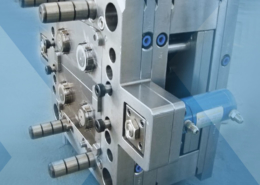
PP Injection Molding: Unveiling the Power of Polypropylene
Author:gly Date: 2024-06-08
Polypropylene (PP) injection molding stands as a cornerstone in the realm of plastic manufacturing, offering versatility, durability, and cost-effectiveness. This article delves into the intricacies of PP injection molding, exploring its methodology, applications, advantages, challenges, and future prospects.
Introduction: Embracing Innovation
PP injection molding revolutionizes the production of plastic components, captivating engineers and manufacturers with its versatility and efficiency. As one of the most widely used thermoplastics, PP boasts a plethora of desirable properties, including high chemical resistance, stiffness, and low density, making it an ideal candidate for a myriad of applications. From automotive parts to packaging materials, PP injection molding permeates various industries, driving innovation and efficiency.
Methodology: Crafting Excellence
PP injection molding involves melting PP resin pellets and injecting the molten material into a mold cavity under high pressure. The mold is then cooled, solidifying the material into the desired shape. This meticulous process demands precise control over parameters such as temperature, pressure, and cooling rates to ensure optimal results. Advanced technologies, including computer-aided design (CAD) and finite element analysis (FEA), facilitate the design and simulation of molds, augmenting the efficiency and accuracy of the process.
Applications: Pervasive Presence
The versatility of PP injection molding renders it indispensable across a myriad of applications. In the automotive industry, PP is used to fabricate interior and exterior components such as bumpers, dashboards, and door panels, owing to its lightweight nature and impact resistance. In the consumer goods sector, PP finds applications in the production of food containers, packaging materials, and household appliances, leveraging its high chemical resistance and durability. Additionally, PP injection molding is employed in the medical field for manufacturing disposable syringes, vials, and surgical instruments, adhering to stringent regulatory requirements.
Advantages: Unlocking Potential
PP injection molding confers a plethora of advantages, cementing its position as a preferred manufacturing technique. Firstly, it offers unparalleled design freedom, enabling the production of complex geometries and intricate details with precision. Moreover, PP exhibits excellent chemical resistance and thermal stability, ensuring the longevity and reliability of molded components. Additionally, PP injection molding facilitates rapid prototyping and iteration, expediting product development cycles and reducing time-to-market.
Challenges: Navigating Complexity
Despite its manifold advantages, PP injection molding poses several challenges. Achieving uniform filling of the mold cavity while minimizing defects such as warpage, sink marks, and flash necessitates meticulous process optimization and control. Moreover, variations in material properties and environmental factors can introduce inconsistencies, mandating continuous monitoring and adjustment. Additionally, the selection of suitable PP grades and additives poses a challenge, as it directly impacts the mechanical properties and performance of molded components.
Future Prospects: Pioneering Innovation
The future of PP injection molding is imbued with promise and innovation. Advancements in material science, including the development of bio-based PP and recyclable additives, promise to enhance sustainability and reduce environmental impact. Furthermore, the integration of Industry 4.0 technologies, such as Internet of Things (IoT) sensors and predictive analytics, holds the potential to optimize process parameters and enhance efficiency. Additionally, the adoption of advanced manufacturing techniques, including multi-material molding and micro-injection molding, may unlock new possibilities for PP applications.
Conclusion: Embracing the Future
In conclusion, PP injection molding epitomizes the convergence of precision, versatility, and efficiency in plastic manufacturing. Its methodology, applications, advantages, challenges, and future prospects underscore its significance in driving innovation and progress. As we navigate an era of relentless change and disruption, embracing advancements in materials, technologies, and methodologies will be paramount in unlocking the full potential of PP injection molding. By fostering collaboration, innovation, and sustainability, we can pave the way towards a future where PP injection molding continues to shape industries and improve lives.
With these insights in mind, let us embark on a journey of discovery and innovation, harnessing the transformative power of PP injection molding to build a brighter and more sustainable future.
GETTING A QUOTE WITH LK-MOULD IS FREE AND SIMPLE.
FIND MORE OF OUR SERVICES:
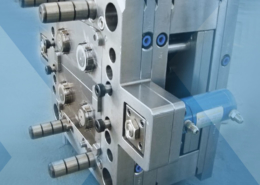
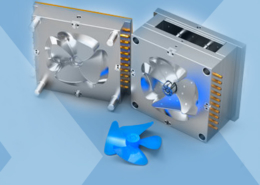
Plastic Molding

Rapid Prototyping
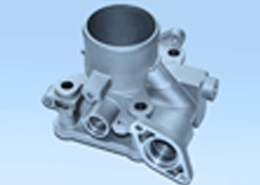
Pressure Die Casting
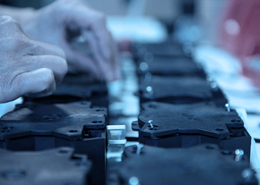
Parts Assembly
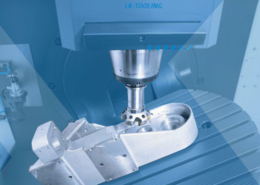