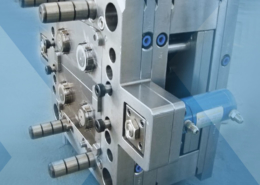
SyBridge acquires manufacturer of multicavity plastic injection moulding
Author:gly Date: 2024-09-30
Across the show, sustainability ruled in new materials technology, from polyolefins and engineering resins to biobased materials.
Faes is starting to build a database of the relationship of strength to stretch ratio in ISBM PET—an area where studies are lacking in the industry, he says. He’s also very interested in work on simulating the ISBM process conducted at Queen’s University in Belfast, Northern Ireland.
Despite price increase nominations going into second quarter, it appeared there was potential for generally flat pricing with the exception of a major downward correction for PP.
FROM ONE PROCESS TO THREE Currier Plastics is a privately owned firm that began as a custom injection molder in 1982. In 1996, it expanded into extrusion blow molding (EBM). In 2010, Currier added another process, injection stretch-blow molding (ISBM) of PET.
Multiple speakers at Molding 2023 will address the ways simulation can impact material substitution decisions, process profitability and simplification of mold design.
Once the agreed contractual term comes to an end, customers have the option of buying the machine. If they choose to return it, the machine can be sent back to the pre-owned machine company ENGEL Used Machinery in a bid to make use of its full service life and facilitate a more sustainable purchase process.
The aim of this presentation is to guide you through the factors and the numbers that will help you determine if a robot is a smart investment for your application. Agenda: Why are you considering automation? What problems are you trying to solve? How and why automation can help Crunch the numbers and determine the ROI
This Knowledge Center provides an overview of the considerations needed to understand the purchase, operation, and maintenance of a process cooling system.
Since moving into the new building, the blow molding department has been reorganized into four cells—one for ISBM, one for large EBM presses, and two for smaller EBM units (separated by manufacturer—Heins or Automa.) “The goal is improved efficiency,” explains Valentino. “Cells bring more focused attention to a limited number of machines with common characteristics.” The injection molding department followed suit with a reorganization into three cells by machine size and product range.
technotrans says climate protection, energy efficiency and customization will be key discussion topics at PTXPO as it displays its protemp flow 6 ultrasonic eco and the teco cs 90t 9.1 TCUs.
Join KraussMaffei for an insightful webinar designed for industry professionals, engineers and anyone interested in the manufacturing processes of PVC pipes. This session will provide a comprehensive understanding of the technology behind the production of high-quality PVC pipes: from raw material preparation to final product testing. Agenda: Introduction to PVC extrusion: overview of the basic principles of PVC pipe extrusion — including the process of melting and shaping PVC resin into pipe forms Equipment and machinery: detailed explanation of the key equipment involved — such as extruders, dies and cooling systems — and their roles in the extrusion process Process parameters: insight into the critical process parameters like temperature, pressure and cooling rates that influence the quality and consistency of the final PVC pipes Energy efficiency: examination of ways to save material and energy use when extruding PVC pipe products
Currier even molds some custom caps without the containers. “The big cap guys typically don’t do custom, and if they do, their response time is more than twice as long as ours,” says Sriraj Patel, injection molding product engineering manager and toolroom manager. “For a 72-cavity cap job, we can go from concept to production—including post-mold automation—in just 15 to 16 weeks.”
Mold maintenance is critical, and with this collection of content we’ve bundled some of the very best advice we’ve published on repairing, maintaining, evaluating and even hanging molds on injection molding machines.
Take a deep dive into all of the various aspects of part quoting to ensure you’ve got all the bases—as in costs—covered before preparing your customer’s quote for services.
While prices moved up for three of the five commodity resins, there was potential for a flat trajectory for the rest of the third quarter.
Thought to avoid the risk of binding capital and freeing customers from the need to seek investment approval, the new model is said to speed up the procurement process. The payment is made once a unit price has been agreed, either per unit produced or unit of machine operating time.
