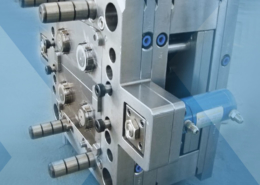
World First: Manufacturer Runs 128-Cavity Mold in 1.9-second Cycle Time - mold i
Author:gly Date: 2024-09-30
Join KraussMaffei for an insightful webinar designed for industry professionals, engineers and anyone interested in the manufacturing processes of PVC pipes. This session will provide a comprehensive understanding of the technology behind the production of high-quality PVC pipes: from raw material preparation to final product testing. Agenda: Introduction to PVC extrusion: overview of the basic principles of PVC pipe extrusion — including the process of melting and shaping PVC resin into pipe forms Equipment and machinery: detailed explanation of the key equipment involved — such as extruders, dies and cooling systems — and their roles in the extrusion process Process parameters: insight into the critical process parameters like temperature, pressure and cooling rates that influence the quality and consistency of the final PVC pipes Energy efficiency: examination of ways to save material and energy use when extruding PVC pipe products
For the most part, machine builders make no claims for increased speed or energy efficiency of hybrid clamps relative to standard hydromechanical presses. However, Meiki points out that some cycle-time savings can be achieved in mold opening and closing with servomotors and ball screws to drive the moving platen. This system has low inertia and very quick acceleration and deceleration—only 100 millisec from zero to maximum speed—as well as a position accuracy of 0.05 mm (0.002 in.) for the switchover position to decelerate from high speed.
Ultradent's entry of its Umbrella cheek retractor took home the awards for Technical Sophistication and Achievement in Economics and Efficiency at PTXPO.
Krauss-Maffei’s two-platen Eltec hybrid line spans a range of 55 to 165 tons. These models use electric ballscrews integrated with the tiebars to drive rapid-traverse open/close movements and a hydromechanical system for lock-up. Once the split-nut locks around each of the tiebars, the system delivers oil to four small short-stroke cylinders on the tiebars in the stationary platen. Clamping occurs in the four corners of the platen, like a standard hydromechanical or toggle press. The cylinder movement is only 6 mm and uses about 1.5 liters of oil for each tiebar. “Our standard C series unit would require about 180 liters [45 gal] of oil,” says Caprio. Tonnage build-up is as quick as 0.5 sec, he says. A servo pump drives the hydraulic system. Electric motors drive injection, ejection, and plastication.
Core Technology Molding turned to Mold-Masters E-Multi auxiliary injection unit to help it win a job and dramatically change its process.
Say “manufacturing automation” and thoughts immediately go to the shop floor and specialized production equipment, robotics and material handling systems. But there is another realm of possible automation — the front office.
Hybrids are said to be more suitable than toggles for coining or injection-compression processes, which require injecting into a partly open mold, followed by full closing and lock-up. Thermosets or optical lenses are applications that commonly use injection-compression, notes Paul Caprio, v.p. for injection molding at Krauss-Maffei.
Demag’s El-Exis Series uses an electric motor to power a “hydrostatic” closed-loop hydraulic system to power a toggle. This arrangement downsizes the hydraulic accumulator and pump package by 66%.
Exhibitors and presenters at the plastics show emphasized 3D printing as a complement and aid to more traditional production processes.
A new choice in injection machines is electric/hydraulic hybrids like this Eltec machine from Krauss-Maffei. Based on hydromechanical two-platen designs, they offer the speed and precision of electric servo drives plus the flexibility of hydraulic clamping.
Join KraussMaffei for an insightful webinar designed for industry professionals, engineers and anyone interested in the manufacturing processes of PVC pipes. This session will provide a comprehensive understanding of the technology behind the production of high-quality PVC pipes: from raw material preparation to final product testing. Agenda: Introduction to PVC extrusion: overview of the basic principles of PVC pipe extrusion — including the process of melting and shaping PVC resin into pipe forms Equipment and machinery: detailed explanation of the key equipment involved — such as extruders, dies and cooling systems — and their roles in the extrusion process Process parameters: insight into the critical process parameters like temperature, pressure and cooling rates that influence the quality and consistency of the final PVC pipes Energy efficiency: examination of ways to save material and energy use when extruding PVC pipe products
Say “manufacturing automation” and thoughts immediately go to the shop floor and specialized production equipment, robotics and material handling systems. But there is another realm of possible automation — the front office.
This Knowledge Center provides an overview of the considerations needed to understand the purchase, operation, and maintenance of a process cooling system.
Meiki developed what it calls a pumpless clamping device for its New Advanced Direct Electric Machine (Nadem) series of hybrid-clamp machines. The line currently ranges from 88 to 1430 tons, but Meiki plans to add models up to 2000 tons in the next year. This design uses two servomotors and ballscrews on diagonal corners of the platen for rapid-traverse clamp movements. What’s unique about this design is that the ballscrews—which have their own locking/unlocking mechanisms separate from that on the central ram—continue turning during lock-up. Their motion compresses cylinders built around the ballscrews, moving a small amount of oil out of those cylinders and into the central clamping cylinder to build hydraulic pressure. The result is to push on the corners of the platen and with the center ram, applying more widely distributed pressure than with other designs.
