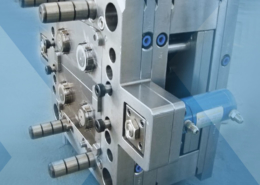
Woodland Plastics adds low-tonnage thermoset molding machine - thermoset plastic
Author:gly Date: 2024-09-30
Small pieces of plastic called microplastics can travel through wastewater into the ocean, where animals may eat them. Learn about plastics in seafood…
VEM Medical is a full-service contract manufacturing organisation for medical plastics, devices and components. We partner with medical device companies across three continents to provide plastic injection molding, in-house tooling, prototyping, assembly, testing and more. A highly experienced team, best-in-class equipment and rigorous quality control help us deliver solutions for challenging medical tooling and molding applications. For more than 20 years, VEM has focused on customer satisfaction as our highest priority. Our clients range from small innovative companies to large multinational original equipment manufacturers (OEMs). Our production facility is certified according to ISO 9001 and ISO 13485, with a Class 100,000 (ISO 8) cleanroom. VEM Medical can produce small and precise molded parts for medical devices. Our medical assembly line is inspected by a stringent quality control team. A static 2K mixer for medical applications. VEM Medical can produce injection-molded parts for medical sub-assembly. Each of our manufactured devices must pass a testing procedure specified by the customer. Medical inserts can be molded in our clean room. We produce parts through complex medical tooling. Our team sub-assembles a tube connection for a breathing device. Many different parts can be moulded in our Class 100,000 cleanroom. Medical plastics and device manufacturing VEM is an integrated partner from design assistance and design for manufacturing to finished device production and assembly. Our fully owned tool shops, cleanroom production, assembly and sub-assembly capabilities provide rich opportunities to partner with us, no matter which stage your product is in. Our experienced team uses the newest equipment and automation, including brands such as Arburg, Toshiba, GF, Hexagon and Makino. Being transparent when producing parts is what makes us stand out. Not only will we set up the production in accordance with all your needs but we can also help to improve process quality and reduce cycle times. In-house medical tooling VEM’s in-house medical molds have helped us develop medical parts for molding and assembly for years. Our fully owned mold manufacturer consistently gives us complete control over molds and materials, allowing for optimal quality control. Optimisation, rigorous quality testing, and a professional approach to solving problems have always been our key approaches. Our molds are used worldwide by large medical companies, including Danaher Corporation, Cepheid, Foamtec Medical and Freudenberg Medical. Cleanroom molding and assembly VEM can offer services in design assistance, prototyping, production mold making, injection molding in a white room or cleanroom, component sourcing, assembly, testing and packaging. Both inside and outside our cleanroom, we have room and equipment for various sizes of injection machines. Our cleanroom is built in a modular way, which allows us to be flexible and increase size as quickly as possible according to customers’ needs. Three of our global locations include high-tech tool shops, which enable us to quickly develop molds from prototype to production, as well as perform maintenance and repairs. Manufacturing transfer Thinking about moving production out of China? Facing rising costs and import/export issues with medical device production in China, VEM helps clients with an expedited manufacturing transfer of plastic injection molding and assembly projects from China to Thailand with their supply chains intact. VEM has been manufacturing in Thailand for 13 years and medical device manufacturing project transfers are among our most popular services and can be set up and running within just a few weeks. For more information, read our case study under the ‘White Papers’ tab on this page. Medical plastics and device manufacturing in Thailand Manufacturing in Southeast Asia offers a lower price point, more flexibility, and a faster time to market than domestic manufacturing can provide. For more than 13 years, VEM has operated its wholly-owned manufacturing operation in Rayong, Thailand. The largest port in Thailand, Laem Chabang Port, is just a 30-minute drive from our facility and many large medical device and healthcare manufacturers are located nearby. There is an undeniable reason behind the growth of the medical device manufacturing industry in Thailand. The location is strategically attractive due to a skilled and educated workforce, a welcoming and open economy with a stable government, quality infrastructure, lower cost of labour and reduced import taxes, and ease of import/export of raw materials and components. About VEM Medical VEM currently has five manufacturing facilities across Asia, Europe and Central America. Our facility in Thailand is ISO 13485:2016 certified and specialises in medical device production and assembly. Our tool shop in Shenzhen, China, manufactures molds for our medical device clients worldwide.
Much concern about microplastics has previously focused on their effect on the marine environment, as they are found in oceans worldwide. Many marine organisms, such as fish and shellfish, have been found to contain microplastics.
VEM Group, a global tooling and molding provider to the medical device, automotive, and consumer goods industry, has expanded operations into Eastern Europe. The wholly owned manufacturing plant is located in Plovdiv, Bulgaria, which is the cultural capital and second largest city in Bulgaria.
