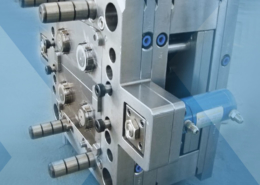
Unlocking the Potential of Polycarbonate Injection
Author:gly Date: 2024-06-08
Polycarbonate injection molding stands as a pinnacle in modern manufacturing, offering unparalleled strength, transparency, and versatility in the production of plastic components. In this comprehensive exploration, we delve into the intricacies of polycarbonate injection molding, from its historical roots to its contemporary applications and future prospects, aiming to pique the curiosity of readers and provide a thorough understanding of this fascinating technique.
Introducing Polycarbonate Injection Molding
Polycarbonate injection molding is a manufacturing process that involves injecting molten polycarbonate resin into a mold cavity under high pressure, where it solidifies to form intricate and durable plastic components. Polycarbonate, known for its exceptional impact resistance, optical clarity, and heat resistance, has emerged as a preferred material for applications requiring high-performance plastics.
The origins of polycarbonate date back to the mid-20th century, with commercial production commencing in the 1950s by Bayer AG. Since then, polycarbonate has gained widespread adoption in various industries, including automotive, electronics, aerospace, and medical, due to its unique combination of properties and processing advantages.
Advantages of Polycarbonate Injection Molding
Polycarbonate injection molding offers a plethora of advantages over traditional materials and manufacturing processes, making it an attractive choice for a wide range of applications. Firstly, polycarbonate exhibits exceptional impact resistance, making it ideal for applications requiring durability and toughness, such as automotive components, safety helmets, and electronic enclosures.
Moreover, polycarbonate boasts excellent optical clarity and transparency, allowing for the production of clear and aesthetically pleasing components for applications such as lenses, windows, and display screens. Additionally, polycarbonate injection molding enables the production of complex geometries and intricate designs with high precision and repeatability, catering to diverse customer needs and design specifications.
Process and Techniques
The process of polycarbonate injection molding involves several steps, including material preparation, mold design, injection molding, cooling, and part ejection. Firstly, polycarbonate resin pellets are fed into a heated barrel of an injection molding machine, where they are melted and homogenized to form a viscous molten state.
Next, the molten polycarbonate is injected into a mold cavity under high pressure, where it fills the cavity and takes the shape of the mold. The mold is then cooled to solidify the polycarbonate, after which the molded part is ejected from the mold cavity and trimmed to remove any excess material or flash.
Applications Across Industries
Polycarbonate injection molding finds extensive applications across various industries, ranging from automotive and aerospace to electronics and consumer goods. In the automotive sector, polycarbonate is used for manufacturing exterior components such as bumpers, body panels, and headlamp lenses, due to its lightweight nature, impact resistance, and design flexibility.
Similarly, in the electronics industry, polycarbonate injection molding is employed for producing housing and enclosures for electronic devices, such as smartphones, tablets, and laptops, providing protection and aesthetics while accommodating complex assemblies. Moreover, in the medical sector, polycarbonate is utilized for manufacturing medical devices and equipment, including surgical instruments, diagnostic devices, and drug delivery systems, due to its biocompatibility and sterilizability.
Challenges and Future Directions
Despite its numerous advantages, polycarbonate injection molding faces challenges such as mold design complexity, material degradation, and environmental sustainability. Addressing these challenges requires ongoing research and development efforts aimed at enhancing process efficiency, material properties, and recycling technologies.
Looking ahead, the future of polycarbonate injection molding lies in innovation and collaboration across industries, leveraging emerging technologies such as additive manufacturing, digital design, and sustainable materials. By embracing these advancements, manufacturers can unlock new opportunities for product innovation, process optimization, and environmental stewardship.
In Conclusion
Polycarbonate injection molding stands as a testament to the ingenuity and versatility of modern manufacturing, offering unparalleled capabilities and benefits across industries. With continuous innovation and collaboration, polycarbonate injection molding will continue to drive efficiency, sustainability, and innovation in the ever-evolving landscape of plastic manufacturing.
GETTING A QUOTE WITH LK-MOULD IS FREE AND SIMPLE.
FIND MORE OF OUR SERVICES:
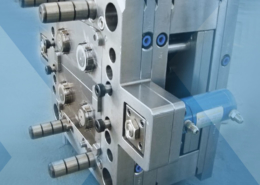
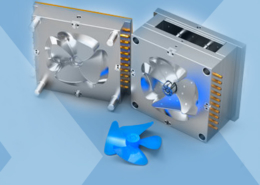
Plastic Molding

Rapid Prototyping
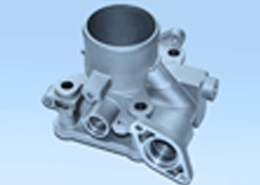
Pressure Die Casting
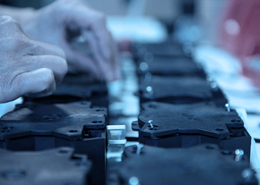
Parts Assembly
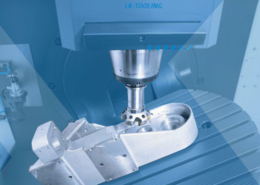