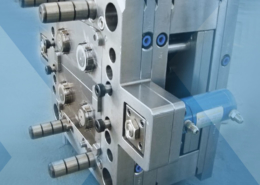
Exploring Low Cost Injection Molding: Revolutionizing Manufacturing
Author:gly Date: 2024-06-08
Introduction
Low cost injection molding stands at the forefront of modern manufacturing, offering innovative solutions to streamline production processes and reduce manufacturing costs. With its revolutionary approach, it has sparked significant interest across industries, reshaping the landscape of production. This article aims to delve into the intricacies of low cost injection molding, providing a comprehensive understanding of its principles, applications, benefits, and challenges.
Principles of Low Cost Injection Molding
Understanding the Basics
Low cost injection molding relies on the fundamental principles of traditional injection molding techniques while integrating cost-effective measures. It involves the injection of molten material into a mold cavity, which then solidifies to form the desired product.
Optimizing Material Usage
One of the key aspects of low cost injection molding is the optimization of material usage. Through innovative design strategies and material selection, manufacturers can minimize material waste, leading to cost savings without compromising quality.
Automation and Efficiency
Automation plays a pivotal role in low cost injection molding, enhancing efficiency and reducing labor costs. Automated systems streamline the production process, from mold design and material handling to injection and quality control, thereby increasing productivity and reducing manufacturing lead times.
Applications Across Industries
Automotive Sector
In the automotive sector, low cost injection molding has revolutionized the production of various components, including interior trims, exterior panels, and engine parts. By leveraging cost-effective molding techniques, automotive manufacturers can achieve significant cost savings while maintaining high product quality.
Consumer Electronics
The consumer electronics industry has also embraced low cost injection molding for the production of housings, enclosures, and other components. With the growing demand for lightweight and durable electronic devices, manufacturers are increasingly turning to cost-effective molding solutions to meet consumer expectations while remaining competitive in the market.
Medical Devices
In the medical device industry, low cost injection molding has enabled the mass production of precision components, such as syringes, IV catheters, and surgical instruments. By optimizing manufacturing processes and reducing production costs, medical device manufacturers can make healthcare more accessible and affordable for patients worldwide.
Benefits and Challenges
Benefits of Low Cost Injection Molding
Cost Savings: By minimizing material waste and optimizing production processes, low cost injection molding offers significant cost savings for manufacturers.
Rapid Prototyping: The versatility of low cost injection molding allows for rapid prototyping and iterative design improvements, accelerating product development cycles.
Customization: With flexible tooling options and design capabilities, manufacturers can easily customize products to meet diverse customer requirements.
Challenges to Overcome
Initial Investment: While low cost injection molding offers long-term cost savings, the initial investment in equipment and automation systems can be substantial, posing a barrier to entry for some manufacturers.
Quality Control: Maintaining consistent product quality can be challenging, especially when using cost-effective materials or implementing automated manufacturing processes. Rigorous quality control measures are essential to ensure compliance with industry standards and regulations.
Conclusion
In conclusion, low cost injection molding represents a paradigm shift in manufacturing, offering a cost-effective solution to produce high-quality products across industries. By leveraging innovative techniques and automation technologies, manufacturers can streamline production processes, reduce manufacturing costs, and stay competitive in today's market. However, overcoming challenges such as initial investment and quality control remains crucial for the widespread adoption of low cost injection molding. Moving forward, continued research and development efforts are needed to further enhance efficiency, quality, and sustainability in injection molding processes.
Through this exploration, it is evident that low cost injection molding holds immense potential to revolutionize the manufacturing landscape, driving innovation, and economic growth in the years to come.
GETTING A QUOTE WITH LK-MOULD IS FREE AND SIMPLE.
FIND MORE OF OUR SERVICES:
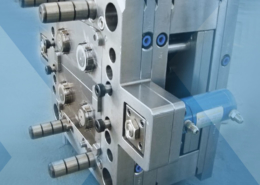
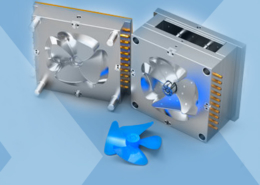
Plastic Molding

Rapid Prototyping
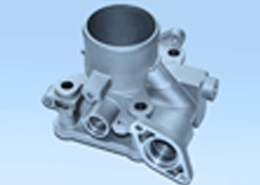
Pressure Die Casting
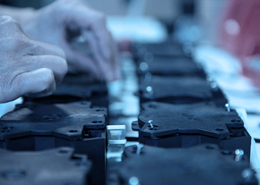
Parts Assembly
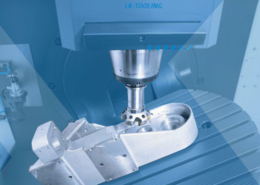