Being transparent when producing parts is what makes us stand out. Not only will we set up the production in accordance with all your needs but we can also help to improve process quality and reduce cycle times. In-house medical tooling VEM’s in-house medical molds have helped us develop medical parts for molding and assembly for years. Our fully owned mold manufacturer consistently gives us complete control over molds and materials, allowing for optimal quality control. Optimisation, rigorous quality testing, and a professional approach to solving problems have always been our key approaches. Our molds are used worldwide by large medical companies, including Danaher Corporation, Cepheid, Foamtec Medical and Freudenberg Medical. Cleanroom molding and assembly VEM can offer services in design assistance, prototyping, production mold making, injection molding in a white room or cleanroom, component sourcing, assembly, testing and packaging. Both inside and outside our cleanroom, we have room and equipment for various sizes of injection machines. Our cleanroom is built in a modular way, which allows us to be flexible and increase size as quickly as possible according to customers’ needs. Three of our global locations include high-tech tool shops, which enable us to quickly develop molds from prototype to production, as well as perform maintenance and repairs. Manufacturing transfer Thinking about moving production out of China? Facing rising costs and import/export issues with medical device production in China, VEM helps clients with an expedited manufacturing transfer of plastic injection molding and assembly projects from China to Thailand with their supply chains intact. VEM has been manufacturing in Thailand for 13 years and medical device manufacturing project transfers are among our most popular services and can be set up and running within just a few weeks. For more information, read our case study under the ‘White Papers’ tab on this page. Medical plastics and device manufacturing in Thailand Manufacturing in Southeast Asia offers a lower price point, more flexibility, and a faster time to market than domestic manufacturing can provide. For more than 13 years, VEM has operated its wholly-owned manufacturing operation in Rayong, Thailand. The largest port in Thailand, Laem Chabang Port, is just a 30-minute drive from our facility and many large medical device and healthcare manufacturers are located nearby. There is an undeniable reason behind the growth of the medical device manufacturing industry in Thailand. The location is strategically attractive due to a skilled and educated workforce, a welcoming and open economy with a stable government, quality infrastructure, lower cost of labour and reduced import taxes, and ease of import/export of raw materials and components. About VEM Medical VEM currently has five manufacturing facilities across Asia, Europe and Central America. Our facility in Thailand is ISO 13485:2016 certified and specialises in medical device production and assembly. Our tool shop in Shenzhen, China, manufactures molds for our medical device clients worldwide.
VEM can offer services in design assistance, prototyping, production mold making, injection molding in a white room or cleanroom, component sourcing, assembly, testing and packaging. Both inside and outside our cleanroom, we have room and equipment for various sizes of injection machines. Our cleanroom is built in a modular way, which allows us to be flexible and increase size as quickly as possible according to customers’ needs. Three of our global locations include high-tech tool shops, which enable us to quickly develop molds from prototype to production, as well as perform maintenance and repairs. Manufacturing transfer Thinking about moving production out of China? Facing rising costs and import/export issues with medical device production in China, VEM helps clients with an expedited manufacturing transfer of plastic injection molding and assembly projects from China to Thailand with their supply chains intact. VEM has been manufacturing in Thailand for 13 years and medical device manufacturing project transfers are among our most popular services and can be set up and running within just a few weeks. For more information, read our case study under the ‘White Papers’ tab on this page. Medical plastics and device manufacturing in Thailand Manufacturing in Southeast Asia offers a lower price point, more flexibility, and a faster time to market than domestic manufacturing can provide. For more than 13 years, VEM has operated its wholly-owned manufacturing operation in Rayong, Thailand. The largest port in Thailand, Laem Chabang Port, is just a 30-minute drive from our facility and many large medical device and healthcare manufacturers are located nearby. There is an undeniable reason behind the growth of the medical device manufacturing industry in Thailand. The location is strategically attractive due to a skilled and educated workforce, a welcoming and open economy with a stable government, quality infrastructure, lower cost of labour and reduced import taxes, and ease of import/export of raw materials and components. About VEM Medical VEM currently has five manufacturing facilities across Asia, Europe and Central America. Our facility in Thailand is ISO 13485:2016 certified and specialises in medical device production and assembly. Our tool shop in Shenzhen, China, manufactures molds for our medical device clients worldwide.
VEM is an integrated partner from design assistance and design for manufacturing to finished device production and assembly. Our fully owned tool shops, cleanroom production, assembly and sub-assembly capabilities provide rich opportunities to partner with us, no matter which stage your product is in. Our experienced team uses the newest equipment and automation, including brands such as Arburg, Toshiba, GF, Hexagon and Makino. Being transparent when producing parts is what makes us stand out. Not only will we set up the production in accordance with all your needs but we can also help to improve process quality and reduce cycle times. In-house medical tooling VEM’s in-house medical molds have helped us develop medical parts for molding and assembly for years. Our fully owned mold manufacturer consistently gives us complete control over molds and materials, allowing for optimal quality control. Optimisation, rigorous quality testing, and a professional approach to solving problems have always been our key approaches. Our molds are used worldwide by large medical companies, including Danaher Corporation, Cepheid, Foamtec Medical and Freudenberg Medical. Cleanroom molding and assembly VEM can offer services in design assistance, prototyping, production mold making, injection molding in a white room or cleanroom, component sourcing, assembly, testing and packaging. Both inside and outside our cleanroom, we have room and equipment for various sizes of injection machines. Our cleanroom is built in a modular way, which allows us to be flexible and increase size as quickly as possible according to customers’ needs. Three of our global locations include high-tech tool shops, which enable us to quickly develop molds from prototype to production, as well as perform maintenance and repairs. Manufacturing transfer Thinking about moving production out of China? Facing rising costs and import/export issues with medical device production in China, VEM helps clients with an expedited manufacturing transfer of plastic injection molding and assembly projects from China to Thailand with their supply chains intact. VEM has been manufacturing in Thailand for 13 years and medical device manufacturing project transfers are among our most popular services and can be set up and running within just a few weeks. For more information, read our case study under the ‘White Papers’ tab on this page. Medical plastics and device manufacturing in Thailand Manufacturing in Southeast Asia offers a lower price point, more flexibility, and a faster time to market than domestic manufacturing can provide. For more than 13 years, VEM has operated its wholly-owned manufacturing operation in Rayong, Thailand. The largest port in Thailand, Laem Chabang Port, is just a 30-minute drive from our facility and many large medical device and healthcare manufacturers are located nearby. There is an undeniable reason behind the growth of the medical device manufacturing industry in Thailand. The location is strategically attractive due to a skilled and educated workforce, a welcoming and open economy with a stable government, quality infrastructure, lower cost of labour and reduced import taxes, and ease of import/export of raw materials and components. About VEM Medical VEM currently has five manufacturing facilities across Asia, Europe and Central America. Our facility in Thailand is ISO 13485:2016 certified and specialises in medical device production and assembly. Our tool shop in Shenzhen, China, manufactures molds for our medical device clients worldwide.
