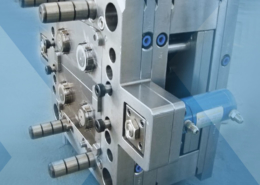
Plastic Injection Molding Market Size is expected to reach - all american inject
Author:gly Date: 2024-09-30
Suppliers have lost some of the spread built up between ethylene and HDPE in 2016, but it remains well above what it was at the end of 2015, and it has been stable to slightly higher in 2017, with some grades such as HDPE pipe, gaining a little more ground than other HDPE grades.
Weight reduction is one of the most effective methods for reducing CO2 emissions. Researchers at Fraunhofer ICT in Pfinztal are supporting the automotive industry in its efforts with a newly developed camshaft module made of thermosetting composite materials. This lightweight camshaft module was realized in cooperation with the MAHLE Group and associated partners Daimler AG, SBHPP/Vyncolit NV and Georges Pernoud.
“The camshaft module is located in the cylinder head, so normally in the upper installation space of the powertrain. Here, it makes particular sense to reduce weight, since doing so also contributes to lowering the vehicle’s center of gravity.”
Buyers have built up stock, as they feared potential shortages because of a series of planned cracker maintenance outages. No production issues have occurred to interfere with HDPE supply, however, and by the end of the first quarter, they were using up stock. Lower prices have been offered for spot imported volumes, while contracted prices have remained relatively firm.
New supply is coming on stream in North America, and while delays mean that growth will have some time to catch up with supply, an impact from new capacities is expected by the end of 2017/beginning 2018, according to sources.
With supply and demand upstream returning to balance once planned cracker outages are over, HDPE output will also get back to normal. European HDPE buyers expect new production to be available to them as early as the third quarter 2017, but that product will only be available in volumes sufficient to affect the market materially by the end of 2017, beginning 2018.
First-quarter spot prices have not been buoyant in the blowmoulding and injection sectors, however. Film prices have held up better, in line with spot prices in associated polyethylene (PE) film markets.
High-density polyethylene (HDPE) is used extensively in blow-moulded products such as milk bottles, packaging containers, drums, car fuel tanks, toys and household goods. Film and sheet are widely used in wrapping, refuse sacks, carrier bags and industrial liners. Injection-moulded products include crates, pallets, packaging containers, housewares and toys. Extrusion grades are used in pipes and conduit.
Further, at up to 500,000 molding cycles, the service life of a thermoset polymer injection mold is significantly higher than that of aluminum high-pressure die cast molds. Furthermore, plastics reinforced with a high fiber content have a much lower CO2 footprint compared with aluminum, since this light metal is very energy-intensive to manufacture.
And there is another advantage: automotive manufacturers are eager to minimize noise emissions. Rattling cars are not only annoying, they are also a clear competitive disadvantage, so noise, vibration and harshness (NVH) characteristics are high up on the list of factors used to assess vehicle quality. Polymers have good damping characteristics. “This makes it very easy to optimize the acoustic performance of the camshaft module,” says Sorg.
European HDPE producers have managed to keep hold of much of the margin they gained in 2015. Fear of more supply disruption saw 2016 contract prices rise, and again 2017 contracts were tougher for many buyers as weak prices in Europe left imported volumes low.
Stephen has been with PlasticsToday and its preceding publications Modern Plastics and Injection Molding since 1992, throughout this time based in the Asia Pacific region, including stints in Japan, Australia, and his current location Singapore. His current beat focuses on automotive. Stephen is an avid folding bicycle rider, often taking his bike on overseas business trips, and is a proud dachshund owner.
The camshaft module features a monolithic design with integrated bearings — in other words, it is manufactured in one piece, thus reducing assembly time in the engine manufacturing plant. Car manufacturers receive a pre-assembled module from their supplier and can mount it on the engine with just a few simple mounting operations. This eliminates the need for separate, time-consuming installation of the camshaft. This innovative solution boasts an additional advantage: aluminum inserts in highly stressed areas of the camshaft bearings absorb the direct forces.
The supply/demand balance in the European HDPE sector has changed significantly in the past three years, following some definitive planned closures that took place between the end of 2012 and 2015. Closures were made as profitability has been poor in this sector, and producers reacted to the increase of low-cost imports by closing older non-competitive plants.
