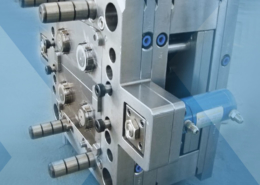
Plastic Injection Molding Market Size is expected to reach - billion injection m
Author:gly Date: 2024-09-30
To assist with seamless production, both IntElect machines are integrated with a Cartesian robot and conveyor to carefully handle the final products.
The goal, it would seem from reading this latest patent, is to produce a high-cavity mold that will cost a fraction of a conventional steel mold with cooling channels. The low-temperature, low constant pressure molding process will allow these soft molds "to extract useful lives of more than 1 million cycles, preferably between 1.25 and 10 million cycles, and more preferably between 2 million cycles and 5 million cycles," notes the patent.
Consumer products giant Procter & Gamble Co. appears to be getting into the moldmaking and injection molding business through its wholly owned subsidiary, iMflux, which is establishing a manufacturing facility in West Chester, OH, and has begun advertising for employees that will eventually number 221 over the next three years.
Part of the Swiss-owned forteq global technology group, the Huddersfield factory has a sustained history of responding to the latest trends in precision engineering and setting a high bar for technical innovation.
Additionally, the use of the soft tooling means that the mold will have "no active cooling system," but be "passively cooled through the conduction of heat through the mold sides and support plates, . . ." That will reduce the cycle times significantly.
Managing Director of forteq UK Paul Wallis said: “forteq UK is striving to realign its business in line with group strategy to ensure we maintain and grow our automotive business content during the market transition to hybrid and full electric vehicles. We are investing in equipment and processes which support this, while at the same time improving our sustainability and environmental impact yet further. In the domestic market we aim to support re-shoring programs, also offering capacity in larger machines which enables more local supply of bigger components. Our other niche products comprise 2k components, precise gears and over-moulded parts, all linked to high precision products.”
PlasticsToday promises to stay on top of this development and bring you the latest in this OEMs foray into moldmaking and molding.
Until she retired in September 2021, Clare Goldsberry reported on the plastics industry for more than 30 years. In addition to the 10,000+ articles she has written, by her own estimation, she is the author of several books, including The Business of Injection Molding: How to succeed as a custom molder and Purchasing Injection Molds: A buyers guide. Goldsberry is a member of the Plastics Pioneers Association. She reflected on her long career in "Time to Say Good-Bye."
This latest patent concerns what iMflux calls a "high productivity injection molding method" including the mold and the molding press that is capable of producing more than 1 million injection molding cycles through the use of soft (aluminum of various grades, beryllium, copper, zinc, among many others) tooling that provides a high level of thermal conductivity so that cooling channels are not required. The molding process will be done through a low-temperature, low constant pressure method that will remove the variability of pressures and temperatures from the molding process.
“The transformation to EV is shifting demands on suppliers. We have already observed uplifts in enquires from automotive customers and are undertaking projects ranging from gears and actuators to vehicle sensors and end caps for battery modules. As legacy parts from combustion engine vehicles start to ebb, new components, many of which can be made from polymer to increase efficiency through light-weighting, will emerge.”
It's not clear whether iMflux will be making its own molds and perhaps doing its own molding at the facility or licensing the technology to its mold and molded parts suppliers to help P&G reduce its costs in those arenas.
Roberts concluded: “We manufacturer a large number of components where the flatness tolerances are very tight. The use of robotics integrated into the injection moulding cells enables us to meet stringent cleanliness requirements, as well as removing the parts at speed and lay them flat on a conveyor to cool. This helps us to maintain our global reputation for quality, as well as reducing scrap rates.
While P&G isn't commenting on all of this, numerous articles in local Cincinnati newspapers and business journals have commented on this development, noting that the company recently received Ohio tax credits of up to $2.6 million for the establishment of the plant located just north of Cincinnati.
Serving predominantly tier 1 automotive customers, supplying electric vehicle components is now one of the company’s key strategic business lines. This complements their reputation in air suspension, actuator gears, engine timing systems and fuel filtration systems. Refreshing their portfolio of machines with the addition of two IntElect 100 tonne machines underpins forteq UK’s strategic roadmap to optimising processing efficiency and supporting domestic manufacturing in the electric vehicle (EV) market. Overall investments are valued at close to £2m.
For over six decades, the company, formerly known as Mikron, has built a reputation as a manufacturer of high-quality moulded parts. Its product portfolio ranges from precision automotive components and utility meters, to precision automotive gears and transmission systems. The highly automated UK facility has secured a number of new blue-chip contracts to supply electric vehicle (EV) components.
