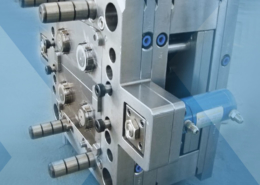
Woodland Plastics adds low-tonnage thermoset molding machine - thermoset molding
Author:gly Date: 2024-09-30
Oerlikon HRS Flow develops hot runner systems that are specifically designed for sustainable applications and that contribute to greater efficiency in injection moulding. Here, the high temperature and shear sensitivity of bio-based and biodegradable polymers are the challenges when it comes to prevent material degradation while achieving short cycle times and good gate quality. In addition, hot runner systems for recycled compounds have to be designed to avoid any damage caused by possible impurities in the melt and to avoid any streaking or flow marks that could jeopardize the cosmetic and functional result of moulding.
The micro injection molding machine market is projected to reach $609 million by 2026 from $381 million in 2021 at a 9.8% CAGR.
Newsletter content may include all products and services of any companies mentioned above, including for example specialist journals and books, events and fairs as well as event-related products and services, print and digital media offers and services such as additional (editorial) newsletters, raffles, lead campaigns, market research both online and offline, specialist webportals and e-learning offers. In case my personal telephone number has also been collected, it may be used for offers of aforementioned products, for services of the companies mentioned above, and market research purposes.
The Micro Injection Molding Machine Market is projected to reach $609 million by 2026, at a CAGR of 9.8% from $381 million in 2021, according to a report published by MarketsandMarkets.
The multi-cavity line for low shot weights, recently named MultiIflow HRS, is suitable for packaging, caps and closure as well as medical applications, manufactured with engineering polymers for technical components. Some of the main benefits include fast cycle time, high production volume, processing of PCR compounds and biopolymers, quick colour change and an excellent finish of the moulded parts.
The company’s Flexflow technology combines a servo-driven valve gate system with a flexibly programmable control system. This configuration enables precise and independent adjustment of stroke and force in the positioning of each individual nozzle during the opening and closing phases of cascading injection processes. Potential applications include future trends such as back injection of films, smart automotive surfaces and lighting.
Asia Pacific (APAC) is projected to be the fastest-growing region for the micro injection molding machine market during the forecast period, with China is the largest market by country. Increasing domestic demand due to the rapid increase in manufacturing facilities and other commercial units is expected to continue driving the demand for micro injection molding machine in the region. Increasing population and demand, accompanied by initiatives for new technologies and products, are projected to make this region a promising micro injection molding machine market. The growing population will have a significant impact on automotive and electronics industry in the region.
There it is also possible to define the optimal system configuration and to predict the part quality for special applications, using advanced hot runner systems mounted on dedicated prototype tools. Among the customer support services, plastic samples according to the weight, thickness and geometry of customer’s applications can be supplied for a preliminary analysis.
Specially developed for HDPE caps and closures, the Vf nozzles of the new multicavity line from Oerlikon HRS Flow are suitable for part weights from 0.5 g to 8 g, and they stand for reliably consistent product quality, fast colour changes and system restarts. The special nozzle tip enables optimum control in the gate area and improves cycle time. Also, its separate replaceability makes maintenance particularly fast and cost-effective.
I understand that I can revoke my consent at will. My revocation does not change the lawfulness of data processing that was conducted based on my consent leading up to my revocation. One option to declare my revocation is to use the contact form found at https://contact.vogel.de. In case I no longer wish to receive certain newsletters, I have subscribed to, I can also click on the unsubscribe link included at the end of a newsletter. Further information regarding my right of revocation and the implementation of it as well as the consequences of my revocation can be found in the data protection declaration, section editorial newsletter.
Naturally, we always handle your personal data responsibly. Any personal data we receive from you is processed in accordance with applicable data protection legislation. For detailed information please see our privacy policy.
I hereby consent to Vogel Communications Group GmbH & Co. KG, Max-Planck-Str. 7/9, 97082 Würzburg, Germany, including any affiliated companies according to §§ 15 et seq. AktG (hereafter: Vogel Communications Group) using my e-mail address to send editorial newsletters. A list of all affiliated companies can be found here
Rheologically optimised, hot runner geometries ensure significantly increased reactivity and thus effectiveness of the system. Special inserts minimise the time required for colour changes while keeping reject rates low, which contributes to the sustainability of production even with particularly critical colours.
Micro molding produces a component or part that is: micro in size, micro in features, micro in tolerances. However, the basic concept of the micro injection molding process is akin to a standard injection molding process; the micro injection unit is simply integrated into the injection molding machine.
Micro injection molding machines are machines used for the manufacture of plastics components for shot weights of 1 to 0.1 grams with tolerances in the range of 10 to 100 microns. This molding process permits the manufacture of complicated small geometries with maximum possible accuracy and precision.
The strong position of the automotive sector is a major factor driving the micro injection molding machine market. Electric vehicles are composed of various electronic parts such as all electric auxiliary, electric traction motor, traction battery pack, electric transmission, power electronics controller, and DC converter among others. These small electronics parts are composed of various micro components that are critical during vehicle manufacture and assembly. These are very small and complex components.
