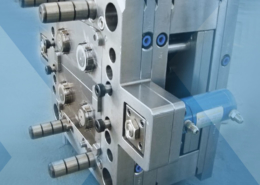
SyBridge acquires manufacturer of multicavity plastic injection moulding
Author:gly Date: 2024-09-30
No matter the material — the printed mold, core, or tooling must withstand higher heat than the injected, dipped, poured, sprayed, or hand-layed material. If the print will be exposed to high temperatures, one recommendation is PPSF/PPSU. If the print needs to be certified for flame, smoke, and toxicity, then Ultem would be the material of choice. If the process will apply pressure on the print, polycarbonate acrylonitrile-butadiene-styrene (PC-ABS) can be used because it has the highest impact resistance. And, ABS-M30i or PC-ISO is suitable for processes that need to use material that is ISO-10993 certified. All of these materials work with fused-deposition-modeling (FDM) printing machines.
Life Cycle Assessment, or LCA, is an emerging science, still in its infancy. Currently, several prominent LCA methodologies compete for legitimacy and recognition. This is reflected in SolidWorks Sustainability FAQ, which states, “The values in SolidWorks Sustainability are useful to within +/- 20% and should be used as an estimate. The more accurate way of using the product is to track the relative changes from one version of a design to the next.”
Kenneth Wong is Digital Engineering’s resident blogger and senior editor. Email him at [email protected] or share your thoughts on this article at digitaleng.news/facebook.
After converting the model into an STL file, upload the file to the software that works with the printer. Choose the resolution, material, and machine that will print the mold. Different systems allow more or fewer adjustments to the build specifications, but the program does most of the work at that point. Set the printer up with the material and (in some machines) the tip to be used. Check for any calibration and cleaning needed, and then start printing. Remove the mold and clean off support material — polish the mold as needed. Plastic molds fit the same as machined molds, so they can be directly inserted into most process machines. But depending on the tool and part, you might need to create a metal box around the plastic to hold it together.fri
“There’s no doubt — printing individual and identical prototypes and end-use parts isn’t the right choice for large-quantity jobs and jobs that needed to be done yesterday,” says Gannon.
The advantage of the full version is the ability to visualize how each individual part contributes to the entire assembly’s environmental impact. The color-coded visualization makes it easy to identify parts that cause the greatest harm, prompting you to switch material, production method, or something else to bring down the carbon count, energy use, and pollution levels. Furthermore, the ability to perform stress analysis and environmental assessment in the same window goes along way to ensure that you don’t inadvertently compromise your design’s structural integrity while you’re exploring ways reduce its carbon footprint.
Machined tooling contributes to the majority of production costs for many small-run jobs. 3D printing can reduce the cost of plastic cores, molds, and tooling, but there are several considerations to examine before choosing this route. Patrick Gannon, engineering manager at Rapid Prototype + Manufacturing LLC, Avon Lake, Ohio, offers a few tips on how and when to 3D print plastic molds and tooling.
Most 3D printers use a soluble structural material. This material can be removed with a solvent or chipped away. Cores printed from soluble material can be used in lost-wax casting applications. Soluble material can also be used as the master for open-molding processes such as spray or hand lay-up. For open-molding processes, print a soluble master slightly smaller than the desired part and layer the master with materials like fiberglass and resins. After the materials are cured, the soluble material can be removed.
Cores used to make molds can also be printed. For instance, a printed part can act as the core to make silicone molds. Cores are traditionally machined from plastic, wood, or metal depending on the tolerance needed and the surrounding temperature. Even though printed cores may require sanding to get a smooth finish, costs are lower than a core requiring several machining processes.
Printed molds, tooling, and cores may require different materials. And, material choice will continue to vary by the process and application. For instance, an injection mold will need high-heat and chemical-resistant material. Ultem of polyphenolsulfone (PPSF/PPSU) satisfies those specifications.
Printed plastic molds can be used in injection, extrusion, and blow-molding processes. Printed tooling can be used in vacuum-forming, thermoforming, and drape-forming processes. In thermoforming applications, for example, printed tooling can make blister packaging for consumer products. Tooling for packaging development may require multiple cavities and, with each cavity, there might be thousands of vent holes. Printing cuts the time and cost spent to drill or CNC those holes.