The addition of two IntElect 100 ton machines underpins forteq UK’s strategic roadmap to optimising processing efficiency.
The IntElect’s generous tie bar spacing and mould height means the machine can accommodate automation to assist with insertion and the removal of parts in a wide range of applications, including safety components with special aesthetics that need to be protected from dents and scratches while the high grade polymers cool and harden.
forteq purchased the all-electric machines to enhance moulding precision and stability. For that reason, forteq UK has assigned its second IntElect to manufacture worm wheel gears used in vehicle power steering applications, as well as a wide range of components deployed in wiper systems, door latches, window regulators, geared actuators, seating systems, HVAC and fluid delivery applications.
Using this low-temperature, low constant pressure molding method will also allow the use of bio-based materials. Another patent published on Nov. 22, 2012, "Method for Injection Molding at Low, Substantially Constant Pressure," details this method that is "more energy - and cost - effective than conventional high-velocity injection molding processes." This method allows "for the filling of a mold cavity at low melt pressure without undesirable premature hardening of the thermoplastic material in the mold cavity and without the need for maintaining a constant temperature of heated mold cavity."
The new contract, which commenced officially in Q4 2021, involves producing three very technical components on four cavity mould tools. When assembled, the components form a complex mechatronic valve featuring tight flatness and roundness characteristics, along with a threaded seal carrier, clips and living hinge to minimise parts list and cost.
A patent was issued on August 29, 2013, detailing iMflux's mold/molding process that the company says could save P&G $1 billion annually. This patent, "Method for Operating a High Productivity Injection Molding Machine," is just one of nearly a dozen patents obtained by Gene Michael Altonen and various colleagues. Altonen currently serves at iMflux's VP of R&D and has been granted 40 patents with 25 patents pending in the field of injection molding.
Processing high performance polymers, machine exactitude forms a critical part of this application’s success. Business development manager Steve Roberts added: “Each element alone is complex with demanding flatness tolerances of +/- 50 microns where nearby features can cause distortion. This level of dimensional accuracy requires the most exact injection moulding precision to achieve the required quality and repeatability.”
The IntElect’s direct drive technology is designed purely for injection moulding. This means it delivers the accelerated injection speeds needed for accurate dosing and injection performance, prerequisites for tight tolerance applications like this gas meter valve.
With the reshoring of technical moulding of components continuing to gain momentum, West Yorkshire-based forteq UK has increased its production capacity by investing in two high-precision IntElect 100 tonne machines from Sumitomo (SHI) Demag.
Consumer products giant Procter & Gamble Co. appears to be getting into the moldmaking and injection molding business through its wholly owned subsidiary, iMflux, which is establishing a manufacturing facility in West Chester, OH, and has begun advertising for employees that will eventually number 221 over the next three years.
Describing the complexity of the worm wheel project, Roberts continued: “It involves the over-moulding of precision machined steel hubs. These are placed into the mould tool on a precision made collapsing collett to maintain centralisation of the gear. The gear ring itself that forms the helix plastic teeth is highly complex and engineered at our gear competence centre in Switzerland.”
One of the new Sumitomo (SHI) Demag machines has been allocated specifically to manufacture 400,000 complex sets of gas meter precision components per annum.
GETTING A QUOTE WITH LK-MOULD IS FREE AND SIMPLE.
FIND MORE OF OUR SERVICES:
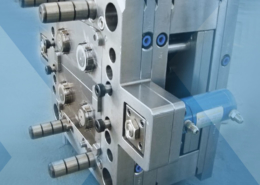
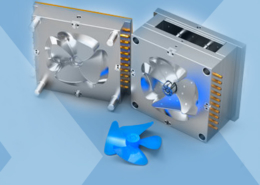
Plastic Molding

Rapid Prototyping
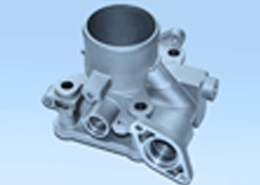
Pressure Die Casting
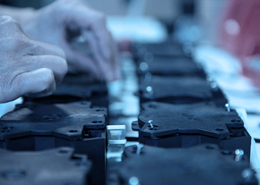
Parts Assembly
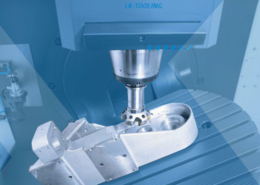