VEM has been manufacturing in Thailand for 13 years and medical device manufacturing project transfers are among our most popular services and can be set up and running within just a few weeks. For more information, read our case study under the ‘White Papers’ tab on this page. Medical plastics and device manufacturing in Thailand Manufacturing in Southeast Asia offers a lower price point, more flexibility, and a faster time to market than domestic manufacturing can provide. For more than 13 years, VEM has operated its wholly-owned manufacturing operation in Rayong, Thailand. The largest port in Thailand, Laem Chabang Port, is just a 30-minute drive from our facility and many large medical device and healthcare manufacturers are located nearby. There is an undeniable reason behind the growth of the medical device manufacturing industry in Thailand. The location is strategically attractive due to a skilled and educated workforce, a welcoming and open economy with a stable government, quality infrastructure, lower cost of labour and reduced import taxes, and ease of import/export of raw materials and components. About VEM Medical VEM currently has five manufacturing facilities across Asia, Europe and Central America. Our facility in Thailand is ISO 13485:2016 certified and specialises in medical device production and assembly. Our tool shop in Shenzhen, China, manufactures molds for our medical device clients worldwide.
VEM Europe, part of VEM Group, a global tooling and molding provider to the medical device and consumer goods industry, will exhibit at the upcoming trade fair Interplas, September 28-30. It is the UK’s leading plastics industry event, an exciting showcase for technologies, manufacturing processes and services essential to the plastics sector. VEM will be exhibiting at booth C69.
Optimisation, rigorous quality testing, and a professional approach to solving problems have always been our key approaches. Our molds are used worldwide by large medical companies, including Danaher Corporation, Cepheid, Foamtec Medical and Freudenberg Medical. Cleanroom molding and assembly VEM can offer services in design assistance, prototyping, production mold making, injection molding in a white room or cleanroom, component sourcing, assembly, testing and packaging. Both inside and outside our cleanroom, we have room and equipment for various sizes of injection machines. Our cleanroom is built in a modular way, which allows us to be flexible and increase size as quickly as possible according to customers’ needs. Three of our global locations include high-tech tool shops, which enable us to quickly develop molds from prototype to production, as well as perform maintenance and repairs. Manufacturing transfer Thinking about moving production out of China? Facing rising costs and import/export issues with medical device production in China, VEM helps clients with an expedited manufacturing transfer of plastic injection molding and assembly projects from China to Thailand with their supply chains intact. VEM has been manufacturing in Thailand for 13 years and medical device manufacturing project transfers are among our most popular services and can be set up and running within just a few weeks. For more information, read our case study under the ‘White Papers’ tab on this page. Medical plastics and device manufacturing in Thailand Manufacturing in Southeast Asia offers a lower price point, more flexibility, and a faster time to market than domestic manufacturing can provide. For more than 13 years, VEM has operated its wholly-owned manufacturing operation in Rayong, Thailand. The largest port in Thailand, Laem Chabang Port, is just a 30-minute drive from our facility and many large medical device and healthcare manufacturers are located nearby. There is an undeniable reason behind the growth of the medical device manufacturing industry in Thailand. The location is strategically attractive due to a skilled and educated workforce, a welcoming and open economy with a stable government, quality infrastructure, lower cost of labour and reduced import taxes, and ease of import/export of raw materials and components. About VEM Medical VEM currently has five manufacturing facilities across Asia, Europe and Central America. Our facility in Thailand is ISO 13485:2016 certified and specialises in medical device production and assembly. Our tool shop in Shenzhen, China, manufactures molds for our medical device clients worldwide.
“The fact that just about everyone has microplastic in their blood isn’t so surprising when you consider that just about everyone has plastics additives in their bodies.”
Three of our global locations include high-tech tool shops, which enable us to quickly develop molds from prototype to production, as well as perform maintenance and repairs. Manufacturing transfer Thinking about moving production out of China? Facing rising costs and import/export issues with medical device production in China, VEM helps clients with an expedited manufacturing transfer of plastic injection molding and assembly projects from China to Thailand with their supply chains intact. VEM has been manufacturing in Thailand for 13 years and medical device manufacturing project transfers are among our most popular services and can be set up and running within just a few weeks. For more information, read our case study under the ‘White Papers’ tab on this page. Medical plastics and device manufacturing in Thailand Manufacturing in Southeast Asia offers a lower price point, more flexibility, and a faster time to market than domestic manufacturing can provide. For more than 13 years, VEM has operated its wholly-owned manufacturing operation in Rayong, Thailand. The largest port in Thailand, Laem Chabang Port, is just a 30-minute drive from our facility and many large medical device and healthcare manufacturers are located nearby. There is an undeniable reason behind the growth of the medical device manufacturing industry in Thailand. The location is strategically attractive due to a skilled and educated workforce, a welcoming and open economy with a stable government, quality infrastructure, lower cost of labour and reduced import taxes, and ease of import/export of raw materials and components. About VEM Medical VEM currently has five manufacturing facilities across Asia, Europe and Central America. Our facility in Thailand is ISO 13485:2016 certified and specialises in medical device production and assembly. Our tool shop in Shenzhen, China, manufactures molds for our medical device clients worldwide.
