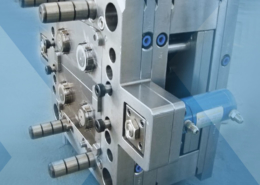
Melting and Molding Plastic: Revolutionizing Manufacturing
Author:gly Date: 2024-06-08
Plastic, an omnipresent material in our modern world, has revolutionized the manufacturing industry with its versatility and ease of manipulation. The process of melting and molding plastic lies at the heart of this revolution, offering endless possibilities for creating a wide array of products. In this article, we delve into the intricacies of melting and molding plastic, exploring its various aspects and the profound impact it has on industries and everyday life.
1. Understanding Plastic Melting
Plastic melting is the initial step in the manufacturing process, where raw plastic material is heated to its melting point, transforming it into a molten state. This molten plastic can then be easily shaped and molded into desired forms using various techniques such as injection molding, blow molding, or extrusion. The choice of melting technique depends on factors like the type of plastic, desired product specifications, and production scale.
The melting process involves precise temperature control to prevent degradation of the plastic material. Different types of plastics have distinct melting points, necessitating specific heating conditions for optimal results. Moreover, additives like stabilizers and colorants may be incorporated into the molten plastic to enhance its properties or achieve desired aesthetics.
2. Injection Molding: Precision Engineering
Injection molding is a widely used technique for producing intricate plastic components with high precision and efficiency. It involves injecting molten plastic material into a mold cavity under high pressure, where it solidifies to form the desired shape. The versatility of injection molding allows for the production of complex geometries and the incorporation of features such as threads, undercuts, and fine details.
The process begins with the design of a mold, which is typically made of metal and precision-machined to exact specifications. Molten plastic resin is then injected into the mold cavity using a reciprocating screw injector, ensuring uniform distribution and filling of the mold. Once the plastic cools and solidifies, the mold opens, and the finished part is ejected, ready for further processing or assembly.
3. Environmental Considerations
While plastic melting and molding offer unparalleled manufacturing capabilities, they also raise concerns regarding environmental sustainability and waste management. The widespread use of plastics has led to pollution, ecosystem degradation, and the accumulation of plastic waste in landfills and oceans. Addressing these challenges requires innovative solutions, such as recycling, biodegradable plastics, and eco-friendly manufacturing practices.
Recycling plays a crucial role in mitigating the environmental impact of plastic waste by diverting used plastics from landfills and incineration. Advanced recycling technologies, such as chemical recycling and mechanical recycling, enable the conversion of waste plastics into raw materials for new products, reducing the reliance on virgin plastic production. Additionally, the development of biodegradable plastics offers a promising alternative to conventional plastics, as they can decompose naturally in the environment, minimizing long-term pollution.
4. Future Directions and Innovations
Looking ahead, advancements in materials science, manufacturing technology, and sustainability will continue to shape the landscape of plastic melting and molding. Researchers are exploring novel materials with enhanced properties, such as bioplastics derived from renewable sources and engineered polymers with superior strength and durability. Furthermore, the integration of digital manufacturing technologies, such as 3D printing and computer-aided design, enables rapid prototyping and customization, driving innovation and efficiency in plastic manufacturing processes.
In conclusion, melting and molding plastic represent a cornerstone of modern manufacturing, offering limitless possibilities for innovation and creativity. By understanding the intricacies of plastic melting, embracing sustainable practices, and fostering innovation, we can harness the full potential of this versatile material while minimizing its environmental footprint. Together, we can pave the way towards a more sustainable and prosperous future.
GETTING A QUOTE WITH LK-MOULD IS FREE AND SIMPLE.
FIND MORE OF OUR SERVICES:
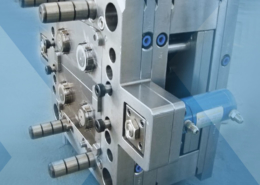
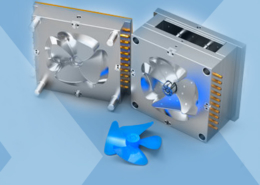
Plastic Molding

Rapid Prototyping
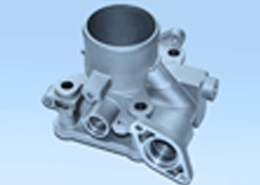
Pressure Die Casting
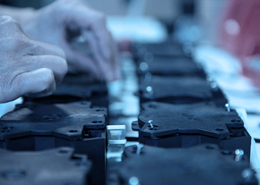
Parts Assembly
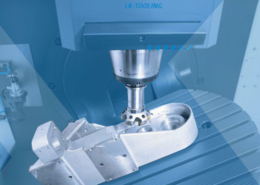