will be key discussion topics at PTXPO as it displays its protemp flow 6 ultrasonic eco and the teco cs 90t 9.1 TCUs.
While the major correction in PP prices was finally underway, generally stable pricing was anticipated for the other four commodity resins.
August 29-30 in Minneapolis all things injection molding and moldmaking will be happening at the Hyatt Regency — check out who’s speaking on what topics today.
While prices moved up for three of the five commodity resins, there was potential for a flat trajectory for the rest of the third quarter.
Across the show, sustainability ruled in new materials technology, from polyolefins and engineering resins to biobased materials.
Toshiba Machine Corp. demonstrated its latest-generation EC SX all-electric presses at work cells in its booth. The high-speed molding cell had a 390-ton EC390SX molding PS spoons in 32 cavities on a 3.9-sec cycle. The machine had a special high-speed clamp with a more powerful motor, which provides a 14% shorter dry-cycle than a standard EC SX model. Another packaging cell is discussed in the IML section below.
Ube Machinery Inc. introduced a new generation of large all-electric presses, the Ubemax UF series of 700 to 1400 tons. Features include the TAF clamp, whose increased rigidity is said to reduce platen deflection by 60% and base deflection by 50%. The new ballscrew design on the toggle reportedly adds wear life while reducing grease consumption by 90%. The new e-HUMMA controller has a large, high-resolution TFT color touchscreen with quick access to all screens from icons on the main menu. It’s also designed for easy addition of future software options. Also new is Flex Servo injection process control, which is said to improve molding accuracy and consistency and to reduce spikes and power consumption.
Second quarter started with price hikes in PE and the four volume engineering resins, but relatively stable pricing was largely expected by the quarter’s end.
Electrostatic paintability without need for a conductive primer is another property that makes conductive plastics attractive to auto makers. GE Plastics is taking a new tack in formulating Noryl PPO alloys for e-paintable auto parts. Five years ago, GE was one of the first to adopt Hyperion’s carbon nano-tubes in Noryl 990E, used in mirror housings. That grade has been discontinued for unstated reasons, but cost certainly played a role in the decision.
When, how, what and why to automate — leading robotics suppliers and forward-thinking moldmakers will share their insights on automating manufacturing at collocated event.
Successfully starting or restarting an injection molding machine is less about ticking boxes on a rote checklist and more about individually assessing each processing scenario and its unique variables.
The Plastics Industry Association (PLASTICS) has released final figures for NPE2024: The Plastics Show (May 6-10; Orlando) that officially make it the largest ever NPE in several key metrics.
Arburg demonstrated high-speed IML production of twin 1-liter PP buckets with separately molded handles in a 2+2 cavity family mold on an Allrounder 720 H press (350 tons). Total part weight was 62 g for each bucket and handle. The robotics from Van den Brink B.V. of The Netherlands inserted the labels, removed the buckets and handles, assembled them together, and placed the finished products on a conveyor—all in 4.8 sec.
Negri Bossi also introduced its brand-new EOSSE series of small two-platen models (the company’s first) from 55 to 130 tons with a variable-displacement pump powered by an electric variable-frequency drive. These presses boast long opening strokes and unusually wide tiebar spacing. The clamp rides on linear bearings and uses two diagonal pistons for traverse movements. At the Milan Plast show in Italy last month, Negri Bossi brought out a modified version of the EOS with almost fully electric operation except for self-contained hydraulic clamp cylinders.
Milacron also showed off some new features on its PowerPAK all-electric series of 440 to 1125 tons. These include water-cooled drives and enhanced diagnostic and maintenance information on the drives in the control system, which includes a built-in energy monitor. Also new is optional high-force electric injection, designed especially for PET preforms. These machines offer optional accumulator-assisted hydraulic injection and ejection (a 330-ton model is available only in this configuration).
Core Technology Molding turned to Mold-Masters E-Multi auxiliary injection unit to help it win a job and dramatically change its process.
As reported in our March preview, NPE was the U.S. debut of Vesta all-electric machines (88 to 470 tons) from Negri Bossi that were introduced at K 2010 in Dusseldorf. Designed for heavy-duty custom molding, they have direct-drive toggle clamps, regenerative braking on the clamp, and a beefed-up injection system (up to 40 oz) with bigger, more durable ballscrews.
Compounders have long mixed carbon black, carbon fibers, stainless-steel fibers, aluminum flakes, and other additives into thermoplastics to meet needs for antistatic performance, electrostatic dissipation (ESD), and electromagnetic interference (EMI) shielding.