Under a microscope, air gap is visible between flow fronts of a fully packed ABS part. Striations are due to incomplete color mixing. (Photo: John Bozzelli)
Take a deep dive into all of the various aspects of part quoting to ensure you’ve got all the bases—as in costs—covered before preparing your customer’s quote for services.
Toggles may have a slight edge in clamp-tonnage build-up time. “A toggle has an amplification ratio at the end of the stroke, meaning it locks up faster than a hydraulic system, says Ward. Lock-up can be as quick as 0.2 sec with a toggle system vs. 0.5 sec for a hydraulic system, he claims.
While prices moved up for three of the five commodity resins, there was potential for a flat trajectory for the rest of the third quarter.
Until recently, the term “hybrid” applied mainly to machines that used electric-driven screw plastication but hydraulics everywhere else. The case for that type of “hybrid” is that it provides most of the achievable energy savings at the smallest additional cost. Now there’s a new kind of hybrid in town, and its rationale is not mainly about energy savings.
Processors with sustainability goals or mandates have a number of ways to reach their goals. Biopolymers are among them.
Boy will debut three new models in its Electric series of machines, which feature a redesigned and more compact drive and inverter technology.
The Plastics Industry Association (PLASTICS) has released final figures for NPE2024: The Plastics Show (May 6-10; Orlando) that officially make it the largest ever NPE in several key metrics.
When determining the best ejection option for a tool, molders must consider the ejector’s surface area, location and style.
Sodick Plustech’s Eclipse line uses a central servomotor and ball screw for mold opening and closing. After clamping locks engage the central ram, a central hydraulic “pancake” cylinder pulls on the tiebars for clamping.
This month’s resin pricing report includes PT’s quarterly check-in on select engineering resins, including nylon 6 and 66.
Thousands of people visit our Supplier Guide every day to source equipment and materials. Get in front of them with a free company profile.
So far, few hybrid units have been sold in the U.S. Meiki leads the way with about a dozen sold here. Krauss-Maffei has around four hybrid machines at North American beta-test sites. Mitsubishi aims to sell 10-20 hybrid presses this year in North America, says Tom Geddes, general manager of engineering. The company has delivered more than 100 units to clients in Asia.
In Part 1 of this series, we address long-fiber processing fundamentals and best practices, including practical tips and guidance on maintaining fiber length and deriving maximum advantages for demanding end applications. Part 2 will provide the same information for short-fiber materials.
For clamping, the ballscrews resume turning and pressurize hydraulic cylinders (3). Valves open to deliver a small volume of oil from those cylinders to the central ram (4). Tonnage is built by pushing with the ballscrews and central ram.
Using a strain gauge on the tiebar, mold-protection sensitivity can be set as low as 5 bar (72.55 psi), and response within 0.2 mm of travel is reportedly achievable.
Discover how artifical intelligence is revolutionizing plastics processing. Hear from industry experts on the future impact of AI on your operations and envision a fully interconnected plant.
technotrans says climate protection, energy efficiency and customization will be key discussion topics at PTXPO as it displays its protemp flow 6 ultrasonic eco and the teco cs 90t 9.1 TCUs.
While prices moved up for three of the five commodity resins, there was potential for a flat trajectory for the rest of the third quarter.
While prices moved up for three of the five commodity resins, there was potential for a flat trajectory for the rest of the third quarter.
Gifted with extraordinary technical know how and an authoritative yet plain English writing style, in this collection of articles Fattori offers his insights on a variety of molding-related topics that are bound to make your days on the production floor go a little bit better.
I asked Bozzelli what he thinks of this approach. He responds, “Adding the overflow channel to improve weld-line strength is not common, but I have seen it done a number of times. Yes, it does help, for two reasons: Often the weld line traps air and the ‘dump’ acts as a vent to allow the air to escape. That helps. Second, depending on the size of the overflow well, you get a little bit of flow melding together, and that helps strength so that you have some intertwining of the polymer chains. This is similar to putting whatever is causing the weld line, like a hole in a part, away from the end of fill. Plastic then has a chance to flow around the hole and re-meld as it continues to fill the part. That really helps to improve strength.”
With advocacy, communication and sustainability as three main pillars, Seaholm leads a trade association to NPE that ‘is more active today than we have ever been.’
Across all process types, sustainability was a big theme at NPE2024. But there was plenty to see in automation and artificial intelligence as well.
Join this webinar to explore the transformative benefits of retrofitting your existing injection molding machines (IMMs). Engel will guide you through upgrading your equipment to enhance monitoring, control and adaptability — all while integrating digital technologies. You'll learn about the latest trends in IMM retrofitting (including Euromap interfaces and plasticizing retrofits) and discover how to future-proof your machines for a competitive edge. With insights from industry experts, it'll walk you through the decision-making process, ensuring you make informed choices that drive your business forward. Agenda: Maximize the value of your current IMMs through strategic retrofitting Learn how to integrate digital technologies to enhance monitoring and control Explore the benefits of Euromap interfaces and plasticizing retrofits Understand how retrofitting can help meet new product demands and improve adaptability Discover how Engel can support your retrofitting needs, from free consultations to execution
Discover how artifical intelligence is revolutionizing plastics processing. Hear from industry experts on the future impact of AI on your operations and envision a fully interconnected plant.
