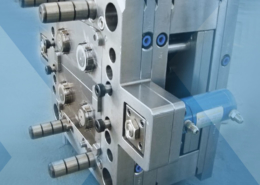
Plastic Injection Molding Market Size is expected to reach - automotive injectio
Author:gly Date: 2024-09-30
Investor & Media Contacts:Joe Caminiti or Stephen Poe, InvestorsTim Peters or Emma Brandeis, MediaNNBR@alpha-ir.com 312-445-2870
Join Engel in exploring the future of battery molding technology. Discover advancements in thermoplastic composites for battery housings, innovative automation solutions and the latest in large-tonnage equipment designed for e-mobility — all with a focus on cost-efficient solutions. Agenda: Learn about cutting-edge thermoplastic composites for durable, sustainable and cost-efficient battery housings Explore advanced automation concepts for efficient and scalable production See the latest large-tonnage equipment and technology innovations for e-mobility solutions
While prices moved up for three of the five commodity resins, there was potential for a flat trajectory for the rest of the third quarter.
Processors with sustainability goals or mandates have a number of ways to reach their goals. Biopolymers are among them.
August 29-30 in Minneapolis all things injection molding and moldmaking will be happening at the Hyatt Regency — check out who’s speaking on what topics today.
“NN is underway with a strategic transformation that includes leveraging our core competencies and implementing a supportive balance sheet” said Harold Bevis, President and CEO of NN, Inc. “IMC is a good, stand-alone plastics injection-molding plant and is not core to our strategic direction. Our core competencies are centered upon delivering globally competitive, mission critical manufacturing solutions to discriminating buyers of high-value, high-precision components and sub-assemblies. This plant is not consistent with this direction and is more general-purpose in nature. Furthermore, the products and customers in this plant are unique to it and there will be no impact to NN’s remaining business. The plant’s business is centered in generic vehicle parts and ball bearing components.”
Across all process types, sustainability was a big theme at NPE2024. But there was plenty to see in automation and artificial intelligence as well.
Solvay also reports interest in Tegracore PPSU foam, a novel high- temperature structural and insulating material based on Solvay’s Radel PPSU, for thermal insulation of the electrified powertrain and engine encapsulation, says Baleno. A key feature is its thermoforming capability, which enables foam shapes to be customized.
Thousands of people visit our Supplier Guide every day to source equipment and materials. Get in front of them with a free company profile.
Roederer also highlights softer flexible materials like Polyvin PVC and Invision TPEs for decorative trim like door and console armrests, shifter knobs, bin liners, and cup holders, which need a dry-to-the- touch and non-tacky feel. Polyfort filled, unfilled, and impact-modified PP in UV-stabilized custom colors also get play in pillar covers, door and instrument-panel components, and rear-quarter trim panels.
Polyscope is also targeting instrument-panel carriers where SMA can meet a broader temperature range (-35 C to 120 C or 31-248 F) than the widely used PP. In particular, PP does not have comparable low- temperature performance, which is important for airbag deployment.
Meanwhile, Polyscope’s main focus is on interior structural parts. Says Muezers,“We are aiming to achieve performance properties that bridge the gap between nylon 6 and nylon 66 in applications such as instrument-panel supports, structural consoles, audio components, and interior trim.” Since 2013, its Xiran IZ terpolymers—based on SMA and N-phenylmaleimide, have made significant commercial strides with several OEMs in sunroof frames. Applications such as this require a high degree of functional integration, high-precision molding, and greater stiffness. Xiran products replace glass-filled PBT/ASA blends, which can have warpage issues, cost more, and are more difficult to process.
Sustainability continues to dominate new additives technology, but upping performance is also evident. Most of the new additives have been targeted to commodity resins and particularly polyolefins.
Multiple speakers at Molding 2023 will address the ways simulation can impact material substitution decisions, process profitability and simplification of mold design.
When, how, what and why to automate — leading robotics suppliers and forward-thinking moldmakers will share their insights on automating manufacturing at collocated event.
Plastics Technology’s Tech Days is back! Every Tuesday in October, a series of five online presentations will be given by industry supplier around the following topics: Injection Molding — New Technologies, Efficiencies Film Extrusion — New Technologies, Efficiencies Upstream/Downstream Operations Injection Molding — Sustainability Extrusion — Compounding Coming out of NPE2024, PT identified a variety of topics, technologies and trends that are driving and shaping the evolution of plastic products manufacturing — from recycling/recyclability and energy optimization to AI-based process control and automation implementation. PT Tech Days is designed to provide a robust, curated, accessible platform through which plastics professionals can explore these trends, have direct access to subject-matter experts and develop strategies for applying solutions in their operations.
