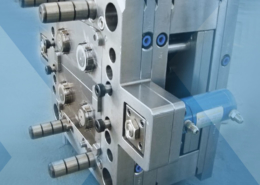
Exploring Plastic Bucket Moulds: Innovation in Manufacturing
Author:gly Date: 2024-06-08
Plastic bucket moulds represent a cornerstone of modern manufacturing, facilitating the production of versatile and durable containers essential in various industries. This article aims to provide readers with an insightful exploration of plastic bucket moulds, from their inception to their significance in contemporary production processes.
Unveiling Plastic Bucket Moulds: A Fascinating Introduction
Plastic bucket moulds play a pivotal role in the production of plastic buckets, pails, and containers of different shapes and sizes. These moulds are meticulously designed to create seamless and structurally sound products, meeting the diverse needs of consumers and industries worldwide.
Background Information
The advent of plastic bucket moulds revolutionized the packaging industry, offering cost-effective solutions for storing, transporting, and distributing liquids, solids, and powders. With advancements in moulding technology and materials, plastic bucket moulds continue to evolve, enabling manufacturers to produce innovative designs with enhanced functionality and aesthetics.
The Anatomy of Plastic Bucket Moulds
Plastic bucket moulds comprise several components, each serving a specific function in the moulding process. These components include the core, cavity, ejector pins, cooling system, and gating system, working in tandem to ensure precise and efficient moulding operations.
Core and Cavity
The core and cavity are the primary components of the mould responsible for shaping the plastic material into the desired form. These components are precision-machined to mirror the exact dimensions and contours of the final product, ensuring uniformity and consistency in every moulded part.
Cooling System
Efficient cooling is crucial in plastic moulding to solidify the molten material and expedite the production cycle. Plastic bucket moulds are equipped with intricate cooling systems, comprising channels and circuits strategically positioned to dissipate heat and maintain optimal temperature levels throughout the mould.
Gating System
The gating system regulates the flow of molten plastic into the mould cavity, determining the filling pattern and minimizing the occurrence of defects such as air traps, weld lines, and shrinkage. Various gating techniques, including edge gating, pin gating, and hot runner gating, offer flexibility and precision in moulding operations.
Applications and Industries
Plastic bucket moulds find widespread use across diverse industries, serving as indispensable tools in packaging, agriculture, construction, and household sectors. Their versatility, durability, and cost-effectiveness make them ideal for storing and transporting a wide range of materials and products.
Packaging Industry
In the packaging industry, plastic bucket moulds are instrumental in producing containers for food, beverages, chemicals, and personal care products. Their lightweight yet robust construction ensures product integrity during storage, transit, and display, meeting stringent quality and safety standards.
Agriculture and Horticulture
Plastic buckets and pails are commonly used in agriculture and horticulture for storing and transporting seeds, fertilizers, pesticides, and harvested produce. These containers offer convenience, portability, and protection against environmental factors, contributing to efficient farm management and crop cultivation.
Construction Sector
In the construction sector, plastic buckets play a vital role in mixing, transporting, and applying construction materials such as cement, mortar, and adhesives. Their rugged construction and ergonomic design make them ideal for heavy-duty applications on construction sites, enhancing productivity and worker safety.
Advancements and Future Directions
As technology continues to evolve, plastic bucket moulds are poised for further advancements in design, materials, and manufacturing processes. Innovations such as 3D printing, multi-material moulding, and sustainable materials offer new possibilities for improving efficiency, reducing environmental impact, and expanding application areas.
Sustainable Solutions
In response to growing environmental concerns, there is a growing emphasis on sustainable manufacturing practices in the plastics industry. Future developments in plastic bucket moulds may focus on incorporating recycled materials, optimizing resource usage, and minimizing waste generation, paving the way for a more eco-friendly approach to plastic packaging.
Conclusion: Shaping the Future of Manufacturing
In conclusion, plastic bucket moulds represent a cornerstone of modern manufacturing, facilitating the production of essential containers used across industries worldwide. From their intricate design to their diverse applications, plastic bucket moulds exemplify innovation, efficiency, and versatility in the realm of plastics processing. Embracing technological advancements and sustainable practices will continue to drive the evolution of plastic bucket moulds, shaping the future of manufacturing in a rapidly changing world.
GETTING A QUOTE WITH LK-MOULD IS FREE AND SIMPLE.
FIND MORE OF OUR SERVICES:
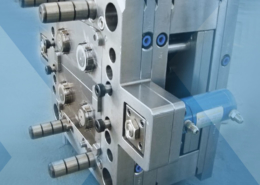
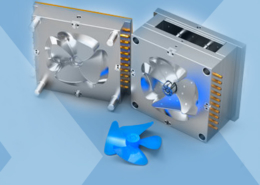
Plastic Molding

Rapid Prototyping
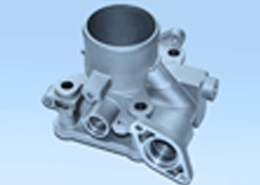
Pressure Die Casting
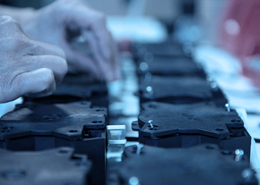
Parts Assembly
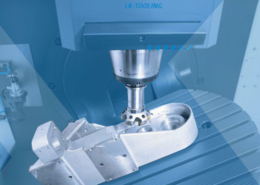