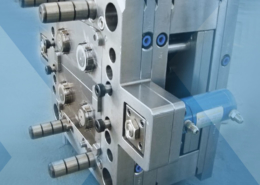
World First: Manufacturer Runs 128-Cavity Mold in 1.9-second Cycle Time - plasti
Author:gly Date: 2024-09-30
There’s been a lot of research put into making discarded thermoset or thermosetting plastics recyclable. The rationale for all these efforts is the protection of the environment and the sustainable management of all those thermoset plastics that will end up in landfills (or in the ocean). Conventional recycling for thermoset plastic-like mechanical and thermal processes cannot break it down. Needless to say, a solution to the above challenges is significant to an already thriving industry of thermoset plastic and plastic additives manufacturing.
Back in October 2016, we listed 30 emerging technologies we believe you should know about. One of those technologies we identified was recyclable thermoset plastics. Our first thought was, aren’t all plastics recyclable? As it turns out, they’re not.
So, when can we expect to see recyclable thermoset plastics? We don’t know but we can be sure about two things. First, that when this does become economically viable enough to commercialize, a huge deal is going to be made out of it, and rightfully so. Second, if it does utilize carbon nanotubes, then investing in carbon nanotube manufacturers like Nanocyl is going to make a whole lot of sense.
You will read a lot of literature classifying plastics into seven sub-groups. Well, these sub-groups were really created so that industry and consumers have a way of sorting all those plastic out either to be recycled or disposed of. When it boils down to key compounds and physical characteristics, plastics are really divided into just two major categories: Thermosetting and Thermoplastics.
Stephen has been with PlasticsToday and its preceding publications Modern Plastics and Injection Molding since 1992, throughout this time based in the Asia Pacific region, including stints in Japan, Australia, and his current location Singapore. His current beat focuses on automotive. Stephen is an avid folding bicycle rider, often taking his bike on overseas business trips, and is a proud dachshund owner.
Nanalyze Weekly includes useful insights written by our team of underpaid MBAs, research on new disruptive technology stocks flying under the radar, and summaries of our recent research. Always 100% free.
Nanalyze Weekly includes useful insights written by our team of underpaid MBAs, research on new disruptive technology stocks flying under the radar, and summaries of our recent research. Always 100% free.
The screw, non-return valve and barrel massively influence the melt quality and repeatability of the injection molding process as well as the lifespan and cost-effectiveness of the injection molding machine. As a provider of tailor-made, integrated system solutions, Engel also adapts the plasticizing unit to the specific requirements of the respective application.
Assume for a moment that the main ingredient for thermoset plastic is an uncut diamond. Diamond once cut into its desired shape or form can no longer be uncut to its original shape and size. To attempt to re-shape it will alter its value and purpose. What if you found a way to uncut it? Not only can you uncut it, but you found a way to take it apart molecule by molecule and then put it together again to form a different shape and size. While you are at it, you made the diamond stronger than before. And, you found a chemical key to bind, unbind, and make the diamond even stronger anytime and anyway you want.
Because you cannot break it down to its original form, you cannot re-use it to create new thermoset plastic. You have to use new raw ingredients and start the molding process with fresh ingredients. The discarded thermoset plastics will obviously end up in a landfill somewhere and form heaps of waste in time like all landfills always do. This is why developing a thermoset plastic that can be recycled is so important.
The plastic less rigid and softens to return to its original form is called thermoplastic. This is the kind of plastic that can be extruded and molded to whatever shape or form you want. You can produce films, packaging, Styrofoam, PET bottles, and PVC pipes from thermoplastics.
These opportunities can mean a lot of things for an industry expected to grow at a compounded rate of 3.7% annually until 2020 in the Asia-Pacific. Thermosetting plastic production globally is estimated to be around 34.99 million tons in 2015 and, by 2020, anticipated to hit 41.96 million tons. Unfortunately, there are no start-ups we can see as channels for investment into these new technologies. Your options will have to be through the companies who invested in the research and will most likely have the greatest success rolling the technology out to produce mainstream products for the plastic additives industry. This technological discovery is particularly significant for IBM because of the large amount of thermoset plastics found in computer hardware and other devices.
This is the kind of plastic where the plastic ingredient, once shaped and cooled, cannot return to its original form. Thermoset plastics are the kind we use to make parts for aircraft, cars, tires, computer casings, medical equipment, etc. Once thermoset plastics are heated then cooled, they will maintain shape and will be durable even under extreme pressure and heat. For all its versatility, the very thing that makes thermoset plastics useful is what makes it so difficult to dispose or to recycle.