Currier now operates 28 injection machines—up from 23 a year ago—in a range of 24 to 500 tons. It has 14 EBM machines, two of them added in the past year, with another on order. Its ISBM capacity has risen from five to eight machines since 2012. To accommodate this growth, Currier built a 40,000-ft2 addition last year dedicated just to blow molding, turning over all the original 65,000-ft2 space to injection molding.
Introduced by Zeiger and Spark Industries at the PTXPO, the nozzle is designed for maximum heat transfer and uniformity with a continuous taper for self cleaning.
Add to these capabilities a tight focus on “lean” manufacturing efficiency and you get a pretty good picture of how Currier competes with the big boys at home and low-cost molders abroad. Clearly, the formula has worked: Its business has expanded 60% since the end of the last recession and an expected 26% this year alone. Employment has grown 18% in the last two years to 130 people today.
The three key ingredients are responsiveness, full-service product development, and control over both the bottle and the cap.
CAD engineer Steve Faes shows off the result of laser scanning of an HDPE detergent jug. Gray shows the original CAD dimensions, yellow shows any deviations in the blown container, and magenta shows deviations in a container filled with water. Laser-scan resolution is less than 1 mil.
Uniloy is revising its machinery lines across the board and strengthening after-sales services in tooling maintenance, spare parts and tech service.
Formnext Chicago is an industrial additive manufacturing expo taking place April 8-10, 2025 at McCormick Place in Chicago, Illinois. Formnext Chicago is the second in a series of Formnext events in the U.S. being produced by Mesago Messe Frankfurt, AMT – The Association For Manufacturing Technology, and Gardner Business Media (our publisher).
“We love to tell our story.” That’s one way Mike Cartner, CFO of Currier Plastics, defines what separates this family-owned custom processor from its competitors.
While the melting process does not provide perfect mixing, this study shows that mixing is indeed initiated during melting.
Maker of one-stage ISBM machines will show off new sizes and styles of handled and stackable PET containers, including novel interlocking products.
Currier’s goal is “the whole package”—molding both the bottle and cap, which avoids “finger-pointing” and delays if the two parts are not perfectly compatible. Additional lightweighting also is possible when Currier helps design both parts.
All Currier’s recent purchases of injection and blow molding machines have been all-electric presses, and that will be the trend in the future. On order is one of the latest all-electric EBM units from Kautex Machines, Inc., North Branch, N.J. It’s a KBB60 double-sided press with 12 heads, one of a new series introduced at the K2013 show in Dusseldorf . It will be running in Kautex’s booth at NPE 2014 in Orlando, Fla., before moving to Currier’s plant.
“Making both bottle and cap puts a stop to the finger-pointing when something goes wrong.” He adds that some packages require the cap to be oriented relative to the bottle. “So thread timing is key, and that’s difficult to achieve if you don’t control both elements.” In cases where Currier doesn’t get that control, it performs its own SQC analysis of a sample of caps and then adjusts the bottle neck design for the expected variability in cap threads and in how tight the customer might torque the cap onto the bottle.
In this collection, which is part one of a series representing some of John’s finest work, we present you with five articles that we think you will refer to time and again as you look to solve problems, cut cycle times and improve the quality of the parts you mold.
Additive technology creates air pockets in film during orientation, cutting down on the amount of resin needed while boosting opacity, mechanical properties and recyclability.
While prices moved up for three of the five commodity resins, there was potential for a flat trajectory for the rest of the third quarter.
