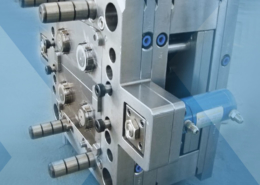
Exploring Polyethylene Injection Molding: Revolutionizing Plastic Manufacturing
Author:gly Date: 2024-06-08
Introduction
Polyethylene injection molding stands as a cornerstone of modern plastic manufacturing, offering unparalleled versatility, efficiency, and cost-effectiveness. This article delves into the intricacies of polyethylene injection molding, shedding light on its applications, advantages, and implications for the industry.
Polyethylene injection molding, a subset of plastic injection molding, involves the precise injection of molten polyethylene resin into molds to produce a wide range of plastic components and products. With its ability to create complex shapes and intricate designs, polyethylene injection molding has become indispensable across various industries, including automotive, packaging, and consumer goods.
Historical Background
The origins of polyethylene injection molding can be traced back to the mid-20th century, coinciding with the rise of synthetic polymers and the development of injection molding technology. Initially used for simple shapes and low-volume production, polyethylene injection molding has evolved significantly over the decades, driven by advancements in materials science, machinery, and manufacturing processes.
Operational Mechanism
Polyethylene injection molding operates on the principle of heating polyethylene resin to its melting point and injecting it into molds under high pressure. Once injected, the molten resin fills the cavity of the mold, solidifying upon cooling to form the desired shape. This process allows for the rapid and cost-effective production of plastic components with precise dimensions and consistent quality.
Materials Selection
Polyethylene injection molding encompasses a variety of polyethylene resins, each tailored to specific applications and performance requirements. Common types of polyethylene include low-density polyethylene (LDPE), high-density polyethylene (HDPE), and linear low-density polyethylene (LLDPE), each offering unique properties such as flexibility, strength, and chemical resistance.
Mold Design and Fabrication
The design and fabrication of molds play a crucial role in polyethylene injection molding, influencing the quality, efficiency, and cost-effectiveness of the manufacturing process. Advanced CAD/CAM software allows engineers to design intricate molds with precision, while CNC machining techniques ensure accuracy and repeatability in mold fabrication.
Process Optimization
Optimizing the injection molding process is essential to maximizing efficiency and minimizing production costs. Variables such as injection speed, pressure, temperature, and cooling time must be carefully controlled to achieve optimal results. Advanced process monitoring systems and automation technologies help manufacturers maintain consistency and quality throughout production runs.
Advantages of Polyethylene Injection Molding
Polyethylene injection molding offers several advantages over traditional manufacturing methods, making it the preferred choice for a wide range of applications.
Versatility
Polyethylene injection molding can accommodate a diverse range of shapes, sizes, and complexities, making it suitable for a wide range of products. From intricate components to large structural parts, polyethylene injection molding offers unparalleled versatility in design and production.
Cost-Effectiveness
Compared to other manufacturing processes, polyethylene injection molding offers significant cost savings in terms of material usage, labor, and time. The ability to produce large quantities of identical parts with minimal waste makes polyethylene injection molding a cost-effective solution for mass production.
Speed and Efficiency
Polyethylene injection molding enables rapid production cycles, with parts being manufactured in a matter of seconds or minutes. The high-speed, high-volume nature of the process ensures swift turnaround times and on-time delivery, meeting the demands of fast-paced industries and consumer markets.
Environmental Considerations
Despite its numerous advantages, polyethylene injection molding raises environmental concerns related to plastic waste and resource consumption.
Material Recycling
Efforts to mitigate the environmental impact of polyethylene injection molding include recycling initiatives aimed at reusing and repurposing plastic waste. Advances in recycling technologies and infrastructure are driving the transition towards a circular economy, where plastic materials are recycled and reused in closed-loop systems.
Biodegradable Alternatives
The development of biodegradable polyethylene resins offers a promising solution to the environmental challenges associated with traditional plastics. Biodegradable polymers break down naturally in the environment, reducing pollution and minimizing the reliance on finite resources.
Future Perspectives and Conclusion
In conclusion, polyethylene injection molding remains a vital process in the realm of plastic manufacturing, offering unparalleled versatility, efficiency, and cost-effectiveness. As technology continues to advance and environmental awareness grows, the future of polyethylene injection molding lies in sustainable practices, materials innovation, and process optimization.
By embracing these principles and leveraging emerging technologies, manufacturers can harness the full potential of polyethylene injection molding to drive innovation, meet evolving customer demands, and contribute to a more sustainable future for generations to come.
GETTING A QUOTE WITH LK-MOULD IS FREE AND SIMPLE.
FIND MORE OF OUR SERVICES:
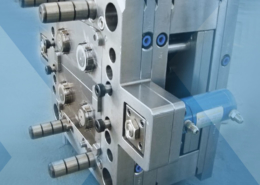
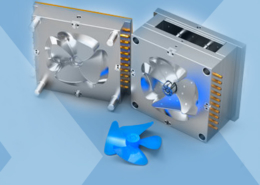
Plastic Molding

Rapid Prototyping
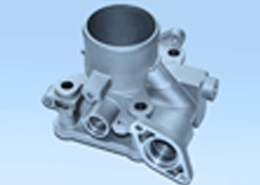
Pressure Die Casting
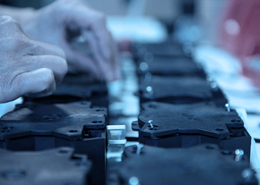
Parts Assembly
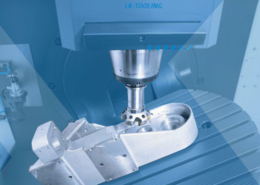