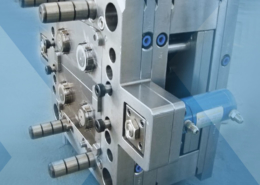
Unraveling the Potential of Large-Scale Injection Moulding
Author:gly Date: 2024-06-08
Large-scale injection moulding stands as a cornerstone of modern manufacturing, facilitating the production of high-volume plastic components with precision and efficiency. In this exploration, we delve into the intricacies of large-scale injection moulding, captivating readers' interest while providing essential background information on this pivotal technique.
Introducing Large-Scale Injection Moulding
Large-scale injection moulding represents a sophisticated manufacturing process used to produce vast quantities of plastic components with consistent quality and high precision. It involves injecting molten thermoplastic material into a mould cavity under high pressure, where it cools and solidifies to form the desired shape.
The allure of large-scale injection moulding lies in its ability to meet the demands of mass production, catering to diverse industries such as automotive, consumer goods, electronics, and packaging. By leveraging advanced machinery, automation, and process optimization techniques, manufacturers can achieve economies of scale and drive down production costs while maintaining stringent quality standards.
Advantages of Large-Scale Injection Moulding
Large-scale injection moulding offers a myriad of advantages over traditional manufacturing methods, making it an indispensable tool for high-volume production. Firstly, it enables the rapid and cost-effective production of complex geometries and intricate designs, allowing manufacturers to meet evolving market demands and consumer preferences.
Moreover, large-scale injection moulding delivers superior part consistency, dimensional accuracy, and surface finish compared to other manufacturing processes, ensuring uniformity and reliability across production batches. Additionally, it supports the integration of value-added features such as inserts, overmoulding, and multi-component assemblies, expanding design possibilities and functionality.
Process and Equipment
The process of large-scale injection moulding comprises several key stages, including material preparation, injection, cooling, ejection, and quality control. Manufacturers utilize state-of-the-art injection moulding machines equipped with robust hydraulic or electric systems, precise controls, and automation capabilities to optimize production efficiency and quality.
Furthermore, advanced mould designs and tooling technologies play a crucial role in large-scale injection moulding, influencing part quality, cycle time, and production scalability. Manufacturers invest in high-performance moulds made from durable materials such as steel or aluminium, equipped with features such as cooling channels, hot runners, and cavity inserts to enhance productivity and consistency.
Applications Across Industries
Large-scale injection moulding finds extensive applications across diverse industries, ranging from automotive and aerospace to healthcare and consumer goods. In the automotive sector, it is used for manufacturing interior and exterior components, under-the-hood parts, and safety systems, contributing to lightweighting initiatives and fuel efficiency.
Similarly, in the consumer goods industry, large-scale injection moulding is employed for producing household appliances, electronic devices, and packaging solutions, meeting the demands of mass consumer markets with efficiency and reliability. Moreover, in the medical sector, it enables the production of precision components, diagnostic equipment, and medical devices, supporting advancements in healthcare technology and patient care.
Challenges and Future Directions
Despite its numerous advantages, large-scale injection moulding poses challenges such as material selection, cycle time optimization, and environmental sustainability. Addressing these challenges requires continuous innovation, research, and collaboration across the industry to develop new materials, processes, and recycling solutions.
Looking ahead, the future of large-scale injection moulding lies in embracing emerging technologies such as Industry 4.0, additive manufacturing, and sustainable materials. By adopting smart manufacturing practices, digital twin technology, and predictive maintenance, manufacturers can enhance productivity, flexibility, and sustainability while staying ahead of market trends and customer expectations.
In Conclusion
Large-scale injection moulding epitomizes the convergence of technology, innovation, and manufacturing excellence, offering unparalleled capabilities and opportunities for industries worldwide. By harnessing the power of large-scale injection moulding, manufacturers can drive efficiency, competitiveness, and sustainability in an ever-evolving global marketplace, shaping the future of manufacturing for generations to come.
GETTING A QUOTE WITH LK-MOULD IS FREE AND SIMPLE.
FIND MORE OF OUR SERVICES:
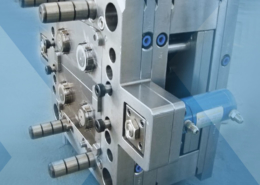
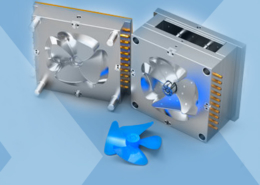
Plastic Molding

Rapid Prototyping
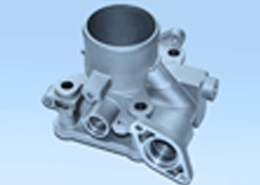
Pressure Die Casting
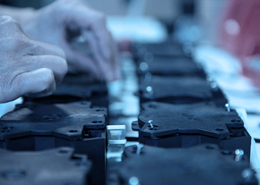
Parts Assembly
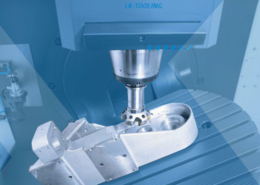