Demag Plastic Group’s El-Exis S series (sold here by Van Dorn Demag) is designed as a high-speed packaging machine. It currently comes in sizes of 66 to 462 tons, though models up to 1000 tons are planned. The El-Exis S has a different kind of hybrid clamp from all the others. It uses self-contained hydraulics (which Demag calls a “hydrostatic drive”) to drive a toggle. The hydraulic pump is driven by an AC frequency motor. The system has response time of 12 millisec, platen speeds up to 25 in./sec, and position control as tight as 0.01 mm, says John Ward, technical sales manager. “We felt that a self-contained hydrostatic drive was a better option than using components such as belt drives or rack-and-pinion systems. The latter may be more sensitive to wear and stretching and can yield variations in accuracy and be less responsive,” he says.
Hybrid clamp designs that combine electric servomotors with novel hydraulic circuit configurations are now competing for molders’ attention as alternatives to all-electric or all-hydraulic clamping systems. A handful of OEMs supplying these new clamp styles say they can deliver greater processing speed and precision than conventional hydraulic-powered clamps at lower cost than all-electric machines.
Following on a similar guide for long-fiber reinforced compounds, here are practical tips on designing and injection molding parts utilizing short-fiber reinforcements.
Across all process types, sustainability was a big theme at NPE2024. But there was plenty to see in automation and artificial intelligence as well.
Mike Sepe has authored more than 25 ANTEC papers and more than 250 articles illustrating the importance of this interdisciplanary approach. In this collection, we present some of his best work during the years he has been contributing for Plastics Technology Magazine.
Take a deep dive into all of the various aspects of part quoting to ensure you’ve got all the bases—as in costs—covered before preparing your customer’s quote for services.
Resin drying is a crucial, but often-misunderstood area. This collection includes details on why and what you need to dry, how to specify a dryer, and best practices.
In this collection of articles, two of the industry’s foremost authorities on screw design — Jim Frankand and Mark Spalding — offer their sage advice on screw design...what works, what doesn’t, and what to look for when things start going wrong.
In this collection of content, we provide expert advice on welding from some of the leading authorities in the field, with tips on such matters as controls, as well as insights on how to solve common problems in welding.
In this three-part collection, veteran molder and moldmaker Jim Fattori brings to bear his 40+ years of on-the-job experience and provides molders his “from the trenches” perspective on on the why, where and how of venting injection molds. Take the trial-and-error out of the molding venting process.
Demag Plastics Group, Krauss-Maffei, Meiki, Mitsubishi, and Sodick Plustech contend that their hybrid clamp configurations deliver the precision, accuracy, repeatability, and energy savings of servomotor designs along with the power, reduced initial cost, and familiarity of a hydraulic drive—but without the contamination and oil-maintenance issues. These suppliers say hybrid clamp systems, which achieve high-speed mold movements and fast tonnage generation, address issues they view as shortcomings of more traditional clamp styles such as hydraulic toggles, fully hydraulic, hydromechanical, and all-electric toggles. The cost of hybrid machines is in between those of hydraulic and all-electric models.
Despite price increase nominations going into second quarter, it appeared there was potential for generally flat pricing with the exception of a major downward correction for PP.
This month’s resin pricing report includes PT’s quarterly check-in on select engineering resins, including nylon 6 and 66.
August 29-30 in Minneapolis all things injection molding and moldmaking will be happening at the Hyatt Regency — check out who’s speaking on what topics today.
Mold maintenance is critical, and with this collection of content we’ve bundled some of the very best advice we’ve published on repairing, maintaining, evaluating and even hanging molds on injection molding machines.
This Knowledge Center provides an overview of the considerations needed to understand the purchase, operation, and maintenance of a process cooling system.
Join Wittmann for an engaging webinar on the transformative impact of manufacturing execution systems (MES) in the plastic injection molding industry. Discover how MES enhances production efficiency, quality control and real-time monitoring while also reducing downtime. It will explore the integration of MES with existing systems, emphasizing compliance and traceability for automotive and medical sectors. Learn about the latest advancements in IoT and AI technologies and how they drive innovation and continuous improvement in MES. Agenda: Overview of MES benefits What is MES? Definition, role and brief history Historical perspective and evolution Longevity and analytics Connectivity: importance, standards and integration Advantages of MES: efficiency, real-time data, traceability and cost savings Emerging technologies: IoT and AI in MES
“Clamp-tonnage build-up will be two to three times faster than a straight hydraulic—and may be as quick as an all-electric,” says Meiki’s Chang. The unit can achieve mold/clamp movements up to 800 mm/sec. Nadem machines also have electric servo-driven ejection, injection, and plastication.
In this collection, which is part one of a series representing some of John’s finest work, we present you with five articles that we think you will refer to time and again as you look to solve problems, cut cycle times and improve the quality of the parts you mold.
In this three-part collection, veteran molder and moldmaker Jim Fattori brings to bear his 40+ years of on-the-job experience and provides molders his “from the trenches” perspective on on the why, where and how of venting injection molds. Take the trial-and-error out of the molding venting process.