A new report highlights how widespread ocean pollution contributes to increasing health risks in human populations all over the world.
For this study, the researchers looked for particles that could be absorbed across membranes in the human body. They filtered the blood to collect any plastic particles between 700 nanometers(nm) and 500,000nm. To avoid any plastic contamination, the researchers used glass fiber filters.
“This paper is good news because it describes a method that is sensitive enough to do this in blood samples and combines size fractionation and mass measurements,” she added.
In a new study published in the journal Environment International, researchers in the Netherlands developed a method of analyzing human blood to detect microplastics. They then used this method to analyze blood from 22 healthy volunteers.
Facing rising costs and import/export issues with medical device production in China, VEM Medical helps clients with an expedited manufacturing transfer of plastic injection molding and assembly projects from China, where costs continue to rise, to Thailand with supply chains intact.
A recent report from the WHO examines the potential impact of microplastics on human health. The main conclusion is that more research is sorely…
Many people are too familiar with distressing images of turtles and dolphins trapped in plastic bags or fishing nets. But there is a less visible effect — microplastics, tiny plastic particles formed when plastics break down and during commercial product manufacturing.
Both inside and outside our cleanroom, we have room and equipment for various sizes of injection machines. Our cleanroom is built in a modular way, which allows us to be flexible and increase size as quickly as possible according to customers’ needs. Three of our global locations include high-tech tool shops, which enable us to quickly develop molds from prototype to production, as well as perform maintenance and repairs. Manufacturing transfer Thinking about moving production out of China? Facing rising costs and import/export issues with medical device production in China, VEM helps clients with an expedited manufacturing transfer of plastic injection molding and assembly projects from China to Thailand with their supply chains intact. VEM has been manufacturing in Thailand for 13 years and medical device manufacturing project transfers are among our most popular services and can be set up and running within just a few weeks. For more information, read our case study under the ‘White Papers’ tab on this page. Medical plastics and device manufacturing in Thailand Manufacturing in Southeast Asia offers a lower price point, more flexibility, and a faster time to market than domestic manufacturing can provide. For more than 13 years, VEM has operated its wholly-owned manufacturing operation in Rayong, Thailand. The largest port in Thailand, Laem Chabang Port, is just a 30-minute drive from our facility and many large medical device and healthcare manufacturers are located nearby. There is an undeniable reason behind the growth of the medical device manufacturing industry in Thailand. The location is strategically attractive due to a skilled and educated workforce, a welcoming and open economy with a stable government, quality infrastructure, lower cost of labour and reduced import taxes, and ease of import/export of raw materials and components. About VEM Medical VEM currently has five manufacturing facilities across Asia, Europe and Central America. Our facility in Thailand is ISO 13485:2016 certified and specialises in medical device production and assembly. Our tool shop in Shenzhen, China, manufactures molds for our medical device clients worldwide.
The researchers found PET — which most drinks bottles are made from — in the blood of more than half of those tested. They did not detect PP in any of the samples.
Several studies have found evidence of plastics in the human body. One revelation came after scientists detected plastic additives such as bisphenol A (BPA) and phthalates in human urine. Researchers have also found microplastics in human feces. However, until now, no published study has directly examined the effect of these tiny plastic specks on human health.
For more than 20 years, VEM has focused on customer satisfaction as our highest priority. Our clients range from small innovative companies to large multinational original equipment manufacturers (OEMs). Our production facility is certified according to ISO 9001 and ISO 13485, with a Class 100,000 (ISO 8) cleanroom. VEM Medical can produce small and precise molded parts for medical devices. Our medical assembly line is inspected by a stringent quality control team. A static 2K mixer for medical applications. VEM Medical can produce injection-molded parts for medical sub-assembly. Each of our manufactured devices must pass a testing procedure specified by the customer. Medical inserts can be molded in our clean room. We produce parts through complex medical tooling. Our team sub-assembles a tube connection for a breathing device. Many different parts can be moulded in our Class 100,000 cleanroom. Medical plastics and device manufacturing VEM is an integrated partner from design assistance and design for manufacturing to finished device production and assembly. Our fully owned tool shops, cleanroom production, assembly and sub-assembly capabilities provide rich opportunities to partner with us, no matter which stage your product is in. Our experienced team uses the newest equipment and automation, including brands such as Arburg, Toshiba, GF, Hexagon and Makino. Being transparent when producing parts is what makes us stand out. Not only will we set up the production in accordance with all your needs but we can also help to improve process quality and reduce cycle times. In-house medical tooling VEM’s in-house medical molds have helped us develop medical parts for molding and assembly for years. Our fully owned mold manufacturer consistently gives us complete control over molds and materials, allowing for optimal quality control. Optimisation, rigorous quality testing, and a professional approach to solving problems have always been our key approaches. Our molds are used worldwide by large medical companies, including Danaher Corporation, Cepheid, Foamtec Medical and Freudenberg Medical. Cleanroom molding and assembly VEM can offer services in design assistance, prototyping, production mold making, injection molding in a white room or cleanroom, component sourcing, assembly, testing and packaging. Both inside and outside our cleanroom, we have room and equipment for various sizes of injection machines. Our cleanroom is built in a modular way, which allows us to be flexible