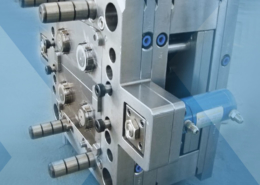
Exploring the Versatility of L-Shaped Plastic Molding
Author:gly Date: 2024-06-08
L-shaped plastic molding stands as a pivotal technique in modern manufacturing, offering unmatched precision, efficiency, and versatility in the production of plastic components with L-shaped profiles. In this comprehensive discourse, we delve into the intricacies of L-shaped plastic molding, from its inception to its contemporary applications and future prospects.
Unveiling L-Shaped Plastic Molding
L-shaped plastic molding refers to the process of shaping and forming plastic materials into components with L-shaped profiles using molding techniques such as injection molding, extrusion molding, and thermoforming. The L-shaped geometry offers unique design possibilities and functional advantages, making it a preferred choice for a wide range of applications in various industries.
The concept of L-shaped plastic molding emerged as a solution to meet the demand for components with specific geometries and functional requirements. By leveraging the capabilities of modern molding techniques, manufacturers can achieve precise L-shaped profiles with high repeatability and consistency, catering to diverse customer needs and design specifications.
Advantages of L-Shaped Plastic Molding
L-shaped plastic molding offers a multitude of advantages over traditional manufacturing methods, making it an attractive option for various applications. Firstly, the ability to produce components with L-shaped profiles enables efficient utilization of space and integration into complex assemblies, optimizing product design and functionality.
Moreover, L-shaped plastic molding offers cost-effective solutions for mass production, with minimal material waste and high production efficiency. The versatility of molding techniques allows for customization of L-shaped components to meet specific performance requirements, such as strength, durability, and aesthetic appeal.
Process and Techniques
The process of L-shaped plastic molding involves several techniques tailored to specific applications and part geometries. Injection molding, the most common method, entails injecting molten plastic into a mold cavity under high pressure, where it solidifies to form the desired L-shaped profile. This technique is widely used for manufacturing precision components with intricate geometries, such as brackets, connectors, and housings.
Extrusion molding, on the other hand, involves forcing molten plastic through a die to create continuous profiles with L-shaped cross-sections. This technique is commonly employed in the production of structural elements, such as beams, channels, and trims, for construction and automotive applications.
Thermoforming, a versatile technique suited for large, complex shapes, entails heating a plastic sheet until it becomes pliable, then forming it over a mold to achieve the desired L-shaped profile. This process is widely used in industries such as packaging, signage, and consumer goods for producing trays, displays, and enclosures.
Applications Across Industries
L-shaped plastic molding finds extensive applications across various industries, ranging from construction and automotive to electronics and consumer goods. In the construction sector, L-shaped plastic components are used for structural framing, cladding, and interior finishes, offering durability, weather resistance, and design versatility.
Similarly, in the automotive industry, L-shaped plastic molding is employed for manufacturing body panels, trim elements, and interior components, contributing to lightweighting initiatives and fuel efficiency improvements. Moreover, in the electronics sector, L-shaped plastic components are utilized for housing electronic devices, providing protection and aesthetics while accommodating complex assemblies.
Challenges and Future Directions
Despite its numerous advantages, L-shaped plastic molding faces challenges such as mold design complexity, material selection, and dimensional stability. Addressing these challenges requires ongoing research and development efforts aimed at enhancing process efficiency, material properties, and design optimization.
Looking ahead, the future of L-shaped plastic molding lies in innovation and collaboration across industries, leveraging emerging technologies such as additive manufacturing, digital design, and sustainable materials. By embracing these advancements, manufacturers can unlock new opportunities for product innovation, process optimization, and environmental stewardship.
In Conclusion
L-shaped plastic molding stands as a testament to the ingenuity and versatility of modern manufacturing, offering unparalleled capabilities and benefits across industries. With continuous innovation and collaboration, L-shaped plastic molding will continue to drive efficiency, sustainability, and innovation in the ever-evolving landscape of plastic manufacturing.
GETTING A QUOTE WITH LK-MOULD IS FREE AND SIMPLE.
FIND MORE OF OUR SERVICES:
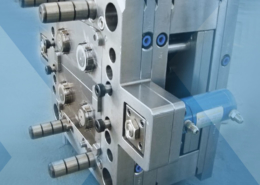
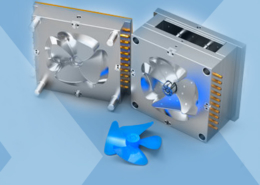
Plastic Molding

Rapid Prototyping
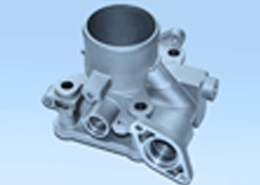
Pressure Die Casting
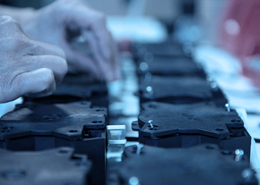
Parts Assembly
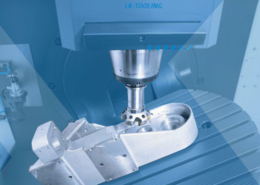