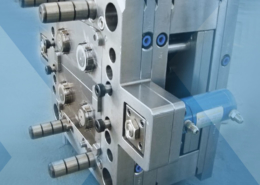
Understanding Prototype Plastic Injection Molding
Author:gly Date: 2024-06-08
In the realm of manufacturing, Prototype Plastic Injection Molding stands as a pivotal process, revolutionizing the way products are developed and brought to market. It embodies the fusion of precision engineering and innovation, shaping raw materials into intricate designs with unparalleled accuracy. This article aims to delve into the depths of Prototype Plastic Injection Molding, exploring its nuances, applications, and significance in modern industrial practices.
Introduction
Prototype Plastic Injection Molding serves as the cornerstone of rapid prototyping, enabling manufacturers to swiftly transform conceptual designs into tangible prototypes. By injecting molten thermoplastic materials into custom molds, this technique facilitates the creation of intricate components with exceptional detail and consistency.
The Process
Injection Phase
The process commences with the injection phase, where the chosen thermoplastic material is heated to its melting point and injected into the mold cavity under high pressure. This phase demands precise control over temperature, pressure, and injection speed to ensure uniformity and quality in the final product.
Cooling and Solidification
Following injection, the mold undergoes a cooling and solidification phase, where the molten material solidifies to form the desired shape. Effective cooling systems are crucial during this stage to expedite the solidification process and minimize cycle times.
Ejection
Once the plastic has solidified, the mold opens, and the newly formed part is ejected. This phase requires careful attention to prevent damage to the part or the mold, ensuring smooth and seamless ejection.
Materials
A diverse range of thermoplastic materials can be utilized in Prototype Plastic Injection Molding, each offering unique properties and characteristics. From ABS and polycarbonate to nylon and polypropylene, manufacturers can tailor material selection to suit specific application requirements, whether it be durability, flexibility, or chemical resistance.
Applications
Product Development
Prototype Plastic Injection Molding plays a pivotal role in product development, enabling designers and engineers to iterate designs quickly and cost-effectively. By producing functional prototypes, manufacturers can conduct thorough testing and validation, identifying and rectifying potential issues before mass production.
Customization
In addition to prototyping, this technique facilitates customization, allowing manufacturers to cater to diverse customer needs and preferences. Whether it's personalized consumer products or bespoke industrial components, Prototype Plastic Injection Molding offers unparalleled versatility and flexibility in design.
Low-Volume Production
Beyond prototyping, Prototype Plastic Injection Molding is also well-suited for low-volume production runs. With minimal tooling and setup costs, manufacturers can produce small batches of parts economically, catering to niche markets and specialty applications.
Advantages and Challenges
Advantages
Rapid Prototyping: Accelerates product development cycles.
Cost-Effective: Reduces time and expenses associated with traditional manufacturing methods.
High Precision: Delivers intricate designs with minimal tolerances.
Challenges
Tooling Costs: Initial investment in molds can be significant.
Design Limitations: Complexity of parts may be constrained by mold design and manufacturing capabilities.
Material Selection: Choosing the right material is critical to achieving desired performance and aesthetics.
Conclusion
In conclusion, Prototype Plastic Injection Molding stands as a cornerstone of modern manufacturing, revolutionizing the way products are developed, customized, and produced. Its versatility, precision, and efficiency make it an indispensable tool for designers, engineers, and manufacturers alike. As technology continues to evolve, the potential applications of this technique are limitless, promising exciting possibilities for innovation and advancement in the industrial landscape.
GETTING A QUOTE WITH LK-MOULD IS FREE AND SIMPLE.
FIND MORE OF OUR SERVICES:
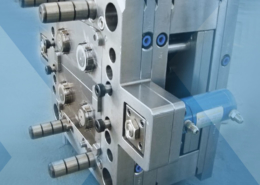
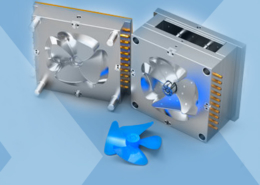
Plastic Molding

Rapid Prototyping
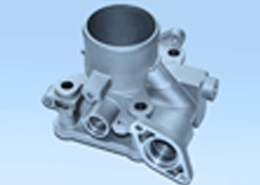
Pressure Die Casting
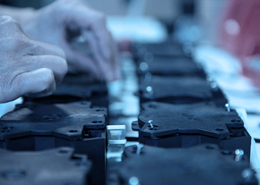
Parts Assembly
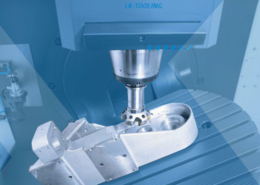