With it acquisition of DuPont’s engineering resins, Celanese’s resin solutions for automotive electrification, e-mobility and consumer electronics are plentiful.
Helms also sees increasing demand for power electronics in both vehicle interior and exterior. “You can imagine these systems will continue to grow as more active safety systems are incorporated, culminating in a growing fleet of autonomous and semiautonomous vehicles” He notes that Celanese is working with both OEMs and component suppliers to help them manage heat dissipation in these devices while minimizing the added part weight and cost.
This Knowledge Center provides an overview of the considerations needed to understand the purchase, operation, and maintenance of a process cooling system.
In this three-part collection, veteran molder and moldmaker Jim Fattori brings to bear his 40+ years of on-the-job experience and provides molders his “from the trenches” perspective on on the why, where and how of venting injection molds. Take the trial-and-error out of the molding venting process.
This press release contains forward-looking statements within the meaning of Section 27A of the Securities Act of 1933, as amended, and Section 21E of the Securities Exchange Act of 1934, as amended, which are intended to be covered by the safe harbor provisions of the Private Securities Litigation Reform Act of 1995 and include this statement for purposes of complying with these safe harbor provisions. Except for specific historical information, many of the matters discussed in this press release may express or imply projections of revenues or expenditures, statements of plans and objectives or future operations or statements of future economic performance. These statements may discuss goals, intentions, and expectations as to future trends, plans, events, results of operations or financial condition, or state other information relating to NN, Inc. based on current beliefs of management as well as assumptions made by, and information currently available to, management. Forward-looking statements generally will be accompanied by words such as “anticipate,” “believe,” “could,” “estimate,” “expect,” “forecast,” “guidance,” “intend,” “may,” “possible,” “potential,” “predict,” “project” or other similar words, phrases or expressions. Forward-looking statements involve a number of risks and uncertainties that are outside of management’s control and that may cause actual results to be materially different from such forward-looking statements. Such factors include, among others, general economic conditions and economic conditions in the industrial sector; the impacts of pandemics, epidemics, disease outbreaks and other public health crises on our financial condition, business operations and liquidity; competitive influences; risks that current customers will commence or increase captive production; risks of capacity underutilization; quality issues; material changes in the costs and availability of raw materials; economic, social, political and geopolitical instability, military conflict, currency fluctuation, and other risks of doing business outside of the United States; inflationary pressures and changes in the cost or availability of materials, supply chain shortages and disruptions, the availability of labor and labor disruptions along the supply chain; our dependence on certain major customers, some of whom are not parties to long-term agreements (and/or are terminable on short notice); the impact of acquisitions and divestitures, as well as expansion of end markets and product offerings; our ability to hire or retain key personnel; the level of our indebtedness; the restrictions contained in our debt agreements; our ability to obtain financing at favorable rates, if at all, and to refinance existing debt as it matures; new laws and governmental regulations; the impact of climate change on our operations; and cyber liability or potential liability for breaches of our or our service providers’ information technology systems or business operations disruptions. The foregoing factors should not be construed as exhaustive and should be read in conjunction with the sections entitled “Risk Factors” and “Management’s Discussion and Analysis of Financial Condition and Results of Operations” included in the Company’s filings made with the Securities and Exchange Commission. Any forward-looking statement speaks only as of the date of this press release, and the Company undertakes no obligation to publicly update or review any forward-looking statement, whether as a result of new information, future developments or otherwise, except as required by law. New risks and uncertainties may emerge from time to time, and it is not possible for the Company to predict their occurrence or how they will affect the Company. The Company qualifies all forward-looking statements by these cautionary statements.
Celanese has continued to reduce volatile emissions in interiors with a novel family of acetals that boast formaldehyde emission levels as low as 2 ppm. These Hostaform XAP2 grades reportedly are now the benchmark for acetals in vehicle interiors. They are used in locks, head-rest guide sleeves, HVAC components, buttons, speaker grills, etc. Speaker grills represent a fairly large interior acetal part where its contribution to interior emissions is more heavily weighted. Celanese is continuing to push emission levels down with a next-generation XAP3 acetal line that promises formaldehyde emissions of 1 ppm.
This month’s resin pricing report includes PT’s quarterly check-in on select engineering resins, including nylon 6 and 66.