and increase size as quickly as possible according to customers’ needs. Three of our global locations include high-tech tool shops, which enable us to quickly develop molds from prototype to production, as well as perform maintenance and repairs. Manufacturing transfer Thinking about moving production out of China? Facing rising costs and import/export issues with medical device production in China, VEM helps clients with an expedited manufacturing transfer of plastic injection molding and assembly projects from China to Thailand with their supply chains intact. VEM has been manufacturing in Thailand for 13 years and medical device manufacturing project transfers are among our most popular services and can be set up and running within just a few weeks. For more information, read our case study under the ‘White Papers’ tab on this page. Medical plastics and device manufacturing in Thailand Manufacturing in Southeast Asia offers a lower price point, more flexibility, and a faster time to market than domestic manufacturing can provide. For more than 13 years, VEM has operated its wholly-owned manufacturing operation in Rayong, Thailand. The largest port in Thailand, Laem Chabang Port, is just a 30-minute drive from our facility and many large medical device and healthcare manufacturers are located nearby. There is an undeniable reason behind the growth of the medical device manufacturing industry in Thailand. The location is strategically attractive due to a skilled and educated workforce, a welcoming and open economy with a stable government, quality infrastructure, lower cost of labour and reduced import taxes, and ease of import/export of raw materials and components. About VEM Medical VEM currently has five manufacturing facilities across Asia, Europe and Central America. Our facility in Thailand is ISO 13485:2016 certified and specialises in medical device production and assembly. Our tool shop in Shenzhen, China, manufactures molds for our medical device clients worldwide.
However, they believe that “[i]t is scientifically plausible that plastic particles may be transported to organs via the bloodstream.”
For more information, read our case study under the ‘White Papers’ tab on this page. Medical plastics and device manufacturing in Thailand Manufacturing in Southeast Asia offers a lower price point, more flexibility, and a faster time to market than domestic manufacturing can provide. For more than 13 years, VEM has operated its wholly-owned manufacturing operation in Rayong, Thailand. The largest port in Thailand, Laem Chabang Port, is just a 30-minute drive from our facility and many large medical device and healthcare manufacturers are located nearby. There is an undeniable reason behind the growth of the medical device manufacturing industry in Thailand. The location is strategically attractive due to a skilled and educated workforce, a welcoming and open economy with a stable government, quality infrastructure, lower cost of labour and reduced import taxes, and ease of import/export of raw materials and components. About VEM Medical VEM currently has five manufacturing facilities across Asia, Europe and Central America. Our facility in Thailand is ISO 13485:2016 certified and specialises in medical device production and assembly. Our tool shop in Shenzhen, China, manufactures molds for our medical device clients worldwide.
VEM currently has five manufacturing facilities across Asia, Europe and Central America. Our facility in Thailand is ISO 13485:2016 certified and specialises in medical device production and assembly. Our tool shop in Shenzhen, China, manufactures molds for our medical device clients worldwide.
VEM Group, a global tooling and molding provider to the medical device and consumer goods industry, will exhibit at the upcoming trade fair Design & Manufacturing West, also known as MD&M West. This event is the leading U.S. tradeshow and conference for the medical device manufacturing industry which takes place August 10-12 in Anaheim, California. VEM will be exhibiting in Hall D, booth 3327.
“It’s highly probable given the prevalence of microplastics in air, water, wildlife, the food chain, that they will also be entering the human body, but the technical difficulties of measuring microplastic particles in the human body has made it hard to confirm this.”
VEM Medical is a full-service contract manufacturing organisation for medical plastics, devices and components. We partner with medical device companies across three continents to provide plastic injection molding, in-house tooling, prototyping, assembly, testing and more. A highly experienced team, best-in-class equipment and rigorous quality control help us deliver solutions for challenging medical tooling and molding applications. For more than 20 years, VEM has focused on customer satisfaction as our highest priority. Our clients range from small innovative companies to large multinational original equipment manufacturers (OEMs). Our production facility is certified according to ISO 9001 and ISO 13485, with a Class 100,000 (ISO 8) cleanroom. VEM Medical can produce small and precise molded parts for medical devices. Our medical assembly line is inspected by a stringent quality control team. A static 2K mixer for medical applications. VEM Medical can produce injection-molded parts for medical sub-assembly. Each of our manufactured devices must pass a testing procedure specified by the customer. Medical inserts can be molded in our clean room. We produce parts through complex medical tooling. Our team sub-assembles a tube connection for a breathing device. Many different parts can be moulded in our Class 100,000 cleanroom. Medical plastics and device manufacturing VEM is an integrated partner from design assistance and design for manufacturing to finished device production and assembly. Our fully owned tool shops, cleanroom production, assembly and sub-assembly capabilities provide rich opportunities to partner with us, no matter which stage your product is in. Our experienced team uses the newest equipment and automation, including brands such as Arburg, Toshiba, GF, Hexagon and Makino. Being transparent when producing parts is what makes us stand out. Not only will we set up the production in accordance with all your needs but we can also help to improve process quality and reduce cycle times. In-house medical tooling VEM’s in-house medical molds have helped us develop medical parts for molding and assembly for years. Our fully owned mold manufacturer consistently gives us complete control over molds and materials, allowing for optimal quality control. Optimisation, rigorous quality testing, and a professional approach to solving problems have always been our key