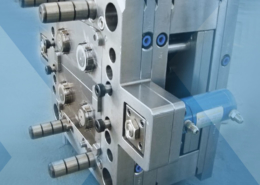
Precision Plastic Molding: Revolutionizing Manufacturing
Author:gly Date: 2024-06-08
Precision plastic molding stands at the forefront of modern manufacturing, redefining possibilities in various industries. It encompasses a sophisticated process where intricate designs are transformed into high-quality plastic components with remarkable accuracy and efficiency. This article aims to delve into the nuances of precision plastic molding, exploring its intricacies, applications, and impact on contemporary production methods.
The Essence of Precision Plastic Molding
Precision plastic molding epitomizes the fusion of artistry and technology, where raw materials are meticulously shaped into intricate forms with unparalleled precision. This process involves the injection of molten plastic into precise molds, enabling the creation of complex geometries and intricate details. By harnessing advanced machinery and computer-aided design (CAD) software, manufacturers can achieve consistency and precision in every component produced.
Historical Evolution
The evolution of precision plastic molding traces back to the mid-20th century, marked by significant advancements in materials science and manufacturing technology. Early techniques, such as compression molding and transfer molding, laid the groundwork for contemporary injection molding processes. Over the decades, innovations in materials, machinery, and automation have propelled precision plastic molding to unprecedented levels of sophistication and efficiency.
Key Components and Processes
At the heart of precision plastic molding lies a synergy of key components and processes. Injection molding machines, molds, and thermoplastic resins form the backbone of this intricate system. The process begins with the design and fabrication of molds, tailored to meet the specific requirements of each component. Molten plastic is then injected into the mold cavity under high pressure, where it solidifies and takes the desired shape. Subsequent stages, such as cooling, ejection, and finishing, ensure the production of flawless components.
Advantages and Applications
The advantages of precision plastic molding are manifold, driving its widespread adoption across diverse industries. From automotive and aerospace to healthcare and consumer electronics, precision plastic components play a pivotal role in various applications. The process offers unparalleled design flexibility, allowing for the creation of complex shapes, intricate details, and customized features. Moreover, precision molding enables cost-effective mass production, rapid prototyping, and superior quality control, making it indispensable in modern manufacturing.
Innovations and Future Prospects
As technology continues to evolve, precision plastic molding is poised for further innovations and advancements. The integration of artificial intelligence (AI), additive manufacturing, and sustainable materials holds promise for the future of plastic molding. AI-driven process optimization, coupled with 3D printing capabilities, could revolutionize the production of intricate components with enhanced efficiency and sustainability. Furthermore, the exploration of bio-based polymers and recyclable materials heralds a new era of eco-friendly manufacturing practices, aligning with the growing emphasis on environmental stewardship.
Challenges and Opportunities
Despite its myriad benefits, precision plastic molding faces certain challenges, including material selection, tooling complexity, and quality control. Addressing these challenges requires a holistic approach, encompassing research, innovation, and collaboration across disciplines. Moreover, as the demand for customized products and shorter lead times continues to rise, manufacturers must embrace agile manufacturing strategies and digital technologies to stay competitive in the global market.
Conclusion
In conclusion, precision plastic molding represents a paradigm shift in modern manufacturing, offering unparalleled precision, efficiency, and versatility. From its humble origins to its current state of the art, this process continues to redefine the possibilities of plastic fabrication. By embracing innovation, sustainability, and collaboration, the future of precision plastic molding holds immense promise for revolutionizing industries and shaping a more sustainable and interconnected world. As we embark on this journey of exploration and innovation, let us harness the power of precision plastic molding to unlock new frontiers and transform ideas into reality.
GETTING A QUOTE WITH LK-MOULD IS FREE AND SIMPLE.
FIND MORE OF OUR SERVICES:
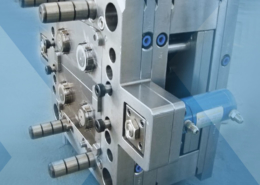
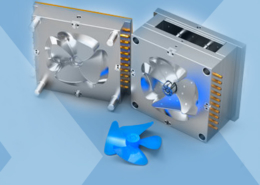
Plastic Molding

Rapid Prototyping
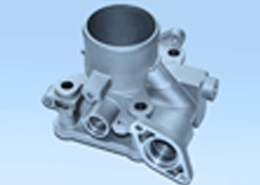
Pressure Die Casting
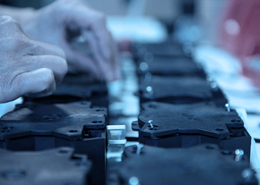
Parts Assembly
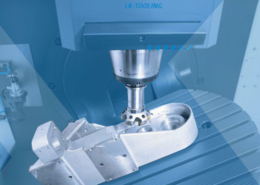