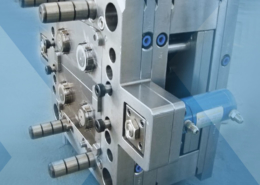
Exploring the Versatility of ABS Injection Moulding
Author:gly Date: 2024-06-08
ABS injection moulding stands as a cornerstone in the realm of plastic manufacturing, offering a versatile solution for producing a wide array of products. This article aims to delve into the world of ABS injection moulding, providing readers with insights into its applications, properties, advantages, challenges, and future prospects.
Introduction to ABS Injection Moulding
ABS (Acrylonitrile Butadiene Styrene) injection moulding is a widely used manufacturing process for producing plastic parts with superior mechanical properties, impact resistance, and surface finish. ABS resin, a thermoplastic polymer composed of acrylonitrile, butadiene, and styrene monomers, exhibits excellent dimensional stability, chemical resistance, and aesthetic appeal, making it a preferred choice for various industries such as automotive, electronics, consumer goods, and construction.
Background and Significance
The adoption of ABS injection moulding technology has revolutionized the production of plastic components, enabling manufacturers to achieve complex geometries, intricate details, and precise features with high efficiency and reliability. With its ability to meet stringent performance requirements, withstand harsh environmental conditions, and facilitate cost-effective mass production, ABS injection moulding plays a vital role in modern manufacturing processes.
Properties and Characteristics of ABS
ABS resin possesses a unique combination of properties that make it well-suited for injection moulding applications, including:
Mechanical Strength and Toughness
ABS exhibits excellent mechanical strength and toughness, making it suitable for producing durable, impact-resistant parts that can withstand varying loads, stresses, and temperatures. Its ability to absorb energy and resist deformation makes ABS an ideal choice for applications requiring structural integrity and reliability.
Surface Finish and Aesthetic Appeal
ABS resin can be easily molded to achieve smooth, glossy surfaces with high dimensional accuracy and aesthetic appeal. Its ability to retain intricate details and decorative features makes ABS suitable for producing visually appealing products such as consumer electronics, appliances, and automotive interior components.
Advantages of ABS Injection Moulding
ABS injection moulding offers numerous advantages over other plastic molding processes, including:
Design Flexibility and Versatility
ABS injection moulding allows for the creation of complex, multi-functional parts with precise features and geometries. Its compatibility with various secondary processes such as painting, plating, and printing further enhances design flexibility and customization options, enabling manufacturers to meet diverse customer requirements.
Cost-Effectiveness and Production Efficiency
ABS injection moulding offers cost-effective production solutions for high-volume manufacturing, thanks to its fast cycle times, minimal scrap rates, and efficient material usage. The ability to produce large quantities of parts with consistent quality and dimensional accuracy contributes to lower production costs and faster time-to-market for products.
Challenges and Future Perspectives
Despite its numerous advantages, ABS injection moulding poses challenges related to material properties, processing parameters, and environmental considerations. Addressing these challenges requires ongoing research, innovation, and collaboration across the industry.
Material Selection and Recycling
Selecting the right grade of ABS resin and optimizing processing parameters are critical for achieving desired part properties and performance. Additionally, increasing emphasis on environmental sustainability and circular economy principles necessitates the development of recyclable, bio-based ABS materials and eco-friendly injection moulding processes.
Advanced Technologies and Industry Trends
Looking ahead, advancements in additive manufacturing, Industry 4.0 integration, and sustainable materials will shape the future of ABS injection moulding. Emerging technologies such as 3D printing, digital twin simulations, and bio-based polymers offer promising opportunities for enhancing product design, manufacturing efficiency, and environmental stewardship.
Conclusion and Future Directions
In conclusion, ABS injection moulding remains a cornerstone of modern manufacturing, offering unparalleled versatility, performance, and cost-effectiveness for producing a wide range of plastic products. By leveraging its unique properties, design flexibility, and production efficiency, ABS injection moulding continues to drive innovation and competitiveness in various industries.
Looking ahead, future research and development efforts should focus on advancing material science, process technology, and sustainability initiatives to further enhance the capabilities and sustainability of ABS injection moulding. By embracing emerging technologies and industry trends, manufacturers can unlock new opportunities and overcome challenges, paving the way for a more efficient, resilient, and sustainable future in plastic manufacturing.
GETTING A QUOTE WITH LK-MOULD IS FREE AND SIMPLE.
FIND MORE OF OUR SERVICES:
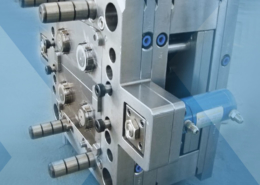
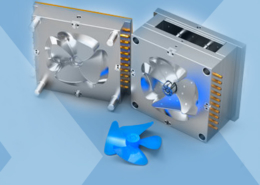
Plastic Molding

Rapid Prototyping
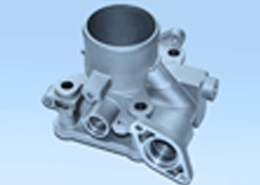
Pressure Die Casting
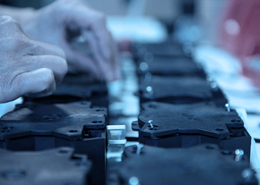
Parts Assembly
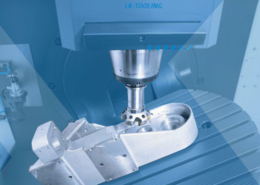