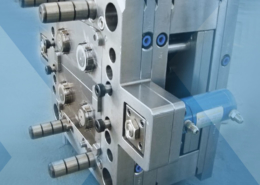
Exploring the World of Polyethylene Moulding
Author:gly Date: 2024-06-08
Polyethylene moulding stands as a cornerstone in the realm of plastic manufacturing, offering unparalleled versatility, durability, and cost-effectiveness. In this comprehensive discourse, we delve into the intricacies of polyethylene moulding, from its inception to its modern applications and future prospects.
Unveiling Polyethylene Moulding
Polyethylene moulding refers to the process of shaping and forming polyethylene, a thermoplastic polymer, into desired shapes and sizes using moulding techniques such as injection moulding, blow moulding, and rotational moulding. Polyethylene, characterized by its lightweight nature, excellent chemical resistance, and low cost, has emerged as one of the most widely used plastics in various industries.
The origins of polyethylene moulding can be traced back to the mid-20th century, with the development of high-density polyethylene (HDPE) and low-density polyethylene (LDPE) by scientists seeking to create versatile materials for diverse applications. Since then, continuous advancements in material science, processing technologies, and mould design have propelled polyethylene moulding to the forefront of modern manufacturing.
Advantages of Polyethylene Moulding
Polyethylene moulding offers a myriad of advantages over traditional materials and manufacturing processes, making it an attractive choice for a wide range of applications. Firstly, polyethylene exhibits excellent chemical resistance, making it suitable for use in corrosive environments such as chemical processing, water treatment, and agricultural applications.
Moreover, polyethylene's lightweight nature and durability make it ideal for applications requiring strength-to-weight ratio, such as automotive components, packaging materials, and outdoor furniture. Additionally, polyethylene is recyclable and can be processed using sustainable methods, aligning with the growing emphasis on environmental sustainability in manufacturing.
Process and Techniques
The process of polyethylene moulding encompasses various techniques tailored to specific applications and part geometries. Injection moulding, the most common method, involves injecting molten polyethylene into a mould cavity under high pressure, where it solidifies to form the desired shape. This technique is widely used for manufacturing intricate components with tight tolerances, such as automotive parts and household appliances.
Blow moulding, on the other hand, involves extruding a hollow tube of molten polyethylene, known as a parison, into a mould cavity, where it is inflated to conform to the shape of the mould. This technique is commonly employed for producing hollow products such as bottles, containers, and tanks.
Rotational moulding, a versatile technique suited for large, hollow components, entails rotating a mould containing powdered polyethylene in multiple axes while heating it to melt and coat the interior surface of the mould. This process is widely used in industries such as automotive, aerospace, and recreational equipment.
Applications Across Industries
Polyethylene moulding finds extensive applications across a diverse range of industries, ranging from packaging and construction to healthcare and transportation. In the packaging industry, polyethylene is utilized for manufacturing bottles, containers, and films, due to its excellent barrier properties and versatility.
In the construction sector, polyethylene is employed for producing pipes, fittings, and insulation materials, offering durability, flexibility, and resistance to harsh environmental conditions. Moreover, in the healthcare industry, polyethylene is used for manufacturing medical devices, such as syringes, catheters, and implantable components, due to its biocompatibility and sterilizability.
Challenges and Future Directions
Despite its numerous advantages, polyethylene moulding faces challenges such as material degradation, process optimization, and environmental impact. Addressing these challenges requires ongoing research and development efforts aimed at enhancing material properties, process efficiency, and sustainability.
Looking ahead, the future of polyethylene moulding lies in innovation and collaboration across industries, leveraging emerging technologies such as additive manufacturing, digital design, and recycled materials. By embracing these advancements, manufacturers can unlock new opportunities for product innovation, process optimization, and environmental stewardship.
In Conclusion
Polyethylene moulding stands as a testament to the ingenuity and versatility of modern manufacturing, offering unparalleled capabilities and benefits across industries. With continuous innovation and collaboration, polyethylene moulding will continue to drive efficiency, sustainability, and innovation in the ever-evolving landscape of plastic manufacturing.
GETTING A QUOTE WITH LK-MOULD IS FREE AND SIMPLE.
FIND MORE OF OUR SERVICES:
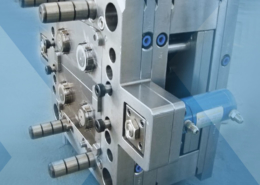
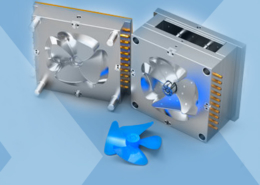
Plastic Molding

Rapid Prototyping
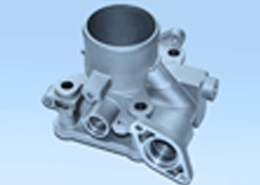
Pressure Die Casting
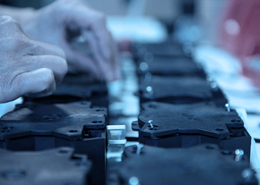
Parts Assembly
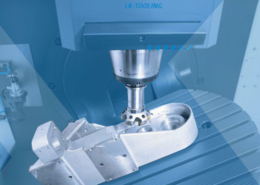