Join Wittmann for an engaging webinar on the transformative impact of manufacturing execution systems (MES) in the plastic injection molding industry. Discover how MES enhances production efficiency, quality control and real-time monitoring while also reducing downtime. It will explore the integration of MES with existing systems, emphasizing compliance and traceability for automotive and medical sectors. Learn about the latest advancements in IoT and AI technologies and how they drive innovation and continuous improvement in MES. Agenda: Overview of MES benefits What is MES? Definition, role and brief history Historical perspective and evolution Longevity and analytics Connectivity: importance, standards and integration Advantages of MES: efficiency, real-time data, traceability and cost savings Emerging technologies: IoT and AI in MES
Faes made imaginative use of his computer tools on a project to optimize an HDPE detergent jug. Since this is a commodity product, Currier wanted to minimize wall thickness without compromising necessary strength and stiffness. Faes used a laser scanner to measure the dimensions of a molded jug when empty and when filled with water. Feeding this data into the SolidWorks system produced a tri-color map of the product, where gray represents the “perfect” CAD geometry, yellow shows any deviations in the empty blown bottle, and magenta shows further deviations in the filled container .
Second quarter started with price hikes in PE and the four volume engineering resins, but relatively stable pricing was largely expected by the quarter’s end.
ORGANIZED FOR EFFICIENCY Lean manufacturing is an expression one hears mentioned repeatedly at Currier. It influenced the company’s choice of molding machines. For example, all of its ISBM units are integrated one-stage injection and stretch-blowing systems from Aoki Laboratory America, Elk Grove Village, Ill. Control over the entire process in one machine was a key consideration, according to Leone. Adds Valentino, another reason is that “the product engineering is really in the preform, and Aoki has extensive experience in that area and provides a lot of help. Our entire team has visited them in Japan more than once.”
One project under way is to get customer qualification to use liquid colors for molded containers and lids. Valentino cites three advantages: Liquid colors give more homogeneous dispersion at low pigment levels for translucent products. PET pellet masterbatches require predrying. And pellet concentrates “leave color residue all through the handling system.”
Currier’s largest blow molded product used to be EBM HDPE dispensing canisters for wet wipes, which ran 20-30 million units annually. But Currier is currently expanding its market thrust into mini bottles (1.5 to 3 oz) beyond hotel amenities into travel-size containers and restaurant portions, which can run to 100-125 million a year for a single job. For example, there’s a 1.5-oz PET squeeze bottle for a restaurant portion of maple syrup that is being converted from glass. Currier molded hundreds of millions of mini bottles last year, both ISBM PET and EBM HDPE. “It’s an area of growth for us,” says Leone. “There are huge volumes, but it’s incredibly competitive. Hotel amenities are ‘free’ give-aways, so they have to be cost-effective. It requires very tight process control and product uniformity.” One unique version Currier produces is amenity bottles with Braille lettering on the side.
One highly engineered specialty is an ISBM pressure vessel molded of Eastman Chemical's Tritan. It’s all curves with no straight walls. Another special bottle is a 4.75-oz ISBM PET bottle for a new extended-release carbohydrate supplement drink. Its unusually complex shape is somewhat flattened, with rounded ends and large panels that are not actually flat but lightly “dished” or concave. It also has three highly elevated ribs on both narrow ends. Molding must be very precise, because the customer will apply a shrink label that conforms tightly to the bottle’s curves and ribs.
IN-HOUSE ENGINEERING Currier has ample experience in helping customers develop products from even the vaguest of concepts. “When we started work on the wet-wipes dispenser, the customer had no specific design in mind,” recalls Kieffer. “The idea was something for the kitchen environment that would give an impression of high quality—that’s all. We drew up 18 different concepts, then winnowed down the list on the basis of manufacturability. We used computer graphics to simulate different product textures, colors, and lighting conditions in a home kitchen. We even asked the women in our company what they thought of the ideas.”
Sidel introduces Qual-IS comprehensive quality system to merge all QC activities in PET aseptic beverage bottling, from the preform blowing to laboratory management.
Processors with sustainability goals or mandates have a number of ways to reach their goals. Biopolymers are among them.
Core Technology Molding turned to Mold-Masters E-Multi auxiliary injection unit to help it win a job and dramatically change its process.
A bulletin board on the molding floor graphs the performance of all the cells—distinguished by different colored trend lines—according to four critical factors: efficiency, floor scrap, production value relative to the schedule, and utilization relative to schedule. The data are published daily and graphed monthly. “It breeds healthy competition,” says Patel.