Meanwhile, much depends on how Asian markets fare. Low prices in Europe have deterred importers, but falling levels in Asia, coupled with firm contracted pricing in Europe – and new capacity coming on stream – is leading to expectations of more imports into Europe, even before the onslaught of the new North American shale-based material.
The unusual situation of 2015 continues to have an impact in HDPE pricing and buying activity. An unprecedented series of force majeures in 2015 meant converters did not have enough product to continue keep all lines running. Apocryphal stories told of empty bottles being airlifted into European sites, and prices soared. The events of 2015 led to many converters changing their buying methods. Security of supply became more important than pricing, and imports have become an integral part of HDPE supply in Europe.
Spot upstream ethylene is still strong, and some HDPE output has been reduced for the lack of ethylene, but when the cracker outages end, a normal balance is expected to return to the market.
The German Federal Ministry for Economic Affairs and Energy (BMWi) has been funding the project. When it comes to the choice of the right polymer, the project partners opted for high strength, fiber-reinforced thermoset polymers, as they are able to withstand high temperatures and mechanical and chemical stresses such as those caused by synthetic motor oils and coolants, for instance. “We contribute the know-how regarding how to design the component geometries to suit the material and the process so that they satisfy all requirements,” says Thomas Sorg, a researcher at Fraunhofer ICT.
Camshafts ensure that the charge-cycle valves in internal combustion engines are opened and closed reliably and precisely. These valves are located in the camshaft module, the standard material for which is still aluminum metal. But automotive manufacturers and suppliers are putting great effort into producing powertrains and their components in lightweight design.
Although the stiffness of the thermoset polymer is only a quarter of that of aluminum, design measures enabled the research team to adhere to the maximum allowable deformation. After 600 hours of testing on the engine test stand, the lightweight design element demonstrated flawless functionality in a state-of-the-art internal combustion engine. With the aid of the planned fuel injection tests, the project partners now want to prove the functionality and the NVH characteristics taking the gas forces of the combustion process into account.
By April 2017, more imports were being offered from Asia and Mexico among others, as Asian prices faltered and European contracted levels rose. Demand in Europe is said to be running at a modest increase over 2016.
Camshaft modules, which are a key component of powertrains, are still being made from aluminum. Now a research team from the Fraunhofer Institute for Chemical Technology ICT, in collaboration with their partners, has succeeded in manufacturing a camshaft module from fiber-reinforced thermoset polymers using the injection molding process. This lightweight design element helps lower engine weight and reduces assembly costs. It is currently available as a functional demonstrator.
Castings made from aluminum require extensive reworking after casting, resulting in high costs. In contrast, fiber-reinforced thermoset polymers allows a near-net-shape manufacturing, thus requiring comparatively little reworking and which again leads to reduced production cost.
An increase in import duties from the major importing region of the Gulf Cooperation Council on 1 January 2014, from 3% to 6.5%, combined with a later crash in crude oil prices and also a crash in the value of the euro against the dollar, meant that some European HDPE buyers were unable to get hold of all the HDPE they needed from local sources. Europe subsequently became a net importer of some HDPE grades.
GETTING A QUOTE WITH LK-MOULD IS FREE AND SIMPLE.
FIND MORE OF OUR SERVICES:
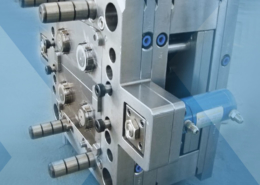
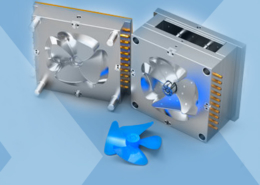
Plastic Molding

Rapid Prototyping
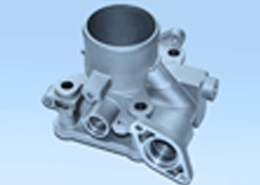
Pressure Die Casting
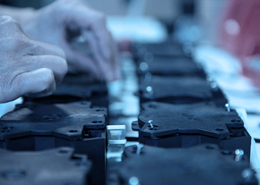
Parts Assembly
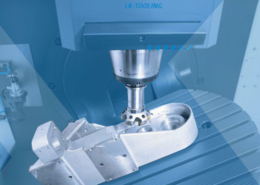