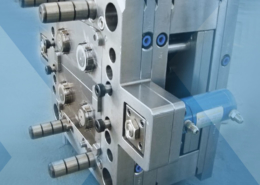
Unlocking the Potential of ABS Injection Molding: A Comprehensive Exploration
Author:gly Date: 2024-06-08
ABS injection molding stands as a cornerstone of modern manufacturing, offering unparalleled versatility, durability, and precision in the production of a wide range of components. As one of the most commonly used thermoplastics, ABS (Acrylonitrile Butadiene Styrene) has found widespread application in industries ranging from automotive and electronics to consumer goods and medical devices. In this comprehensive exploration, we delve into the world of ABS injection molding, unraveling its significance, capabilities, and impact on global manufacturing.
Introduction: The Backbone of Industrial Innovation
ABS injection molding serves as the linchpin of industrial innovation, enabling the production of complex geometries, intricate details, and customized features with exceptional precision and efficiency. As a thermoplastic polymer renowned for its strength, rigidity, and impact resistance, ABS lends itself seamlessly to injection molding processes, offering manufacturers unparalleled flexibility and performance across diverse applications. From automotive dashboards and appliance housings to electronic enclosures and toy components, ABS injection molding shapes the products we rely on daily, driving progress and prosperity in the global marketplace.
Material Properties and Performance
The success of ABS injection molding lies in its unique material properties, which combine the strength and rigidity of acrylonitrile and styrene with the toughness and impact resistance of butadiene. This versatile combination of properties makes ABS ideally suited for applications where durability, dimensional stability, and aesthetic appeal are paramount. Moreover, ABS exhibits excellent chemical resistance, thermal stability, and processability, further enhancing its suitability for injection molding processes. As such, ABS has become the material of choice for manufacturers seeking to achieve high-quality, cost-effective solutions across a diverse range of industries.
Design Freedom and Customization
One of the key advantages of ABS injection molding lies in its ability to offer design freedom and customization options to manufacturers and designers. Through advanced CAD/CAM software, mold flow analysis, and rapid prototyping technologies, designers can create intricate part geometries, fine-tune wall thicknesses, and optimize gating and cooling systems to maximize part quality and performance. Moreover, the versatility of ABS allows for the integration of features such as ribs, bosses, and snap fits, enabling designers to enhance functionality, reduce weight, and improve assembly efficiency.
Process Optimization and Efficiency
Achieving consistency, repeatability, and cost-effectiveness in ABS injection molding requires careful process optimization and control. By leveraging state-of-the-art injection molding machines, robotics, and automation technologies, manufacturers can streamline production workflows, minimize cycle times, and reduce material waste. Moreover, the adoption of advanced mold technologies, such as hot runner systems and gas-assisted injection molding, enables manufacturers to overcome challenges related to part warpage, sink marks, and surface defects, ensuring the production of high-quality, defect-free components.
Quality Assurance and Regulatory Compliance
Maintaining the highest standards of quality and regulatory compliance is paramount in ABS injection molding. Through comprehensive quality control measures, including dimensional inspection, material testing, and process validation, manufacturers ensure the integrity and performance of molded components. Moreover, adherence to industry-specific standards, such as ISO 9001 and IATF 16949, demonstrates a commitment to quality management systems and customer satisfaction. By upholding these standards, manufacturers instill confidence in customers and end-users, fostering trust and credibility in the marketplace.
Economic Considerations and Market Dynamics
The economic viability of ABS injection molding is influenced by a myriad of factors, including material costs, production volumes, labor rates, and market demand. While economies of scale and process optimization can drive down unit costs for high-volume production runs, niche markets and specialized applications may require customized solutions and higher upfront investments. Furthermore, fluctuations in raw material prices, currency exchange rates, and geopolitical factors can impact production costs and profitability, underscoring the importance of strategic planning and risk management.
Conclusion: Shaping the Future of Manufacturing
In conclusion, ABS injection molding represents not just a manufacturing process but a catalyst for innovation, efficiency, and progress in the global marketplace. By harnessing the unique properties of ABS and leveraging advanced molding technologies, manufacturers can unlock new opportunities for design innovation, performance optimization, and cost-effectiveness across industries. Looking ahead, the future of ABS injection molding holds promise for further advancements in materials science, process technologies, and product design, paving the way for a new era of manufacturing excellence and opportunity.
GETTING A QUOTE WITH LK-MOULD IS FREE AND SIMPLE.
FIND MORE OF OUR SERVICES:
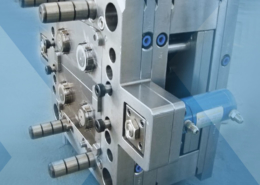
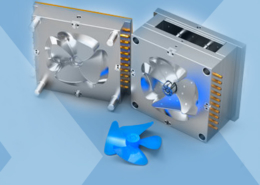
Plastic Molding

Rapid Prototyping
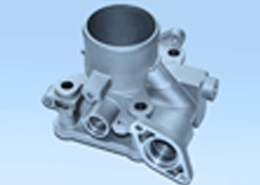
Pressure Die Casting
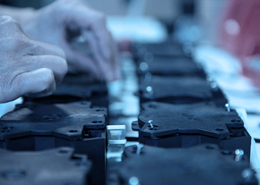
Parts Assembly
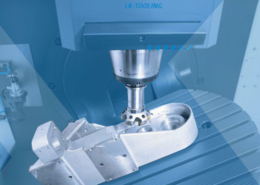