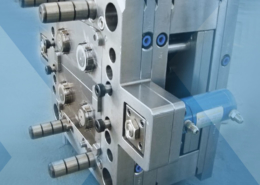
Exploring Plastic Mold Parts: Innovation and Application
Author:gly Date: 2024-06-08
Introduction:
Plastic mold parts are integral components in various industries, facilitating the production of intricate and functional products. This article delves into the realm of plastic mold parts, elucidating their significance, applications, and evolving trends.
1. Understanding Plastic Mold Parts:
Plastic mold parts, also known as injection mold parts, are manufactured through the injection molding process, wherein molten plastic material is injected into a mold cavity and cooled to form the desired shape. This process offers unmatched precision, repeatability, and efficiency, making it indispensable in modern manufacturing.
Plastic mold parts encompass a diverse range of products, including automotive components, consumer electronics, medical devices, and household appliances. From intricate gears to complex housings, plastic mold parts play a pivotal role in shaping various aspects of everyday life.
2. Material Selection and Properties:
Material selection is paramount in plastic mold part manufacturing, as it directly influences the properties and performance of the final product. A myriad of thermoplastic and thermosetting materials are utilized, each offering distinct characteristics such as strength, durability, and thermal resistance.
Common materials include ABS, polycarbonate, polypropylene, and nylon, chosen based on factors such as application requirements, cost-effectiveness, and environmental considerations. Understanding material properties and their interactions is essential for achieving optimal results in plastic mold part production.
3. Design Considerations and Optimization:
Designing plastic mold parts requires meticulous attention to detail and adherence to design principles to ensure manufacturability and functionality. Key considerations include part geometry, draft angles, wall thickness, and surface finish.
Utilizing computer-aided design (CAD) software enables designers to simulate molding processes, identify potential issues, and optimize designs for enhanced moldability and performance. Iterative prototyping and testing further refine designs, minimizing defects and maximizing productivity.
4. Emerging Trends and Future Directions:
The landscape of plastic mold part manufacturing is continuously evolving, driven by technological advancements and market demands. Emerging trends include the integration of additive manufacturing techniques, such as 3D printing, for rapid prototyping and customization.
Furthermore, the adoption of smart materials and Industry 4.0 technologies, such as IoT-enabled sensors and predictive analytics, promises to revolutionize production processes, enhancing efficiency, and quality control. Research into sustainable materials and eco-friendly manufacturing practices is also gaining traction, reflecting a growing emphasis on environmental stewardship and circular economy principles.
Conclusion:
Plastic mold parts represent a cornerstone of modern manufacturing, enabling the production of complex and functional components across diverse industries. Understanding the intricacies of material selection, design optimization, and emerging trends is essential for harnessing the full potential of plastic mold part technology.
As technology continues to advance, embracing innovation and embracing sustainable practices will be crucial for driving the future of plastic mold part manufacturing. By fostering collaboration, investing in research, and embracing transformative technologies, the industry can pave the way for a more efficient, sustainable, and interconnected future.
Through continuous learning and adaptation, plastic mold parts will remain at the forefront of innovation, shaping the way we design, produce, and interact with products in the years to come.
GETTING A QUOTE WITH LK-MOULD IS FREE AND SIMPLE.
FIND MORE OF OUR SERVICES:
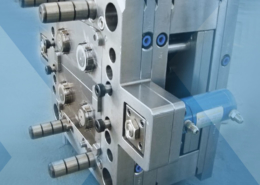
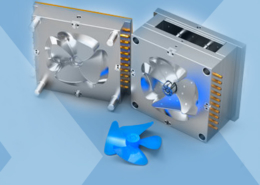
Plastic Molding

Rapid Prototyping
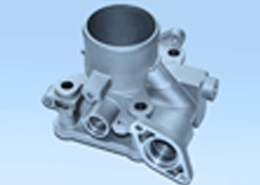
Pressure Die Casting
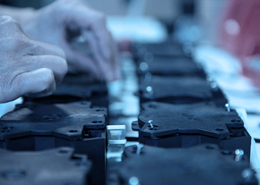
Parts Assembly
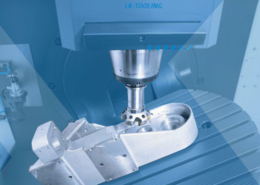