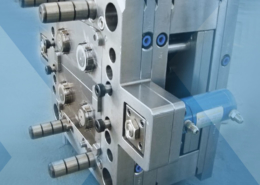
SyBridge acquires manufacturer of multicavity plastic injection moulding
Author:gly Date: 2024-09-30
“When a liner is used in our bottle, it is not adhered or glued to the fiber layer. Meaning, it is easily separated by almost any mechanical process. We are working with various waste management facilities in various markets around the world to understand what this looks like in practice – not just theory.”
And it’s not just cellulose that can be used – the team is also exploring how so-called non-tree-based fibers could work. “In addition to virgin fiber, we can incorporate recycled content and, in some cases, non-tree-based fibers for added properties,” he told us.
DMF packaging is already being produced at scale, including in the shape of bottles for dry goods, but a DMF container for storing liquids hadn’t been successfully developed before.
designboom has received this project from our ‘DIY submissions‘ feature, where we welcome our readers to submit their own work for publication. see more project submissions from our readers here.
precious plastic project based in netherlands really cares about plastic recycling. aiming to minimize the environmental damage, the team created a method to make a do-it-yourself iPhone case.
According to the product brief, the PA/PulPac Bottle Collective – as the prototype is called - can store water, dairy, non-carbonated soft drinks, adult beverages, and even hair- and skin-care products. The bottle can also be customized with bespoke shapes, sizes and decorations to reflect brand identity, with a growing number of businesses already taking an interest in the product, we were told.
So how does DMF compare to cardboard production on emissions, for example? “This solution is quite different to cardstock,” Perrotta said. “We can produce a myriad of sizes and shapes not possible in either cardstock or wet-molded processes today.
Copyright - Unless otherwise stated all contents of this web site are © 2024 - William Reed Ltd - All Rights Reserved - Full details for the use of materials on this site can be found in the Terms & Conditions
While PulPac and PA Consulting believe they have proof of concept, the challenge now lies in scaling this up to create a solution fit for the FMCG industry. The plan is to release the bottles at scale by 2025.
Packaging manufacturer PulPac and global consultancy PA Consulting claim they have come up with the technology that can finally make it possible for dry-molded fiber (DMF) to be made into beverage containers. The companies say that the bottles would be a sustainable alternative to wide-spread packaging solutions such as cardboard and single-use plastics.
“We have not finalized a set of markets to launch in but expect Europe to be very high on the list of priorities,” concluded Perrotta. The intention of our next phase of work is to demonstrate the scalability options to meet demand.”
“We expect our packaging to be a valid alternative for dairy beverages,” Perrotta told us. “We have not yet trialed shelf life for a full range of beverages yet; as we further engage specific brands and their unique needs, material transfer, color and taste profile and fragrance needs will all be addressed, too.
“We are designing for standard kerbside collection and expect the dustcart pressure to easily and quickly separate the liner from the outer layer," Perrotta continued. “In addition, since a liner is being employed, the pulp is of a higher grade than alternatives,” he claimed. “The liner houses the product and any chemistry of the product keeping the pulp high grade.”
Since it’s still early days for the Bottle Collective, Perrotta couldn’t share specifics around how the packaging affects shelf life, or taste and flavor properties of milk – although the companies claim the bottle can hold water for six months.
DMF is made when cellulose pulp is dry-molded into solid packaging. PulPac says the process brings significant environmental benefits since it requires less water and energy during production. Plus, DMF can take various shapes and forms that aren’t possible to achieve through so-called wet-molding. The process can also utilize recycled, residue as well as virgin cellulose, making use of readily available, renewable and affordable material.
PulPac and PA Consulting say they will announce some of their first branded partners in the project ‘shortly’, but the team is yet to decide on the markets to launch the bottles in come 2025.
“Emissions work is currently being evaluated but since our process is a dry-molded process, there is a significant reduction in water use and energy compared to alternative forming methods.”
a diverse digital database that acts as a valuable guide in gaining insight and information about a product directly from the manufacturer, and serves as a rich reference point in developing a project or scheme.
“Creating a DMF bottle already represents an enormous challenge,” opened Tony Perrotta, PulPac partnership lead at PA Consulting. “Creating a scalable and commercially viable process to replicate this has been even more so. Our aim is to provide a scalable process that meets existing need for cost, scale, speed, sustainability profile, and brand needs. It’s a tall order indeed but we have already demonstrated the foundational aspects of this work.”
having a 3D model of it done, the team ordered their CNC (computer numerical control) machined mold for the case through 3D hubs, the network of manufacturing services. after they received the mold, they brought it to perfection by hand and attached to their homemade injection molder. with one big push of the handle, the plastic pellets are pushed through the nozzle at the base forming into the shape of anything your mold is cut to, for instance an iPhone case.
Asked how a DMF milk bottle could look like - including what type of lining would be used and how easy that would be to recycle - Perrotta explained: “Our approach allows for the use of multiple types of liners, hence we could replicate existing use or find another alternative.
founded by dave hakkens, precious plastic is specialized in encouraging people to create their own plastic recycling center, wherever they are based. sharing their knowledge, techniques, and tools with people all over the world, they established a community comprising hundreds of locations taking old plastic and turning it into new innovative products for the environmentally conscious consumer.
GETTING A QUOTE WITH LK-MOULD IS FREE AND SIMPLE.
FIND MORE OF OUR SERVICES:
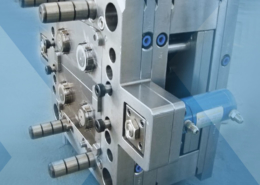
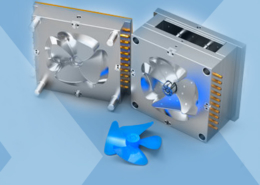
Plastic Molding

Rapid Prototyping
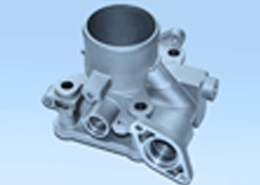
Pressure Die Casting
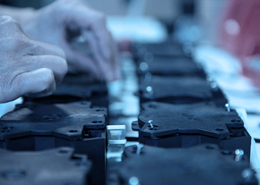
Parts Assembly
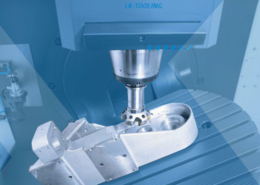