Mike Chiandussi, powertrain market segment specialist at BASF Corporation - Engineering Plastics, Florham Park, N.J., notes that powertrain and chassis account for more than 50% of the total weight of the vehicle. “It’s logical to take mass out of the largest pieces of the pie per se.” He notes that thermoplastics allow one to achieve complex geometries and design while driving weight out of the vehicle. But He also identifies technical challenges such as high-operating temperatures and chemical wear.
Torlon PAI is known for maintaining strength, stiffness, and toughness at high temperature. Its claim to fame is wear resistance in both lubricated and dry environments. Some grades specially formulated for wear resistance include ones with PTFE and graphite, carbon fiber, and carbon fiber plus PTFE. KetaSpire PEEK reportedly offers better fatigue and wear resistance, higher impact strength and higher ductility than other commercial PEEK products.
A. Schulman’s Lingnau cites compounds based on innovative reinforcements (such as micro or nano fillers) and polymer alloys that have lower density but the same performance profile as conventional compounds. “We have alternatives as drop-in products with 8-16% lower specific density, which is a big step forward.” Such compounds include Polyfort impact-modified PP with nano filler, which can be further optimized for weight reduction by adding glass spheres. He also cited the Shulamid nylon family aimed at lightweighting. Its reduced-density RD nylon 6 and RD nylon 66 grades are available with standard 15% and 30% glass fiber. Reduced-density PP compounds are also now available, based on minerals with reduced density and/or hollow glass bubbles.
BASF’s Chiandussi says the company’s Ultramid Endure high-heat-resistant nylon 66 portfolio can be used in turbocharged air-induction systems, including the air-intake manifold, charge-air ducts, resonators, intercooler end caps, and throttle bodies. It can also achieve long-term-service temperatures of 220 C/428 F and withstand peak temperatures of 240 C/464 F.
Join Wittmann for an engaging webinar on the transformative impact of manufacturing execution systems (MES) in the plastic injection molding industry. Discover how MES enhances production efficiency, quality control and real-time monitoring while also reducing downtime. It will explore the integration of MES with existing systems, emphasizing compliance and traceability for automotive and medical sectors. Learn about the latest advancements in IoT and AI technologies and how they drive innovation and continuous improvement in MES. Agenda: Overview of MES benefits What is MES? Definition, role and brief history Historical perspective and evolution Longevity and analytics Connectivity: importance, standards and integration Advantages of MES: efficiency, real-time data, traceability and cost savings Emerging technologies: IoT and AI in MES
Introduced by Zeiger and Spark Industries at the PTXPO, the nozzle is designed for maximum heat transfer and uniformity with a continuous taper for self cleaning.
Trinseo focuses its Velvex family of factory-colored TPOs with glass reinforcement for interior applications. “With these products, we bridge the gap between technical and aesthetic performance, and we’re doing so at an affordable cost,” says Mazur. These materials boast improved soft touch, outstanding scratch resistance, and low gloss while meeting key requirements of cost-efficiency. These materials reportedly offer a superior finish for unpainted parts such as door panels.
Take a deep dive into all of the various aspects of part quoting to ensure you’ve got all the bases—as in costs—covered before preparing your customer’s quote for services.
In this collection of content, we provide expert advice on welding from some of the leading authorities in the field, with tips on such matters as controls, as well as insights on how to solve common problems in welding.
Solvay’s lightweighting material developments include Amodel PPA and Omnix HPP high-performance nylon with 30-60% long fiber. They are aimed at gears used in EGR (exhaust gas recirculation) and ETC (electronic throttle control), as well as structural parts on the interior panels and consoles and components in chassis systems.
At the K 2016 show in Dusseldorf, Ineos Styrolution, Aurora, Ill., launched what are believed to be the first styrenic thermoplastic composites, with mechanical properties that reportedly exceed composites of nylon 6 or PC. Its StyLight composites are based on a modified SAN with glass or carbon-fiber fabrics for structural and aesthetic/semi-structural applications in interior and exterior panels, seat structures, door modules, center consoles, tail-gates, and parts with a carbon-fiber look. StyLight grades are offered as semifinished goods or thermoplastic sheets, which are ready for processing via thermoforming and overmolding. The company has been in talks with several car makers and, in cooperation with German engineering company KTM Technologies, has developed a selection of concept studies of StyLight in exterior and interior applications like body panels, tailgates, door modules, and consoles.
technotrans says climate protection, energy efficiency and customization will be key discussion topics at PTXPO as it displays its protemp flow 6 ultrasonic eco and the teco cs 90t 9.1 TCUs.