How common is this, really? Bozzelli answers, “As I remember, nearly all of the TEMs that I had done at Dow showed an air gap, whether the resin was filled or unfilled, filled being a bit worse. Since I left Dow, I try to break the part at the weld line and look at the surface of the break on both sides under a simple magnifying glass. Sometimes the areas on both sides of the weld line are glossy and cupped inward, an indication of a bubble or air. Also, often they do not match or mate, so to me that is an indication that the flow fronts were separated by an air gap. Filled or unfilled, I see this about 65% of the time. Now, I just assume it is there and do what I can to eliminate or reduce the weld line. Installing vents near the area often helps, But once you put in a vent on the parting line near the weld line, the weld line often moves and then you have to put in another vent. Vacuum on the mold does help and many times eliminates the weld line.”
Toggle critics also raise questions about maintaining mold parallelism if the linkages don’t all perform or wear uniformly. There is also potential for higher platen deflection since most toggles generate force on the corners of the platen rather than the center. (Nissei recently came out with an all-electric three-stage toggle clamp that answers this criticism by applying force at the center of the platen.) Finally, the need for grease to lubricate toggle linkages presents potential contamination issues that counteract the cleanliness argument for all-electrics.
An electric-driven center ballscrew performs rapid-traverse motions on the Eclipse series of hybrid presses from Sodick Plustech (sold here by Yamazen). After the center ram is locked in position, an accumulator-assisted, doughnut-shaped, central “pancake” hydraulic cylinder surrounding the ballscrew pulls on the tiebars to create clamping force. These hybrids come in sizes of 5.5 to 385 tons, including a vertical 40-tonner. Servomotors also actuate the ejector and plasticating screw, while injection is accomplished hydraulically with the assistance of a gas accumulator for high speed.
Additive technology creates air pockets in film during orientation, cutting down on the amount of resin needed while boosting opacity, mechanical properties and recyclability.
Multiple speakers at Molding 2023 will address the ways simulation can impact material substitution decisions, process profitability and simplification of mold design.
While prices moved up for three of the five commodity resins, there was potential for a flat trajectory for the rest of the third quarter.
Introduced by Zeiger and Spark Industries at the PTXPO, the nozzle is designed for maximum heat transfer and uniformity with a continuous taper for self cleaning.
In this collection of content, we provide expert advice on welding from some of the leading authorities in the field, with tips on such matters as controls, as well as insights on how to solve common problems in welding.
In this collection of articles, two of the industry’s foremost authorities on screw design — Jim Frankand and Mark Spalding — offer their sage advice on screw design...what works, what doesn’t, and what to look for when things start going wrong.
In between all-electric and hydraulic-powered injection machines, a new species of hybrid clamp has emerged. Advocates say it combines the best qualities of electric servos and hydraulics without their disadvantages.
Core Technology Molding turned to Mold-Masters E-Multi auxiliary injection unit to help it win a job and dramatically change its process.
Formnext Chicago is an industrial additive manufacturing expo taking place April 8-10, 2025 at McCormick Place in Chicago, Illinois. Formnext Chicago is the second in a series of Formnext events in the U.S. being produced by Mesago Messe Frankfurt, AMT – The Association For Manufacturing Technology, and Gardner Business Media (our publisher).
Hybrid clamping designs typically start with hydromechanical locking. This EM unit from Mitsubishi uses a split-nut lock system.
Ultradent's entry of its Umbrella cheek retractor took home the awards for Technical Sophistication and Achievement in Economics and Efficiency at PTXPO.
While the major correction in PP prices was finally underway, generally stable pricing was anticipated for the other four commodity resins.
In a time where sustainability is no longer just a buzzword, the food and beverage packaging industry is required to be at the forefront of this innovation. By adopting circular packaging processes and solutions, producers can meet regulatory requirements while also satisfying consumer demand and enhancing brand reputation. Join Husky to learn more about the broader implications of the circular economy — as well as how leading brands are leveraging this opportunity to reduce costs, increase design flexibility and boost product differentiation. Agenda: The cost and operational benefits of embracing circularity Key materials in circular packaging — including rPET and emerging bioplastics How to design a circular food and beverage package Strategies for selecting sustainable closures to future-proof packaging solutions Optimization and streamlining of production processes for enhanced efficiency How Husky Technologies can enable your sustainable success
Despite price increase nominations going into second quarter, it appeared there was potential for generally flat pricing with the exception of a major downward correction for PP.
In this collection, which is part one of a series representing some of John’s finest work, we present you with five articles that we think you will refer to time and again as you look to solve problems, cut cycle times and improve the quality of the parts you mold.
MHI’s EM machines also have electric plastication, injection, and ejection. The line now spans 720 to 1200 tons, though plans are being considered to add a 1500-tonner and maybe a 2000-ton model. The line may eventually extend to 3000 tons.
Plastics Technology’s Tech Days is back! Every Tuesday in October, a series of five online presentations will be given by industry supplier around the following topics: Injection Molding — New Technologies, Efficiencies Film Extrusion — New Technologies, Efficiencies Upstream/Downstream Operations Injection Molding — Sustainability Extrusion — Compounding Coming out of NPE2024, PT identified a variety of topics, technologies and trends that are driving and shaping the evolution of plastic products manufacturing — from recycling/recyclability and energy optimization to AI-based process control and automation implementation. PT Tech Days is designed to provide a robust, curated, accessible platform through which plastics professionals can explore these trends, have direct access to subject-matter experts and develop strategies for applying solutions in their operations.