Tolerance must be taken into account when designing a mold. This means opening up gaps and realizing that you will never get extremely tight tolerances. If extreme tolerances are needed, a printed mold will not be acceptable right off the printer — even after postmachining.
To date, SolidWorks remains one of the few CAD companies offering a sustainable design development tool, built right into the modeling environment. If you’re on the latest release of SolidWorks (2010), you can use Sustainability Xpress, the app under the Evaluation tab, to calculate your design’s environmental impact. But the free Xpress version works only on parts. To work on assemblies, you need SolidWorks Sustainability, the full license that costs roughly $3,000.
“What we do know is that 3D printing plastic molds adds value because most machining operations can be eliminated. It’s not uncommon for a machined tool to cost $45,000 and take six to eight weeks to complete. The same mold, 3D printed, will cost about $2,000 and is made in a matter of hours to one week. Printed plastic molds are great for jobs producing 500 parts or less, and for jobs that use complex tooling. But remember, as with any 3D printing project, the best approach is to expect less-than-perfect results. And, if you have to make multiple versions of the tool, you begin to lose the benefits.”
Both Sustainability and Sustainability Xpress are designed as a comparison tool—that is, to set up one scenario as your baseline, then compare it against other iterations. This method lets you pick the best materials, production methods, and acquisition regions to make your product greener.
3D printed mold design is similar to metal molds. Mounting holes can be modeled in the same pattern as a metal mold. And, if overmolding or dual material injecting is desired, the design mimics metal molds. However, printed design changes when heat transfer is an issue. Plastic molds transfer heat poorly so to help move heat, add several holes to the mold to help cool injected parts quicker. Another method is to insert copper or other heat-transfer materials into the holes.
With Sustainability Xpress, you can use your material specifications, manufacturing methods (injection molding, machining, etc.), raw material locations, and deployment destinations (where the end products will be used) to tally up your parts’ environmental impact in four areas: carbon emission, energy use, air pollution, and water pollution. In the full version, in addition to the parameters listed above, you can also specify transportation mode (air, train, truck, and so on) and lifetime energy use (say, the anticipated energy used by a washing machine’s average lifespan).
Lindsey has been an Associate Editor for Machine Design since 2012. She holds a Bachelor of Science in mechanical engineering from Cleveland State University. Prior to joining Penton, she worked in product design, packaging, development and strategy, and manufacturing. She covers the materials market and other areas of interest for design engineers such as 3D printing and methods to operate efficiently.
The two quickest ways to reduce your design’s impact are (1) reducing your design’s overall mass and (2) switching to less harmful materials. For the latter, you can use SolidWorks Sustainability’s Find Similar tool to single out alternative materials with comparable tensile strength, yield strength, and heat conductivity.
For more on SolidWorks Sustainability Xpress, read the previous blog post “A Look at SolidWorks Sustainability Xpress (Or How Green is Homer Simpson’s Beer Can?).”
The results can be exported as a PDF report, a good way to present your findings or justify your engineering change orders to those who might not have SolidWorks. If you’d like to learn more about the results, you may visit SolidWorks’ Sustainability portal, which has a free carbon footprint calculator. The browser-based app lets you compare your design’s impact (measured in kg of CO2) to the effects of driving an average U.S., European, or hybrid car for a number of miles, adding more weight to your understanding of the assessment.
GETTING A QUOTE WITH LK-MOULD IS FREE AND SIMPLE.
FIND MORE OF OUR SERVICES:
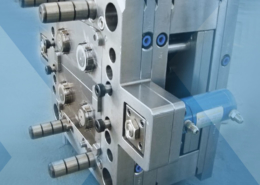
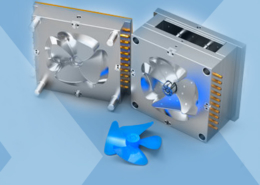
Plastic Molding

Rapid Prototyping
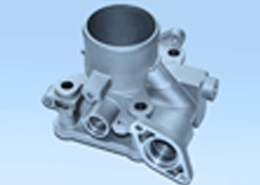
Pressure Die Casting
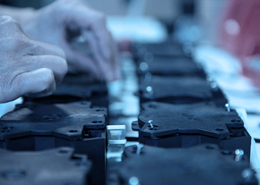
Parts Assembly
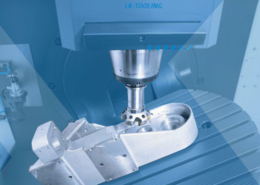