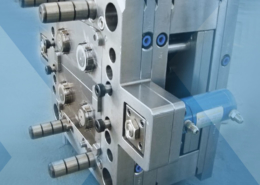
Exploring the World of Plastic Mold Tooling
Author:gly Date: 2024-06-08
Plastic mold tooling is a fascinating field that sits at the heart of modern manufacturing processes. With its intricate techniques and precise methodologies, it plays a crucial role in shaping various industries, from automotive to consumer electronics. In this article, we delve into the depths of plastic mold tooling, exploring its significance, techniques, innovations, challenges, and future prospects.
The Significance of Plastic Mold Tooling
Plastic mold tooling serves as the backbone of mass production in numerous industries. Its significance lies in its ability to create complex shapes and structures with high precision and repeatability. By enabling the efficient production of plastic components, it facilitates cost-effective manufacturing processes and fosters innovation in product design. Moreover, plastic mold tooling empowers industries to meet the growing demand for customized and high-quality products in today's competitive market landscape.
Techniques and Processes
Plastic mold tooling encompasses a diverse range of techniques and processes, each tailored to specific manufacturing requirements. Injection molding, the most common method, involves injecting molten plastic into a mold cavity under high pressure. This technique offers versatility in design and material selection, making it ideal for producing a wide array of plastic components. Other techniques include blow molding, compression molding, and rotational molding, each offering unique advantages in terms of production efficiency and product quality.
Innovations Driving the Industry Forward
The field of plastic mold tooling is constantly evolving, driven by continuous innovation and technological advancements. Additive manufacturing, commonly known as 3D printing, has emerged as a disruptive force, revolutionizing the prototyping and production of plastic molds. By enabling rapid iteration and customization, 3D printing accelerates the product development cycle and reduces time-to-market. Furthermore, advancements in mold design software and simulation tools empower engineers to optimize mold performance and minimize defects, leading to higher productivity and quality in manufacturing.
Challenges and Solutions
Despite its many advantages, plastic mold tooling faces several challenges, ranging from material selection to mold maintenance. One significant challenge is achieving precise dimensional accuracy and surface finish, especially for complex geometries and thin-walled parts. To address this challenge, manufacturers are investing in advanced mold materials and coatings, as well as implementing process optimization techniques such as scientific molding. Additionally, the growing emphasis on sustainability has prompted the development of eco-friendly materials and recycling solutions, reducing the environmental impact of plastic mold tooling processes.
Future Prospects and Opportunities
Looking ahead, the future of plastic mold tooling holds immense promise, driven by ongoing technological innovation and market demand. Industry 4.0 technologies, including automation, robotics, and artificial intelligence, are expected to revolutionize the manufacturing landscape, enhancing productivity, efficiency, and flexibility in plastic mold tooling processes. Moreover, the advent of smart manufacturing concepts such as digital twinning and predictive maintenance will enable real-time monitoring and optimization of mold performance, further improving quality and reducing downtime. As manufacturers continue to explore new materials, processes, and applications, plastic mold tooling will remain a vital enabler of innovation and progress in the global manufacturing industry.
Conclusion
In conclusion, plastic mold tooling plays a pivotal role in modern manufacturing, enabling the efficient production of high-quality plastic components across various industries. By leveraging advanced techniques, embracing innovation, and addressing challenges, the field of plastic mold tooling continues to evolve and thrive. As we look to the future, embracing emerging technologies and sustainable practices will be key to unlocking new opportunities and driving further advancements in plastic mold tooling. With its profound impact on product development, manufacturing efficiency, and market competitiveness, plastic mold tooling remains an indispensable cornerstone of the industrial landscape.
GETTING A QUOTE WITH LK-MOULD IS FREE AND SIMPLE.
FIND MORE OF OUR SERVICES:
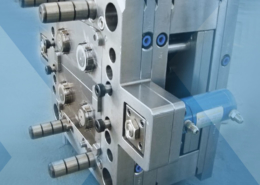
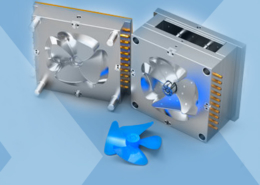
Plastic Molding

Rapid Prototyping
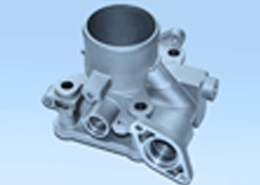
Pressure Die Casting
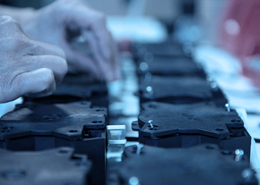
Parts Assembly
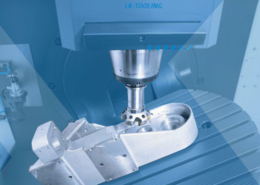