approaches. Our molds are used worldwide by large medical companies, including Danaher Corporation, Cepheid, Foamtec Medical and Freudenberg Medical. Cleanroom molding and assembly VEM can offer services in design assistance, prototyping, production mold making, injection molding in a white room or cleanroom, component sourcing, assembly, testing and packaging. Both inside and outside our cleanroom, we have room and equipment for various sizes of injection machines. Our cleanroom is built in a modular way, which allows us to be flexible and increase size as quickly as possible according to customers’ needs. Three of our global locations include high-tech tool shops, which enable us to quickly develop molds from prototype to production, as well as perform maintenance and repairs. Manufacturing transfer Thinking about moving production out of China? Facing rising costs and import/export issues with medical device production in China, VEM helps clients with an expedited manufacturing transfer of plastic injection molding and assembly projects from China to Thailand with their supply chains intact. VEM has been manufacturing in Thailand for 13 years and medical device manufacturing project transfers are among our most popular services and can be set up and running within just a few weeks. For more information, read our case study under the ‘White Papers’ tab on this page. Medical plastics and device manufacturing in Thailand Manufacturing in Southeast Asia offers a lower price point, more flexibility, and a faster time to market than domestic manufacturing can provide. For more than 13 years, VEM has operated its wholly-owned manufacturing operation in Rayong, Thailand. The largest port in Thailand, Laem Chabang Port, is just a 30-minute drive from our facility and many large medical device and healthcare manufacturers are located nearby. There is an undeniable reason behind the growth of the medical device manufacturing industry in Thailand. The location is strategically attractive due to a skilled and educated workforce, a welcoming and open economy with a stable government, quality infrastructure, lower cost of labour and reduced import taxes, and ease of import/export of raw materials and components. About VEM Medical VEM currently has five manufacturing facilities across Asia, Europe and Central America. Our facility in Thailand is ISO 13485:2016 certified and specialises in medical device production and assembly. Our tool shop in Shenzhen, China, manufactures molds for our medical device clients worldwide.
The researchers suggest several ways the plastics may have entered the bloodstream — via air, food, water, personal care products such as toothpaste and lip gloss, dental polymers, and tattoo ink residues. What happens to the microplastics once they enter the bloodstream is unclear.
VEM Group, a global tooling and molding provider to the medical device and consumer goods industry, has been selected by Manufacturing Outlook magazine a Top 10 Injection Molding Service Companies 2021.
How harmful are microplastics in food, and what can we do to mitigate the health risks? In this Honest Nutrition feature, Medical News Today…
Our experienced team uses the newest equipment and automation, including brands such as Arburg, Toshiba, GF, Hexagon and Makino. Being transparent when producing parts is what makes us stand out. Not only will we set up the production in accordance with all your needs but we can also help to improve process quality and reduce cycle times. In-house medical tooling VEM’s in-house medical molds have helped us develop medical parts for molding and assembly for years. Our fully owned mold manufacturer consistently gives us complete control over molds and materials, allowing for optimal quality control. Optimisation, rigorous quality testing, and a professional approach to solving problems have always been our key approaches. Our molds are used worldwide by large medical companies, including Danaher Corporation, Cepheid, Foamtec Medical and Freudenberg Medical. Cleanroom molding and assembly VEM can offer services in design assistance, prototyping, production mold making, injection molding in a white room or cleanroom, component sourcing, assembly, testing and packaging. Both inside and outside our cleanroom, we have room and equipment for various sizes of injection machines. Our cleanroom is built in a modular way, which allows us to be flexible and increase size as quickly as possible according to customers’ needs. Three of our global locations include high-tech tool shops, which enable us to quickly develop molds from prototype to production, as well as perform maintenance and repairs. Manufacturing transfer Thinking about moving production out of China? Facing rising costs and import/export issues with medical device production in China, VEM helps clients with an expedited manufacturing transfer of plastic injection molding and assembly projects from China to Thailand with their supply chains intact. VEM has been manufacturing in Thailand for 13 years and medical device manufacturing project transfers are among our most popular services and can be set up and running within just a few weeks. For more information, read our case study under the ‘White Papers’ tab on this page. Medical plastics and device manufacturing in Thailand Manufacturing in Southeast Asia offers a lower price point, more flexibility, and a faster time to market than domestic manufacturing can provide. For more than 13 years, VEM has operated its wholly-owned manufacturing operation in Rayong, Thailand. The largest port in Thailand, Laem Chabang Port, is just a 30-minute drive from our facility and many large medical device and healthcare manufacturers are located nearby. There is an undeniable reason behind the growth of the medical device manufacturing industry in Thailand. The location is strategically attractive due to a skilled and educated workforce, a welcoming and open economy with a stable government, quality infrastructure, lower cost of labour and reduced import taxes, and ease of import/export of raw materials and components. About VEM Medical VEM currently has five manufacturing facilities across Asia, Europe and Central America. Our facility in Thailand is ISO 13485:2016 certified and specialises in medical device production and assembly. Our tool shop in Shenzhen, China, manufactures molds for our medical device clients worldwide.
In vitro studies have shown the effects of microplastics on cells. A recent study in Germany found that microplastic particles can destabilize lipid membranes — the barriers that surround all cells — which may affect their functioning. Another study found that microplastics had many effects on cells, including cell death.