Arburg’s LSR demonstration involved overmolding LSR onto PBT in a coupling cushion for a car windshield rain sensor. The part consist of a PBT frame and a silicone diaphragm into which a sensor is inserted. The soft silicone conforms to the windshield curvature. The PBT frame was molded in an all-electric Allrounder 570 A (220 tons) with a 4+4 cavity mold from Rico Elastomere of Austria (rico.at). After hot-runner injection of the PBT, an Arburg Multilift V robot transferred the first shot to the LSR cold-runner overmolding cavities. Cycle time was 38 sec.
Additive technology creates air pockets in film during orientation, cutting down on the amount of resin needed while boosting opacity, mechanical properties and recyclability.
A relative newcomer to NPE was Woojin Plaimm, Inc. of South Korea. It established an office in Brea, Calif. Although the company has at least 10 machine series, it highlighted three at NPE: the TE all-electric series from 33 to 500 tons; the TH-S series with energy-saving, servo-driven hydraulic pumps (55 to 500 tons); and the DL two-platen hydraulic series (servo-driven pumps optional) from 500 to 3300 tons.
Stainless-steel fibers are the key ingredient in the Faradex line of EMI shielding compounds that LNP recently acquired from DSM. They are aimed more at consumer electronics and business machines, namely thin-wall housings for cell phones and computer equipment. Unlike carbon additives, stainless steel does not limit colorability, but the fibers are easily damaged in melt processing. LNP uses a special compounding technique to retain fiber length for good shielding.
Plastics Technology’s Tech Days is back! Every Tuesday in October, a series of five online presentations will be given by industry supplier around the following topics: Injection Molding — New Technologies, Efficiencies Film Extrusion — New Technologies, Efficiencies Upstream/Downstream Operations Injection Molding — Sustainability Extrusion — Compounding Coming out of NPE2024, PT identified a variety of topics, technologies and trends that are driving and shaping the evolution of plastic products manufacturing — from recycling/recyclability and energy optimization to AI-based process control and automation implementation. PT Tech Days is designed to provide a robust, curated, accessible platform through which plastics professionals can explore these trends, have direct access to subject-matter experts and develop strategies for applying solutions in their operations.
Multiple speakers at Molding 2023 will address the ways simulation can impact material substitution decisions, process profitability and simplification of mold design.
Core Technology Molding turned to Mold-Masters E-Multi auxiliary injection unit to help it win a job and dramatically change its process.
Say “manufacturing automation” and thoughts immediately go to the shop floor and specialized production equipment, robotics and material handling systems. But there is another realm of possible automation — the front office.
The aim of this presentation is to guide you through the factors and the numbers that will help you determine if a robot is a smart investment for your application. Agenda: Why are you considering automation? What problems are you trying to solve? How and why automation can help Crunch the numbers and determine the ROI
Take a deep dive into all of the various aspects of part quoting to ensure you’ve got all the bases—as in costs—covered before preparing your customer’s quote for services.
JSW Plastics Machinery introduced all-electric models in its J-AD series from 220 to 650 tons specifically for high-speed packaging. They have reinforced bed frames to support heavy stack molds, along with linear guide rails for the moving platen and sliding shoes for stack-mold center plates. Besides 30% higher mold-weight capability, they have bigger motors, 50% faster injection acceleration/deceleration response, 24:1 mixing screw with higher rpm (yielding 20% greater PP plasticating capacity), extended daylight, 20% faster clamp movements, 20% less platen deflection, 100% greater nozzle-touch force (using a hydraulic cylinder), and greater heater capacity.
In this three-part collection, veteran molder and moldmaker Jim Fattori brings to bear his 40+ years of on-the-job experience and provides molders his “from the trenches” perspective on on the why, where and how of venting injection molds. Take the trial-and-error out of the molding venting process.
DuPont is one firm working to broaden plastics’ opportunities in these applications. DuPont has developed a pair of acetal compounds for injection molding. Delrin 300AS and 300AT utilize carbon fiber to provide ESD capability (106 ohm/sq) and enhanced stiffness. Delrin 300AT has twice the toughness of a standard acetal. It is aimed at fuel-tank caps and filler pockets. Delrin 300AS exhibits 300% higher stiffness than standard acetals and is aimed at uses inside the tank—such as a support flange on sender modules (a device that primes the fuel pump). DuPont has also launched nylon 66 ESD grades, some of them glass-filled, and plans to launch ESD versions of its Zytel HTN high-temperature nylon.
Ultradent's entry of its Umbrella cheek retractor took home the awards for Technical Sophistication and Achievement in Economics and Efficiency at PTXPO.
