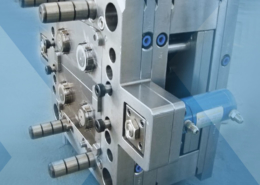
Exploring the World of 2K Injection Molding
Author:gly Date: 2024-06-08
In the realm of manufacturing, 2K injection molding stands as a pinnacle of innovation and efficiency. This advanced molding technique involves the use of two different materials injected into a single mold to produce a final product with enhanced functionality, aesthetics, and durability. Let's delve deeper into the intricacies of 2K injection molding and uncover its significance in modern manufacturing processes.
Understanding 2K Injection Molding
2K injection molding, also known as two-shot molding or multi-material molding, revolutionizes traditional injection molding by integrating two materials into a single, seamless process. This technique allows manufacturers to create complex parts with varying colors, textures, and properties in a single operation, eliminating the need for secondary assembly processes. By combining materials such as thermoplastics, elastomers, or metals, 2K injection molding enables the production of highly customized and functional components for a wide range of industries.
Process Overview
The process of 2K injection molding begins with the design of a specialized mold with multiple cavities or components. Two different materials, typically referred to as the substrate and the overmold, are selected based on their compatibility and desired properties. The first material is injected into the mold to form the substrate, followed by the injection of the second material to create the overmold layer. Through precise control of injection parameters such as temperature, pressure, and timing, manufacturers can achieve accurate placement and bonding between the two materials, resulting in a high-quality finished product.
Material Selection
Choosing the right combination of materials is crucial for the success of 2K injection molding. Factors such as compatibility, adhesion, shrinkage, and mechanical properties must be carefully considered to ensure optimal performance and durability of the final product. Thermoplastic-thermoplastic, thermoplastic-elastomer, and thermoplastic-metal combinations are commonly used in 2K molding, each offering unique advantages and challenges.
Applications and Industries
The versatility of 2K injection molding makes it suitable for a wide range of applications across various industries. From automotive components and consumer electronics to medical devices and household appliances, 2K molding offers endless possibilities for product design and innovation. Its ability to integrate multiple functions, reduce assembly steps, and enhance product aesthetics has made it a preferred choice for manufacturers seeking to stay competitive in today's fast-paced market.
Advantages and Challenges
Advantages
Cost Efficiency
: By consolidating multiple manufacturing processes into one, 2K injection molding reduces labor costs, material waste, and time-to-market, resulting in overall cost savings for manufacturers.
Design Flexibility
: The ability to combine different materials and colors in a single mold opens up new possibilities for product design and customization, allowing manufacturers to meet diverse customer demands.
Improved Product Quality
: With precise control over material distribution and bonding, 2K molding ensures consistent part quality, enhanced functionality, and better surface finish, leading to higher customer satisfaction and brand loyalty.
Challenges
Complexity
: The complexity of mold design, material selection, and process optimization can pose challenges for manufacturers new to 2K injection molding, requiring specialized expertise and equipment.
Material Compatibility
: Ensuring compatibility and adhesion between the substrate and overmold materials is critical for achieving strong bonding and avoiding delamination or defects in the final product.
Production Efficiency
: While 2K molding offers efficiency gains in terms of reduced assembly and handling, optimizing cycle times and minimizing downtime are essential for maximizing throughput and profitability.
Future Outlook and Innovations
As technology continues to advance, the future of 2K injection molding looks promising with ongoing developments in materials, equipment, and process optimization. Research into novel materials, advanced mold technologies, and automation solutions aims to further improve efficiency, quality, and sustainability in 2K molding processes. By embracing these innovations and continuously refining their processes, manufacturers can stay ahead of the curve and unlock new possibilities in product design and manufacturing.
Conclusion
In conclusion, 2K injection molding represents a transformative approach to manufacturing, offering unparalleled versatility, efficiency, and quality in the production of complex parts and components. By harnessing the power of two materials in a single process, manufacturers can achieve new levels of design flexibility, cost efficiency, and product performance, driving innovation and competitiveness in today's dynamic market landscape. As the industry continues to evolve, the future of 2K injection molding holds immense potential for revolutionizing product design, streamlining production processes, and delivering superior value to customers worldwide.
GETTING A QUOTE WITH LK-MOULD IS FREE AND SIMPLE.
FIND MORE OF OUR SERVICES:
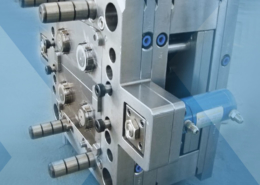
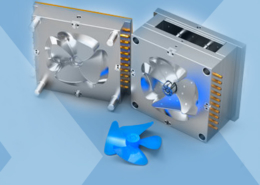
Plastic Molding

Rapid Prototyping
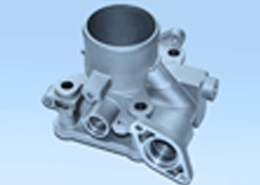
Pressure Die Casting
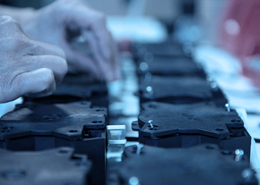
Parts Assembly
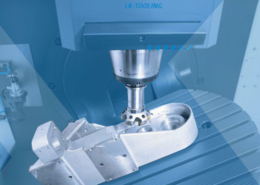