At present, U.S. molders decline to comment on their experience with hybrid clamps. “It is too early to say what improvements we are getting with the hybrid clamp,” says John Hahn, v.p. of engineering for molder MGS Mfg. Group of Germantown, Wis. The firm recently installed a new Eltec unit from Krauss-Maffei. The press may be used in a clean-room or optical application, Hahn says.
Gifted with extraordinary technical know how and an authoritative yet plain English writing style, in this collection of articles Fattori offers his insights on a variety of molding-related topics that are bound to make your days on the production floor go a little bit better.
Bozzelli explains, “It’s a huge issue in the industry that few know about. Many resin suppliers actually make thing worse by putting in too much lube, wax or flow aids. The black line of material is not ABS, but a wax, oil or other additive that phase-separated. It is much lower in molecular weight and rushes to the flow front because it is much easier flowing than the plastic and forms a barrier preventing the two flow fronts from melding together. Again, no wonder weld lines are weak—this is not a junction of plastic to plastic, but of plastic to wax. Most plastics have some additive that is low in molecular weight and has the potential to phase-separate. Make a guess how many plastics people even have a hint about this issue.”
When, how, what and why to automate — leading robotics suppliers and forward-thinking moldmakers will share their insights on automating manufacturing at collocated event.
Sustainability continues to dominate new additives technology, but upping performance is also evident. Most of the new additives have been targeted to commodity resins and particularly polyolefins.
Across the show, sustainability ruled in new materials technology, from polyolefins and engineering resins to biobased materials.
I’ve been thinking about weld lines lately. We published in Plastics Technology a two-part series from Avient on molding long- and short-fiber reinforced thermoplastics; Part 2 comes out in March. Both parts note that fiber-reinforced plastics lose much of their robustness at weld lines, because the fibers tend to line up side by side, rather than “reach across” the point where flow fronts meet. It’s not just a problem for reinforced plastics.
As everyone knows, weld lines are weak points. What’s less well known is just what’s going on inside that weld line on a microstructural level. Here’s a close-up look at some nasty little secrets.
All-electric machines have made considerable headway in the marketplace, despite their higher price, and have accounted for 20% to 25% of U.S. machine sales in the last three years. All-electrics are said to provide energy savings, greater speed and precision, and cleaner, quieter operation than hydraulic-powered machines. However, one aspect of all-electric machines that may not appeal to some molders is that they are toggle-clamp machines. The rare exceptions are some small (3.2 to 7.5 tons) non-toggle electric machines built by Nissei. According to Nissei sources, this non-toggle approach is limited to such small presses because it requires larger servo motors, which add to the price premium for electric machines.
A homogenous melt is required for consistent part quality, but achieving it requires balancing a number of factors, including barrel usage and temperature as well as screw speed, backpressure and residence time. Learn how to prepare your melt for molding success in this two-part series.
The pipe and fittings manufacturer’s new 200,000-square-foot facility represents a $200 million investment and will create 150 jobs.
While the melting process does not provide perfect mixing, this study shows that mixing is indeed initiated during melting.
Plastics Technology’s Tech Days is back! Every Tuesday in October, a series of five online presentations will be given by industry supplier around the following topics: Injection Molding — New Technologies, Efficiencies Film Extrusion — New Technologies, Efficiencies Upstream/Downstream Operations Injection Molding — Sustainability Extrusion — Compounding Coming out of NPE2024, PT identified a variety of topics, technologies and trends that are driving and shaping the evolution of plastic products manufacturing — from recycling/recyclability and energy optimization to AI-based process control and automation implementation. PT Tech Days is designed to provide a robust, curated, accessible platform through which plastics professionals can explore these trends, have direct access to subject-matter experts and develop strategies for applying solutions in their operations.
While the major correction in PP prices was finally underway, generally stable pricing was anticipated for the other four commodity resins.
Like other two-platen, hydromechanical machines, most of the new hybrid clamps reduce the overall machine length vs. toggles or fully hydraulic machines. Compared with hydraulic two-platen machines, the hybrids are said to offer increased precision and accuracy and reduced maintenance.
Coverage of single-use plastics can be both misleading and demoralizing. Here are 10 tips for changing the perception of the plastics industry at your company and in your community.
Second quarter started with price hikes in PE and the four volume engineering resins, but relatively stable pricing was largely expected by the quarter’s end.
When, how, what and why to automate — leading robotics suppliers and forward-thinking moldmakers will share their insights on automating manufacturing at collocated event.
Who knows what evil lurks within weld lines? One who does know is molding expert, trainer and technical guru John Bozzelli, a prolific contributor to this magazine. When he worked in R&D at Dow Chemical, Bozzelli had access to an electron microscopy lab. He recalls the case of an unfilled ABS computer keycap back in 1987: The weld line where three flow fronts came together was “barely visible—barely a scratch to the human eye.” Under a transmission electron microscope (TEM), the ABS flow fronts appeared as a gray “soup,” larded with darker blobs of the rubber phase; but between the flow fronts, the scan was pure white. “Nobody could believe there was nothing between the flow fronts,” Bozzelli states. That was a revelation of the true nature of weld lines.
After successfully introducing a combined conference for moldmakers and injection molders in 2022, Plastics Technology and MoldMaking Technology are once again joining forces for a tooling/molding two-for-one.
