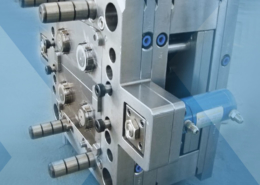
Exploring the Versatility of PMMA Molding
Author:gly Date: 2024-06-08
PMMA molding stands as a testament to the ingenuity of modern manufacturing, offering unparalleled precision, clarity, and versatility in the production of plastic components. In this comprehensive exploration, we delve into the intricacies of PMMA molding, from its historical roots to its contemporary applications and future prospects.
Unveiling PMMA Molding
PMMA, or polymethyl methacrylate, commonly known as acrylic or acrylic glass, is a transparent thermoplastic with exceptional optical clarity and weather resistance. PMMA molding refers to the process of shaping and forming PMMA into desired shapes and sizes using molding techniques such as injection molding, extrusion molding, and vacuum forming.
The origins of PMMA can be traced back to the early 20th century, with commercial production beginning in the 1930s by German chemists. Since then, PMMA has gained widespread adoption in various industries, including automotive, construction, electronics, and healthcare, due to its unique combination of optical clarity, impact resistance, and ease of processing.
Advantages of PMMA Molding
PMMA molding offers a plethora of advantages over traditional materials and manufacturing processes, making it an attractive choice for a wide range of applications. Firstly, PMMA exhibits exceptional optical properties, including high transparency and light transmission, making it ideal for applications requiring optical clarity, such as lenses, displays, and lighting fixtures.
Moreover, PMMA is highly resistant to yellowing and degradation from UV exposure, making it suitable for outdoor applications such as signage, architectural glazing, and automotive lenses. Additionally, PMMA's ease of processing and compatibility with various molding techniques enable the production of complex geometries and intricate designs with minimal waste and high precision.
Process and Techniques
The process of PMMA molding encompasses various techniques tailored to specific applications and part geometries. Injection molding, the most common method, involves injecting molten PMMA into a mold cavity under high pressure, where it solidifies to form the desired shape. This technique is widely used for manufacturing optical components, electronic enclosures, and consumer products.
Extrusion molding, on the other hand, involves forcing molten PMMA through a die to create continuous profiles such as rods, tubes, and sheets. This technique is commonly employed in the production of architectural profiles, lighting diffusers, and signage.
Vacuum forming, a versatile technique suited for large, complex shapes, entails heating a PMMA sheet until it becomes pliable, then draping it over a mold and applying vacuum to draw the material into the desired shape. This process is widely used in automotive, aerospace, and medical industries for producing interior panels, enclosures, and housings.
Applications Across Industries
PMMA molding finds extensive applications across a diverse range of industries, ranging from automotive and aerospace to electronics and healthcare. In the automotive sector, PMMA is used for manufacturing headlights, taillights, and interior trim components, due to its optical clarity, impact resistance, and design flexibility.
Similarly, in the electronics industry, PMMA is employed for producing display screens, lenses, and covers for electronic devices, offering exceptional optical properties and durability. Moreover, in the healthcare sector, PMMA is utilized for manufacturing medical devices such as surgical instruments, diagnostic equipment, and prosthetic components, due to its biocompatibility and sterilizability.
Challenges and Future Directions
Despite its numerous advantages, PMMA molding faces challenges such as material brittleness, surface defects, and environmental sustainability. Addressing these challenges requires ongoing research and development efforts aimed at enhancing material properties, process optimization, and recycling technologies.
Looking ahead, the future of PMMA molding lies in innovation and collaboration across industries, leveraging emerging technologies such as additive manufacturing, digital design, and sustainable materials. By embracing these advancements, manufacturers can unlock new opportunities for product innovation, process efficiency, and environmental stewardship.
In Conclusion
PMMA molding stands as a testament to the versatility and adaptability of modern manufacturing, offering unparalleled capabilities and benefits across industries. With continuous innovation and collaboration, PMMA molding will continue to drive efficiency, sustainability, and innovation in the ever-evolving landscape of plastic manufacturing.
GETTING A QUOTE WITH LK-MOULD IS FREE AND SIMPLE.
FIND MORE OF OUR SERVICES:
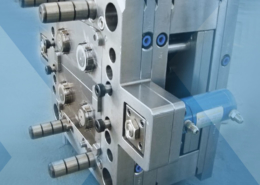
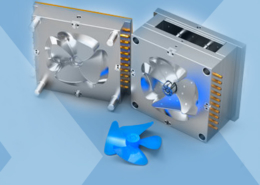
Plastic Molding

Rapid Prototyping
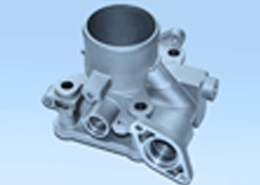
Pressure Die Casting
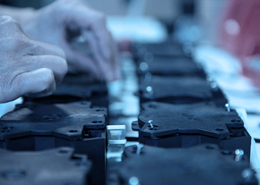
Parts Assembly
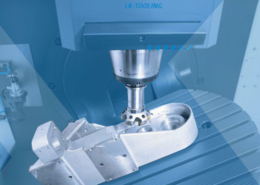