The Plastics Industry Association (PLASTICS) has released final figures for NPE2024: The Plastics Show (May 6-10; Orlando) that officially make it the largest ever NPE in several key metrics.
Solvay Specialty Polymers, Alpharetta, Ga., has focused on three areas for its polymers, according to global automotive business-development manager Brian Baleno: transmissions, where the need is for thermally stable, wear-resistant materials; lightweighting; and electrification of the drivetrain.
AESTHETICS, AERODYNAMICS & STRUCTURAL PROPERTIES Automotive interiors is one key focus for A. Schulman, Inc., Fairlawn, Ohio., says Frank Roederer, senior v.p. & general manager for North America. He and his European counterpart Heinrick Lingnau, point to the growth of touchscreen technologies that demand specialized plastics and the demand for more plastic parts with look and feel of natural materials.
While the major correction in PP prices was finally underway, generally stable pricing was anticipated for the other four commodity resins.
Eliminating the need to contact each supplier for every individual quote, a new CRM for automotive supplier Axiom Group tracks past quotes as well as industry history to generate fast, reliable RFQs and more.
Driven by brand owner demands and new worldwide legislation, the entire supply chain is working toward the shift to circularity, with some evidence the circular economy has already begun.
Of all the trends you can see at NPE2024, this one is BIG. Not only is the auto industry transitioning to electrification but there are concerted efforts to modify the materials used, especially polymers, for interior applications.
As a result of this portfolio divestiture and debt reduction and deleveraging transaction, NN is revising its full-year 2024 outlook modestly as follows:
The Tier One automotive supplier with compounding and blowmolding machine capabilities adds the 50-yr-old molder and moldmaker.
Join KraussMaffei for an insightful webinar designed for industry professionals, engineers and anyone interested in the manufacturing processes of PVC pipes. This session will provide a comprehensive understanding of the technology behind the production of high-quality PVC pipes: from raw material preparation to final product testing. Agenda: Introduction to PVC extrusion: overview of the basic principles of PVC pipe extrusion — including the process of melting and shaping PVC resin into pipe forms Equipment and machinery: detailed explanation of the key equipment involved — such as extruders, dies and cooling systems — and their roles in the extrusion process Process parameters: insight into the critical process parameters like temperature, pressure and cooling rates that influence the quality and consistency of the final PVC pipes Energy efficiency: examination of ways to save material and energy use when extruding PVC pipe products
Jeffrey Helms, global automotive OEM corporate accounts director at Celanese Engineered Materials, Irving, Texas, exemplifies others’ responses in noting that vehicle fuel economy and CO2 emission targets are the two biggest drivers and challenges in the global auto- motive market. Driving materials developments are hotter under-hood temperatures associated with downsized and turbocharged internal combustion engines, and an increase in electrification with a corresponding need to reduce vehicle mass to increase vehicle range. “Each of these is driving the need for material advances in thermoplastics. Cost-effective metal replacement for component and vehicle structures are creating increases in demand for thermoplastic composites and engineering thermoplastics along with processing methods to enable large-scale production capability. Higher underhood temperatures are driving highly engineered plastics to provide the durability that consumers demand.”
After successfully introducing a combined conference for moldmakers and injection molders in 2022, Plastics Technology and MoldMaking Technology are once again joining forces for a tooling/molding two-for-one.
While prices moved up for three of the five commodity resins, there was potential for a flat trajectory for the rest of the third quarter.
“A key element of NN’s transformation and leadership plan is to progressively correct our balance sheet back to market norms. We will pay down debt with the net proceeds from this transaction and continue to advance our balance sheet initiatives. We have a tremendous amount of opportunities in front of us and are excited to implement them. We will continue to focus and refine our business plans in our chosen markets of auto, electrical, industrial and medical,” said Bevis.
Mold maintenance is critical, and with this collection of content we’ve bundled some of the very best advice we’ve published on repairing, maintaining, evaluating and even hanging molds on injection molding machines.
For underhood parts such as radiator air fans, the leading producer of styrene-maleic anhydride (SMA) copolymers. The Netherlands’ Polyscope (U.S. office in Novi, Mich.), is developing highly glass-filled SMA/nylon blends to address water-absorption issues of nylons and replace over-engineered nylons, according to CEO Patrick Muezers.