When determining the best ejection option for a tool, molders must consider the ejector’s surface area, location and style.
In this collection, which is part one of a series representing some of John’s finest work, we present you with five articles that we think you will refer to time and again as you look to solve problems, cut cycle times and improve the quality of the parts you mold.
It's no surprise, then, that underlying demand for conductive plastic compounds in North America is forecasted to grow 8-10%/yr from a current base of around 450 million lb.
After successfully introducing a combined conference for moldmakers and injection molders in 2022, Plastics Technology and MoldMaking Technology are once again joining forces for a tooling/molding two-for-one.
EMI protection is another area of major growth potential for conductive plastics in automotive. Stimulating factors are increased use of sensitive electronic gadgetry in cars, a pending shift to 42-volt battery power, and the need to preserve space under the hood, according to David Riffer, electrical-electronics market manager for EMS-Grivory. His company has long put carbon and stainless steel into ESD versions of its nylon 6, 66, and 12 compounds for automotive fuel-line and under-hood applications. Now, the company is moving into nylon EMI-shielding compounds using stainless steel as the conductive ingredient. These are aimed at automotive electronics as well as business-machine housings and coaxial-cable connectors.
Processors with sustainability goals or mandates have a number of ways to reach their goals. Biopolymers are among them.
As reported in March, Absolute Haitian introduced Zhafir Mercury all-electrics to the U.S. This novel tiebarless design with two-stage injection now is available in 55, 100, and 150 metric tons. Later this year, the company will add 250- and 400-m.t. models, which will later be followed by 75 and 125 m.t.
Besides showing two new E Series hybrids with servo-driven pumps, Boy Machines demonstrated its new auxiliary injector for converting a standard machine to multi-component molding. This add-on injection unit is based on Boy’s XS hydraulic machine. It can be mounted in various positions and comes in sizes of 12, 14, and 16 mm screw diam. with its own hydraulic drive and control, which can be interfaced with most makes and models of presses.
When, how, what and why to automate — leading robotics suppliers and forward-thinking moldmakers will share their insights on automating manufacturing at collocated event.
While prices moved up for three of the five commodity resins, there was potential for a flat trajectory for the rest of the third quarter.
In recent years, others have introduced compounds based on IDPs comparable to (but different from) Noveon’s. New players include LNP, RTP, Lati USA, and DSM Engineering Plastics. DSM has just diversified its carbon-based ElectraFil line by adding IDP-based products.
LNP’s Ultra-Clean Stat-Kon slate of ESD materials for high-purity applications uses nano-tubes in PEEK and PEI compounds for wafer-carrier and disk-drive components. Ionic contamination is said to be 65% to 90% lower than in carbon-fiber compounds.
Permastat IDP-based compounds from RTP afford antistatic capability (1010 to 1011 ohm/sq) for business-machine and appliance parts, gears, and video cases. RTP recently introduced PermaStat Plus grades that extend the series' conductivity into the ESD range (“E” versions) or offer enhanced mechanical performance (“M” versions).
IDP-based compounds offer ESD protection, good colorability, and even translucency, as shown in ABS silicon-wafer carriers (top) and nylon handles of computer screwdrivers. (Photos: PolyOne and LNP)
Processors with sustainability goals or mandates have a number of ways to reach their goals. Biopolymers are among them.
As reported in March, Sumitomo (SHI) Demag brought to the show its new SE-EV all-electric, direct-drive series (55 to 198 tons). It replaces the Demag DUZ series at no increase in price. The SE-EV line reportedly uses 20% less energy than other all-electrics. For example, it requires no power to hold the clamp closed. It also has a shorter machine base but 100 mm more daylight than before, as well as 50 mm more vertical tiebar spacing. Faster servomotors are said to provide greater injection speed—350 mm/sec, up from 300 mm/sec previously. New linear guides on the moving platen replace tiebar bushings, providing greater rigidity and at least 20% more mold-weight capacity while eliminating grease on the tiebars. Two pull-in cylinders add more nozzle-touch force.
Exhibitors and presenters at the plastics show emphasized 3D printing as a complement and aid to more traditional production processes.
In a time where sustainability is no longer just a buzzword, the food and beverage packaging industry is required to be at the forefront of this innovation. By adopting circular packaging processes and solutions, producers can meet regulatory requirements while also satisfying consumer demand and enhancing brand reputation. Join Husky to learn more about the broader implications of the circular economy — as well as how leading brands are leveraging this opportunity to reduce costs, increase design flexibility and boost product differentiation. Agenda: The cost and operational benefits of embracing circularity Key materials in circular packaging — including rPET and emerging bioplastics How to design a circular food and beverage package Strategies for selecting sustainable closures to future-proof packaging solutions Optimization and streamlining of production processes for enhanced efficiency How Husky Technologies can enable your sustainable success
This process has been used for 15 years, mostly abroad, to mold automotive, healthcare, and consumer products, including auto fuel and water tanks and intake manifolds. It involves molding two halves of a hollow part in a mold that then slides to bring the mating halves together and overmolds a seal around them in a second cycle. Both shots use the same material.