Mike Sepe has authored more than 25 ANTEC papers and more than 250 articles illustrating the importance of this interdisciplanary approach. In this collection, we present some of his best work during the years he has been contributing for Plastics Technology Magazine.
Resin drying is a crucial, but often-misunderstood area. This collection includes details on why and what you need to dry, how to specify a dryer, and best practices.
Across all process types, sustainability was a big theme at NPE2024. But there was plenty to see in automation and artificial intelligence as well.
According to Valentino, the company’s goal is to achieve better efficiency through innovation. “We want technology to be the driver,” he says. On the blow molding side, Currier is evaluating multi-parting-line (MPL) technology patented last year by Fidelity Tool & Mold Ltd., Batavia, Ill. Similar to stack molds for injection molding, the tool has two independent parting lines, though the centerlines remain stationary. Special twin-row heads are offered for this process by W. Muller GmbH (U.S. office in Agawam, Mass.). Like stack molds, this approach can double machine capacity if the extruder is up to it.
New World Consumer Products, TricorBraun, and Currier partnered in development of this highly complex ISBM PET bottle for a new “performance supplement.” It requires precise molding to accept a full-body shrink label.
Another new feature of Currier’s reorganized plant layout is the location of multiple QA stations on the plant floor—one for each injection molding cell and three for the blow molding department. These stations cost $25,000 each to outfit with equipment for measuring—in one blow molding example—topload strength, bottle height and weight, min/max wall thickness and wall variation. One station also has a vacuum chamber. All measurement data goes automatically into the company’s central SPC database.
After successfully introducing a combined conference for moldmakers and injection molders in 2022, Plastics Technology and MoldMaking Technology are once again joining forces for a tooling/molding two-for-one.
Company president John Currier (son of the founder) adds another consideration: “When you control both the bottle and cap, you can often lightweight more than you could if they were produced separately. The reason is that it’s awfully difficult to ask the other guy to change his mold to help you save some material.”
Currier has also launched in-house initiatives to boost productivity. “On some machines, our engineers can squeeze 75% to 100% more cavities into an EBM mold,” boasts Valentino. “They can take a 6-up, double-sided machine and remodel it to run as many as 20 cavities. The machine builder didn’t believe we could do it.” The reason why is obvious: On a double-sided press, the extra cavities required enlarging the molds until they just barely miss touching each other when the two shuttles come together.
“Automotive and medical manufacturing uses this approach, but not many custom molders,” says Steve Feaster, injection molding plant manager. Each cell is headed by a cell engineer, who is responsible for the machines, processes, automation, and efficiency. “It took us a while to define the role of the cell engineer,” recalls Feaster. “We decided that the cell engineers would have no direct reports, freeing them from that management burden. For plant managers and plant engineers, our job is to support the cell engineers. We’re measuring their performance every day, and we have a roundtable meeting once a week at lunch to talk over how things are going.”
Learn about sustainable scrap reprocessing—this resource offers a deep dive into everything from granulator types and options, to service tips, videos and technical articles.
All production cells delivered as part of the pay-per-use model are said to be regularly maintained by ENGEL service technicians and feature e-connect.24, an online support and remote maintenance tool. While the in-person support is expected to facilitate early planning for maintenance work and minimise machine downtime, e-connect.24’s machine utilisation serves as the basis for billing.
In this collection of content, we provide expert advice on welding from some of the leading authorities in the field, with tips on such matters as controls, as well as insights on how to solve common problems in welding.
• Third, Currier gains substantial advantage by molding both the container and the closure for about 70% of its customers. “Our corporate mission is the whole package, meaning the bottle and the cap,” says Gary Kieffer, v.p. of new product development.
When, how, what and why to automate — leading robotics suppliers and forward-thinking moldmakers will share their insights on automating manufacturing at collocated event.
