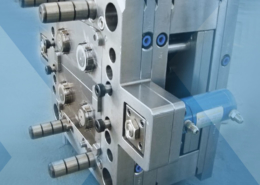
Unveiling the Potential of LDPE Injection Molding
Author:gly Date: 2024-06-08
LDPE injection molding heralds a new era of versatility and efficiency in plastic manufacturing. With its unique properties and widespread applications, LDPE (Low-Density Polyethylene) stands as a cornerstone of modern industry. In this article, we embark on a journey to explore the intricacies of LDPE injection molding, uncovering its transformative impact and untapped potential.
Unlocking the Power of LDPE
An Introduction to LDPE
At the forefront of polymer innovation lies LDPE, a thermoplastic known for its low density, flexibility, and chemical resistance. Originally developed in the 1930s, LDPE has since become ubiquitous in various industries, ranging from packaging to automotive.
The Injection Molding Advantage
Injection molding emerges as the preferred method for processing LDPE, offering unparalleled precision, efficiency, and cost-effectiveness. By melting LDPE pellets and injecting the molten material into molds under high pressure, manufacturers can produce complex geometries with remarkable consistency and speed.
Advancements in Material Science
Recent advancements in material science have further expanded the capabilities of LDPE injection molding. Through additives and reinforcements, LDPE can be tailored to meet specific performance requirements, enhancing properties such as strength, durability, and UV resistance.
Applications Across Industries
Packaging Solutions
In the realm of packaging, LDPE injection molding reigns supreme. From bottles and containers to film and sheeting, LDPE offers unparalleled versatility and cost-effectiveness, making it the material of choice for a wide range of packaging applications.
Automotive Components
The automotive industry also benefits greatly from LDPE injection molding. From interior trim components to under-the-hood parts, LDPE's lightweight nature, impact resistance, and corrosion resistance make it ideal for automotive applications, contributing to improved fuel efficiency and durability.
Medical Devices
In the healthcare sector, LDPE injection molding plays a crucial role in the production of medical devices and equipment. Its biocompatibility, sterilizability, and ease of processing make LDPE a preferred material for applications such as syringes, IV bags, and surgical instruments.
Sustainability and Environmental Considerations
Recyclability and Circular Economy
As the global focus on sustainability intensifies, LDPE injection molding offers a compelling solution. LDPE is highly recyclable, enabling the creation of a closed-loop system that reduces waste and conserves resources. By embracing LDPE injection molding, industries can contribute to a more sustainable future.
Challenges and Opportunities
While LDPE injection molding holds immense promise, challenges remain in terms of material compatibility, process optimization, and waste reduction. Addressing these challenges will require collaboration among industry stakeholders and continued innovation in both technology and materials.
Conclusion: Charting the Course for LDPE Injection Molding
In conclusion, LDPE injection molding stands as a testament to the ingenuity and adaptability of modern manufacturing. By leveraging the unique properties of LDPE and embracing advanced injection molding techniques, industries can achieve unprecedented levels of efficiency, reliability, and sustainability. As we look to the future, it is imperative to seize the opportunities presented by LDPE injection molding while addressing the challenges that lie ahead. Through innovation, collaboration, and a steadfast commitment to excellence, LDPE injection molding will continue to shape the landscape of plastic manufacturing for generations to come.
GETTING A QUOTE WITH LK-MOULD IS FREE AND SIMPLE.
FIND MORE OF OUR SERVICES:
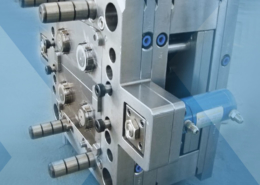
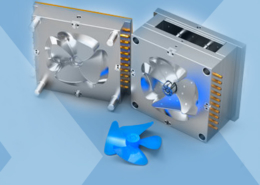
Plastic Molding

Rapid Prototyping
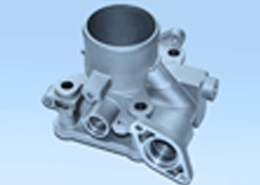
Pressure Die Casting
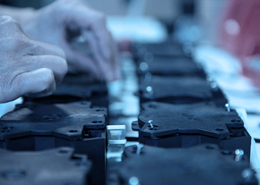
Parts Assembly
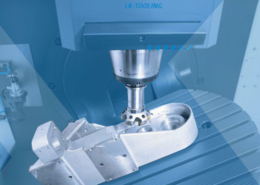