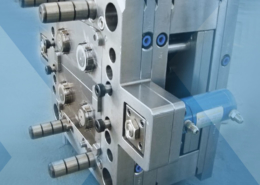
Exploring the World of Plastic Cap Moulds: A Comprehensive Guide
Author:gly Date: 2024-06-08
Plastic cap moulds play a crucial role in the packaging industry, enabling the production of caps and closures that seal and protect a wide range of products. From beverages to pharmaceuticals, plastic cap moulds are essential components of packaging solutions, ensuring product integrity and consumer safety. In this article, we delve into the intricacies of plastic cap moulds, from their design and manufacturing process to their applications and future prospects.
Introduction to Plastic Cap Moulds
Plastic cap moulds are specialized tools used in the injection moulding process to produce caps and closures for bottles, jars, tubes, and containers. These moulds are designed to impart precise shapes, dimensions, and features to the caps, ensuring compatibility with the corresponding containers and meeting stringent quality standards. As an integral part of packaging systems, plastic cap moulds contribute to product freshness, tamper resistance, and brand identity, making them indispensable in various industries.
Evolution of Plastic Cap Moulds
Historical Context
The development of plastic cap moulds can be traced back to the mid-20th century, coinciding with the rapid expansion of the plastics industry and the adoption of injection moulding technology. Initially used for simple screw caps, plastic cap moulds have evolved to accommodate a wide range of designs, including flip-top caps, snap caps, and child-resistant closures. Advancements in materials science, mould design, and manufacturing processes have enabled the production of caps with enhanced functionality, aesthetics, and performance.
Design and Manufacturing Process
Plastic cap moulds undergo a meticulous design and manufacturing process to ensure precision, reliability, and efficiency. The design phase involves CAD/CAM software to create 3D models of the mould cavity, incorporating features such as threads, tamper bands, and sealing surfaces. Once the design is finalized, CNC machining or EDM techniques are employed to fabricate the mould inserts with high precision and surface finish, ensuring optimal moulding conditions and part quality.
Injection Moulding Process
During the injection moulding process, molten plastic is injected into the mould cavity under high pressure, where it solidifies to form the desired cap shape. Factors such as material selection, melt temperature, injection speed, and cooling time are carefully controlled to achieve uniform filling, minimize defects, and optimize cycle times. With advancements in automation and process monitoring, manufacturers can achieve higher productivity and consistency in cap production.
Applications and Industry Trends
Plastic cap moulds find applications across diverse industries, including food and beverage, pharmaceuticals, cosmetics, and household products. In the food and beverage sector, plastic caps ensure product freshness and integrity, preventing contamination and leakage. In pharmaceuticals, tamper-evident closures provide security and reassurance to consumers, safeguarding against counterfeit and tampering. As consumer preferences evolve and sustainability concerns grow, industry trends such as lightweighting, recyclability, and biodegradability are influencing the design and production of plastic caps.
Sustainability Initiatives
Amid increasing awareness of environmental issues, the packaging industry is embracing sustainability initiatives to reduce waste and minimize environmental impact. Plastic cap mould manufacturers are exploring alternative materials, such as bio-based plastics and recycled resins, to create eco-friendly caps with comparable performance to conventional plastics. Additionally, innovations in design optimization, lightweighting, and recycling technologies are driving progress towards a circular economy model, where plastic caps are reused, recycled, or composted at the end of their life cycle.
Conclusion
In conclusion, plastic cap moulds play a vital role in the packaging industry, enabling the production of caps and closures that ensure product safety, freshness, and convenience. As consumer preferences evolve and sustainability concerns intensify, plastic cap mould manufacturers are innovating to meet the changing needs of the market. By embracing advanced technologies, sustainable practices, and collaborative partnerships, the industry is poised to drive positive change and shape the future of packaging solutions. Through continuous innovation and a commitment to quality and sustainability, plastic cap moulds will remain indispensable components of packaging systems, facilitating the delivery of safe, reliable, and environmentally responsible products to consumers worldwide.
GETTING A QUOTE WITH LK-MOULD IS FREE AND SIMPLE.
FIND MORE OF OUR SERVICES:
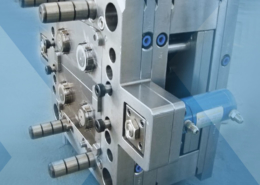
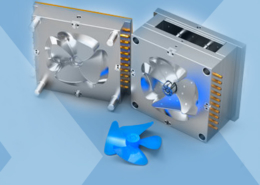
Plastic Molding

Rapid Prototyping
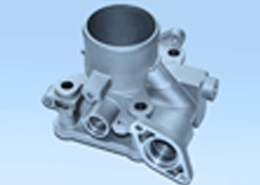
Pressure Die Casting
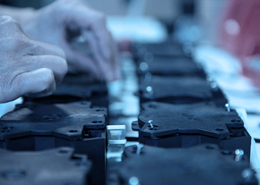
Parts Assembly
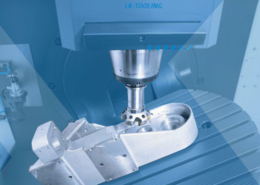