Our image of plastics are wrappers, plastic cups, PET bottles, cars, computers, medical equipment, dashboards, electrical equipment, and more. We can also see large heaps of motherboards, discarded plastic parts of factories, equipment, circuit boards, etc. Plastics have not only supported a large industry but also drove a consumption for plastic that reached 297.5 million tons in 2015. This led to plastic waste turning up in oceans in a volume equivalent to 8 million metric tons a year. Here’s a part of the Maldives you’re not going to see as you’re being whisked away to that $1000 a night all-inclusive:
As it turns out, Baker Hughes Incorporated (NYSE:BHI) apparently was into the same research with this patent application but, only for a process to synthesize a thermosetting plastic identical to one of IBM’s without the introduction of carbon nanotubes during synthesis. The patent application was filed in 2015 and is driven by their existing investment into polymers as additives to the plastic industry.
The anticipated increase in demand, driven by the introduction of carbon nanotubes in reinforcing the strength of PHT, can also be significant to companies like Nanocyl, a Belgian company manufacturing carbon nanotubes and its German distribution partner Velox already serving the global market for plastic additives.
Engel's response to the increasing requirements of the automotive industry in particular, and the increasing use of fibre-reinforced materials, takes the form of two new screws – the PFS (Physical Foaming Screw) and the LFS (Long Glass Fibre Screw).
The PFS was developed specifically for structural foam molding. In conjunction with a new material design, the new screw geometry ensures even better homogenisation of the gas-loaded melt and increases both productivity and the screw service life wherever fibre-reinforced polymers are used. A victory injection molding machine equipped with the new PFS will produce highly decorated, three-dimensionally complex parts at Engel's stand during K 2019. The application combines MuCell structural foam molding from Trexel with the roll-to-roll in-mold decoration (IMD) process.
Long glass-fiber reinforced polypropylene and polyamide are commonly used for lightweight automotive construction – above all when high impact strength, excellent impact behaviour and low weight are required. The processing challenge in injection molding is to keep the fiber as long as possible and ensure uniform distribution of the fibers in the melt.
The LFS for processing long glass fiber-reinforced materials reliably maintains the fiber length and ensures uniform distribution of the fibres in the melt. Picture: Engel
The requirements placed on plasticizing units are continuing to grow. “This is driven, among other things, by the on-going substitution of traditional technical materials, which generates considerable increases in the performance of polymer materials,” reports Günther Klammer, head of the Plasticising Systems division at Engel. “We ensure that even new materials can be processed even faster and to even higher quality standards despite what are in part increasing stresses on mechanical components.” The keys to this are, on the one hand, continuous investment in new machining technologies and, on the other, splitting the screw portfolio in order to offer the best possible solution for every material execution.
A team of researchers at the IBM Almaden Research Center inadvertently stumbled upon this very key and created two new thermosetting polymers. One of the polymers, poly(hexahydrotriazine) or PHT was even made more durable through the introduction of carbon nanotubes. Not only have the IBM research group synthesized two new thermosetting plastics, they inadvertently discovered a gel to make damaged plastic heal itself. They referred to it as “elastic organogel”.
A not well-known fact may be that Engel is the world’s largest screw manufacturer in the injection molding industry. At K 2019 Düsseldorf, Germany, the company will be presenting its extensive plasticizing portfolio.
The previous solution was a single flighted 3-zone screw with a bolt-on long glass-fiber (LGF) mixing head. With the demand for injection molding machines for processing long glass fiber-reinforced plastic in rod granule form on the rise, Engel decided to manufacture the screw and mixing head from a single piece and to further optimise the screw geometry. The newly developed LFS offers maximum plasticizing consistency when processing rod granules and reduces fiber breakage. In order to ensure superior distribution of the fiber bundles in the product, the screw geometry was also optimised. Highly effective flight-welding gives the screw the required wear- and corrosion-resistance.
GETTING A QUOTE WITH LK-MOULD IS FREE AND SIMPLE.
FIND MORE OF OUR SERVICES:
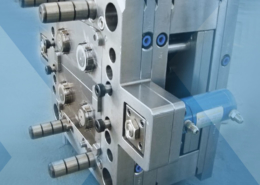
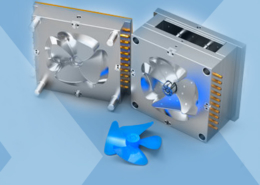
Plastic Molding

Rapid Prototyping
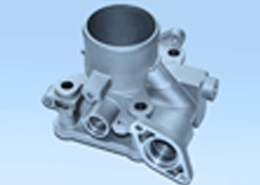
Pressure Die Casting
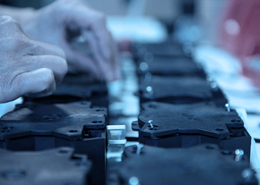
Parts Assembly
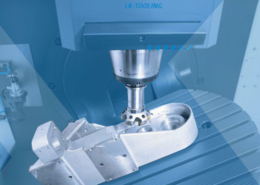