From a business that was once 100% injection molding, Currier now derives 60% of its revenues from blow molding, divided 75/25 between EBM and ISBM. Most of Currier’s injection molding is now of closures for bottles and jars, as well as some electrical and healthcare parts (see blog). Although most bottle caps are PP, Currier created an HDPE cap for one HDPE bottle to meet the customer’s desire for enhanced recyclability.
ENGEL has expanded its injection moulding machinery range with a pay-per-use model in the hopes of reducing investment risk while boosting flexibility in production.
For the Tritan pressure vessel, Currier used the 3D printer to produce parts of a prototype fixture to trim off one end of the part to expose a second set of threads. Perhaps the most unusual aspect of that development process was an animated motion study to simulate the automated process for trimming the part in the fixture. “We had to make sure the trim process was reliably consistent and operator-safe,” says Steve Faes, CAD designer.
Blow molding plant manager Steve Valentino at one of six QA stations located at injection and blow molding cells on the plant floor.
Plastics Technology’s Tech Days is back! Every Tuesday in October, a series of five online presentations will be given by industry supplier around the following topics: Injection Molding — New Technologies, Efficiencies Film Extrusion — New Technologies, Efficiencies Upstream/Downstream Operations Injection Molding — Sustainability Extrusion — Compounding Coming out of NPE2024, PT identified a variety of topics, technologies and trends that are driving and shaping the evolution of plastic products manufacturing — from recycling/recyclability and energy optimization to AI-based process control and automation implementation. PT Tech Days is designed to provide a robust, curated, accessible platform through which plastics professionals can explore these trends, have direct access to subject-matter experts and develop strategies for applying solutions in their operations.
In a time where sustainability is no longer just a buzzword, the food and beverage packaging industry is required to be at the forefront of this innovation. By adopting circular packaging processes and solutions, producers can meet regulatory requirements while also satisfying consumer demand and enhancing brand reputation. Join Husky to learn more about the broader implications of the circular economy — as well as how leading brands are leveraging this opportunity to reduce costs, increase design flexibility and boost product differentiation. Agenda: The cost and operational benefits of embracing circularity Key materials in circular packaging — including rPET and emerging bioplastics How to design a circular food and beverage package Strategies for selecting sustainable closures to future-proof packaging solutions Optimization and streamlining of production processes for enhanced efficiency How Husky Technologies can enable your sustainable success
This month’s resin pricing report includes PT’s quarterly check-in on select engineering resins, including nylon 6 and 66.
Gifted with extraordinary technical know how and an authoritative yet plain English writing style, in this collection of articles Fattori offers his insights on a variety of molding-related topics that are bound to make your days on the production floor go a little bit better.
The Plastics Industry Association (PLASTICS) has released final figures for NPE2024: The Plastics Show (May 6-10; Orlando) that officially make it the largest ever NPE in several key metrics.
Currier streamlined its ISBM installations by moving the dryers off the floor onto the machine hoppers and designing the water manifolds so staff can quickly blow out the molds during changeovers. For the new building, an overhead crane was added so that one person can perform a mold change instead of two. (Overhead cranes were also added to the injection molding department.)
• Currier also offers customers full-service product-development and engineering services. It uses laser scanning, finite-element analysis, 3D printing, computer simulation, and even motion analysis to advise customers on material selection and product design. Product development manager Joel Sieber calls this method “predictive design in a virtual environment.”
August 29-30 in Minneapolis all things injection molding and moldmaking will be happening at the Hyatt Regency — check out who’s speaking on what topics today.
While the major correction in PP prices was finally underway, generally stable pricing was anticipated for the other four commodity resins.
Discover how artifical intelligence is revolutionizing plastics processing. Hear from industry experts on the future impact of AI on your operations and envision a fully interconnected plant.
Mini bottles for hotel amenities or travel sizes are a major market thrust for Currier. It molds these by the hundreds of millions, vs. tens of millions for its largest jobs in the past.
Thousands of people visit our Supplier Guide every day to source equipment and materials. Get in front of them with a free company profile.