Ultradent's entry of its Umbrella cheek retractor took home the awards for Technical Sophistication and Achievement in Economics and Efficiency at PTXPO.
Core Technology Molding turned to Mold-Masters E-Multi auxiliary injection unit to help it win a job and dramatically change its process.
NN, Inc., a global diversified industrial company, combines advanced engineering and production capabilities with in-depth materials science expertise to design and manufacture high-precision components and assemblies for a variety of markets on a global basis. Headquartered in Charlotte, North Carolina, NN has facilities in North America, Europe, South America, and Asia. For more information about the company and its products, please visit www.nninc.com.
Say “manufacturing automation” and thoughts immediately go to the shop floor and specialized production equipment, robotics and material handling systems. But there is another realm of possible automation — the front office.
While the melting process does not provide perfect mixing, this study shows that mixing is indeed initiated during melting.
Minnichelli also heralds the use of a 20% carbon-fiber reinforced Ultramid nylon 66 to produce the grille-opening reinforcement (GOR) on the 2016 Ford Shelby GT359 Mustang. Not only 2.5 lb lighter than the traditional GOR of metal stampings overmolded with plastic, but the new part’s aesthetic quality prompted Ford to forgo the “beauty cover” to hide the GOR, saving another 1.9 lb for a 45% weight reduction overall.
Learn about sustainable scrap reprocessing—this resource offers a deep dive into everything from granulator types and options, to service tips, videos and technical articles.
CHARLOTTE, N.C., July 02, 2024 (GLOBE NEWSWIRE) -- NN, Inc. (NASDAQ: NNBR), a global diversified industrial company that engineers and manufactures high-precision components and assemblies, today announced it has entered into a definitive agreement to sell its lone plastics products plant known as Industrial Molding Corporation (IMC), to Davalor Mold Company, a wholly owned portfolio company of Blackford Capital. Total net cash proceeds will be approximately $16 million.
SABIC sees demand for Stamax long-glass PP (LGF-PP) to replace metal in structural applications like front-end modules, door modules, inner tailgate components, and instrument panels. Up to 50% in weight savings are possible, with high stiffness and dimensional stability. Stamax LGF-PP has allowed an Asian auto- maker to shave 30% in weight from the inner tailgate of a recently launched car. “Lightweight tailgate construction is an area of focus for us. SABIC is engaged in multiple projects on all-plastic tailgate designs and we have a full portfolio of solutions for all tailgate components—from the inner structure and outer skin panel to the window. Building on the validated uses of thermoplastics in tailgate components and in glazing, an all-plastic tailgate with a PC-based backlite presents significant opportunity for the industry. A car maker can save up to 30% or 12.5 kg (27.5 lb), depending on the size and design of the entire tailgate,” says Fallon.
In this collection of articles, two of the industry’s foremost authorities on screw design — Jim Frankand and Mark Spalding — offer their sage advice on screw design...what works, what doesn’t, and what to look for when things start going wrong.
Despite price increase nominations going into second quarter, it appeared there was potential for generally flat pricing with the exception of a major downward correction for PP.
Lanxess has responded to these needs with Durethan XTS series, its latest generation of high-heat-resistant nylon 6 grades, as well as the Durethan HR line of high-temperature hydrolysis-resistant nylon 66 for cooling systems. Chirino sees further opportunities for high-tech plastics in battery systems (housing/carrier, cell holder, battery management systems, connectors), engines (bracket, rotor, connectors, cooling circuit), and power electric (housing, power electronics, and connectors). He adds that newer designs for oil-pan modules are rejecting nylon 66 in favor of equally robust but economical nylon 6. The latest example is the module for the new six-cylinder Boxter engines of the Porsche 911 Carrera, which is made with Durethan BKV 30 H2.0.
LANXESS Corporation, Pittsburgh, sees OEMs targeting improvements in the powertrain, aerodynamics, and overall weight to meet global fuel-efficiency regulations. With the introduction of more small, turbo-charged engines and exhaust-recovery systems, the demand is for materials that can withstand higher engine operating temperatures in a smaller space. Cooling systems also are operating at high temperatures, explains, Jose Chirino, Americas technical director at Lanxess’ high-performance materials business unit. Adds BASF’s Chiandussi, “We predict that about 20% of all turbocharger applications will require a high-heat- resistant plastic as engine temperatures increase.”
Resin drying is a crucial, but often-misunderstood area. This collection includes details on why and what you need to dry, how to specify a dryer, and best practices.