Hybrid presses are well-suited to injection-compression molding. Sodick Plustech also offers the option of this novel “ejection-compression” function using its electric-powered ejector.
Mike Sepe has authored more than 25 ANTEC papers and more than 250 articles illustrating the importance of this interdisciplanary approach. In this collection, we present some of his best work during the years he has been contributing for Plastics Technology Magazine.
Join Engel in exploring the future of battery molding technology. Discover advancements in thermoplastic composites for battery housings, innovative automation solutions and the latest in large-tonnage equipment designed for e-mobility — all with a focus on cost-efficient solutions. Agenda: Learn about cutting-edge thermoplastic composites for durable, sustainable and cost-efficient battery housings Explore advanced automation concepts for efficient and scalable production See the latest large-tonnage equipment and technology innovations for e-mobility solutions
Formnext Chicago is an industrial additive manufacturing expo taking place April 8-10, 2025 at McCormick Place in Chicago, Illinois. Formnext Chicago is the second in a series of Formnext events in the U.S. being produced by Mesago Messe Frankfurt, AMT – The Association For Manufacturing Technology, and Gardner Business Media (our publisher).
Other machine functions—injection, core pull, ejection, and carriage movement—are powered by a gas accumulator and variable-volume hydraulic pump. This arrangement provide high precision, low noise, and energy consumption half that of a comparable hydraulic machine without compromising performance, says Ward.
In a time where sustainability is no longer just a buzzword, the food and beverage packaging industry is required to be at the forefront of this innovation. By adopting circular packaging processes and solutions, producers can meet regulatory requirements while also satisfying consumer demand and enhancing brand reputation. Join Husky to learn more about the broader implications of the circular economy — as well as how leading brands are leveraging this opportunity to reduce costs, increase design flexibility and boost product differentiation. Agenda: The cost and operational benefits of embracing circularity Key materials in circular packaging — including rPET and emerging bioplastics How to design a circular food and beverage package Strategies for selecting sustainable closures to future-proof packaging solutions Optimization and streamlining of production processes for enhanced efficiency How Husky Technologies can enable your sustainable success
A collaboration between show organizer PLASTICS, recycler CPR and size reduction experts WEIMA and Conair recovered and recycled all production scrap at NPE2024.
Determining the source of streaking or contamination in your molded parts is a critical step in perfecting your purging procedures ultimately saving you time and money.
Additive technology creates air pockets in film during orientation, cutting down on the amount of resin needed while boosting opacity, mechanical properties and recyclability.
What else can you do about weld lines—besides redesigning the mold or gate locations or adjust the flow pattern during fill with sequential valve gating? I recently saw a report on this issue from Moldex3D, the maker of molding simulation software. It explored the use of an overflow well (see illustration) that is designed to fill after the weld line forms, such that filling the well causes melt flow across the weld line. Simulations of 35% glass-reinforced nylon 66 indicated that higher mechanical properties should result from use of the overflow well.
technotrans says climate protection, energy efficiency and customization will be key discussion topics at PTXPO as it displays its protemp flow 6 ultrasonic eco and the teco cs 90t 9.1 TCUs.
“The toggle has greater opening force than a hydraulic clamp, and thus the toggle lends itself well to deep-draw parts,” adds Ward. Cycle time in the molding phase is also an area of debate. “With an electric driven system a user can start injection while the clamp is closing, so functions can be overlapped for cycle time savings,” says Milacron’s Royer. “Likewise, during the cooling phase, we can unlock and decompress the tonnage without opening the clamp. This can minimize the delay and shave half a second of cycle time. This unlocking step can be done with a hydraulic system, but there is a question of accuracy,” says Royer.
Mold maintenance is critical, and with this collection of content we’ve bundled some of the very best advice we’ve published on repairing, maintaining, evaluating and even hanging molds on injection molding machines.
Learn about sustainable scrap reprocessing—this resource offers a deep dive into everything from granulator types and options, to service tips, videos and technical articles.
And where would we be without the handful of uber-experienced plastics veterans who generously share their hard-earned knowledge about industry-wide problems like this?
Sodick Plustech sources say electric drive provides faster acceleration and deceleration of mold travel, as well as greater position accuracy. Meanwhile, direct hydraulic clamping reportedly provides finer pressure control, more uniform pressure distribution, delicate mold protection, and greater die-height range.
The Plastics Industry Association (PLASTICS) has released final figures for NPE2024: The Plastics Show (May 6-10; Orlando) that officially make it the largest ever NPE in several key metrics.
Successfully starting or restarting an injection molding machine is less about ticking boxes on a rote checklist and more about individually assessing each processing scenario and its unique variables.
Plastics Technology covers technical and business Information for Plastics Processors in Injection Molding, Extrusion, Blow Molding, Plastic Additives, Compounding, Plastic Materials, and Resin Pricing. About Us
It’s widely known that when flow fronts converge at a weld line, the polymer chains (like fiber reinforcements) tend not to intermingle across the boundary. As Bozzelli puts it, “Weld lines are weak because you do not have any polymer chain bridging the weld line.” But his TEM photo (not available for publication) shows that’s not just a matter of polymer chains butting up against each other without intermingling. In some, or perhaps many, areas of the weld line, the polymer chains do not even meet!
