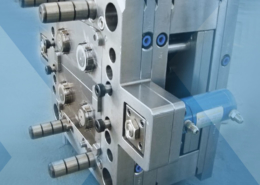
Unraveling the World of Rubber Plastic Molding
Author:gly Date: 2024-06-08
Introduction
Rubber plastic molding stands at the intersection of versatility and innovation in modern manufacturing. This intricate process involves shaping and forming rubber and plastic materials into a diverse range of products, spanning from everyday consumer goods to critical industrial components. Exploring the realm of rubber plastic molding unveils a world where creativity meets precision, where material science converges with engineering prowess, and where every mold tells a story of ingenuity.
Understanding Rubber Plastic Molding
Rubber plastic molding encompasses a variety of techniques aimed at molding rubber and plastic materials into desired shapes and forms. From injection molding to compression molding, each method offers unique advantages in terms of precision, efficiency, and material compatibility.
Injection Molding: Precision at Scale
Injection molding is a widely utilized technique in rubber plastic molding, offering unparalleled precision and scalability. Through the injection of molten rubber or plastic into a mold cavity, manufacturers can produce complex geometries with consistent quality and minimal waste. This process finds applications in industries ranging from automotive to medical, where precision and efficiency are paramount.
Compression Molding: Versatility and Durability
Compression molding, another common method in rubber plastic molding, relies on the application of heat and pressure to shape materials within a mold cavity. This technique is favored for its versatility, allowing for the production of large, intricate parts with excellent durability and strength. From automotive components to industrial seals, compression molding caters to diverse applications where robustness is essential.
Overmolding: Enhancing Functionality and Aesthetics
Overmolding is a specialized process in rubber plastic molding that involves encapsulating a substrate with a layer of rubber or plastic. This technique not only enhances the functionality and durability of products but also allows for creative designs and aesthetic customization. Overmolded components, such as ergonomic handles and soft-touch grips, exemplify the fusion of form and function in modern product design.
Material Selection and Optimization
Material selection plays a crucial role in rubber plastic molding, influencing the performance, appearance, and cost-effectiveness of the final product.
Rubber Materials: Elasticity and Resilience
Rubber materials offer unique properties such as elasticity, resilience, and chemical resistance, making them ideal for applications requiring flexibility and durability. Natural rubber, synthetic elastomers, and thermoplastic elastomers each have distinct advantages and applications in rubber plastic molding, catering to diverse industry needs.
Plastic Polymers: Versatility and Stability
Plastic polymers boast a wide range of properties, including high strength-to-weight ratio, chemical resistance, and thermal stability. Polyethylene, polypropylene, and polycarbonate are among the commonly used plastics in rubber plastic molding, offering versatility in design and performance across various applications.
Material Optimization: Balancing Performance and Cost
Optimizing material selection involves striking a balance between performance requirements and cost considerations. By leveraging advanced materials science and engineering expertise, manufacturers can tailor material formulations to meet specific application needs while optimizing production efficiency and cost-effectiveness.
Technological Advancements and Future Trends
The landscape of rubber plastic molding continues to evolve with advancements in technology, materials, and manufacturing processes.
Industry 4.0 Integration: Smart Manufacturing
The integration of Industry 4.0 technologies, such as automation, robotics, and artificial intelligence, revolutionizes rubber plastic molding processes. Smart manufacturing solutions enable real-time monitoring, predictive maintenance, and data-driven optimization, enhancing efficiency, quality, and sustainability.
Sustainable Practices: Eco-Friendly Solutions
Amid growing environmental concerns, rubber plastic molding manufacturers are embracing sustainable practices to minimize waste, energy consumption, and environmental impact. From recyclable materials to closed-loop manufacturing systems, sustainable solutions underscore a commitment to responsible production and resource stewardship.
Advanced Design Tools: Digital Innovation
Digital design tools, such as computer-aided design (CAD) software and simulation technologies, empower manufacturers to optimize product designs and manufacturing processes. Virtual prototyping, mold flow analysis, and topology optimization enable faster iterations, reduced time-to-market, and enhanced product performance.
Conclusion
In conclusion, rubber plastic molding represents a convergence of innovation, versatility, and sustainability in modern manufacturing. From injection molding to compression molding, the myriad techniques and materials at play underscore the complexity and diversity of this field. By leveraging technological advancements, embracing sustainable practices, and fostering collaboration across disciplines, rubber plastic molding manufacturers can continue to drive innovation and meet the evolving needs of industries worldwide. As we look towards the future, the journey of rubber plastic molding unfolds with endless possibilities, shaping a world where imagination meets engineering excellence.
GETTING A QUOTE WITH LK-MOULD IS FREE AND SIMPLE.
FIND MORE OF OUR SERVICES:
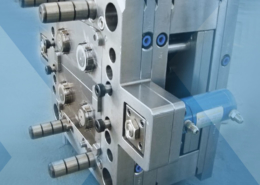
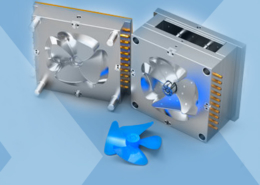
Plastic Molding

Rapid Prototyping
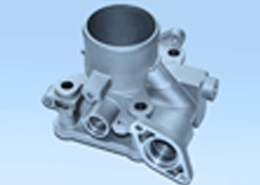
Pressure Die Casting
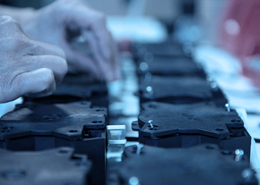
Parts Assembly
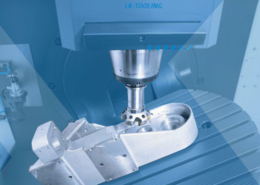