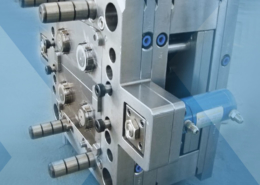
Short Mold in Injection Molding: Redefining Efficiency
Author:gly Date: 2024-06-08
Short mold in injection molding represents a groundbreaking approach to optimizing production processes, offering enhanced efficiency, reduced material wastage, and improved cost-effectiveness. This article aims to explore the concept of short mold in injection molding, providing readers with a comprehensive understanding of its significance, applications, and potential impact on modern manufacturing practices.
Unveiling the Concept of Short Mold
Short mold, also known as reduced-height mold or low-profile mold, refers to a specialized mold design that minimizes the distance between the mold cavity and the parting line. Unlike traditional molds, which feature standard mold heights, short molds are characterized by their compact design, allowing for shorter molding cycles and reduced material consumption. This innovative approach aims to streamline the injection molding process, optimize production efficiency, and mitigate manufacturing costs.
Evolution and Adoption
The evolution of short mold in injection molding mirrors the continuous quest for efficiency and optimization in manufacturing. As industries strive to meet escalating demands for faster production cycles and higher output volumes, the adoption of short molds has gained momentum across various sectors. From automotive and electronics to consumer goods and medical devices, manufacturers are embracing this novel approach to enhance productivity and competitiveness in the global market.
Design Considerations and Benefits
Short mold design encompasses a myriad of considerations, ranging from mold geometry and cooling system layout to part ejection mechanisms and material flow dynamics. By minimizing mold height, short molds facilitate quicker cooling times, thereby reducing cycle times and increasing throughput. Moreover, the compact design of short molds translates into lower material costs, as less material is required to fill the reduced cavity volume. Additionally, shorter mold cycles enable manufacturers to meet stringent production deadlines and respond swiftly to market demands, thereby enhancing operational agility and customer satisfaction.
Technical Insights and Innovations
Short mold in injection molding is underpinned by a range of technical insights and innovations, driving continuous improvement and optimization. Advanced simulation software allows engineers to simulate mold filling, cooling, and part ejection processes, enabling precise optimization of short mold designs for maximum efficiency and quality. Furthermore, the integration of sensor technology and real-time monitoring systems enhances process control and quality assurance, minimizing defects and ensuring consistency in production outcomes.
Challenges and Solutions
Despite its numerous benefits, short mold in injection molding presents certain challenges, including increased mold complexity, limited cavity space, and potential design constraints. Addressing these challenges requires a holistic approach, encompassing innovative design methodologies, advanced materials, and cutting-edge manufacturing techniques. Through collaborative research and development efforts, industry stakeholders can overcome these hurdles and unlock the full potential of short mold technology, paving the way for enhanced productivity, sustainability, and competitiveness in the manufacturing landscape.
Future Directions and Opportunities
Looking ahead, the future of short mold in injection molding holds immense promise for further innovation and advancement. Continued research into material science, mold design, and process optimization will drive the development of next-generation short mold solutions with enhanced performance and versatility. Furthermore, the integration of digitalization, automation, and additive manufacturing technologies will revolutionize the production landscape, enabling on-demand manufacturing, mass customization, and agile supply chains.
Conclusion
In conclusion, short mold in injection molding represents a transformative paradigm shift in modern manufacturing, offering unprecedented levels of efficiency, flexibility, and cost-effectiveness. By reimagining traditional mold design principles and embracing innovative technologies, manufacturers can optimize production processes, reduce lead times, and elevate product quality to new heights. As we navigate the dynamic landscape of 21st-century manufacturing, the adoption of short mold technology holds the key to unlocking new opportunities, driving sustainable growth, and shaping the future of industry innovation.
GETTING A QUOTE WITH LK-MOULD IS FREE AND SIMPLE.
FIND MORE OF OUR SERVICES:
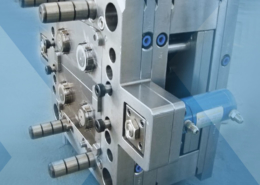
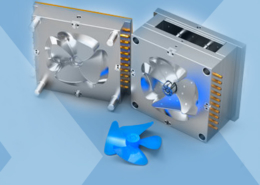
Plastic Molding

Rapid Prototyping
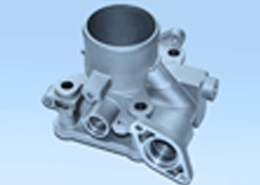
Pressure Die Casting
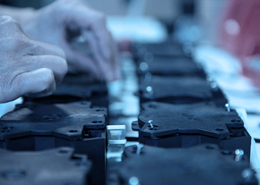
Parts Assembly
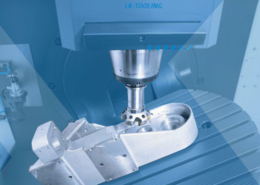