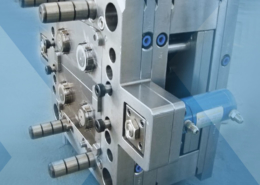
Unraveling the Science of Injection Molding: A Deep Dive into Scientific Molding
Author:gly Date: 2024-06-08
Introduction:
Scientific molding stands as a pinnacle of precision and efficiency in the realm of injection molding, revolutionizing the way plastic components are manufactured. Rooted in the principles of material science, process optimization, and data-driven decision-making, scientific molding transcends traditional practices to deliver unparalleled quality and consistency. In this article, we embark on a journey to unravel the intricacies of scientific molding, exploring its foundations, methodologies, and transformative impact on the manufacturing landscape.
1. Understanding the Fundamentals
At the heart of scientific molding lies a deep understanding of material behavior, process dynamics, and tooling design. Unlike conventional molding approaches that rely on trial-and-error methods, scientific molding embraces a systematic and data-centric approach to process optimization. By leveraging principles of rheology, thermodynamics, and fluid mechanics, manufacturers can gain profound insights into material flow behavior, thermal characteristics, and mold filling dynamics.
Furthermore, scientific molding emphasizes the importance of robust process control parameters, such as injection pressure, temperature, and cooling rates. Through meticulous experimentation and analysis, molders can identify the optimal processing conditions that yield consistent part quality and dimensional accuracy. This holistic understanding of the molding process lays the foundation for continuous improvement and innovation in the field of injection molding.
2. Implementing Advanced Process Monitoring
Central to the success of scientific molding is the integration of advanced process monitoring and control systems. Real-time data acquisition technologies, such as pressure transducers, temperature sensors, and cavity pressure monitoring systems, enable molders to capture invaluable insights into process variability and part quality. By analyzing key performance indicators (KPIs) such as fill time, pressure profile, and cooling efficiency, manufacturers can diagnose potential defects and optimize process parameters proactively.
Moreover, the advent of Industry 4.0 technologies has ushered in a new era of connectivity and automation in injection molding. Smart manufacturing platforms leverage machine learning algorithms and predictive analytics to anticipate process deviations and preemptively adjust machine settings. This data-driven approach not only enhances production efficiency but also minimizes scrap rates and rework, driving significant cost savings for manufacturers.
3. Leveraging Simulation and Virtual Prototyping
Simulation tools play a pivotal role in the scientific molding process, allowing manufacturers to validate design concepts and optimize process parameters virtually. Finite element analysis (FEA) and mold flow simulation software simulate material behavior under varying processing conditions, enabling engineers to predict potential defects such as warpage, sink marks, and air traps. By iteratively refining mold designs and process settings in a virtual environment, manufacturers can minimize trial runs and expedite time-to-market.
Furthermore, virtual prototyping facilitates collaboration and communication across multidisciplinary teams, enabling stakeholders to visualize and iterate on design concepts in real-time. This agile approach to product development fosters innovation and accelerates the pace of technological advancement in the injection molding industry.
4. Driving Continuous Improvement and Innovation
Scientific molding embodies a culture of continuous improvement and innovation, where data-driven insights drive iterative refinement of processes and products. By establishing key performance indicators (KPIs) and performance benchmarks, manufacturers can monitor process stability and identify areas for enhancement. Furthermore, cross-functional collaboration between design, engineering, and production teams fosters a holistic approach to problem-solving and innovation.
Moreover, the adoption of lean manufacturing principles and Six Sigma methodologies empowers organizations to streamline workflows, eliminate waste, and optimize resource utilization. By fostering a culture of continuous learning and adaptation, manufacturers can stay ahead of the curve in an increasingly competitive marketplace and drive sustainable growth and profitability.
Conclusion:
In conclusion, scientific molding represents a paradigm shift in the field of injection molding, ushering in a new era of precision, efficiency, and innovation. By embracing principles of material science, process optimization, and data-driven decision-making, manufacturers can achieve unprecedented levels of part quality, consistency, and cost-effectiveness. As we look towards the future, the potential for further advancements in scientific molding technology remains boundless, promising a future where manufacturing excellence knows no bounds.
GETTING A QUOTE WITH LK-MOULD IS FREE AND SIMPLE.
FIND MORE OF OUR SERVICES:
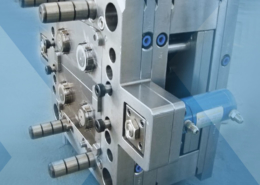
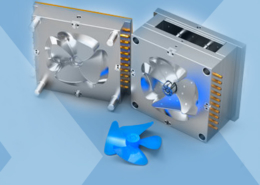
Plastic Molding

Rapid Prototyping
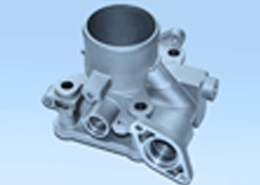
Pressure Die Casting
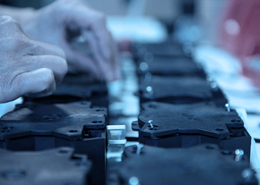
Parts Assembly
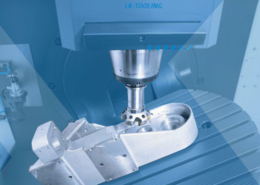