After successfully introducing a combined conference for moldmakers and injection molders in 2022, Plastics Technology and MoldMaking Technology are once again joining forces for a tooling/molding two-for-one.
Mixed in among thought leaders from leading suppliers to injection molders and mold makers at the 2023 Molding and MoldMaking conferences will be molders and toolmakers themselves.
Additive technology creates air pockets in film during orientation, cutting down on the amount of resin needed while boosting opacity, mechanical properties and recyclability.
A particular strength of ICPs is their ability to drain off static charge in a highly exact and reproducible way, says Sam Dahman, product development engineer at RTP Co. RTP holds exclusive North American rights to develop ESD compounds based on the only commercial polyaniline ICP, a product supplied by Panipol of Finland. A recent breakthrough by RTP and Panipol maintains thermal stability and ensures uniform dispersion of polyaniline during melt processing.Conventional carbon black tends to suffer twin deficits when used to impart ESD protection: It dissipates across a wide range of surface conductivities, while disparities in voltage also tend to persist on the part surface in the form of “hot” and “cold” spots. RTP data, for instance, show that a part made of one carbon-black-filled PP has a surface resistivity ranging from 105 to 1012 ohm/sq. A comparable ICP-based part consistently hits a narrow range of 106 to 107 ohm/sq.
Learn about sustainable scrap reprocessing—this resource offers a deep dive into everything from granulator types and options, to service tips, videos and technical articles.
Also new was Niigata’s MDVR vertical electric press series (35 to 165 tons), also with wider tiebar spacing and new controls, as well as a faster oscillating mold table. It can mold two different parts on alternate cycles with separate injection profiles for each part.
Second quarter started with price hikes in PE and the four volume engineering resins, but relatively stable pricing was largely expected by the quarter’s end.
GE is also focusing on fuel filler doors, 78% of which are made of steel and painted on-line with other steel parts. GE sources believe that conversion of this application to plastics requires on-line e-paintable compounds. GE is proposing a nylon-modified PPO (Noryl GTX) made electrically conductive with carbon black.
Mixed in among thought leaders from leading suppliers to injection molders and mold makers at the 2023 Molding and MoldMaking conferences will be molders and toolmakers themselves.
AE Plast opted for tiebarless multimaterial Engel victory machines as it took on complex parts for the appliance and power tool market, including a 3K housing for Dremel’s rotary tool.
Also emphasizing caps and closures was Husky Injection Molding Systems Ltd., which introduced its next-generation HyCAP system for high-output beverage closures. The new HyCAP system ran a 300-ton hybrid press and a 0.95-g 26/22 closure in a 96-cavity KTW mold (Husky acquired KTW last year) on a 2.2-sec cycle. Husky launched the first HyCAP system at NPE 2009, where a 300-ton press molded a similar closure in 72 cavities on a 2.4-sec cycle. The 45% productivity improvement since then is attributed to improvements in the mold, machine, and controls. And that’s not all: Later in April, the Chinaplas show in Shanghai saw the debut of Husky’s HyCAP High Performance Package, billed as the “world’s fastest closure system.” It ran a 1.2-g 29/25 lightweight water cap in a 72-cavity KTW mold in 1.85 sec. This system is said to save up 20% in energy consumption vs. the previous HyCAP generation.
Lati recently launched the LatiOhm family of IDP-based compounds in PP, nylon 6, PBT, and PC. They are aimed at ESD roles in smoke detectors and power-tool housings. This family is said to provide surface resistivity from 104 to 1012 ohm/sq. Products are non-sloughing and are colorable in blue, purple, and green.
Automotive fuel delivery systems are a focus of interest for makers of ESD compounds. Parts subject to swift or turbulent gas flow (e.g., filler-line pockets or line connectors) require conductivity to thwart static build-up and the risk of sparks and explosion. That is a major reason why large-volume applications like fuel filler lines, chassis pipes, and fuel-pump housings are still overwhelmingly made of steel.
