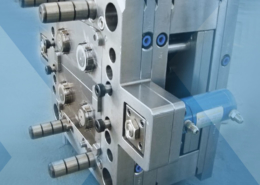
Exploring Prototype Plastic Molding
Author:gly Date: 2024-06-08
Prototype plastic molding stands as a beacon of innovation in the manufacturing realm, revolutionizing the way products are conceptualized, designed, and brought to fruition. This article embarks on a journey into the realm of prototype plastic molding, aiming to captivate readers' interest by unraveling its intricacies and unveiling its significance in modern industrial practices.
Introduction
Prototype plastic molding represents a pivotal stage in the product development process, serving as the bridge between ideation and realization. It encompasses a spectrum of techniques aimed at creating prototypes of varying complexities, enabling designers and engineers to refine their concepts and validate their designs before proceeding to full-scale production.
Evolution of Prototype Plastic Molding
Historical Perspectives
The roots of prototype plastic molding can be traced back to the early 20th century when rudimentary injection molding techniques emerged. Over the decades, advancements in materials science, machinery, and manufacturing processes have propelled prototype plastic molding into the forefront of modern industrial practices.
Technological Advancements
The advent of computer-aided design (CAD) and computer-aided manufacturing (CAM) has revolutionized prototype plastic molding, empowering designers to create intricate geometries with unparalleled precision. Additive manufacturing technologies, such as 3D printing, have further expanded the possibilities, offering rapid prototyping capabilities and reducing time-to-market for innovative products.
Industry Applications
From aerospace and automotive industries to consumer electronics and medical devices, prototype plastic molding finds applications across diverse sectors. It enables manufacturers to test new designs, evaluate performance, and gather feedback from end-users, fostering iterative improvements and innovation.
Key Processes
Injection Molding
Injection molding stands as the cornerstone of prototype plastic molding, involving the injection of molten thermoplastic materials into a mold cavity. This process offers high precision, repeatability, and scalability, making it ideal for producing complex geometries with tight tolerances.
Compression Molding
Compression molding entails the compression of preheated thermosetting materials within a mold cavity, followed by curing under heat and pressure. While traditionally associated with mass production, compression molding is also utilized in prototype plastic molding for its ability to produce parts with excellent surface finish and dimensional stability.
Vacuum Casting
Vacuum casting involves the replication of master patterns using silicone molds and polyurethane resins. This process is well-suited for low-volume production of prototypes, offering a cost-effective alternative to injection molding for small batch sizes.
Material Selection
Thermoplastic Polymers
A myriad of thermoplastic polymers, including ABS, polycarbonate, and nylon, are utilized in prototype plastic molding. Each material exhibits distinct properties, such as strength, flexibility, and chemical resistance, allowing designers to tailor material selection to meet specific application requirements.
Thermosetting Resins
Thermosetting resins, such as epoxy and silicone, are favored for their superior heat resistance and dimensional stability. These materials are commonly used in applications where high temperature performance and durability are paramount, such as in aerospace and automotive components.
Challenges and Opportunities
Design Complexity
The complexity of prototype designs presents a challenge in terms of mold design and manufacturing feasibility. However, advancements in mold-making technologies and simulation software mitigate these challenges, enabling the realization of intricate geometries with minimal iterations.
Time-to-Market
Speed-to-market is crucial in today's competitive landscape, necessitating rapid prototyping techniques that accelerate the product development cycle. Prototype plastic molding offers a streamlined approach to iterative design, reducing lead times and enabling faster market entry.
Conclusion
In conclusion, prototype plastic molding embodies the convergence of innovation, precision, and versatility, empowering manufacturers to translate ideas into reality with unprecedented efficiency. Its applications span across industries, driving innovation and fueling technological advancements. As we embark on the journey of technological evolution, prototype plastic molding remains poised to reshape the future of manufacturing, unlocking new possibilities and driving transformative change.
GETTING A QUOTE WITH LK-MOULD IS FREE AND SIMPLE.
FIND MORE OF OUR SERVICES:
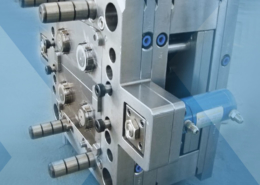
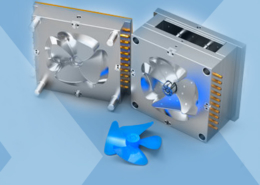
Plastic Molding

Rapid Prototyping
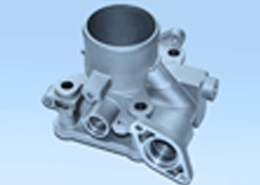
Pressure Die Casting
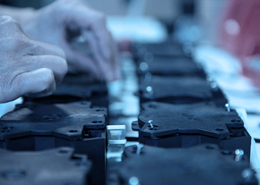
Parts Assembly
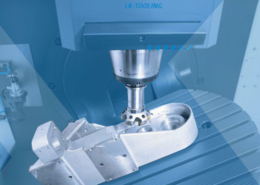