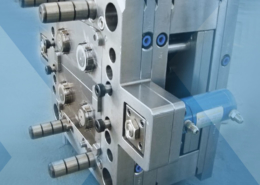
Injection Tray Plastic: Revolutionizing Packaging Solutions
Author:gly Date: 2024-06-08
Injection tray plastic, a cornerstone of modern packaging solutions, offers a versatile and efficient means of protecting and transporting various goods. In today's consumer-driven market, where product safety, sustainability, and convenience are paramount, injection tray plastic emerges as a compelling option. This article aims to explore the intricacies of injection tray plastic, from its inception to its widespread applications across diverse industries.
Introduction to Injection Tray Plastic
Injection tray plastic, also known as injection-moulded trays, is a packaging solution characterized by its durability, customization options, and cost-effectiveness. Typically manufactured using thermoplastic materials such as polyethylene (PE), polypropylene (PP), or polystyrene (PS), injection tray plastic serves as a protective enclosure for a wide range of products, including food items, electronics, and medical devices. Its versatility in design and production makes it a preferred choice for manufacturers seeking reliable and sustainable packaging solutions.
Evolution of Injection Tray Plastic
Historical Context
The evolution of injection tray plastic traces back to the mid-20th century, coinciding with the rise of injection moulding technology. Initially used for simple packaging applications, such as housing electronic components, injection tray plastic has evolved to meet the evolving needs of various industries, driven by advancements in material science, manufacturing processes, and consumer preferences.
Design and Customization
Injection tray plastic offers unparalleled flexibility in design and customization, allowing manufacturers to tailor trays to specific product requirements. From size and shape to compartmentalization and branding, injection-moulded trays can be designed to optimize product protection, shelf appeal, and consumer convenience. Advanced CAD/CAM software enables precise modelling and prototyping, facilitating rapid iterations and customization to meet changing market demands.
Material Selection
The choice of material plays a crucial role in the performance and sustainability of injection tray plastic. Depending on the application and desired properties, manufacturers may opt for materials with varying degrees of rigidity, impact resistance, and barrier properties. Additionally, considerations such as recyclability and biodegradability are increasingly influencing material selection, as companies strive to align with environmental objectives and consumer preferences.
Applications Across Industries
Injection tray plastic finds applications across a wide range of industries, owing to its versatility, reliability, and cost-effectiveness. In the food and beverage sector, injection-moulded trays are used for packaging fresh produce, meat, poultry, and dairy products, offering protection against contamination and physical damage. Similarly, in the electronics industry, trays serve as protective enclosures for delicate components during shipping and storage, safeguarding against electrostatic discharge and mechanical stress.
Sustainability Initiatives
As concerns about plastic waste and environmental impact intensify, stakeholders across industries are exploring sustainable alternatives and practices. Injection tray plastic, when manufactured from recycled or biodegradable materials, offers a compelling solution to reduce carbon footprint and promote circular economy principles. Initiatives such as closed-loop recycling and eco-friendly packaging designs contribute to the ongoing sustainability efforts within the packaging industry.
Conclusion
In conclusion, injection tray plastic stands at the forefront of packaging innovation, offering a versatile, efficient, and sustainable solution for protecting and transporting various goods. Through advancements in material science, design capabilities, and manufacturing processes, injection-moulded trays continue to evolve to meet the changing needs of industries and consumers. By embracing principles of sustainability, customization, and technological innovation, stakeholders can harness the full potential of injection tray plastic to drive positive change and shape the future of packaging solutions.
Through this exploration of injection tray plastic, we aim to underscore its significance as a pivotal component of modern packaging ecosystems. By understanding its origins, capabilities, and applications, stakeholders can make informed decisions and leverage injection tray plastic to enhance product safety, sustainability, and consumer satisfaction. Looking ahead, continued research and collaboration hold the key to unlocking new possibilities and advancing the field of injection-moulded packaging towards a more sustainable and resilient future.
GETTING A QUOTE WITH LK-MOULD IS FREE AND SIMPLE.
FIND MORE OF OUR SERVICES:
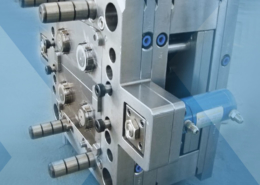
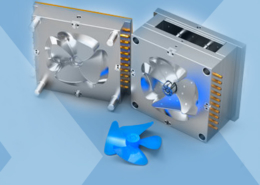
Plastic Molding

Rapid Prototyping
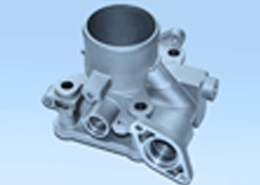
Pressure Die Casting
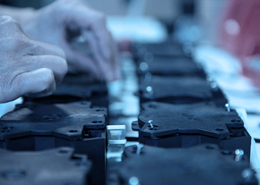
Parts Assembly
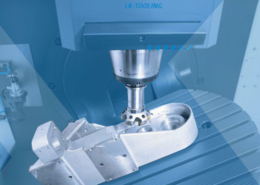