Boy Machines demonstrated a new LSR pumping station on its XS V vertical hydraulic press. The pneumatic unit is small and easily movable (photo at right). The system has a reportedly unique ability to lock the “back” position of the screw so as to eliminate the need for a shutoff valve on the mixing block. The screw has a special nonreturn valve that’s said to be easy to clean and to allow material changes with very little waste of costly LSR material.
In this collection of articles, two of the industry’s foremost authorities on screw design — Jim Frankand and Mark Spalding — offer their sage advice on screw design...what works, what doesn’t, and what to look for when things start going wrong.
"Nano-carbons may prove to be in the 21st century what aluminum was in the 20th," declares Max Lake, president of Applied Sciences, an advanced-materials R&D firm in Cedarsville, Ohio. Like aluminum, he says, the miniscule, high-aspect-ratio nano-particles impart extraordinary strength and light weight. In plastics, nano-carbons can also significantly enhance both electrical and thermal conductivity.
Plastics processors are finding applications for 3D printing around the plant and across the supply chain. Here are 8 examples to look for at NPE2024.
GE has now shifted its attention to e-paintable PPO compounds for automotive body panels like fenders. It is using carbon-black powder and a high-temperature PPO that can withstand 400 F bake temperatures for the E-Coat anticorrosion treatment. This e-paintable PPO is due to be commercialized this summer.
Sumitomo demonstrated the SL screw at the show in a high-precision medical micromolding application on a 55-ton SE50DUZ press. The part was a 57.5-mm-long, hairpin-shaped device molded of Ultem polyetherimide. The barbed legs are around 400 μm wide at the barbs and the end where they are joined has a 500-μm hole. Molding tolerances are 25 μm. The two-cavity mold came from micromolder Makuta Technics, Shelbyville, Ind.
One of the difficulties with carbon black is that small changes in concentration in a plastic compound can produce large leaps in conductivity. The “smoother” ESD performance curve offered by ICP-based compounds is a big advantage, Dahman says. It is far easier to tailor performance for a specific end-use and thereby optimize cost-performance. ICP compounds are priced at an intermediate point between carbon-black and carbon-fiber compounds.
Join KraussMaffei for an insightful webinar designed for industry professionals, engineers and anyone interested in the manufacturing processes of PVC pipes. This session will provide a comprehensive understanding of the technology behind the production of high-quality PVC pipes: from raw material preparation to final product testing. Agenda: Introduction to PVC extrusion: overview of the basic principles of PVC pipe extrusion — including the process of melting and shaping PVC resin into pipe forms Equipment and machinery: detailed explanation of the key equipment involved — such as extruders, dies and cooling systems — and their roles in the extrusion process Process parameters: insight into the critical process parameters like temperature, pressure and cooling rates that influence the quality and consistency of the final PVC pipes Energy efficiency: examination of ways to save material and energy use when extruding PVC pipe products
Netstal, which claims to be number one in the world in IML installations, molded tubs on an Evos 3500 (350 m.t.) hybrid in eight cavities in 5.75 sec with automation from Ilsemann.
Jeff Frankish, director of global market development at PolyOne’s Compounds & Colors unit, says OEM users of conductive compounds are “raising the performance bar” for these materials. “Multi-functionality” is increasingly being built into formulations, he says. As examples, he cites ESD and EMI grades from PolyOne that are also lubricated, based partly on recycled resins, or modified to process on specific equipment.
technotrans says climate protection, energy efficiency and customization will be key discussion topics at PTXPO as it displays its protemp flow 6 ultrasonic eco and the teco cs 90t 9.1 TCUs.
GETTING A QUOTE WITH LK-MOULD IS FREE AND SIMPLE.
FIND MORE OF OUR SERVICES:
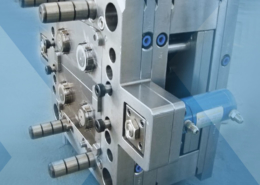
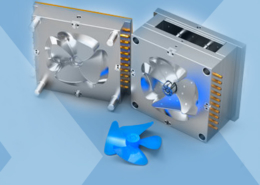
Plastic Molding

Rapid Prototyping
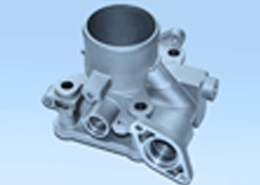
Pressure Die Casting
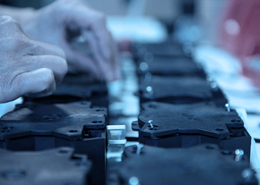
Parts Assembly
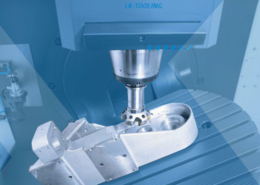