A highly experienced team, best-in-class equipment and rigorous quality control help us deliver solutions for challenging medical tooling and molding applications. For more than 20 years, VEM has focused on customer satisfaction as our highest priority. Our clients range from small innovative companies to large multinational original equipment manufacturers (OEMs). Our production facility is certified according to ISO 9001 and ISO 13485, with a Class 100,000 (ISO 8) cleanroom. VEM Medical can produce small and precise molded parts for medical devices. Our medical assembly line is inspected by a stringent quality control team. A static 2K mixer for medical applications. VEM Medical can produce injection-molded parts for medical sub-assembly. Each of our manufactured devices must pass a testing procedure specified by the customer. Medical inserts can be molded in our clean room. We produce parts through complex medical tooling. Our team sub-assembles a tube connection for a breathing device. Many different parts can be moulded in our Class 100,000 cleanroom. Medical plastics and device manufacturing VEM is an integrated partner from design assistance and design for manufacturing to finished device production and assembly. Our fully owned tool shops, cleanroom production, assembly and sub-assembly capabilities provide rich opportunities to partner with us, no matter which stage your product is in. Our experienced team uses the newest equipment and automation, including brands such as Arburg, Toshiba, GF, Hexagon and Makino. Being transparent when producing parts is what makes us stand out. Not only will we set up the production in accordance with all your needs but we can also help to improve process quality and reduce cycle times. In-house medical tooling VEM’s in-house medical molds have helped us develop medical parts for molding and assembly for years. Our fully owned mold manufacturer consistently gives us complete control over molds and materials, allowing for optimal quality control. Optimisation, rigorous quality testing, and a professional approach to solving problems have always been our key approaches. Our molds are used worldwide by large medical companies, including Danaher Corporation, Cepheid, Foamtec Medical and Freudenberg Medical. Cleanroom molding and assembly VEM can offer services in design assistance, prototyping, production mold making, injection molding in a white room or cleanroom, component sourcing, assembly, testing and packaging. Both inside and outside our cleanroom, we have room and equipment for various sizes of injection machines. Our cleanroom is built in a modular way, which allows us to be flexible and increase size as quickly as possible according to customers’ needs. Three of our global locations include high-tech tool shops, which enable us to quickly develop molds from prototype to production, as well as perform maintenance and repairs. Manufacturing transfer Thinking about moving production out of China? Facing rising costs and import/export issues with medical device production in China, VEM helps clients with an expedited manufacturing transfer of plastic injection molding and assembly projects from China to Thailand with their supply chains intact. VEM has been manufacturing in Thailand for 13 years and medical device manufacturing project transfers are among our most popular services and can be set up and running within just a few weeks. For more information, read our case study under the ‘White Papers’ tab on this page. Medical plastics and device manufacturing in Thailand Manufacturing in Southeast Asia offers a lower price point, more flexibility, and a faster time to market than domestic manufacturing can provide. For more than 13 years, VEM has operated its wholly-owned manufacturing operation in Rayong, Thailand. The largest port in Thailand, Laem Chabang Port, is just a 30-minute drive from our facility and many large medical device and healthcare manufacturers are located nearby. There is an undeniable reason behind the growth of the medical device manufacturing industry in Thailand. The location is strategically attractive due to a skilled and educated workforce, a welcoming and open economy with a stable government, quality infrastructure, lower cost of labour and reduced import taxes, and ease of import/export of raw materials and components. About VEM Medical VEM currently has five manufacturing facilities across Asia, Europe and Central America. Our facility in Thailand is ISO 13485:2016 certified and specialises in medical device production and assembly. Our tool shop in Shenzhen, China, manufactures molds for our medical device clients worldwide.
“Human biomonitoring methods for measuring plastics additives have been available for several years […] But measuring microplastics, especially at the small size that would likely circulate in blood vessels (<7 microns), is very hard,” Prof. Galloway told Medical News Today.
VEM’s in-house medical molds have helped us develop medical parts for molding and assembly for years. Our fully owned mold manufacturer consistently gives us complete control over molds and materials, allowing for optimal quality control. Optimisation, rigorous quality testing, and a professional approach to solving problems have always been our key approaches. Our molds are used worldwide by large medical companies, including Danaher Corporation, Cepheid, Foamtec Medical and Freudenberg Medical. Cleanroom molding and assembly VEM can offer services in design assistance, prototyping, production mold making, injection molding in a white room or cleanroom, component sourcing, assembly, testing and packaging. Both inside and outside our cleanroom, we have room and equipment for various sizes of injection machines. Our cleanroom is built in a modular way, which allows us to be flexible and increase size as quickly as possible according to customers’ needs. Three of our global locations include high-tech tool shops, which enable us to quickly develop molds from prototype to production, as well as perform maintenance and repairs. Manufacturing transfer Thinking about moving production out of China? Facing rising costs and import/export issues with medical device production in China, VEM helps clients with an expedited manufacturing transfer of plastic injection molding and assembly projects from China to Thailand with their supply chains intact. VEM has been manufacturing in Thailand for 13 years and medical device manufacturing project transfers are among our most popular services and can be set up and running within just a few weeks. For more information, read our case study under the ‘White Papers’ tab on this page. Medical plastics and device manufacturing in Thailand Manufacturing in Southeast Asia offers a lower price point, more flexibility, and a faster time to market than domestic manufacturing can provide. For more than 13 years, VEM has operated its wholly-owned manufacturing operation in Rayong, Thailand. The largest port in Thailand, Laem Chabang Port, is just a 30-minute drive from our facility and many large medical device and healthcare manufacturers are located nearby. There is an undeniable reason behind the growth of the medical device manufacturing industry in Thailand. The location is strategically attractive due to a skilled and educated workforce, a welcoming and open economy with a stable government, quality infrastructure, lower cost of labour and reduced import taxes, and ease of import/export of raw materials and components. About VEM Medical VEM currently has five manufacturing facilities across Asia, Europe and Central America. Our facility in Thailand is ISO 13485:2016 certified and specialises in medical device production and assembly. Our tool shop in Shenzhen, China, manufactures molds for our medical device clients worldwide.