Currier’s injection and blow molding equipment has been newly reorganized into cells (like this EBM cell) according to equipment type and size. Each cell is run by a cell engineer. The goal is greater efficiency through narrow focus on a smaller group of machines that share some commonality.
Currier’s ISBM products range from ultra-thin spherical and flat PET bottles with a 0.010-in. wall to ultra-thick perfume and cosmetic bottles in Eastman’s Tritan copolyester with walls of up to 0.250 in. to give the heavy feel of glass. There’s even an ISBM amenity bottle molded of 100% post-consumer recycled PET—fairly uncommon, says Steve Valentino, blow molding plant manager.
Currier Plastics in upstate Auburn, N.Y., is a relatively small custom molder, but it competes in consumer and healthcare packaging markets served by firms many times its size. Blowing bottles for personal care, beauty and cosmetics, household chemicals, and healthcare is not for the faint of heart. And one of Currier’s major market thrusts is into mini bottles for hotel amenities, travel sizes, and the like, where industry volumes are in the billions of bottles per year and pricing is rock-bottom. So how does a $30-million business thrive in such a competitive field?
Next, Currier recommended a different material—Tritan copolyester—to ensure the product could withstand repeated dishwasher cycles (a particular strong point for this unique resin), and performed further FEA work to determine the minimum wall thickness allowable. “Doing in-house FEA is unusual for a company our size, which would typically farm it out,” observes Leone.
Previously, Coca-Cola Europacific Partners and Innovative Tap Solutions worked together to develop a pay-per-use beverage dispensing solution for consumers.
Say “manufacturing automation” and thoughts immediately go to the shop floor and specialized production equipment, robotics and material handling systems. But there is another realm of possible automation — the front office.
The home carbonation pressure vessel illustrates the kinds of technologies Currier can bring to bear on product engineering. The product was originally made of PETG and was suffering failures in the field. Currier used SolidWorks Premium Simulation to perform finite-element analysis (FEA) of structural properties, which indicated that the molded lettering on the sides of the vessel was a point of weakness that had to be eliminated.
Ultradent's entry of its Umbrella cheek retractor took home the awards for Technical Sophistication and Achievement in Economics and Efficiency at PTXPO.
“Every custom molder thinks he needs a proprietary product,” says John Currier, president and co-owner of the injection molding firm his father founded, Currier Plastics in upstate Auburn, N.Y.
Sustainability continues to dominate new additives technology, but upping performance is also evident. Most of the new additives have been targeted to commodity resins and particularly polyolefins.
Join Engel in exploring the future of battery molding technology. Discover advancements in thermoplastic composites for battery housings, innovative automation solutions and the latest in large-tonnage equipment designed for e-mobility — all with a focus on cost-efficient solutions. Agenda: Learn about cutting-edge thermoplastic composites for durable, sustainable and cost-efficient battery housings Explore advanced automation concepts for efficient and scalable production See the latest large-tonnage equipment and technology innovations for e-mobility solutions
Mixed in among thought leaders from leading suppliers to injection molders and mold makers at the 2023 Molding and MoldMaking conferences will be molders and toolmakers themselves.
Plastics Technology covers technical and business Information for Plastics Processors in Injection Molding, Extrusion, Blow Molding, Plastic Additives, Compounding, Plastic Materials, and Resin Pricing. About Us
Join this webinar to explore the transformative benefits of retrofitting your existing injection molding machines (IMMs). Engel will guide you through upgrading your equipment to enhance monitoring, control and adaptability — all while integrating digital technologies. You'll learn about the latest trends in IMM retrofitting (including Euromap interfaces and plasticizing retrofits) and discover how to future-proof your machines for a competitive edge. With insights from industry experts, it'll walk you through the decision-making process, ensuring you make informed choices that drive your business forward. Agenda: Maximize the value of your current IMMs through strategic retrofitting Learn how to integrate digital technologies to enhance monitoring and control Explore the benefits of Euromap interfaces and plasticizing retrofits Understand how retrofitting can help meet new product demands and improve adaptability Discover how Engel can support your retrofitting needs, from free consultations to execution
• Currier is all too happy to provide individualized solutions for customers, even to the extent of exploring brand-new technologies to solve unique problems.