Imprint Cookie-Manager About Media Subscription cancellation Privacy General Terms and Conditions Help AI-Guidelines
Because the growing electric vehicle market requires more micro injection molded products than a standard internal combustion (ICE) vehicle, the increased electric demand should positively impact market growth.
An example of this, presented at Fakuma, is a smart 2K rear panel consisting of a PC+ABS frame that is overmoulded with PMMA or alternatively PC. A hydraulic 2-drop system from Oerlikon HRS Flow was used in the first injection phase, and a single nozzle from the Ga series in the second phase. Finally, the part was decorated with a capacitive and aesthetic film directly in the mould. The realisation of these complex requirements demanded exact rheological calculations.
Flexflow is also suitable for family moulds, which can offer significant cost savings compared to conventional sequential injection. An example is the use of an 8-drop system for a car door panel. Equipped with a Ma series conical valve gate, three different cavities are filled simultaneously. Thanks to extensive flow simulations carried out at Oerlikon HRS Flow, the system is perfectly balanced and enables high surface quality.
The demand for micro molded plastic parts in automotive, electronics and medical application is driving the demand for micro injection molding machine with clamping force 30 to 40 tons. However, micro injection molding machine with clamping force 0 to 10 tons is expected to grow at the highest CAGR during the forecast period.
The system, ideal for high filling pressures, is equipped with nozzles of the new Xd series, engineered for thin wall packaging applications and mounted on a 220 mm hot half plate. It is a prime solution for cost-efficient production, ensuring long term quality standards.
In case I access protected data on Internet portals of Vogel Communications Group including any affiliated companies according to §§ 15 et seq. AktG, I need to provide further data in order to register for the access to such content. In return for this free access to editorial content, my data may be used in accordance with this consent for the purposes stated here.
Especially developed for time, material and energy saving injection moulding of thin-walled packaging, the Oerlikon HRS Flow new stack mould system is dedicated to meet the latest requirements of the circular economy. Thanks to its patent-pending design, thought to make the system easy to assemble and maintain, it can be included in plug-and-play solutions that allow to avoid long and costly downtime. The stack principle also allows it to be installed in smaller injection moulding machines and enables flexible use for different applications.
By clicking on „Subscribe to Newsletter“ I agree to the processing and use of my data according to the consent form (please expand for details) and accept the Terms of Use. For more information, please see our Privacy Policy.
The shift towards nanotechnology in every sector including medical, automotive, fiber optics, electronics and others is increasing the necessity of smaller high-precision parts.
At Fakuma, the know-how of Oerlikon HRS Flow was highlighted through the display of the multi-cavity system designed for the production of 72 caps. Thanks to the new Vf nozzle series, it enables very short cycle times from 2.2 to 3.5 seconds while at the same time ensuring maximum process reliability thanks to excellent control and optimum balancing of the filling process. This technical solution, which is equally suitable for carbonated and non-carbonated beverages as well as for liquid and powdered concentrates, meets all the requirements of the new European single-use plastic directive, which makes tethered closures mandatory for all beverage containers up to three litres in capacity.
At Fakuma 2023, Oerlikon HRS Flow presented hot runner technology for more sustainability and efficiency in injection moulding. The focus was on applications such as thin-walled packaging, caps and closures as well as medical technology products and also included the processing of biopolymers and compostable compounds.
To strengthen its expertise in thin-wall packaging, the company has also expanded its injection moulding machine park in its test lab with a new hybrid Engel e-Speed 280. With its high injection pressure (up to 2,600 bar) and high-speed injection screw (up to 1,400 mm/s), it is particularly suitable for processing R-PET, bio-based and compostable polymers, in compliance with the new EU Packaging and Packaging Waste Regulation (PPWR).
This portal is a brand of Vogel Communications Group. You will find our complete range of products and services on www.vogel.com
GETTING A QUOTE WITH LK-MOULD IS FREE AND SIMPLE.
FIND MORE OF OUR SERVICES:
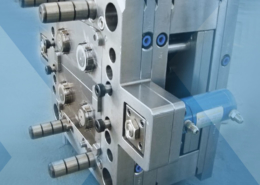
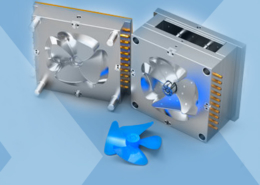
Plastic Molding

Rapid Prototyping
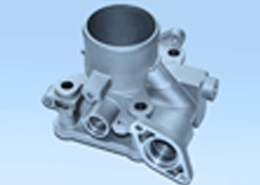
Pressure Die Casting
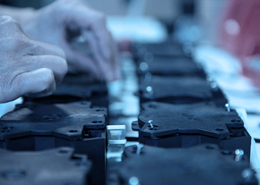
Parts Assembly
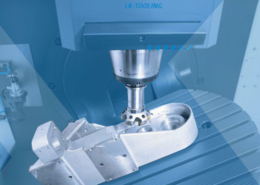