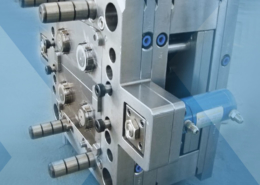
Exploring the Intersection of Prototype and Plastic Mold
Author:gly Date: 2024-06-08
The world of manufacturing is constantly evolving, driven by innovation, efficiency, and the quest for perfection. At the heart of this evolution lies the symbiotic relationship between prototype development and plastic mold fabrication. In this article, we delve into the dynamic interplay between prototype and plastic mold, unraveling its significance, applications, and implications for the future of manufacturing.
Introducing Prototype and Plastic Mold
The Essence of Prototyping
Prototyping serves as a fundamental step in the product development process, allowing designers and engineers to validate concepts, test functionality, and iterate designs before moving into full-scale production. By creating physical prototypes, manufacturers can identify potential issues early on, streamline the design process, and ultimately, reduce time to market.
The Role of Plastic Mold
Plastic mold fabrication, on the other hand, plays a pivotal role in transforming design concepts into tangible products. Plastic molds serve as the backbone of injection molding, enabling the mass production of plastic components with precision, consistency, and efficiency. By leveraging advanced molding techniques and materials, manufacturers can produce high-quality parts at scale, meeting the demands of diverse industries.
Exploring Key Aspects
Prototyping Methods
Various prototyping methods exist, each offering unique advantages and applications. From rapid prototyping technologies like 3D printing and CNC machining to traditional methods such as hand sculpting and foam modeling, designers and engineers have a plethora of tools at their disposal to bring their ideas to life. The choice of prototyping method depends on factors such as complexity, material requirements, and budget constraints.
Design for Manufacturability
Designing for manufacturability is crucial when transitioning from prototype to plastic mold. Engineers must optimize designs for injection molding, considering factors such as part geometry, draft angles, wall thickness, and undercuts. By incorporating manufacturability considerations early in the design process, manufacturers can minimize production costs, reduce cycle times, and enhance product quality.
Meeting Industry Demands
Customization and Flexibility
The synergy between prototype and plastic mold offers unparalleled customization and flexibility in manufacturing. With rapid prototyping and mold fabrication capabilities, manufacturers can respond quickly to changing market demands, customize products to meet customer specifications, and iterate designs on the fly. This agility is particularly valuable in industries with short product lifecycles and evolving consumer preferences.
Quality Assurance and Optimization
Quality assurance is paramount in both prototyping and plastic mold fabrication. Manufacturers employ rigorous testing, inspection, and validation processes to ensure that prototypes and molds meet the highest quality standards. By leveraging advanced simulation tools and optimization techniques, engineers can fine-tune designs, minimize defects, and optimize production processes for efficiency and consistency.
Conclusion: Shaping the Future of Manufacturing
In conclusion, the synergy between prototype development and plastic mold fabrication represents a cornerstone of modern manufacturing. By seamlessly integrating prototyping and mold fabrication processes, manufacturers can accelerate innovation, enhance product quality, and drive business growth. As technology continues to advance and barriers to entry diminish, the future holds exciting possibilities for the convergence of prototype and plastic mold, paving the way for a new era of manufacturing excellence and innovation.
GETTING A QUOTE WITH LK-MOULD IS FREE AND SIMPLE.
FIND MORE OF OUR SERVICES:
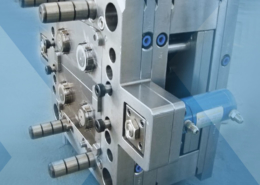
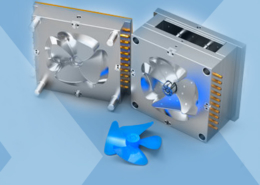
Plastic Molding

Rapid Prototyping
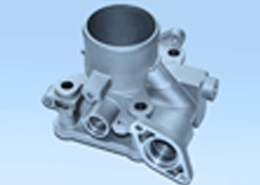
Pressure Die Casting
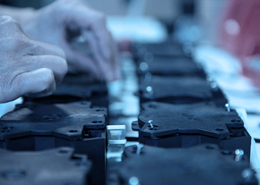
Parts Assembly
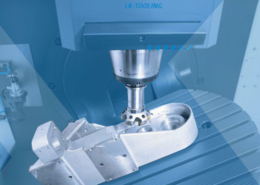