All Currier’s EBM machines have automated trimming. “We sold off our last mold-and-drop press. We’re big fans of in-machine trimming and prefer it to add-on automation if we can avoid it,” says Valentino. “With separate manual trim, one operator can handle four cavities in 16 sec. With in-machine trim, the same operator can run eight cavities in 15 sec.” In addition, every standup bottle is 100% leak tested on the exit conveyor at the machine. We’ve had zero leaks at production rates of 70-80 million bottles a year,” Valentino notes.
Another recent project saw ENGEL collaborate with ALPLA Group, Brink, and IPB Printing to produce thin-walled containers made of PET and rPET in a single injection moulding process step using ENGEL’s e-speed machine with a newly-developed injection unit.
This was followed by rapid prototyping on an Objet 30 inkjet-style 3D printer, which Currier purchased in 2012. “We use the 3D printer on most jobs today, especially for simulating the cap/bottle interface,” says Sieber. “We have simulated multiple thread-start positions to ensure correct orientation.”
Successfully starting or restarting an injection molding machine is less about ticking boxes on a rote checklist and more about individually assessing each processing scenario and its unique variables.
3D printed prototypes of this ISBM PET hotel amenity bottle and cap were made to test the snap-fit closure, which is more cost-effective than a threaded cap. To withstand the closing force, this tiny bottle required engineering for extra topload strength without sacrificing squeezability
Its blow molding business is quite varied. On the EBM side, it ranges from commodities like HDPE detergent jugs to more specialized products like coextruded bottles for a body lotion that have HDPE on the inside and soft-touch TPE on the outside. “We’re also one of the few custom blow molders that still runs PVC,” notes Max Leone, v.p. of business development. The main vinyl job in the plant currently is a bottle for a hair-coloring formula that is an oxygen scavenger, which tends to pull in the bottle sidewalls. Rigid PVC provides the needed combination of rigidity, squeezability, and chemical resistance.
In this three-part collection, veteran molder and moldmaker Jim Fattori brings to bear his 40+ years of on-the-job experience and provides molders his “from the trenches” perspective on on the why, where and how of venting injection molds. Take the trial-and-error out of the molding venting process.
Exhibitors and presenters at the plastics show emphasized 3D printing as a complement and aid to more traditional production processes.
In this collection of articles, two of the industry’s foremost authorities on screw design — Jim Frankand and Mark Spalding — offer their sage advice on screw design...what works, what doesn’t, and what to look for when things start going wrong.
GETTING A QUOTE WITH LK-MOULD IS FREE AND SIMPLE.
FIND MORE OF OUR SERVICES:
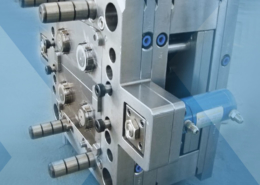
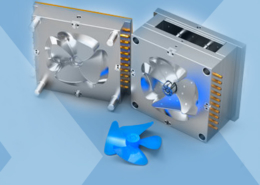
Plastic Molding

Rapid Prototyping
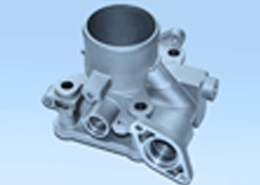
Pressure Die Casting
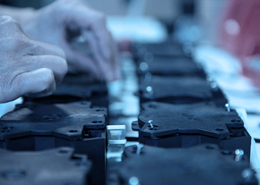
Parts Assembly
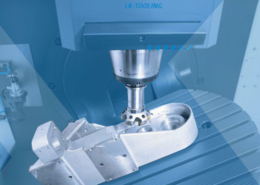