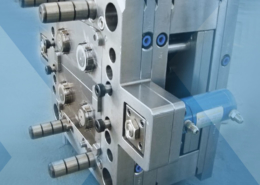
Exploring the World of Medical Plastic Injection Molding
Author:gly Date: 2024-06-08
Medical plastic injection molding is a fascinating and integral process within the realm of medical device manufacturing. It involves the creation of intricate and precise components used in various medical applications through the injection of molten plastic into a mold cavity. This method offers unparalleled flexibility, efficiency, and precision, making it a cornerstone in the production of medical devices worldwide.
1. Precision and Accuracy
Achieving Microscopic Detail
One of the most remarkable aspects of medical plastic injection molding is its ability to produce parts with incredibly precise and intricate details. The process can create features as small as micrometers, crucial for medical devices where accuracy is paramount.
Consistency in Production
Moreover, the consistency achieved in each production cycle ensures uniformity across all parts, essential for maintaining the highest standards in medical equipment. This consistency minimizes defects and ensures reliability in the final product.
Applications in Complex Devices
From intricate surgical instruments to complex diagnostic equipment, the precision offered by injection molding enables the creation of sophisticated medical devices that meet the stringent requirements of modern healthcare.
2. Material Selection and Biocompatibility
Medical-Grade Materials
Choosing the right material is critical in medical device manufacturing to ensure safety and efficacy. Medical plastic injection molding utilizes a wide range of medical-grade materials, each selected for its specific properties and biocompatibility.
Ensuring Patient Safety
The biocompatibility of these materials is of utmost importance to prevent adverse reactions when the devices come into contact with patients. Rigorous testing and certification processes guarantee that the materials meet the necessary regulatory standards.
Compatibility with Sterilization Methods
Furthermore, these materials must withstand various sterilization methods without compromising their structural integrity or performance. Injection-molded medical components are designed to endure autoclaving, gamma radiation, ethylene oxide sterilization, and other sterilization processes commonly used in healthcare settings.
3. Design Flexibility and Innovation
Iterative Prototyping
Medical plastic injection molding facilitates iterative prototyping, allowing designers to quickly refine and optimize device designs. This agility in the prototyping phase accelerates the development timeline and ultimately brings innovative medical solutions to market faster.
Complex Geometries
The process enables the production of parts with complex geometries that would be challenging or impossible to achieve with traditional manufacturing methods. This capability opens up new possibilities for designing cutting-edge medical devices with enhanced functionality and performance.
Integration of Features
Moreover, injection molding allows for the integration of multiple features into a single component, reducing the need for assembly and minimizing the risk of failure points. This integration enhances the overall reliability and durability of medical devices.
4. Cost-Effectiveness and Scalability
Economies of Scale
Medical plastic injection molding offers significant cost advantages, particularly at scale. The ability to produce large volumes of parts quickly and efficiently results in economies of scale, driving down per-unit costs and making medical devices more accessible to patients.
Tooling Optimization
Additionally, advancements in tooling technologies and process optimization have further improved the cost-effectiveness of injection molding. Techniques such as mold flow analysis and rapid tooling development help minimize tooling costs and reduce time to market.
Sustainable Manufacturing Practices
Furthermore, the shift towards sustainable manufacturing practices has led to the development of biodegradable and recyclable materials for medical injection molding. These eco-friendly alternatives not only reduce environmental impact but also align with the growing demand for sustainable healthcare solutions.
Conclusion
In conclusion, medical plastic injection molding plays a pivotal role in the production of high-quality, reliable, and innovative medical devices. Its precision, material versatility, design flexibility, and cost-effectiveness make it indispensable in modern healthcare manufacturing. As technology continues to advance, the future of medical injection molding holds even greater promise, with potential advancements in materials, processes, and sustainability practices. Embracing these opportunities will undoubtedly lead to further improvements in patient care and medical outcomes.
GETTING A QUOTE WITH LK-MOULD IS FREE AND SIMPLE.
FIND MORE OF OUR SERVICES:
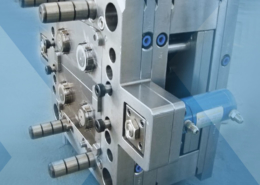
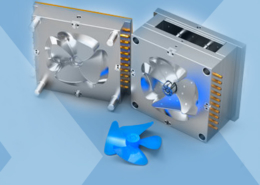
Plastic Molding

Rapid Prototyping
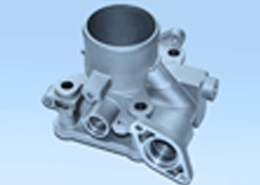
Pressure Die Casting
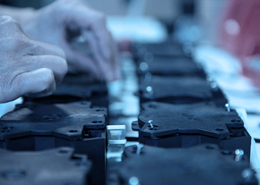
Parts Assembly
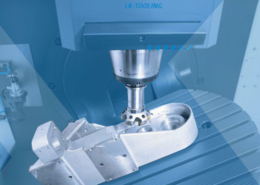