Formnext Chicago is an industrial additive manufacturing expo taking place April 8-10, 2025 at McCormick Place in Chicago, Illinois. Formnext Chicago is the second in a series of Formnext events in the U.S. being produced by Mesago Messe Frankfurt, AMT – The Association For Manufacturing Technology, and Gardner Business Media (our publisher).
Trinseo has also developed lower-density Pulse PC/ABS products that not only enable less weight and cost in parts, but also offer low gloss, easy flow, faster cycles, high impact strength at low temperatures, heat resistance optimized for the majority of interior auto components, and low odor and VOCs. For example, Pulse GX50 is approved by BMW for UV and hydrolytic stability and is used on the BMW 1 series, i3 and i8.
Lingnau also notes the higher-quality appearance trend in exteriors, where Schulman’s fully compounded compounds are replacing painted parts in metallic colors. The company provides silver metallic compounds by using special pigments and mineral fillers to achieve metallic optics without weld lines and injection marks. This earned the company the 2016 Grand Innovation Award of SPE Europe for the Mercedes Benz GLA skid plate for front and rear bumpers, produced with Polyfort FIPP 10 T K2369, a silver-metallic, impact-modified PP compound using an innovative filler system.
The aim of this presentation is to guide you through the factors and the numbers that will help you determine if a robot is a smart investment for your application. Agenda: Why are you considering automation? What problems are you trying to solve? How and why automation can help Crunch the numbers and determine the ROI
Mike Sepe has authored more than 25 ANTEC papers and more than 250 articles illustrating the importance of this interdisciplanary approach. In this collection, we present some of his best work during the years he has been contributing for Plastics Technology Magazine.
Higher temperatures and more demanding wear requirements for transmissions are fueling the need for heat-stable and more wear-resistant materials including Torlon PAI and KetaSpire PEEK, says Solvay’s Baleno. Three key applications in transmissions that demand high- temperature and wear resistance are seal rings, thrust washers, and thrust bearings. Thrust bearings of PAI and PEEK now used to replace axial needle bearings can save 2.5 mm/0.098 in. per bearing. This spatial savings enables designers to downsize aluminum housings and achieve significant weight savings.
In the area of aerodynamics, active grill shutters play a role in increasing fuel efficiency by as much as 1.1 mpg, but weight and warpage can be an issue. To address this, Lanxess’ new Durethan XF (Xtreme Flow) easy-flowing nylon 6 is being evaluated for reduced warpage and improved cycle times.
Join this webinar to explore the transformative benefits of retrofitting your existing injection molding machines (IMMs). Engel will guide you through upgrading your equipment to enhance monitoring, control and adaptability — all while integrating digital technologies. You'll learn about the latest trends in IMM retrofitting (including Euromap interfaces and plasticizing retrofits) and discover how to future-proof your machines for a competitive edge. With insights from industry experts, it'll walk you through the decision-making process, ensuring you make informed choices that drive your business forward. Agenda: Maximize the value of your current IMMs through strategic retrofitting Learn how to integrate digital technologies to enhance monitoring and control Explore the benefits of Euromap interfaces and plasticizing retrofits Understand how retrofitting can help meet new product demands and improve adaptability Discover how Engel can support your retrofitting needs, from free consultations to execution
Houston-based SABIC sees PP making its way into underhood applications. Scott Fallon, global leader of SABIC’s automotive business, points to the 2016 SPE Automotive Innovation Award powertrain winner: the air-intake manifold in VW’s 2015 EA21 1.6L engines, said to be the first such part launched in China using 35% glass-reinforced PP to replace nylon 66. The part provides a 25-30% cost reduction and 15-20% weight reduction while retaining properties and improving weld strength. SABIC’s G3135X PP in this part utilizes finer glass fibers and special sizing.
Discover how artifical intelligence is revolutionizing plastics processing. Hear from industry experts on the future impact of AI on your operations and envision a fully interconnected plant.
In this collection, which is part one of a series representing some of John’s finest work, we present you with five articles that we think you will refer to time and again as you look to solve problems, cut cycle times and improve the quality of the parts you mold.
Lightweighting and resistance to heat, chemicals and weathering drive developments in thermoplastics for interiors, exteriors, underhood, powertrain and chassis.
Additive technology creates air pockets in film during orientation, cutting down on the amount of resin needed while boosting opacity, mechanical properties and recyclability.
