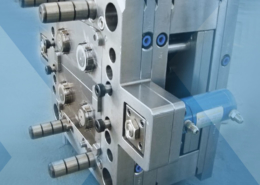
Exploring the Dynamics of Plastic Molded Products
Author:gly Date: 2024-06-08
Introduction
Plastic molded products represent a cornerstone of modern manufacturing, offering versatility, efficiency, and cost-effectiveness across a myriad of industries. From consumer goods to automotive components, their ubiquity underscores their significance in contemporary society. This article delves into the multifaceted world of plastic molded products, elucidating their various aspects, from production techniques to environmental impacts, aiming to provide readers with a comprehensive understanding of their importance and implications.
Production Techniques
Plastic molded products encompass a diverse array of manufacturing processes, each tailored to specific requirements. Injection molding, the most prevalent technique, involves injecting molten plastic into a mold cavity, where it solidifies into the desired shape. This method offers high precision and rapid production rates, making it ideal for mass production of intricate components. Conversely, rotational molding entails heating and rotating a hollow mold filled with plastic powder, resulting in seamless, hollow products like tanks and containers.
Another prominent method is blow molding, which utilizes air pressure to inflate molten plastic into a mold cavity, yielding hollow objects such as bottles and containers. Compression molding, characterized by compressing preheated plastic sheets or compounds into a mold, finds applications in manufacturing durable products like automotive parts and electrical components. Understanding these techniques is crucial for optimizing product design and production efficiency.
Material Selection
The choice of plastic material profoundly influences the performance, durability, and environmental footprint of molded products. Polyethylene (PE), renowned for its flexibility and chemical resistance, dominates packaging and consumer goods due to its affordability and versatility. Polypropylene (PP) offers similar advantages along with enhanced heat resistance, making it suitable for automotive parts and medical devices.
For applications requiring superior mechanical properties, acrylonitrile butadiene styrene (ABS) emerges as a preferred option, excelling in impact resistance and dimensional stability. Meanwhile, polycarbonate (PC) stands out for its exceptional transparency and strength, rendering it indispensable in optical applications and electronic enclosures. Moreover, bioplastics derived from renewable sources exhibit promising potential in mitigating environmental concerns associated with conventional plastics.
Design Considerations
Effective design plays a pivotal role in maximizing the functionality, aesthetics, and manufacturability of plastic molded products. Utilizing computer-aided design (CAD) software enables engineers to iteratively refine product designs, optimizing geometric complexity and material distribution for enhanced performance and cost-efficiency. Incorporating features such as draft angles and fillets facilitates mold release and minimizes defects like sink marks and warpage.
Furthermore, embracing design for manufacturability (DFM) principles streamlines the production process by minimizing tooling complexity, reducing cycle times, and enhancing product quality. Employing advanced simulation tools allows designers to predict and mitigate potential issues such as mold filling imbalance and residual stresses, ensuring robustness and reliability throughout the product lifecycle.
Environmental Implications
Despite their undeniable utility, plastic molded products raise concerns regarding environmental sustainability and waste management. The proliferation of single-use plastics exacerbates pollution and endangers ecosystems, necessitating concerted efforts to promote recycling and circular economy initiatives. Enhancing material recyclability and incorporating bio-based alternatives can mitigate environmental impact while conserving finite resources.
Furthermore, adopting eco-friendly manufacturing practices, such as energy-efficient processes and renewable energy utilization, can reduce carbon emissions and minimize ecological footprint. Embracing closed-loop systems that facilitate the recovery and repurposing of post-consumer plastics fosters a circular economy paradigm, wherein waste is transformed into valuable resources, promoting environmental stewardship and long-term sustainability.
Conclusion
Plastic molded products epitomize innovation and efficiency in modern manufacturing, offering unparalleled versatility and scalability across diverse industries. Understanding the intricacies of production techniques, material selection, design considerations, and environmental implications is paramount for optimizing performance, minimizing environmental footprint, and fostering sustainable development. By embracing technological advancements and holistic approaches, stakeholders can harness the full potential of plastic molded products while mitigating their adverse effects, thereby shaping a more resilient and sustainable future.
GETTING A QUOTE WITH LK-MOULD IS FREE AND SIMPLE.
FIND MORE OF OUR SERVICES:
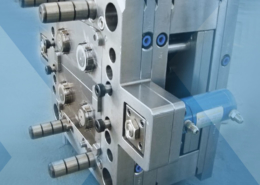
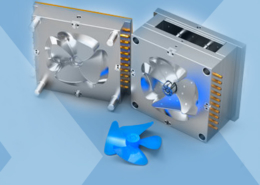
Plastic Molding

Rapid Prototyping
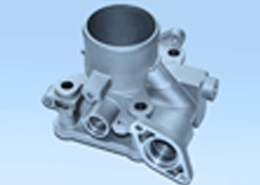
Pressure Die Casting
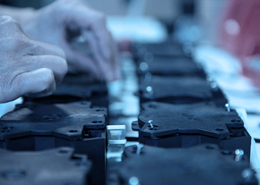
Parts Assembly
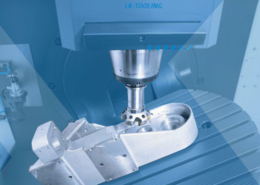