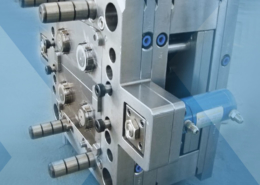
Understanding Polymer Injection Molding: Revolutionizing Manufacturing Processes
Author:gly Date: 2024-06-08
Polymer injection molding stands as a cornerstone in modern manufacturing, revolutionizing industries with its efficiency, versatility, and precision. This article serves as a comprehensive exploration of polymer injection molding, elucidating its mechanisms, applications, advancements, and future prospects.
Introduction: Unveiling the Essence of Polymer Injection Molding
Polymer injection molding is a manufacturing process that involves injecting molten polymer materials into a mold cavity under high pressure. The molten material then solidifies, taking the shape of the mold cavity, and is subsequently ejected as a finished product. This method has gained immense popularity due to its ability to produce complex shapes with high accuracy and repeatability.
Advantages of Polymer Injection Molding
Polymer injection molding offers numerous advantages over traditional manufacturing methods. Firstly, it enables mass production of intricate components with minimal waste. Secondly, it allows for the use of a wide range of materials, including thermoplastics, thermosets, and elastomers, catering to diverse industry needs. Additionally, it facilitates cost-effective production by reducing labor and material expenses.
Polymer injection molding also boasts superior efficiency and consistency compared to alternative processes. With precise control over temperature, pressure, and cooling rates, manufacturers can achieve tight tolerances and uniformity in their products. Furthermore, advancements in automation and computer-aided design (CAD) have further streamlined the process, enhancing productivity and reducing lead times.
Applications Across Industries
The versatility of polymer injection molding extends across various industries, including automotive, aerospace, electronics, medical, and consumer goods. In the automotive sector, it is utilized for manufacturing interior and exterior components, such as dashboards, bumpers, and lighting systems. In aerospace, it facilitates the production of lightweight and durable parts for aircraft and spacecraft.
Moreover, polymer injection molding plays a pivotal role in the electronics industry, enabling the fabrication of intricate housings, connectors, and casings for electronic devices. In the medical field, it is instrumental in producing precise and biocompatible components for surgical instruments, implants, and diagnostic equipment. Additionally, consumer goods such as toys, appliances, and packaging rely on this method for efficient and cost-effective production.
Recent Advances and Innovations
Recent years have witnessed significant advancements in polymer injection molding technology, enhancing its capabilities and expanding its applications. One notable development is the integration of additive manufacturing techniques, such as 3D printing, into the injection molding process. This hybrid approach allows for the creation of customized molds with intricate geometries, optimizing part performance and reducing tooling costs.
Furthermore, the adoption of advanced materials, including bioplastics and composites, has broadened the range of applications for polymer injection molding. These materials offer enhanced strength, durability, and sustainability, aligning with the growing emphasis on eco-friendly manufacturing practices. Additionally, innovations in mold design, cooling systems, and process monitoring have improved efficiency, quality control, and cycle times.
Challenges and Future Directions
Despite its myriad benefits, polymer injection molding faces certain challenges, including issues related to material selection, process optimization, and environmental impact. Addressing these challenges requires ongoing research and development efforts aimed at enhancing material properties, refining process parameters, and implementing sustainable practices.
Looking ahead, the future of polymer injection molding lies in embracing advanced technologies such as artificial intelligence, machine learning, and digital twins. These technologies hold the potential to optimize process parameters, predict defects, and minimize downtime, thereby further improving efficiency and reducing costs. Moreover, continued collaboration between industry stakeholders, academia, and government agencies is essential for driving innovation and ensuring the continued evolution of polymer injection molding.
Conclusion: Shaping the Future of Manufacturing
In conclusion, polymer injection molding stands as a cornerstone of modern manufacturing, offering unparalleled efficiency, versatility, and precision. Its widespread applications across industries have transformed the way products are designed, produced, and distributed. By embracing innovation, overcoming challenges, and fostering collaboration, the future of polymer injection molding holds immense promise in shaping a more efficient, sustainable, and technologically advanced manufacturing landscape.
GETTING A QUOTE WITH LK-MOULD IS FREE AND SIMPLE.
FIND MORE OF OUR SERVICES:
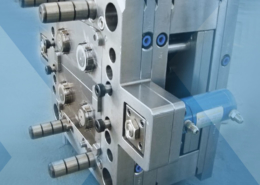
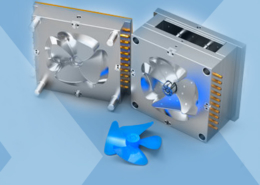
Plastic Molding

Rapid Prototyping
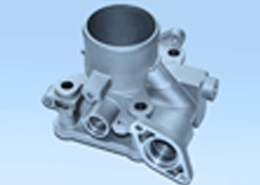
Pressure Die Casting
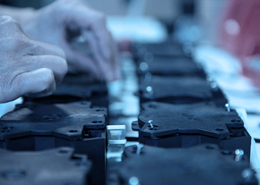
Parts Assembly
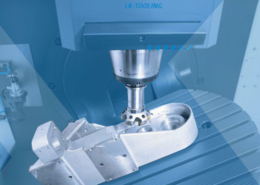