The aim of this presentation is to guide you through the factors and the numbers that will help you determine if a robot is a smart investment for your application. Agenda: Why are you considering automation? What problems are you trying to solve? How and why automation can help Crunch the numbers and determine the ROI
Mixed in among thought leaders from leading suppliers to injection molders and mold makers at the 2023 Molding and MoldMaking conferences will be molders and toolmakers themselves.
Processors with sustainability goals or mandates have a number of ways to reach their goals. Biopolymers are among them.
Multiple speakers at Molding 2023 will address the ways simulation can impact material substitution decisions, process profitability and simplification of mold design.
“Toggle units have a shorter locking time and pressure-generation time, since the design or kinematics leverage a larger force with less energy,” says John Ward, technical sales manager at Van Dorn Demag. His firm’s El-Exis machines are the only members of the hybrid category that have toggles powered by an electric servo-driven hydraulic pump.
In many part designs, flow fronts will inevitably be split, but how and where they come back together is hugely important to the molded part’s finished strength.
The Eltec hybrid from Krauss-Maffei uses electric ballscrews integrated with the tiebars for opening and closing. A self-contained, “closed-loop” hydraulic system buried inside in the fixed platen delivers 1.5 liters of oil to each tiebar for clamping. The “power nut” engages to generate clamp pressure. A “travel nut” is engaged during platen movements.
Notwithstanding these criticisms, toggle clamps remain popular and they have plenty of defenders. At least 17 firms offer all-electric presses with toggle clamps. Says Kent Royer, product sales manager for Milacron’s Roboshot electric-toggle machines, “Toggle clamps are a proven technology and offer the user reliability, simplicity, and rigidity. We have tests that show an electrically driven toggle clamp can achieve ±0.0005-in. positioning accuracy. That means that the molder who is adding automation can be sure that the robot will find the part in the same place every time.”
Second quarter started with price hikes in PE and the four volume engineering resins, but relatively stable pricing was largely expected by the quarter’s end.
Hybrid presses are made by the same firms that build hydraulic and all-electric machines, so clearly they feel the hybrids have a place. Yet they still must convince molders why they should spend more for this design than on a hydraulic model, and why they should not go all the way and get an all-electric machine.
Exhibitors and presenters at the plastics show emphasized 3D printing as a complement and aid to more traditional production processes.
Image used by John Bozzelli in his training seminars shows a short shot with a weld line forming around a square hole. In his experience, a microscopic air gap is apt to remain between the flow fronts even after the part is fully packed. (The training tool was designed by consultant Glenn Beall to illustrate design and molding problems.)
Join this webinar to explore the transformative benefits of retrofitting your existing injection molding machines (IMMs). Engel will guide you through upgrading your equipment to enhance monitoring, control and adaptability — all while integrating digital technologies. You'll learn about the latest trends in IMM retrofitting (including Euromap interfaces and plasticizing retrofits) and discover how to future-proof your machines for a competitive edge. With insights from industry experts, it'll walk you through the decision-making process, ensuring you make informed choices that drive your business forward. Agenda: Maximize the value of your current IMMs through strategic retrofitting Learn how to integrate digital technologies to enhance monitoring and control Explore the benefits of Euromap interfaces and plasticizing retrofits Understand how retrofitting can help meet new product demands and improve adaptability Discover how Engel can support your retrofitting needs, from free consultations to execution
Join Wittmann for an engaging webinar on the transformative impact of manufacturing execution systems (MES) in the plastic injection molding industry. Discover how MES enhances production efficiency, quality control and real-time monitoring while also reducing downtime. It will explore the integration of MES with existing systems, emphasizing compliance and traceability for automotive and medical sectors. Learn about the latest advancements in IoT and AI technologies and how they drive innovation and continuous improvement in MES. Agenda: Overview of MES benefits What is MES? Definition, role and brief history Historical perspective and evolution Longevity and analytics Connectivity: importance, standards and integration Advantages of MES: efficiency, real-time data, traceability and cost savings Emerging technologies: IoT and AI in MES
Another advantage claimed for hybrids is the “closed-loop” nature of their hydraulic systems. The hydraulics are completely encapsulated within one of the platens—instead of being recirculated to a central tank—so leaks are much less likely. Only a small amount of oil is used in these systems, which are designed to require no servicing by the molder. “The oil reservoir for the clamping units holds just 1 gal of oil,” says Henry Chang, Meiki’s assistant manager of customer service. “The amount is so small that the machine ships with the oil in it.” Sodick Plustech’s Eclipse and Krauss-Maffei’s Eltec machines use only about 1.5 gal of oil.
Most, though not all, of the new hybrids are two-platen clamps with a hydromechanical style of locking mechanism. Hydromechanical clamps are characterized by split nuts or other means of locking the position of the moving platen before applying clamp tonnage with one or more short-stroke or “pancake” hydraulic cylinders. In the hybrids, electric servomotors instead of hydraulics are used for mold traverse movements.