Two new studies find tiny pieces of plastic, or microplastics, in stool and table salt samples from across the globe. What does this mean for our…
Thinking about moving production out of China? Facing rising costs and import/export issues with medical device production in China, VEM helps clients with an expedited manufacturing transfer of plastic injection molding and assembly projects from China to Thailand with their supply chains intact. VEM has been manufacturing in Thailand for 13 years and medical device manufacturing project transfers are among our most popular services and can be set up and running within just a few weeks. For more information, read our case study under the ‘White Papers’ tab on this page. Medical plastics and device manufacturing in Thailand Manufacturing in Southeast Asia offers a lower price point, more flexibility, and a faster time to market than domestic manufacturing can provide. For more than 13 years, VEM has operated its wholly-owned manufacturing operation in Rayong, Thailand. The largest port in Thailand, Laem Chabang Port, is just a 30-minute drive from our facility and many large medical device and healthcare manufacturers are located nearby. There is an undeniable reason behind the growth of the medical device manufacturing industry in Thailand. The location is strategically attractive due to a skilled and educated workforce, a welcoming and open economy with a stable government, quality infrastructure, lower cost of labour and reduced import taxes, and ease of import/export of raw materials and components. About VEM Medical VEM currently has five manufacturing facilities across Asia, Europe and Central America. Our facility in Thailand is ISO 13485:2016 certified and specialises in medical device production and assembly. Our tool shop in Shenzhen, China, manufactures molds for our medical device clients worldwide.
VEM Medical provides plastic injection molding, in-house tooling, prototyping, assembly, testing and more for medical devices, plastics and components.
Plastics are everywhere. Although, in theory, much of it can be recycled, a lot of it ends up in landfills, or worse, in watercourses and marine ecosystems.
The samples from the filters were processed by double-shot pyrolysis to produce chromatograms from which scientists could identify the contents.
Microplastics are specks of plastic. By definition, they are less than 5mm in any dimension, but many are invisible to the naked eye. There are two types of microplastics: primary microplastics and secondary microplastics. The former are the particles used in some cosmetics, and the latter comes from the breakdown products of larger plastic items.
Manufacturing in Southeast Asia offers a lower price point, more flexibility, and a faster time to market than domestic manufacturing can provide. For more than 13 years, VEM has operated its wholly-owned manufacturing operation in Rayong, Thailand. The largest port in Thailand, Laem Chabang Port, is just a 30-minute drive from our facility and many large medical device and healthcare manufacturers are located nearby. There is an undeniable reason behind the growth of the medical device manufacturing industry in Thailand. The location is strategically attractive due to a skilled and educated workforce, a welcoming and open economy with a stable government, quality infrastructure, lower cost of labour and reduced import taxes, and ease of import/export of raw materials and components. About VEM Medical VEM currently has five manufacturing facilities across Asia, Europe and Central America. Our facility in Thailand is ISO 13485:2016 certified and specialises in medical device production and assembly. Our tool shop in Shenzhen, China, manufactures molds for our medical device clients worldwide.
There is an undeniable reason behind the growth of the medical device manufacturing industry in Thailand. The location is strategically attractive due to a skilled and educated workforce, a welcoming and open economy with a stable government, quality infrastructure, lower cost of labour and reduced import taxes, and ease of import/export of raw materials and components. About VEM Medical VEM currently has five manufacturing facilities across Asia, Europe and Central America. Our facility in Thailand is ISO 13485:2016 certified and specialises in medical device production and assembly. Our tool shop in Shenzhen, China, manufactures molds for our medical device clients worldwide.
GETTING A QUOTE WITH LK-MOULD IS FREE AND SIMPLE.
FIND MORE OF OUR SERVICES:
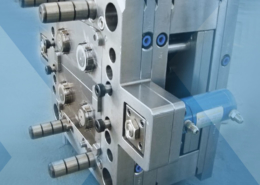
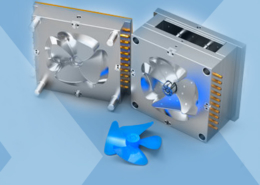
Plastic Molding

Rapid Prototyping
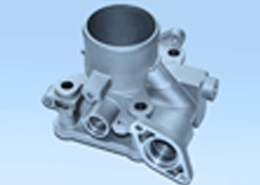
Pressure Die Casting
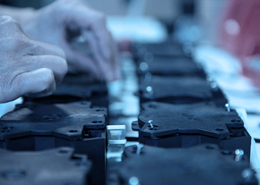
Parts Assembly
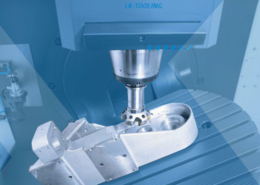