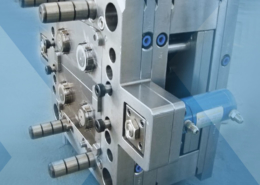
Metal Molds for Plastic: Revolutionizing Manufacturing Processes
Author:gly Date: 2024-06-08
Plastics have become an indispensable part of modern manufacturing, finding application in a myriad of industries ranging from automotive to consumer goods. Central to the production of plastic components is the use of metal molds, which play a pivotal role in shaping and forming these materials into desired shapes and sizes. In this article, we delve into the world of metal molds for plastic, exploring their significance, applications, and advancements.
The Importance of Metal Molds
Metal molds serve as the backbone of plastic manufacturing processes, offering precision, repeatability, and efficiency. Unlike traditional methods, such as manual molding, metal molds ensure uniformity in product dimensions and surface finish, essential for meeting quality standards in mass production. Moreover, the durability and heat resistance of metals enable the molding of a wide range of plastic materials, including thermoplastics and thermosets.
Metal molds have revolutionized the manufacturing landscape by facilitating intricate designs and complex geometries previously unattainable through other methods. From intricate automotive components to delicate medical devices, metal molds empower designers and engineers to materialize their innovative concepts with precision and reliability.
Advancements in Metal Mold Technology
In recent years, advancements in materials science and manufacturing technology have propelled metal mold development to new heights. The integration of computer-aided design (CAD) and computer-aided manufacturing (CAM) has streamlined the mold design process, allowing for rapid prototyping and iteration. Additionally, the use of advanced materials, such as hardened steels and exotic alloys, has enhanced mold longevity and wear resistance, prolonging operational lifespan and reducing downtime.
Furthermore, the advent of additive manufacturing, commonly known as 3D printing, has opened new avenues for metal mold production. Additive manufacturing techniques enable the creation of complex mold geometries with intricate cooling channels, optimizing cycle times and improving part quality. This convergence of digital design and advanced manufacturing techniques heralds a new era of customization and on-demand production in the plastic molding industry.
Applications Across Industries
Metal molds for plastic find extensive applications across various industries, driving innovation and efficiency in manufacturing processes. In the automotive sector, metal molds are utilized for the production of exterior body panels, interior components, and functional parts, contributing to lightweighting initiatives and fuel efficiency improvements. Similarly, in the electronics industry, metal molds enable the fabrication of intricate casings, connectors, and housings for electronic devices, ensuring precise fit and function.
Moreover, the medical and aerospace sectors benefit from the use of metal molds for the fabrication of critical components with stringent tolerances and regulatory requirements. From surgical instruments to aircraft interiors, metal molds play a vital role in ensuring product integrity and performance in demanding applications.
Challenges and Future Perspectives
Despite the numerous advantages offered by metal molds for plastic, challenges remain in terms of cost, lead time, and environmental impact. The initial investment required for mold design and fabrication can be substantial, particularly for complex geometries and specialized materials. Additionally, long lead times associated with traditional manufacturing processes may hinder responsiveness to market demands and product iterations.
Looking ahead, research efforts are focused on addressing these challenges through advancements in material science, process optimization, and sustainability initiatives. Novel approaches, such as hybrid manufacturing combining additive and subtractive techniques, hold promise for reducing costs and lead times while enhancing design flexibility. Furthermore, the adoption of recyclable and biodegradable materials in mold construction aligns with the growing emphasis on environmental sustainability in the manufacturing sector.
In conclusion, metal molds for plastic represent a cornerstone of modern manufacturing, enabling the realization of complex designs and ensuring product quality and consistency across industries. With continued innovation and collaboration, the future holds exciting possibilities for further enhancing the efficiency, sustainability, and versatility of metal mold technology in shaping the world of plastic manufacturing.
GETTING A QUOTE WITH LK-MOULD IS FREE AND SIMPLE.
FIND MORE OF OUR SERVICES:
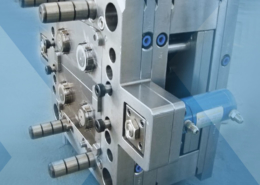
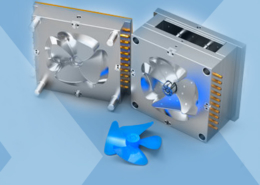
Plastic Molding

Rapid Prototyping
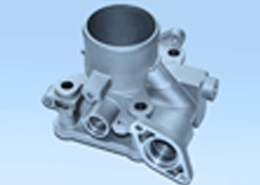
Pressure Die Casting
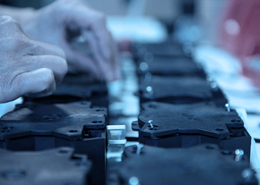
Parts Assembly
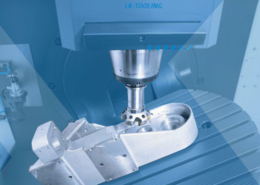