Plastics Technology covers technical and business Information for Plastics Processors in Injection Molding, Extrusion, Blow Molding, Plastic Additives, Compounding, Plastic Materials, and Resin Pricing. About Us
The new EM line from Mitsubishi (MHI) generates hydraulic clamp force on the four tiebars in the corners of the platen. An electric inverter motor drives the hydraulic system. One servomotor drives a single central ballscrew mechanism to move the platen back and forth. The drive system drives opening and closing motions up to 1.3 times faster than a conventional hydraulic Mitsubishi press. Clamp-speed accuracy is so tight that a zero setting is possible for clamp-slowdown areas, says MHI. The unit provides a mold stopping accuracy of 0.0012 in., which compares favorably to 0.039 in. for MHI’s hydraulic machine, says Tom Geddes. He adds that the platen design helps reduce deflection by at least 50%.
Across the show, sustainability ruled in new materials technology, from polyolefins and engineering resins to biobased materials.
Learn about sustainable scrap reprocessing—this resource offers a deep dive into everything from granulator types and options, to service tips, videos and technical articles.
While the melting process does not provide perfect mixing, this study shows that mixing is indeed initiated during melting.
Join Engel in exploring the future of battery molding technology. Discover advancements in thermoplastic composites for battery housings, innovative automation solutions and the latest in large-tonnage equipment designed for e-mobility — all with a focus on cost-efficient solutions. Agenda: Learn about cutting-edge thermoplastic composites for durable, sustainable and cost-efficient battery housings Explore advanced automation concepts for efficient and scalable production See the latest large-tonnage equipment and technology innovations for e-mobility solutions
Sustainability continues to dominate new additives technology, but upping performance is also evident. Most of the new additives have been targeted to commodity resins and particularly polyolefins.
Successfully starting or restarting an injection molding machine is less about ticking boxes on a rote checklist and more about individually assessing each processing scenario and its unique variables.
After successfully introducing a combined conference for moldmakers and injection molders in 2022, Plastics Technology and MoldMaking Technology are once again joining forces for a tooling/molding two-for-one.
If all this isn’t enough to inspire a righteous fear of the harm that weld lines can cause if placed in critical locations, Bozzelli knows of one more “evil” that lurks within those weld lines: “Take another look at the TEM photo of the ABS keycap. First is the air gap; but on one side, note the black line separating two flow fronts. That’s not supposed to be there. Yet another problem!”
Thousands of people visit our Supplier Guide every day to source equipment and materials. Get in front of them with a free company profile.
August 29-30 in Minneapolis all things injection molding and moldmaking will be happening at the Hyatt Regency — check out who’s speaking on what topics today.
The aim of this presentation is to guide you through the factors and the numbers that will help you determine if a robot is a smart investment for your application. Agenda: Why are you considering automation? What problems are you trying to solve? How and why automation can help Crunch the numbers and determine the ROI
The toggle clamp is styled to generate clamp forces at an angle to the mold face. Along with the platen design, it helps to drive the clamp force toward the center of the platen for uniform distribution across the mold face, says Ward. He also notes that the motor and pump work only as hard as is required to meet the instantaneous demand of the process and stop during idle portions of the cycle, rather than spilling oil over a relief valve back to the tank. “This hybrid system saves energy,” he claims. “A 200-ton conventional hydraulic machine may need 100 gal of oil, but our unit needs only 1.5 liters.” The hydrostatic system is mounted atop the clamp for ease of access.
Resin drying is a crucial, but often-misunderstood area. This collection includes details on why and what you need to dry, how to specify a dryer, and best practices.
Hybrid systems are designed to appeal to molders who like some of the features of all-electric machines but do not favor toggle clamps. Debates over the relative merits of toggles and fully hydraulic clamps have persisted for decades. Among the drawbacks cited for toggles are their more limited range of stroke adjustment and the risk that die-height adjustment when the mold is closed can lead to overclamping after the mold warms up and expands. Toggles also reportedly make it difficult to use less than maximum tonnage or to ramp tonnage up and down during a cycle. Some machine builders say that toggles also require more time for mold set-up (die-height adjustment) than a hydraulic or hybrid unit.
Mixed in among thought leaders from leading suppliers to injection molders and mold makers at the 2023 Molding and MoldMaking conferences will be molders and toolmakers themselves.
Introduced by Zeiger and Spark Industries at the PTXPO, the nozzle is designed for maximum heat transfer and uniformity with a continuous taper for self cleaning.
GETTING A QUOTE WITH LK-MOULD IS FREE AND SIMPLE.
FIND MORE OF OUR SERVICES:
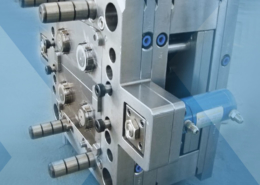
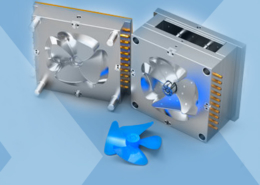
Plastic Molding

Rapid Prototyping
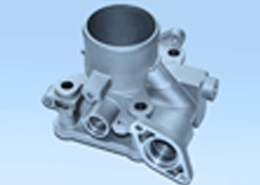
Pressure Die Casting
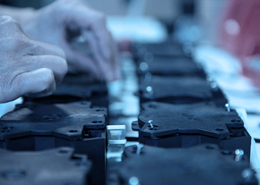
Parts Assembly
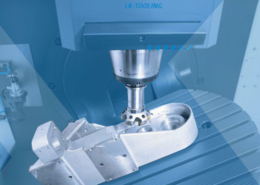