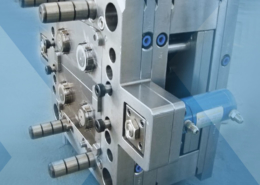
Plastic Mold Press: Revolutionizing Manufacturing Efficiency
Author:gly Date: 2024-06-08
Plastic mold press technology has become an indispensable tool in modern manufacturing, offering unmatched precision, efficiency, and versatility in the production of plastic components. In this comprehensive exploration, we delve into the intricacies of plastic mold presses, from their historical roots to their contemporary applications and future prospects.
Unveiling Plastic Mold Presses
Plastic mold presses, also known as injection molding machines, are sophisticated manufacturing devices designed to melt and inject molten plastic into a predefined mold cavity, resulting in the formation of precise and intricate plastic components. These machines have revolutionized the production process by enabling high-volume, high-speed manufacturing with minimal waste and unparalleled repeatability.
The concept of injection molding dates back to the late 19th century, with the first patent for an injection molding machine granted in 1872 to John Wesley Hyatt. Since then, continuous advancements in materials, technology, and process optimization have propelled plastic mold presses to the forefront of modern manufacturing.
Advancements in Machine Design
Over the years, plastic mold press technology has undergone significant evolution, with continuous improvements in machine design, control systems, and automation capabilities. Modern plastic mold presses feature robust hydraulic or electric-driven systems that deliver precise control over injection pressure, speed, and temperature, ensuring consistent part quality and dimensional accuracy.
Furthermore, the integration of advanced sensors, actuators, and monitoring systems enables real-time process monitoring and optimization, enhancing productivity and reducing downtime. Additionally, the adoption of servo-driven motors and energy-efficient components contributes to sustainability efforts by minimizing energy consumption and carbon footprint.
Material and Mold Considerations
The success of plastic mold pressing relies not only on the machine itself but also on the selection of suitable materials and mold design considerations. A wide range of thermoplastic and thermosetting materials are compatible with injection molding, each offering unique properties and characteristics.
Moreover, mold design plays a crucial role in determining part quality, cycle time, and production efficiency. Factors such as gate design, cooling channels, and venting systems must be carefully considered to optimize mold filling, minimize defects, and maximize throughput.
Applications Across Industries
Plastic mold presses find extensive applications across a diverse range of industries, including automotive, electronics, medical devices, consumer goods, and packaging. In the automotive sector, plastic mold presses are used for manufacturing interior and exterior components, such as dashboards, bumpers, and trim panels, due to their high strength, durability, and design flexibility.
Similarly, in the electronics industry, plastic mold pressing enables the production of precision components, such as casings, connectors, and housings, meeting stringent requirements for dimensional accuracy and surface finish. The versatility and scalability of plastic mold presses make them indispensable tools for manufacturers seeking to innovate and streamline production processes across various sectors.
Challenges and Future Directions
Despite their numerous advantages, plastic mold presses face challenges such as material selection, mold design complexity, and environmental sustainability. Addressing these challenges requires interdisciplinary research and collaboration among material scientists, engineers, and manufacturers.
Looking ahead, the future of plastic mold pressing lies in the integration of digital technologies, such as artificial intelligence, machine learning, and additive manufacturing. By leveraging these technologies, manufacturers can optimize process parameters, improve part quality, and accelerate time-to-market for new products.
In conclusion, plastic mold presses represent a cornerstone of modern manufacturing, offering unparalleled precision, efficiency, and versatility in the production of plastic components. With continuous innovation and advancements, plastic mold presses will continue to drive efficiency, sustainability, and innovation across industries, shaping the future of manufacturing for generations to come.
GETTING A QUOTE WITH LK-MOULD IS FREE AND SIMPLE.
FIND MORE OF OUR SERVICES:
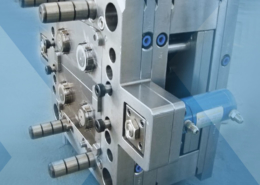
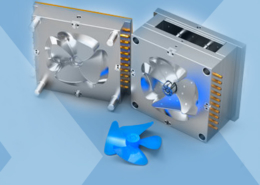
Plastic Molding

Rapid Prototyping
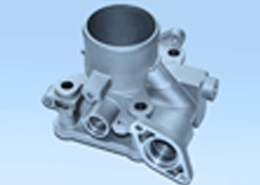
Pressure Die Casting
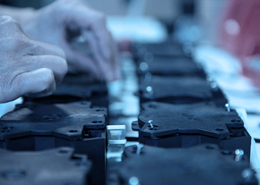
Parts Assembly
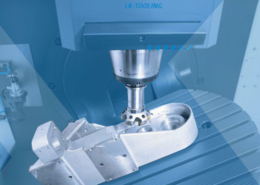