The firm’s high-flow, low-emissions Schulablend M/MK ABS/ nylon and M/MW ASA/nylon and other alloys offer the potential to eliminate painting and achieve a consistent low-gloss/matte finish. Available in UV-stabilized custom colors and low gloss, they are found in trim such as loudspeaker grilles, pillar covers, instrument panels (masks, end caps, HVAC bezels), trunk and window frames, seat side shields and AV system bezels.
Successfully starting or restarting an injection molding machine is less about ticking boxes on a rote checklist and more about individually assessing each processing scenario and its unique variables.
Celanese’s CoolPoly thermally conductive plastics, which comes in electrically conductive and insulative grades, have taken hold in automotive heat sinks by matching thermal properties of aluminum while offering weight and cost savings. These plastics enable 40-55% mass savings due to reduced density and design optimization. A commercial use is in the Ford Mondeo lighting module, where replacing die cast aluminum saved 54% in weight. CoolPoly is also being evaluated for metal replacement in power electronics and lighting.
We asked key materials suppliers (not all of whom responded) that have been among the leaders in the development of automotive applications to weigh in on what they see as the areas of an automobile experiencing the most dramatic developments in thermoplastic materials offerings.
Trinseo’s Majur notes that his company has worked with long-standing partner Renault to convert semi-structural parts to LGF-PP. With the fourth generation of the Renault Clio, launched in 2012, Renault reached its target of reducing the lift-gate weight by about 15%, and the effort continues. Front-end modules and air-flow systems, door modules, IPs, center consoles, under-vehicle belly pans, and seat structures are other potential opportunities. Majur adds that LGF concentrates enable improved-cost efficiency and improved manufacturing flexibility vs. fully formulated LGF grades by allowing addition in varying amounts to unfilled PP at the injection molding machine.
Mixed in among thought leaders from leading suppliers to injection molders and mold makers at the 2023 Molding and MoldMaking conferences will be molders and toolmakers themselves.
Mark Minnichelli, director of technical development at BASF’s performance materials division, points to Ford’s new Lincoln Continental, which features an innovative seating architecture. With its 35% glass-filled, impact resistant Ultramid nylon 6, BASF contributed a 20% weight reduction for the front-row seat pan vs. the metal predecessor, and 15% cost savings.
Two new powertrain applications, which debuted on the 2017 Alfa Romeo Giulia’s 2.0L GME engine, utilize BASF’s high-heat nylon: The air-intake manifold with integrated charge-air cooler is made with Ultramid Endure D3G7, a 35% glass-filled nylon 66 that is replacing less thermally stable versions of nylons 6 and 66. And the hot-side turbo duct is made with Ultramid Endure D5G3 BM, a 15% glass-filled nylon 66 that is replacing metals in turbo ducts.
Jerry Mazur, new business development manager for automotive at Trinseo, Berwin, Pa., views semi-structural applications as the most dramatic development. “Lighter, safer and environmentally sustainable vehicles are a priority, and cost savings is a primary target for manufacturers. It’s in this space that innovative materials and their applications are replacing previous technologies.”
Summarizing recent innovations in thermoplastics for automotive is no small task. Virtually everything that meets one’s eye in a vehicle’s interior is thermoplastic these days, and the same goes for a look under the hood and a good deal of what is visible on the exterior—not to mention innumerable plastic components that don’t meet the eye in powertrain, chassis, and elsewhere. And while much of the conversation about automotive plastics dwells on lightweighting for fuel efficiency, there are many other performance requirements that drive materials developments, such as resistance to fuels and chemicals, heat, wear, sunlight, and weather. In other cases, the goal is improved process- ability to enhance quality and reduce manufacturing cost.
PlastiComp, Inc., Winona, Minn., is targeting structural parts for its long-carbon-fiber (LCF) thermoplastic compounds and its unique hybrids of LGF and LCF in a unified pellet—currently available in nylon 66, PP, and TPU—says business-development manager Steve Ouendag. The company is working with several Tier 1 suppliers on metal replacement in underhood and powertrain assemblies with LCF-PP and nylon. Weight savings as high as 50% can be achieved when replacing aluminum or cast metals.
LIGHTWEIGHTING ALL AROUND Lanxess’ Chirino says these XF grades are also gaining applications in structural parts such as front ends, lightweight cross-car beams, rear bumpers, and door modules—thanks to the high-modulus/high-flow materials like Durethan BKV 60 XF, a 60% glass-filled nylon 6 that facilitates complex, thinwall, lightweight applications that replace metal with weight reductions up to 50%.
Coverage of single-use plastics can be both misleading and demoralizing. Here are 10 tips for changing the perception of the plastics industry at your company and in your community.
In a time where sustainability is no longer just a buzzword, the food and beverage packaging industry is required to be at the forefront of this innovation. By adopting circular packaging processes and solutions, producers can meet regulatory requirements while also satisfying consumer demand and enhancing brand reputation. Join Husky to learn more about the broader implications of the circular economy — as well as how leading brands are leveraging this opportunity to reduce costs, increase design flexibility and boost product differentiation. Agenda: The cost and operational benefits of embracing circularity Key materials in circular packaging — including rPET and emerging bioplastics How to design a circular food and beverage package Strategies for selecting sustainable closures to future-proof packaging solutions Optimization and streamlining of production processes for enhanced efficiency How Husky Technologies can enable your sustainable success
With advocacy, communication and sustainability as three main pillars, Seaholm leads a trade association to NPE that ‘is more active today than we have ever been.’
NN is committed to creating a sustainable and profitable growth business model by participating in large growing markets; partnering with innovative customers on innovative programs; and providing unique value through a global footprint of plants delivering high quality and on-time performance. NN is also strengthening its core values around climate leadership, diversity, and inclusion.
Across the show, sustainability ruled in new materials technology, from polyolefins and engineering resins to biobased materials.
HEAT, CHEMICAL & WEAR RESISTANCE As underhood temperatures rise, suppliers are offering more heat- resistant products, often with an added lightweight advantage. The new Fortron flexible PPS by Celanese has enabled significant weight reductions in underhood applications while resisting extreme temperatures (>75% tensile strength retention after 1000 hr at 175 C/347 F). Helms notes that because nylon absorbs moisture and undergoes variable performance in rising temperatures, parts manufacturers and OEMs will look to PPS due to its chemical resistance and long-term high-temperature performance stability under the hood and in applications such as EDS (electrical distribution system) fasteners. China’s Chinaust utilized Flexible Fortron PPS to blow mold and thermoform a positive crankcase ventilation (PCV) tube that is now in production on three GM car platforms. The material reduced part count by 50%, saved over $3/car per car, and consolidated a metal-and-plastic assembly into one plastic unit.
Gifted with extraordinary technical know how and an authoritative yet plain English writing style, in this collection of articles Fattori offers his insights on a variety of molding-related topics that are bound to make your days on the production floor go a little bit better.
Exhibitors and presenters at the plastics show emphasized 3D printing as a complement and aid to more traditional production processes.
Meanwhile, car makers are striving to make premium inte- riors affordable, says Trinseo’s Mazur. They want surfaces to have a high-quality look and feel, to be durable and less expensive to manufacture in order to pass savings on to customers. This is why the OEMs have stringent requirements for plastics with aesthetics and haptics and best-in-class scratch resistance, along with good processability and cost-effectiveness.
Second quarter started with price hikes in PE and the four volume engineering resins, but relatively stable pricing was largely expected by the quarter’s end.
Plastics Technology covers technical and business Information for Plastics Processors in Injection Molding, Extrusion, Blow Molding, Plastic Additives, Compounding, Plastic Materials, and Resin Pricing. About Us
GETTING A QUOTE WITH LK-MOULD IS FREE AND SIMPLE.
FIND MORE OF OUR SERVICES:
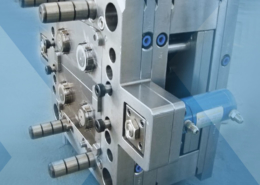
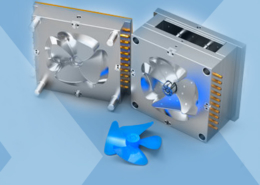
Plastic Molding

Rapid Prototyping
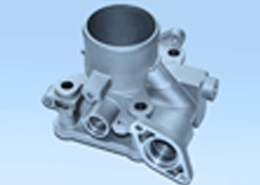
Pressure Die Casting
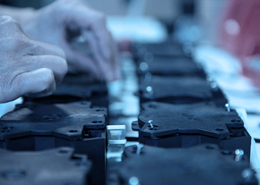
Parts Assembly
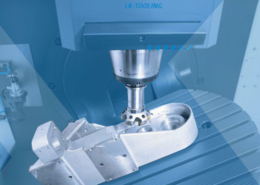